Характеристика Ремонтно - механического цеха
Организационно-производственная структура ремонтного хозяйства определяется масштабом завода и принятой формой организации ремонта. На ОАО «Русполимет» существует как общезаводские и цеховые ремонтные службы. К общезаводским подразделениям относятся отдел (управление) главного механика, ремонтно-механический цех, склад оборудования и запасных частей, цех по ремонту кольцевого и металлургического оборудования (ЦРКО И ЦРМО). Руководит ремонтным хозяйством главный механик завода через отдел главного механика, который состоит из ряда бюро: оборудования (планово-предупредительного ремонта), планово-производственного, технического и др. Отдел главного механика выполняет конструкторскую, технологическую, производственную и планово-экономическую работу для всего ремонтного хозяйства.
Ремонтно-механический цех (РМЦ) подчинен главному механику и проводит капитальный ремонт и модернизацию сложного оборудования, изготавливает запасные части, технологической оснастки и нестандартное оборудование, оказывает помощь цеховым ремонтным службам.
Структура ремонтного цеха имеет комплексный характер и обеспечивает выполнение всех ремонтных работ и их обслуживание. К числу отделении и участков РМЦ относятся демонтажное, заготовительное, механическое, слесарно-сборочное, кузнечное, сварочное, жестяницкое, восстановления деталей, окрасочное и др.
|
|
В состав цеховой ремонтной базы входят механическая мастерская, слесарный участок, ремонтные бригады, кладовая. Руководство ремонтными работами в цехах осуществляют механики цехов через мастеров и бригадиров. На большинстве заводов механики цехов административно подчинены начальникам производственных цехов. Виды и объемы выполняемых ремонтных работ в цехе обусловливаются принятой на заводе формой организации ремонта оборудования. Техническая база ремонтного хозяйства определяется Типовой системой технического обслуживания и ремонта металло- и деревообрабатывающего оборудования, а также общемашиностроительными нормативами технологического проектирования РМЦ и предусматривает количество и структуру оборудования, производственные площади, средства механизации ремонтных работ и технологию их выполнения. Состав и количество основного оборудования в ремонтном хозяйстве должны обеспечивать выполнение всех видов ремонтных работ, изготовление запасных частей и нестандартизованного оборудования, а также его модернизацию. Основное оборудование ремонтных служб - универсальные станки для обработки металла резанием (токарно-револьверные - 50%, фрезерные - 12, шлифовальные - 16% и др.)- Вспомогательное и слесарно-сборочное оборудование определяется в виде комплекта (набора). Общее количество основного оборудования в РМЦ рассчитывается исходя из трудоемкости станочных работ по ремонту установленного на заводе оборудования и эффективного фонда-времени работы одного станка при двухсменной работе, но не должно превышать 2-2,5% оборудования завода. Площадь определяется на основе компоновки отделений и помещений цеха, а также планировки оборудования и рабочих мест с учетом норм технологического проектирования вспомогательных цехов. Используют и укрупненный метод по удельной площади на единицу основного оборудования (36-46 м). Запасные детали изготавливаются в основном на универсальном оборудовании по устаревшей технологии. Слесарные же работы выполняются, как правило, вручную. Практически не используются механические шаберы, переносные шлифовальные приспособления, электрозаклепочники и пневматические ключи.
|
|
1.2.2 Анализ выполнения производственного плана
Задачами анализа являются:
Оценка степени выполнения плана производства и реализации продукции;
Определение влияния факторов на изменение этих показателей и т.д.
|
|
Объектами анализа служат:
Объем производства и реализации продукции в целом и по ассортименту;
Качество продукции;
Структура производства и реализации продукции;
Ритмичность производства и реализации продукции.
Источниками информации для анализа являются бизнес-план предприятия, оперативные планы-графики, отчетность форма № 1 “Отчет по продукции”, форма № 2 “Отчет о прибылях и убытках” и т.д.
Анализ выполнения плана по производству продукции является отправной стадией экономического анализа работы РМЦ и представлен в таблице 10
Таблица10
Выполнение плана по производству продукции.
Показатели | 2008 год, (отчет) тыс. руб. | 2009 год, тыс. руб. | ||||
План | Факт | Отклонение (+,-) | % к плану | % к 2008 г. | ||
Объем реализации продукции в действующих ценах предприятия | 400 | 605 | 600 | -5 | -1,0 | 150 |
Товарная продукция в действующих ценах предприятия, в т.ч. | 580 | 870 | 850 | -20 | -2,3 | 153,5 |
Запчасти для станочного оборудования | 129 | 250 | 260 | +10 | 4,0 | 201,6 |
Запчасти для проканых станов | 130 | 125 | 84 | -41 | -32,8 | 64,6 |
Запчасти для кранов | 128 | 228 | 250 | +22 | 9,6 | 195,3 |
Из таблицы видно, что за отчетный год план по выпуску готовой продукции недовыполнен на 2,3% из-за невыполнения плана по производству продукции, а по сравнению с 2008 годом произошло увеличение выпуска готовой продукции на 153,5%. На объем товарной продукции влияет численность работающих и выработка на одного работающего.
|
|
Таблица11
Численность работающих и выработка на одного работающего.
