Основные методы формования изделий из композиционных материалов. Метод напыления.
Напыление — способ нанесения порошкообразных или жидких полимеров (или композиций на их основе) на поверхность детали или формы, используемый для получения покрытий различного назначения, а также и некоторых изделий. Для напыления могут быть использованы практически все полимеры; композиции на их основе могут содержать наполнители, пластификаторы, стабилизаторы, отвердители, порообразователи и другие ингредиенты.
Для реализации промышленных способов напыления применяются твердые порошкообразные композиции, основой которых могут служить полиэтилен, сополимеры этилена с винилацетатом, эфиры целлюлозы, фторопласты, поликарбонаты, полиакрилаты, эпоксидные смолы, полиамиды и др. Напыление осуществляется под действием сил электрического поля, а также пневматических или механических сил.
Сущность способа напыления в электрическом поле заключается в том, что распыленным частицам порошка и заземленному изделию сообщают заряды противоположного знака (порошок заряжают, как правило, отрицательно). Для распыления применяют заряжающую распылительную головку или ручной пистолет.
Практическое применение нашли два способа зарядки частиц — контактный и ионный. В первом случае частица приобретает заряд в результате контакта с металлическим электродом, соединенным с источником высокого напряжения. При ионной зарядке с источником высокого напряжения соединяются тонкие металлические электроды, которые коронируют и создают в воздухе поток ионов. Последние, атакуя частицы, сообщают им заряд (рисунок 10.9).
|
|
1 – корпус; 2 – металлическая заряжающая головка; 3 – винтовые каналы;
4 – металлическая коронирующая игла; 5 – кольцо
22)
23) Рисунок 10.9 – Схема головок для контактной (а) и ионной (б) зарядки порошковой краски
Существуют также устройства, в которых сочетаются контактная и ионная зарядка.
Слой полимерного материала образуется в результате осаждения частиц порошка на поверхности противоположно заряженного изделия и их последующего сплавления (для этого изделие помещают в печь).
Процесс осуществляют обычно в камере с конвейером, на котором размещают детали. Источником высокого напряжения служат роторные электростатические генераторы или трансформаторы с выпрямителями (частота 10 – 20 кГц),обеспечивающие напряжение 50 – 120 кВи силу тока 100 – 250 мкА.
В случае контактной зарядки (рисунок 10.9, а) порошок подается воздухом по винтовым каналам головки к острой заряжающей кромке, соединенной с источником высокого напряжения (при прохождении порошка по винтовым каналам развивается центробежная сила, обеспечивающая контакт частиц с головкой).
|
|
Около острой кромки напряженность электрического поля наибольшая, и поэтому частица порошка приобретает максимальный заряд. При ионной зарядке (рисунок 10.9, б)порошок подается воздухом к головке с коронирующими иглой и кольцом.
Способом напыления в электрическое поле можно наносить порошковые материалы на тонкостенные изделия, например, из фольги, что трудно осуществить при использовании других способов, и получать покрытия толщиной от 10 – 20 мкм до 1,0 мм.
Недостаток способа — трудность получения покрытия в углубленных местах изделия из-за уменьшения в этих местах напряженности электрического поля.
С применением для напыления камер непрерывного действия, внутри которых установлены вентиляторы, поддерживающие непрерывную циркуляцию порошка, удается получить равномерное покрытие на изделиях сложной конфигурации и ускорить процесс напыления.
Способ напыления в электрическом поле получил в промышленности наибольшее распространение. Это обусловлено возможностью его автоматизации, а также минимальными потерями порошкового материала.
При использовании способа напыления в псевдоожиженном слое порошка деталь, предварительно нагретую на 50 – 150 °С выше температуры плавления полимера (и зависимости от ее теплоемкости и массы), помещают на несколько секунд в емкость с порошком, находящимся во взвешенном состоянии. При соприкосновении с поверхностью детали порошок нагревается, прилипает к ней и сплавляется. Окончательное сплавление нанесенного слоя происходит в печи. Псевдоожижение порошка может быть достигнуто с помощью воздуха (или другого газа) или вибрации, а также при их одновременном действии.
|
|
Выбор метода определяется способностью порошка к псевдоожижению. При воздушном псевдоожижении («вихревой» метод) используют емкость с расположенной в его нижней части пористой перегородкой, на которую помещают порошок, а снизу подают под давлением воздух, создающий псевдоожиженный (взвешенный) слой порошка, объем которого превышает объем исходного слоя в 1,4 – 1,7 раза.
