Прессовое гранулирование(грануляция прессованием или прокаткой)
Перспективный метод подготовки материала к таблетированию.
Сущность метода: заключается в уплотнении порошков и их смесей в специальных грануляторах без увлажнения до получения прочных, примерно одинаковых по форме гранул.
Преимущества: Исключение воздействия влаги на лекарственные средства, возможность развивать высокое прессующее усилие, что позволяет гранулировать смеси с незначительной прессуемостью.
Грануляция прессованием или прокаткой
- ТП. 1. Получение таблеточной массы
- ТП. 1.1. Смешивание компонентов
- ТП.1.2. Компактирование
- ТП.1.3. Просеивание
- ТП.1.4.Опудривание
Технологические схемы производства таблеток: прямое прессование и применение гранулирования в производстве таблеток.
Технологическая схема производства таблеток прямым прессованием
ВР 1. Подготовка помещения, оборудования, персонала, воздуха Кт, Кх, Кмб | ВР1.1. подготовка помещения | ||
ВР1.2. подготовка оборудования | |||
ВР1.3. подготовка персонала | |||
ВР1.4. подготовка воздуха | |||
ВР 2. Подготовка фармацевтических субстанций, вспомогательных веществ и контейнеров Кт, Кх, Кмб | ВР 2.1. отвешивание | ||
ВР 2.2. измельчение | |||
ВР 2.3. просеивание | |||
ТП 1. Получение массы для таблетирования Кт
| ТП 1.1. смешивание | ||
ТП 1.2. опудривание | |||
ТП 2. Таблетирование и обеспыливание Кт | ТП 2.1. таблетирование | ||
ТП 2.2. обеспыливание | |||
ТП 3. Стандартизация Кт, Кх, Кмб | |||
МО 1. Упаковка, маркировка, отгрузка Кт, Кх, Кмб | УМО 1.1. упаковка в первичный контейнер | ||
УМО 1.2. упаковка в вторичный контейнер | |||
УМО 1.3. маркировка | |||
УМО 1.4. упаковка в групповой контейнер | |||
УМО 1.5. отгрузка на склад |
Таблетирование с применений влажной грануляции
Технологическая схема производства таблеток с применение влажной грануляции
ВР 1. Подготовка помещения, оборудования, персонала, воздуха Кт, Кх, Кмб | ВР1.1. подготовка помещения | ||
ВР1.2. подготовка оборудования | |||
ВР1.3. подготовка персонала | |||
ВР1.4. подготовка воздуха | |||
ВР 2. Подготовка фармацевтических субстанций, вспомогательных веществ и контейнеров Кт, Кх, Кмб | ВР 2.1. отвешивание | ||
ВР 2.2. измельчение | |||
ВР 2.3. просеивание | |||
ВР 2.4. получение раствора связующего вещества | |||
ТП 1. Получение массы для таблетирования
Кт | ТП 1.1. смешивание и увлажнение | ||
ТП 1.2. влажное гранулирование | |||
ТП 1.3. сушка гранулята | |||
ТП 1.4. сухое гранулирование | |||
ТП 1.5. опудривание | |||
ТП 2. Таблетирование и обеспыливание Кт | ТП 2.1. таблетирование | ||
ТП 2.2. обеспыливание | |||
ТП 3. Стандартизация Кт, Кх, Кмб | |||
МО 1. Упаковка, маркировка, отгрузка Кт, Кх, Кмб | УМО 1.1. упаковка в первичный контейнер | ||
УМО 1.2. упаковка в вторичный контейнер | |||
УМО 1.3. маркировка | |||
УМО 1.4. упаковка в групповой контейнер | |||
УМО 1.5. отгрузка на склад |
Технологическая схема производства таблеток прессовым гранулированием
ВР 1. Подготовка помещения, оборудования, персонала, воздуха Кт, Кх, Кмб | ВР1.1. подготовка помещения | ||
ВР1.2. подготовка оборудования | |||
ВР1.3. подготовка персонала | |||
ВР1.4. подготовка воздуха | |||
ВР 2. Подготовка фармацевтических субстанций, вспомогательных веществ и контейнеров
Кт, Кх, Кмб | ВР 2.1. отвешивание | ||
ВР 2.2. измельчение | |||
ВР 2.3. просеивание | |||
ТП 1. Получение массы для таблетирования Кт | ТП.1.1. смешивание компонентов | ||
