Методы пригонки и регулирования
Требуемая точность замыкающего звена системы сборочное устройство – собираемые детали достигается в результате автоматического изменения величины одного из составляющих звеньев путем снятия с него необходимого слоя материала. Такое звено называется компенсирующим, а метод достижения точности – методом пригонки. Для достижения требуемой точности замыкающего звена необходимо удалить лишнюю величину компенсирующего звена
(табл. 18.1).
Наибольшее распространение метод автоматической пригонки (подгоночного шлифования) получил при сборке плунжерных пар топливной аппаратуры.
При автоматизации сборки изделий применяют метод регулирования, сущность которого заключается в том, что требуемая точность выходного параметра изделия достигается изменением величины заранее выбранного компенсирующего звена (детали) без снятия с него слоя материала. При этом методе существуют два способа изменения компенсирующего звена: 1) изменение положения одной из деталей (путем ее линейного перемещения при повороте или того и другого одновременно) на величину, равную излишней погрешности замыкающего звена; 2) введение в соединение (в размерную цепь) специальной детали требуемого размера или с требуемыми относительными поворотами ее поверхностей – неподвижного компенсатора.
Технологический процесс автоматической сборки резьбовых соединений
Технологический процесс автоматизации сборки резьбовых соединений состоит из ряда переходов, число которых зависит от типа крепежных деталей и резьбового соединения.
Основными типовыми переходами при автоматической сборке являются:
· загрузка болтов, винтов, шпилек, гаек и шайб в бункерные загрузочные устройства, кассеты или магазины-накопители и их предварительная ориентация;
· подача и установка на сборочные позиции закрепляемых деталей;
· подача из бункерных устройств, кассет или магазинов крепежных деталей в отсекающие устройства в предварительно ориентированном положении;
· подача крепежных деталей сложной формы в специальные устройства для их окончательной ориентации;
· передача деталей в устройства, для окончательной ориентации перед их сопряжением;
· наживление резьбовых деталей;
· завинчивание с предварительным или окончательным тарированным крутящим моментом;
· окончательная затяжка резьбового соединения;
· разгрузка и снятие собранного изделия.
Для надежного входа заборной части сбега резьбы болта (или гайки) в заборную часть сбега резьбы резьбового отверстия необходимо соблюдать соотношение скоростей v (м/с), осевого перемещения и вращения одной из собираемых деталей:
,
где n – частота вращения детали, об/с; Р – шаг резьбы, мм.
Как правило, скорость перемещения должна быть несколько больше произведения пР для компенсации возможного наживления в начальном контакте резьбовых деталей.
При наживлении болта и гайки необходимо, чтобы болт, вращаясь, перемещался вдоль его оси со скоростью v и чтобы было соблюдено условие наживления
Применение шпилек в резьбовых соединениях имеет преимущества по сравнению с болтовыми соединениями.
1. Ввинченные шпильки в корпусную деталь являются направляющими и облегчают установку других деталей, например крышек коренных подшипников в блоки картеров двигателей.
2. Наживление гайки на ввинченную шпильку осуществляется с меньшими трудностями. Резьбовой зазор компенсирует возможные отклонения в перпендикулярности торца гайки и оси шпильки.
Шпильки принято устанавливать в корпус с натягом, который создается различными способами. Натяг в резьбе создается за счет упора торца шпильки в шайбу (рис. 20.1, а), в шарик (рис. 20.1, б), в торец резьбового отверстия (рис. 20.1, в), за счет упора торца шпильки в торец резьбовой детали (рис. 20.1, г, д), в самой резьбе шпильки и конической резьбе корпусной детали (рис. 20.1, е), в конической резьбе шпильки и корпусной детали (рис. 20.1, ж), при наличии натяга в самой резьбе между шпилькой и резьбовым отверстием (рис. 20.1, з). Наибольшее распространение в машиностроении получили шпилечные соединения с натягом по среднему диаметру в резьбе (рис. 20.1, з) и натягом на сбег в резьбе (рис. 20.1, и).
Рис. 20.1 Виды посадок шпилечных соединений
Завершающими переходами автоматической сборки являются завинчивание и затяжка резьбовых соединений с регламентированным моментом или силой затяжки, от которых в конечном счете зависит работоспособность собираемого изделия. Основным параметром качественной затяжки резьбового соединения является точность силы затяжки крепежной детали (болта или шпильки) Q ЗАТ, которая определяется по удлинению крепежной детали
Такой метод измерения силы затяжки применяют только в тех случаях, когда величину удлинения D l болта можно измерить, т. е. при l > 6 d (рис. 20.2).
Рис. 20.2 Схема измерения силы затяжки болтового соединения по удлинению D l болта
В большинстве случаев при затяжке резьбовых соединений, достигнутую силу затяжки контролируют путем измерения косвенных технологических параметров.
В машиностроении применяют следующие методы контроля силы затяжки, основанные на измерении:
· крутящего момента на ключе резьбозавертывающего инструмента МЗАТ с применением кулачковых или других муфт и с остановом шпинделя, настроенных на заданный момент;
· угла поворота болта или гайки (j ЗАТ после его касания опорного торца о корпус;
· величины удлинения стержня болта (шпильки);
· крутящего момента предварительной затяжки МПР (пороговый момент) и дополнительного угла затяжки (j ДОП (комбинированный метод);
· деформации встроенных специальных упругих элементов крепежных деталей или индикаторных шайб;
· силы предварительного растяжения болта, выполненного со специальными элементами;
· температуры нагрева стержня болта (шпильки);
· напряжений в стержне болта (шпильки) тензометрированием.
В процессе автоматического наживления, завинчивания и затяжки резьбового соединения изменение крутящего момента на шпинделе резьбозавинчивающего устройства для резьбовых соединений представлено на рис. 20.3. На этапе I наживления происходит скачкообразное возрастание момента, в процессе завинчивания на II этапе момент монотонно увеличивается, а затем резко возрастает на III этапе затяжки.
Рис. 20.3. Схемы изменения силы затяжки резьбовых соединений
По экспериментальным данным 50 % крутящего момента идет на преодоление трения в опорных поверхностях; 40 % – на преодоление трения в резьбе и только 10 % – непосредственно создают силу затяжки.
Дата добавления: 2019-07-15; просмотров: 465; Мы поможем в написании вашей работы! |
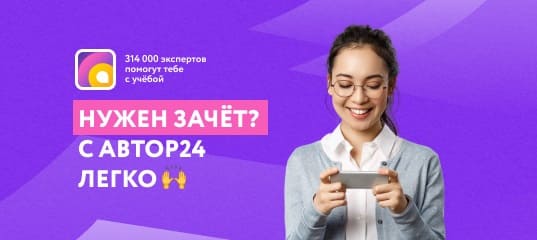
Мы поможем в написании ваших работ!