Пористые перегородки изготовляют из войлока толщиной 25 – 35 мм, 3 – 4 слоев стеклоткани, а также из других материалов с размером пор 40 – 150 мкмпри пористости 50 %. Давление воздуха под перегородкой составляет 0,2 – 0,4 МН/м2,его скорость в емкости — 3 – 5 м/сек (скорость тем больше, чем крупнее частицы порошка).
Метод пригоден для порошков, которые легко переходят в псевдоожиженное состояние. Если псевдоожижение затруднено (например, в случае полиэтиленовых порошков), то используют вибрационный или вибро-вихревой метод. В первом случае псевдоожижение происходит в результате вибрации (частота 50 – 100 Гц,амплитуда 1 – 3 мм)всей емкости или только ее дна.
|
|
Вибро-вихревой метод, представляющий собой сочетание вибрационного и вихревого, позволяет увеличить объем порошка в 2 – 2,7 раза.
Способ напыления в псевдоожиженном слое широко распространен в промышленности. Это объясняется простотой оборудования и технологии, а также вполне удовлетворительным качеством покрытий. Недостатки способа — трудность получения слоев равномерной толщины на деталях сложной конфигурации, сепарация частиц псевдоожиженного порошка по размерам, охлаждение нагретой детали струей воздуха. В связи с тем, что максимальная толщина псевдоожиженного слоя составляет 15 см,способ применяют при напылении порошков на сравнительно малогабаритные изделия.
В усовершенствованных комбинированных способах напыления, например,электровихревом, псевдоожижение порошка совмещается с его ионной зарядкой (рисунок 10.10): псевдоожиженный порошок заряжается от коронирующей сетки и осаждается на заземленной детали. При этом получается более равномерный слой и ускоряется процесс.
Для напыления могут быть также использованы ванны с игольчатым электродом, в которых как псевдоожижение порошка, так и его перенос на заземленное изделие осуществляются под действием сил электрического поля.
24)
1 – деталь; 2 – пористая перегородка; ,3 – труба для подачи газа;
4 – коронирующая проволочная сетка
25)
26) Рисунок 10.10 – Схема ванны для «вихревого» напыления с ионной зарядкой порошковой краски
При газопламенном напылении струя воздуха со взвешенными в ней частицами порошка выбрасывается из сопла распылительного пистолета и проходит сквозь пламя газовой горелки автогенного типа, смонтированной вместе с пистолетом (рисунок 10.11).
1 – шланг для подачи порошковой краски струей воздуха из питательного бака;
2 – шланг для подачи горючего газа; 3 – шланг для подачи воздуха;
4 – инжектор; 5 – корпус пистолета; 6 – факел горелки; 7 – изделие
Рисунок 10.11 – Схема пистолета для газопламенного напыления
К пистолету по одному шлангу струей воздуха подается из питательного бачка порошок, по второму шлангу — горючий газ (например, ацетилен), по третьему — воздух. Под действием тепла горелки порошок нагревается до температуры размягчения полимера, а на поверхности детали сплавляется, образуя сплошной слой (обычно 0,1 – 3 мм). Продолжительность контакта порошка с горючим газом (температура около 1500 °С) — доли секунды, и поэтому значительная деструкция полимера, как правило, не происходит.
Струя, выходящая из горелки, должна быть направлена перпендикулярно покрываемой поверхности, т.к. при этом достигается большая равномерность нанесенного слоя. Для лучшей адгезии покрытия поверхность изделия перед напылением прогревают горелкой.
Недостатки способа — малая производительность (3 – 5 м2/ч);неравномерная толщина слоя; большие потери краски, которая сгорает или не попадает на изделие; коробление тонких материалов, например, листов, при их прогреве; невозможность напыления порошка на изделия большой толщины из-за трудности их прогрева. Способ газопламенного напыления применяют в ремонтном деле, например, при заделке дефектов покрытий или раковин в металле, облицовке сварных швов, а также при нанесении покрытий на крупные металлические конструкции.
Разновидность газопламенного напыления — плазменное напыление. Способ состоит в нагревании порошка плазмой (ионизированным инертным газом — аргоном, гелием, азотом) с температурой 15000 – 30000 °С, образующейся в пламени вольтовой дуги. Порошок инжектируется в пламя также с помощью инертного газа. Несмотря на высокую температуру, полимер не деструктируется, т.к. находится в инертной среде, а продолжительность его контакта с плазмой составляет доли секунды. Этим способом можно наносить порошки на основе любых полимеров, в том числе и с высокой температурой плавления.
При струйном напылении порошковый материал наносят на предварительно нагретое изделие из специальных пневматических распылителей — ручных или механических. Способ отличается простотой, сравнительно большой производительностью и позволяет получать покрытия хорошего качества. Однако его широкое использование ограничивается необходимостью предварительного нагрева изделия.