ТП.1.2. компактирование | |||
ТП.1.3. размалывание | |||
ТП 1.4. просеивание | |||
ТП 1.5. опудривание | |||
ТП 2. Таблетирование и обеспыливание Кт | ТП 2.1. таблетирование | ||
ТП 2.2. обеспыливание | |||
ТП 3. Стандартизация Кт, Кх, Кмб | |||
МО 1. Упаковка, маркировка, отгрузка Кт, Кх, Кмб | УМО 1.1. упаковка в первичный контейнер | ||
УМО 1.2. упаковка в вторичный контейнер | |||
УМО 1.3. маркировка | |||
УМО 1.4. упаковка в групповой контейнер | |||
УМО 1.5. отгрузка на склад |
Подготовка фармацевтических субстанций и вспомогательных веществ. Измельчение и просеивание фармацевтических субстанций и вспомогательных веществ.
|
|
Подготовка включает в себя: отвешивание, измельчение и просеивание фармацевтических субстанций и вспомогательных веществ.
Измельчение препарата используется для достижения однородности смешения, устранения крупных агрегатов в комкующихся и склеивающихся материалах, увеличения технологических и биологических эффектов.
Измельчение порошков приводит к определенному увеличению прочности и числа контактов между частицами и в результате – к образованию прочных конгломератов.
Тонкое измельчение лекарственных порошков, несмотря на возможные преимущества биодоступности, не нашло применения, за исключением отдельных случаев, широкого применения в технологии производства твердых лекарственных форм. Это обусловлено тем, что кристалл представляет собой жестко сформированную структуру с минимальной свободной и высокой внутренней энергией. Поэтому для его разрушения требуются значительные внешние усилия. При этом в системе кристаллов одновременно с измельчением усиливается трение, которое уменьшает прилагаемую внешнюю нагрузку до величин, способных вызвать только эластическую или незначительную пластическую деформацию. Поэтому эффективность измельчения, особенно в кристаллических веществах с высокой температурой плавления, быстро падает.
Для увеличения пластической деформации в измельчаемый порошок вводят некоторое количество жидкой фазы.
Увеличение свободной энергии кристаллов при измельчениии может служить причиной механо-химической деструкции препаратов и уменьшения их стабильности при хранении.
Измельчение высокопластичных материалов с низкими температурами плавления, таких как скользящие и смазывающие вещества, может привести к значительному увеличению их эффективности при изготовлении таблеток.
Некоторые мягкие конгломераты порошков могут быть устранены просеиванием их или протиранием через перфорированные пластины или сита с определенным размером отверстий. В других случаях просеивание является неотъемлемой частью измельчения для получения смеси с определенным гранулометрическим составом.
Для осуществления измельчения порошков и гранул предложен ряд аппаратов с различными рабочими органами. Нередко измельчающие агрегаты входят в комплекс оборудования для обработки исходных субстанций и конечной продукции – гранул (грануляторы, смесители-грануляторы, классификаторы и др.).
Измельчение: грубое и среднее – молотковые дробилки, мелкое – барабанные и шаровые мельницы и дисмембраторы. Сверхтонкое измельчение – газоструйные мельницы. Измельченные в-ва просеивают на вибрационном сите.
Смешение ингредиентов, входящих в состав таблеточной массы. Характеристика смесителей, используемых в таблеточном производстве: барабанных, червячно-лопастных, ленточных, центробежных, установок СПМ-200.
