Техническая характеристика бетонно-растворных смесей, арматурных элементов, материалов и полуфабрикатов
Сваи должны удовлетворять требованиям ГОСТ 13015.0:
- по показателям фактической прочности бетона: в проектном возрасте, передаточной и отпускной (пп. 7.2, 7.4 - 7.7);
- по морозостойкости и водонепроницаемости бетона (п. 7.8);
- к маркам сталей для арматурных и закладных изделий, в том числе для монтажных петель (пп. 8.5, 8.6);
- по защите от коррозии (пп. 7.15, 8.7).
Сваи должны удовлетворять установленным при проектировании требованиям по трещиностойкости и выдерживать контрольные испытания, указанные в рабочих чертежах на эти сваи.
Сваи следует изготовлять из тяжелого бетона по ГОСТ 26633 классов по прочности на сжатие, указанных в рабочих чертежах на эти сваи.
При опирании свай на скальные и крупнообломочные грунты класс бетона по прочности на сжатие следует принимать не ниже В25 независимо от длины сваи.
В качестве крупного заполнителя для бетона свай должен применяться фракционированный щебень из естественного камня или гравия, при этом размер фракции не должен быть более 40 мм.
Нормируемая передаточная прочность бетона должна быть не менее 70% прочности, соответствующей классу бетона по прочности на сжатие.
Нормируемая отпускная прочность бетона свай должна быть равна 100% класса бетона по прочности на сжатие.
Для армирования свай следует применять арматурную сталь следующих видов и классов:
- в качестве ненапрягаемой продольной арматуры - стержневую горячекатаную периодического профиля классов А-400, A-300 и Ас-300 по ГОСТ 5781, термомеханически упрочненную классов Ат-400С и Ат-600С по ГОСТ 10884;
|
|
- в качестве конструктивной арматуры (спирали, сетки, хомуты) - проволоку обыкновенную периодического профиля класса Вр-I по ГОСТ 6727, стержневую горячекатаную гладкую класса А-240 по ГОСТ 5781.
Допускается в качестве ненапрягаемой продольной арматуры применять арматурную сталь класса А-240 по ГОСТ 5781.
Значения действительных отклонений напряжений в напрягаемой арматуре не должны превышать предельных, указанных в рабочих чертежах на эти сваи.
Форма и размеры арматурных и закладных изделий и их положение в сваях должны соответствовать указанным в рабочих чертежах на эти сваи.
Сварные арматурные и закладные изделия должны удовлетворять требованиям ГОСТ 10922 (при классе точности свай 8) и ГОСТ 19804-91.
Технологическая схема производства
Графическая схема работы технологической линии
Склад сырьевых материалов
↓
Бетоносмесительный узел
↓
Подготовка и чистка форм. Смазочный состав наносить ровным слоем. Расход 0.2 кг на 1 м2
↓
Укладка арматурной стали. Защитный слой 30 мм
|
|
↓
Укладка бетонной смеси 30 м/мин
↓
Уплотнение посредством вибрирования (до появления цементого «молока»)
↓
Тепло-влажностная обработка при 95-100 оC, продолжительность полного цикла 13 ч.
↓
Распалубка
↓
Чистка поверхности ЖБИ
↓
Готовое изделие
↓
Склад готовой продукции
Описание технологической схемы
Технология изготовления сборных железобетонных изделий включает в себя следующие основные технологические переделы: подготовку форм или формующей ленты (установка бортоснастки, очистка, смазка внутренней поверхности форм); изготовление арматурных сеток, каркасов, отдельных стержней, закладных деталей и их установку в формы; приготовление бетонной смеси, ее укладку и уплотнение в формах; термообработку отформованных изделий; распалубку готовых изделий на склад; их хранение и выдачу на внешний транспорт.
