Основные методы формования изделий из композиционных материалов. Метод намотки.
Полимерные композиционные материалы (ПКМ), армированные непрерывными стеклянными, углеродными, органическими, борными, а в последние годы керамическими волокнами, являются весьма перспективными для применения в ответственных высоконагруженных конструкциях. Наиболее распространённым методом их получения является намотка пропитанных связующих непрерывных волокнистых материалов на оправку с последующей фиксацией на ней формы изделия при отверждении связующего. Таким образом, армированные пластики формируются непосредственно в процессе изготовления изделия. Это позволяет придать материалу (изделию) анизотропию прочности, жёсткости и деформируемости, отвечающую условиям нагружения конструкции, снизив тем самым материалоёмкость, а, следовательно, и массу изделия.
Эти особенности армированных ПКМ предопределили их широкое применение в авиационно-космической технике, судо- и автостроении, в создании энергетических систем, изготовлении высококачественного спортивного снаряжения. Метод намотки наиболее удобен для изготовления оболочек, труб, баллонов, коробов самых разных размеров и назначения. Характерным примером могут служить шаровые и цилиндрические ёмкости для хранения и транспортировки жидкостей и газов.
Иногда намотку используют как удобный технологический приём для изготовления препрегов, например стеклошпона, который затем перерабатывают различными способами. Получение изделий из предварительно пропитанных связующим тканей методом так называемой "ковровой" намотки осуществляется сравнительно просто и не требует дорогостоящего оборудования. Однако свойства материалов, изготовленных таким образом, относительно невысоки, т.к. не обеспечивается строгая ориентация волокон и оптимальная структура материала.
|
|
В наиболее общем виде метод намотки заключается в том, что пропитанные связующим непрерывные нити, жгуты или ленты из армирующих волокон наматывают на оправку до достижения определённой толщины, отверждают и затем отделяет изделие от оправки. Это позволяет осуществить натяжение и строгую ориентацию волокон в соответствии с заданной схемой армирования и благодаря этому реализовать высокую жёсткость и прочность армирующих волокон в материале.
Методы переработки ПКМ делятся на так называемые "сухой" и "мокрый". При намотке первым методом используют препреги в виде нитей, жгутов или лент, вторым — пропитка армирующих материалов связующим осуществляется непосредственно в процессе намотки.
"Сухой" метод имеет ряд преимуществ: в первую очередь, равномерное распределение связующего по толщине изделия; изготовление препрегов осуществляется в специализированных условиях, что позволяет при пропитке армирующих материалов растворами связующих обеспечить удаление растворителей и их рекуперацию. Тем самым становится возможным сделать экологически чистым и процесс пропитки, и последующую переработку препрега в изделия. Однако следует отметить, что жизнеспособность олигомерных связующих ограничивается лишь несколькими месяцам. При намотке изделий "сухим" методом требуется нагревание препрегов для перехода связующего в жидкое состояние, чтобы обеспечить соединение между собой отдельных слоев нитей и получение монолитного материала. Особенности технологии получения и переработки препрегов не позволяют достичь высокого объёмного содержания волокон; обычно оно не превышает 65 %. Эти ограничения обусловили широкое распространение " мокрого " метода намотки.
|
|
Пропиточно-натяжной тракт намоточного станка для "мокрой" намотки включает: шпулярник, на котором устанавливаются бобины с нитями или жгутами; устройство, обычно называемое "гребёнкой", с помощью которого они собираются в ленту; ванну для пропитки волокон связующим; натяжитель и укладчик, формирующий наматываемый элемент на конечном этапе вблизи поверхности оправки (рисунок 10.6).
|
|
Рисунок 10.6 – Технологическая схема намоточного станка
для "мокрой" намотки
Элементы пропиточно-натяжного тракта, в зависимости от типа волокнистого материала, количества нитей или жгутов, особенностей полимерного связующего, способа намотки могут быть выполнены различным образом, снабжены дополнительно термокамерами для подсушки волокнистого материала, устройствами для улучшения пропитки волокон связующим, снятия его избытка и т.д. В ряде случаев, когда необходимо использовать растворы связующих, пропиточно-натяжной тракт включает термокамеру для удаления растворителя. Образующийся при этом материал типа препрега содержит связующее с высокой вязкостью. Поэтому в зоне контакта наматываемого элемента с оправкой обеспечивают, как и при "сухом" способе намотки, локальный нагрев, а иногда используют прикаточные ролики, усиливающие контактное давление для повышения монолитности материала.
Типичные схемы укладки волокон при намотке оболочек из армированных пластиков показаны на рисунке 10.7.
|
|
а – косоугольная; б – кольцевая, поперечная тангенциальная;
в – спирально-продольная; г – полярная
19)
Рисунок 10.7 – Различные схемы намотки армированных
полимерных композиционных материалов
Наиболее распространённым способом является сочетание поперечной (тангенциальной) укладки волокон со спиральными (продольными) слоями. Для их осуществления используют намоточные станки различных типов. В настоящее время уже имеется оборудование, снабжённое компьютерными системами управления, позволяющими осуществлять самые разнообразные схемы армирования, получать например, трубы с изгибами или другие изделия сложной геометрии, не являющиеся телами вращения. Разрабатываются ещё более современные системы, которые путём гибкой технологии смогут укладывать волокна на оправке в любом заданном направлении.