Смешивание порошков проводится с целью достижения однородной массы и равномерности распределения действующего вещества таблеток. Для смешивания и увлажнения порошкообразных веществ применяются смесители различных конструкций.
С вращающимися лопастями
Шнековые
Смесители барабаны
При смешивании порошков необходимо придерживаться следующих правил:
к большому количеству добавлять меньшее;
ядовитые и сильнодействующие вещества, применяемые в малых количествах, предварительно просеянные через сито, добавлять у массе отдельными порциями в виде тритураций, т.е. в разведении с наполнителем в концентрации 1:100;
окрашенные вещества и вещества с большой удельной массой загружают в смеситель в последнюю очередь;
легколетучие эфирные масла вводятся в сухую гранулированную массу перед прессованием на стадии опудривания, во избежание их улетучивания.
Практика производства таблеток показывает, что время, необходимое для смешивания простой прописи (двух- и трехкомпонентные) в сухом состоянии, составляет 5-7 минут, для более сложной – 10-12 минут.
После смешивания сухих порошков в массу отдельными порциями добавляют увлажнитель, что необходимо для предотвращения ее комкования.
При влажном смешивании порошков равномерность их распределения в значительной степени улучшается, не наблюдается разделения частиц и расслоения массы, улучшается ее пластичность. Перемешивание смоченных порошков сопровождается некоторым уплотнением массы вследствие вытеснения воздуха, что позволяет получать более плотные твердые гранулы. Время перемешивания влажной массы: для простых смесей 7-10 минут, для сложных – 15-20 минут. Оптимальное количество увлажнителя определяется экспериментально (исходя из физико-химических свойств порошков) и указывается в регламенте. Ошибка может привести к браку: если увлажнителя ввести мало, то гранулы после сушки будут рассыпаться, если много – масса будет вязкой, липкой и плохо гранулируемой. Масса с оптимальной влажностью представляет собой влажную, компактную смесь, не прилипающую к руке, но рассыпающуюся при сдавливании на отдельные комочки.
Барабанные смесители
Перемешивание сыпучих материалов в барабанах достигается их вращением. Для увеличения эффективности перемешивания внутри барабанов устанавливают насадки в виде различных
перегородок‚ полок или винтовой спирали на внутренней поверхности стенки.
Барабанные смесители применяют для периодического и непрерывного смешивания сухих
порошкообразных материалов.
Смесительный барабан (рис. 3.28) представляет собой емкость 1 на 200 л, четырехугольной формы,
внутри смесителя имеются отбойники, способствующие перемешиванию и рыхлению смешиваемых
материалов. Загрузка и выгрузка осуществляется пери0дически через люк 5. Смеситель вращается вокруг горизонтальной оси со скоростью 28 об/мин.
(барабанный)
Корпус подобных смесителей может быть цилиндрическим, кубическим, призматическим. Для лучшего перемешивания внутри корпусов часто укрепляют перегородки различного размера и формы. Для обеспечения равномерности смешивания требуют длительной работы, в пределах одного или нескольких часов.
В корпусе 1 вращаются в противоположном направлении две сигмооб разные лопасти (вала) с различными скоростями. Одна вращается со скоростью 17-24 об/мин, а вторая со скоростью 6-11 об/мин. Корпус имеет рубашку для охлаждения и нагревания порошковой смеси. Для безопасной работы корпус смесителя закрывается крышкой с электроблокировкой привода.
Ленточный смеситель со спиральной лентой.
Ленточные смесители оснащены корпусом и ротором, состоящим из приводного вала, на котором закреплены спиральная лента большого диаметра и спиральная лента малого диаметра. Спиральные ленты могут быть разделены на две части: право- и левозаходную. В процессе работы спиральная лента большого диаметра перемещает материал в центральную часть корпуса, а спиральная лента малого диаметра - к его торцам. Корпус имеет цилиндрическую форму с плоской крышкой в верхней части, на которой находятся люк для загрузки сыпучего материала и штуцеры для подачи жидких добавок и отсоса воздуха в момент загрузки компонентов в смеситель. Снизу корпуса
посередине расположена разгрузочная коробка с клапаном. Процесс смешивания происходит в результате хаотического перемещения лентами ротора сыпучего материала по корпусу.