При получении покрытий порошок наносят па поверхность, которую предварительно очищают и обезжиривают теми же методами, что и при получении лакокрасочных покрытий, в частности, металлы часто подвергают пескоструйной обработке и обезжириванию органическими растворителями. После образования покрытия изделие охлаждают в воде, в маслах или на воздухе. Скорость процесса и охлаждающая среда влияют на адгезию и механические свойства пленок. Так, медленное охлаждение покрытий на основе аморфных полимеров, особенно в средах, пластифицирующих полимер, уменьшает внутренние напряжения в пленке и повышает ее адгезию к подложке. Улучшение свойств покрытий на основе кристаллических полимеров достигается их быстрым охлаждением (закалкой), приводящим к уменьшению структурной упорядоченности в пленке. Покрытия, получаемые напылением, контролируют теми же методами и приборами, что и лакокрасочные.
Напыление имеет ряд преимуществ перед нанесением лакокрасочных покрытий: можно использовать более широкий ассортимент полимеров и, следовательно, получать покрытия с самыми разнообразными свойствами; нет необходимости в применении растворителей, что важно не только с экономической, но и с санитарно-гигиенической точки зрения (выброс горячих газов из нагревательных устройств в атмосферу уменьшается в несколько раз); при использовании усовершенствованных способов напыления процесс сопровождается минимальными потерями порошка и может быть легко автоматизирован.
Технико-экономическая эффективность напыления обусловлена повышением сроков службы изделий, защищенных покрытием, а также экономией цветных металлов и нержавеющих сталей (вместо изделий из этих материалов можно применять изделия из углеродистых сталей, защищенных покрытием). Трудоемкость напыления ниже трудоемкости нанесения гальванических и лакокрасочных покрытий соответственно в 5 – 10 и 2 – 3 раза. Однако производительность механизированных способов нанесения лакокрасочных покрытий выше, а их декоративные свойства лучше, чем у покрытий, получаемых напылением.
Описанными выше способами можно также изготовлять полые тонкостенные изделия (например, емкости), сплавляя заготовки, полученные напылением порошкового материала на поверхность формы. Особенно перспективно применение напыление для производства изделий из полимеров с высокой температурой плавления.
При напылении в электрическом поле высокого напряжения порошок равномерно распределяется по форме, образуя плотные заготовки, которые прочно фиксируются на стенках формы. Необходимая толщина стенки изделия достигается напылением нескольких слоев порошка, повышением температуры формы или изменением напряженности электрического поля. Частично сплавленную заготовку подвергают дополнительной термообработке.
Формы изготовляют из легко вытравляемого металла (например, алюминия), растворимой соли (например, NaNО2) или из стекла, которое растрескивается при быстром охлаждении формы с нанесенным слоем после его сплавления. Эффективность процесса в случае напыления порошка на стеклянную форму повышается при использовании заземленного экрана, расположенного на внутренней поверхности формы.
Показатели механических свойств и монолитности стенки изделий (например, из фторопластов), полученных напылением в электрическом поле и последующим сплавлением заготовок, на 20 – 40 % выше, чем соответствующие показатели таких же изделий, изготовленных литьем под давлением или экструзией.
При использовании способа напыления концентрация распыленных порошков в производственных помещениях не должна превышать допустимые нормы. Помимо вредного влияния на здоровье работающих, превышение норм запыленности может приводить к пожарам, т.к. смеси распыленных порошков с воздухом (аэродисперсии) взрывоопасны. Поэтому при напылении необходимы механизация и автоматизация технологического процесса, дистанционный контроль и управление, полная герметизация оборудования и очистка выбрасываемого воздуха. При движении аэродисперсий по трубопроводам следует соблюдать правила защиты от возникающего в этих условиях статического электричества, в частности при напылении в электрическом поле применять источники питания с небольшой силой тока (до 150 – 200 мкА).
Дата добавления: 2019-07-15; просмотров: 353; Мы поможем в написании вашей работы! |
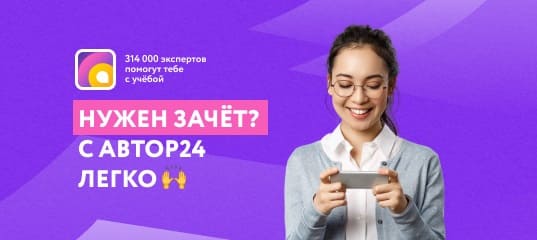
Мы поможем в написании ваших работ!