После отверждения в термокамере намотанные изделия подвергаются при необходимости механической обработке и снимаются с оправки. Изделия простой формы (например, цилиндрической) обычно легко снимаются с оправки, покрытой антиадгезионным покрытием. Разделительные антиадгезионные вещества наносятся на поверхность формы в жидком виде при помощи кисти или пульверизатором, либо в виде пасты посредством натирания. Жидкости представляют собой растворы, например, поливинилового спирта с ПАВ в смеси растворителей. Рекомендуется пользоваться окрашенными растворами, чтобы можно было видеть разделительное вещество после нанесения его на оправку (форму). Пасты представляют собой большей частью восковые эмульсии и их применяют лишь в тех случаях, когда материал формы сам по себе обладает некоторой антиадгезионной способностью. Для изготовления ёмкостей с днищами используют весьма сложные сборно-разборные металлические оправки или же вымываемые, выплавляемые или разрушаемые оправки одноразового пользования, которые изготавливают из соли, песчано-полимерных смесей или гипса.
Метод намотки позволяет в широких пределах изменять структуру армированного пластика, в частности относительное содержание компонентов, схему армирования, и соответственно варьировать физико-механические свойства получаемого материала.
Чтобы достичь высокой прочности и герметичности изделий из композиционных материалов, получаемых методом намотки, необходимо обеспечить при их формовании высокое относительное содержание волокна в единице объёма материала, высокую адгезию связующего к наполнителю и монолитность всего материала. Все эти характеристики находятся в прямой зависимости от контактного давления формования, способствующего уплотнению структуры армированного пластика при намотке изделия.
Методы и приёмы уплотнения весьма разнообразны и могут носить локальный или общий характер. Развиваемые при уплотнении нагрузки прямо связаны с характеристикой технологической оснастки и оборудования. Деформационные и особенно прочностные свойства волокнистых наполнителей являются одновременно и важнейшими их технологическими характеристиками и требуют изучения при разработке технологического и аппаратурного оформления процессов формования изделий методом намотки.
Как уже отмечалось, формование изделий связано с пропиткой волокнистого наполнителя связующим. На скорость пропитки, а, следовательно, и производительность процесса формования в целом влияют многие факторы, в числе которых существенная роль отводится проницаемости наполнителя. Проницаемость является характеристикой наполнителя, зависящей от ориентации волокон и степени их уплотнения.
Техническая характеристика нитей, жгутов, холстов и тканей, как правило, содержит такие параметры, как разрывная нагрузка и плотность.
Достигаемая в процессе намотки степень уплотнения наполнителя на оправке определяется его натяжением. При натяжении нити одновременно с уменьшением её диаметра в структуре создаётся давление, под действием которого происходит отжим излишков связующего и возникает достаточно большая адгезия связующего к нити. Использование формующих (прикатывающих) роликов при намотке с локальным прижимом также обеспечивает получение высококачественных изделий в тех случаях, когда это не сочетается с расслоением структуры из-за неверного конструктивного оформления этого приёма.
Один из методов получения изделий повышенной плотности состоит в формовании с объёмным уплотнением структуры. Сущность этого метода заключается в следующем. Намотку армирующего наполнителя — нити, жгута, ленты, ровницы, ткани и др. — проводят на технологическую оправку. Предварительное контактное давление формования по ряду конструктивно-технологических причин из-за малой кривизны поверхности и сложного профиля оправки, большой ширины лент незначительно и недостаточно для обеспечения заданной плотности структуры материала. Поэтому после намотки арматуры осуществляют уплотнение стенок изделия повышением контактного давления формования. Технологически это можно осуществить изменением кривизны поверхности за счёт упругого увеличения объёма оправки.
Волокна в стенках намотанной оболочки оказывают сопротивление упругой деформации формующего элемента (оправки), а величина натяжения армирующей основы возрастает. Таким образом, объёмное расширение оправки способствует дополнительному отжиму связующего из наполнителя, улучшению адгезии, повышению объёмной плотности и прочности изделия.
Влияние температуры формования проявляется через вязкость связующего; с повышением температуры вязкость связующего уменьшается, отжим его усиливается, и в результате возрастает объёмная плотность структуры за счёт уменьшения количества пустот, непропитанных участков, газовых включений и т.д.
Скорость намотки, число газовых включений и пор в изделии также технологически взаимосвязаны.
Дата добавления: 2019-07-15; просмотров: 1398; Мы поможем в написании вашей работы! |
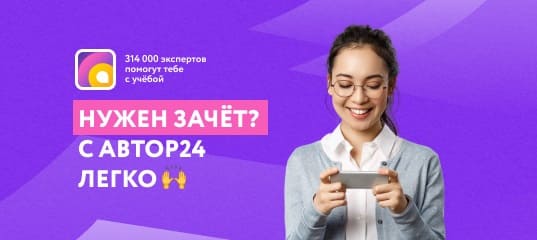
Мы поможем в написании ваших работ!