Ленточный смеситель!
Смеситель состоит из следующих элементов: вертикального цилиндрического корпуса 1, крышки 2 с загрузочными патрубками 3, приводного вала 4 с ротором 5, выполненным в виде диска 6 с прикрепленными к нему концентрично расположенными полыми усеченными конусами: внутреннего 7, среднего 8, внешнего 9. Высота конусов и угол наклона их образующей к основанию увеличиваются от центральной части к периферии. На рабочей поверхности конусов 7 и 8 имеются по четыре перепускных окна 10, ограниченные снизу поверхностью диска. На рабочей поверхности среднего 8 и внешнего 9 конусов, над перепускными окнами выполнены тангенциальные отверстия 11, полученные путем развертки двух плоскостей: внутренней 12 - направленной противоположно вращению ротора, и наружной 13 - направленной в сторону вращения ротора. В верхней части корпуса, ограниченной поверхностью крышки, установлен статичный отражатель 14, состоящий из внешнего и внутреннего колец 15, между которыми, под девяносто градусов относительно друг друга, закреплены четыре направляющих 16, изогнутых по дуге круга, рабочая (вогнутая) поверхность которых направлена навстречу вращению ротора. Вал крепится в подшипниковых опорах 17 и приводится во вращение через клиноременную передачу 18 от электродвигателя 19. Выгрузка смеси происходит через разгрузочный патрубок 20 в коническом днище 21.
Центробежный смеситель работает следующим образом.
Сыпучие компоненты дозаторами подаются в загрузочные патрубки 3 и попадают на днище вращающегося конуса 7. Под действием центробежных сил частицы материала ускоренно движутся от центра к периферии, распределяясь равномерно по внутренней поверхности конуса, при этом толщина слоя на периферии уменьшается за счет увеличения поверхности распределения частиц. Часть смешиваемых материалов движется через окна 10, после чего разреженным, опережающим потоком попадает на поверхность среднего конуса 8, имеющего большую высоту и угол наклона образующей к основанию. Другая часть движется по образующей внутреннего конуса 7 и сбрасывается через верхнее основание на поверхность среднего, где происходит наложение основного и опережающего потоков (т.е. происходит процесс усреднения компонентов). На среднем конусе 8 материалопоток разделяется на три части: первая, пройдя через окна 10, с опережением попадает на поверхность внешнего конуса 9; вторая (основная) движется по поверхности конуса и сбрасывается на поверхность последующего конуса; и третья часть, отрываясь от рабочей поверхности конуса при движении потока по внутренней плоскости тангенциального отверстия, возвращается к основанию среднего конуса. Смесь, пройдя внутренний 7 и средний 8 конуса, поступает на внешний конус 9. На внешнем конусе материалопоток разделяется на две части: первая под действием центробежной силы движется по внутренней поверхности конуса и выбрасывается через верхнее основание в пространство между ротором и корпусом; вторая - отрывается от рабочей поверхности конуса при движении потока по внутренней плоскости тангенциального отверстия, и материал возвращается к основанию внешнего конуса. Далее смесь попадает на коническое днище 21, откуда удаляется через разгрузочный патрубок 20.
Дата добавления: 2019-07-15; просмотров: 695; Мы поможем в написании вашей работы! |
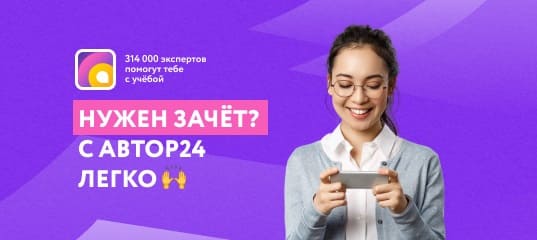
Мы поможем в написании ваших работ!