Технология производства железобетонных свай по конвейерному способу осуществляется следующим образом. Цемент поступает на механизированный склад завода в специализированных железнодорожных цементовозах-цистернах. Разгрузка цемента на складе осуществляется пневматическим способом с подачей цемента непосредственно в силосные баки. Из силосов цемент по наклонному аэрожелобу поступает к пневмонасосу, посредством которого он подается в расходные бункера бетоносмесительного цеха. Мелкий заполнитель – песок доставляется на территорию завода в специальных саморазгружающихся четырехосных полувагонах – гондолах с люками в бортовой части. Разгрузка материала осуществляется гравитационным способом в специально оборудованные на складе приемные бункера, заглубленные в землю. Доставка и разгрузка крупного заполнителя – щебня осуществляется аналогично. Из приемных бункеров заполнитель с помощью питателей подается на основной эстакадно-траншейный полубункерный склад закрытого типа. Забор песка и щебня со склада осуществляется снизу через ленточный конвейер в подземной части. По конвейеру материал транспортируется в расходные бункера бетоносмесительного цеха.
|
|
Дозирование компонентов (воды, цемента, мелкого и крупного заполнителей) осуществляется комплексом весовых дозаторов серии АДУБ-425 (автоматические дозаторы установок бетона). Отдозированные компоненты поступают в стационарные циклические бетоносмесители СБ-93 для принудительного смешивания. Продолжительность перемешивания составляет 3-5 мин. Для уменьшения водопотребности смеси, а также увеличения активности цемента и вследствие этого увеличения прочности бетона используют предварительную виброактивацию цемента, которая заключается в 5-10 минутном вибрировании густого цементного теста при частоте 6000 колебаний в минуту и незначительной амплитуде.
|
|
Приготовленная в бетоносмесителях бетонная смесь выгружается в раздаточный бункер. Тележка с заполненным по рельсам из бетоносмесительного цеха поступает в основной цех – цех для формования железобетонных свай. Для формования изделий используют металлические формы. Перед закладкой в формы бетонной смеси формы очищают, собирают и смазывают специальными составами (саледольная смазка, масляная №1 и №2, прямая и обратная эмульсии и другие виды смазок), препятствующими сцеплению бетона с металлом формы.
После смазки в формы укладываются арматурные каркасы, которые поступают из арматурного цеха и укладываются на место, отведенное для складирования каркасов с 4 часовым запасом. Затем каркасы укладываются в стационарные, предварительно подготовленные формы, при помощи мостового крана грузоподъемностью 10т. Раздаточный бункер выезжает по эстакаде из бетоносмесительного цеха и останавливается над самоходной бадьей для перегрузки бетонной смеси. Перегрузку смеси из раздаточного бункера, имеющей секторный затвор с ручным приводом и вибратор – побудитель, прикрепленный к стенке бункера, производят при высоте падения в самоходную бадью – 150 мм. Затем при помощи мостового крана бадью, имеющую также секторный затвор с ручным приводом и вибратор – побудитель, прикрепленный к ее стенке, снимают с тележки и транспортируют к горизонтально расположенной форме, после чего производят укладку бетонной смеси (высота падения бетонной смеси не более 1м). Уплотнение уложенной в формы смеси происходит при помощи глубинных вибраторов с гибкими валами и составляет 20-30 с на одной позиции. Цикл повторяетсяна каждом из постов. Пропаривание изделий осуществляется с использованием нормальных режимов твердения.
В результате пропаривания бетон в возрасте 28 суток будет иметь меньшую прочность, чем бетон нормального твердения. После пропаривания, общий цикл которого составляет 13 часов, изделия вынимаются из стенд-камеры и переносятся посредством мостового крана на пост доводки и контроля свай.
Освобожденные изделия при помощи мостового крана укладываются на тележку СМЖ-151 с прицепом СМЖ-154 грузоподъемностью 20т, предназначенную для вывоза готовой продукции на склад. Вывезенные на склад изделия сортируются по маркам и укладываются в штабеля (в 4 ряда по высоте). Складская площадь предусматривает хранение изделий в течение 7 суток.
Вывоз изделий со склада осуществляется при помощи грузовых автомобилей или железно-дорожным транспортом.
Тепловые агрегаты
В качестве тепловых агрегатов в курсовом проекте была выбрана камера непрерывного действия, а именно туннельная камера. В качестве теплоносителя был выбран водяной пар.
Таблица 2.
Дата добавления: 2019-07-15; просмотров: 187; Мы поможем в написании вашей работы! |
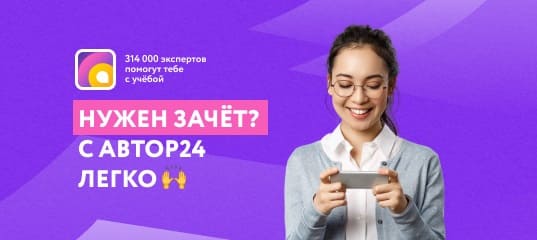
Мы поможем в написании ваших работ!