Показатели | 2009 год | Отклонение от плана | Выполнение плана, % | |||||
По плану | Фактически | |||||||
Тыс.руб. | тн. | тыс руб. | тн. | тыс. руб. | тн. | тыс. руб. | тн. | |
Товарная продукция | 603 | 28000 | 594 | 28500 | -9 | +500 | 98,5 | 101,8 |
Среднесписочная численность работающих, чел. |
120 |
119
|
-1 |
99,2 | ||||
Годовая выработка на одного работающего | 5,03 | 233,3 | 4,99 | 239,5 | -0,04 | 6,2 | 99,2 | 102,6 |
Из таблицы. видно, что уменьшение численности работающих составило 1 человека.
Выработка на одного работающего (в денежном выражении – млн. рублей) упала на 0,04 тыс. рублей по сравнению с планом за счет изменения цен на готовую продукцию в течение 2009 года. Выработка на одного работающего в натуральном выражении (тн) увеличилась на 6,2 тонн по сравнению с планом за счет увеличения объема производства. Важнейшим фактором, влияющим на выполнение производственной программы, является производительность основных агрегатов.
Показатели работы вертикально-фрезерного станка 6Р82Ш за 2009 год даны в таблице12
Таблица12 - Показатели работы станка за 2009год.
Показатели | Всего по цеху | |||
План | Факт | Отклонение | в % к плану | |
1 | 2 | 3 | 4 | 5 |
Календарное время, сутки | 365 | 365 | - | 100,0 |
Календарное время, час | 8760 | 8760 | - | 100,0 |
Нерабочее время (кап. ремонты, плановые, текущие ремонты, дни отдыха), сутки | 125 | 113 | -12 | 90,4 |
Номинальное время, сутки | 240 | 252 | +12 | 105,0 |
Номинальное время, час | 5760 | 6048 | +288 | 105,0 |
Текущие простои, час | 760 | 672 | -88 | 88,4 |
Фактическое время, сутки | 208,3 | 224 | +15,7 | 107,5 |
Фактическое время, час | 4999,2 | 5376 | +376,8 | 107,5 |
Производство продукции, тн. | 15035 | 19032 | +3997 | 126,6 |
Часовая производительность фактически, тн. | 3,007~3 | 3,540~4 | +1 | 133,3 |
Незавершенное производство, т | 700,0 | 515,3 | 184,7 | 73,6 |
Производительность в номинальные сутки, тн. | 62,646~63 | 75,524~76 | +13 | 120,6 |
На выполнение плана по объему производства влияют экстенсивные и интенсивные факторы работы оборудования. К экстенсивным факторам относятся:
Длительность ремонтов (капитальных, холодных и текущих);
Продолжительность простоев по другим причинам;
Сортамент продукции;
Технологические факторы и степень механизации и автоматизации.
Анализ влияния экстенсивных факторов приведен в таблице 13
Таблица13 - Влияние экстенсивных факторов по производство продукции по станку
Показатели | Вертикально фрезерный станок 6Р82Ш |
Продолжительность капитального ремонта, сутки по плану по отчету отклонение в сутки влияние капитального ремонта, шт. | 125 113 -12 12 х 75,5 ~ 906 |
Продолжительность холодного ремонта, сутки по плану по отчету отклонение в сутки влияние холодного ремонта, шт. | - - - - |
Продолжительность текущих ремонтов, сутки по плану по отчету отклонение в сутки влияние текущих ремонтов, шт. | 32 28 -4 4 х 84,96 ~ 340 |
Всего по цеху, шт. | 1246 |
Влияние продолжительности капитального ремонта на производство продукции рассчитывается по формуле:
Вр = (Тпл - Тф) х Пф
где Вр – изменение производства продукции, тн.;
Тпл – плановая продолжительность капитального ремонта, сутки;
Тф – фактическая продолжительность капитального ремонта, сутки;
Пф – фактически произведенная продукция в номинальные сутки, тн.
Вр = (125-113) х 75,5 = 906 тн.
Влияние текущих ремонтов на производство продукции рассчитывается по формуле:
В’р = (Т’пл – Т’ф) х П’ф
где В’р – изменение производства продукции, тн.;
Т’пл – плановая продолжительность текущих простоев, сутки;
Т’ф – фактическая продолжительность текущих простоев, сутки;
П’ф – фактическое производство продукции в фактические сутки,тн.
В’р = (32 - 28) х (19032 / 224) = 4 х 84,96 = 340 тн.
К факторам интенсивных нагрузок относятся:
Изменение суточной производительности в фактические сутки;
Длительность производства.
Изменение производства продукции в зависимости от интенсивных факторов определяется по формуле:
В = (Пф - Ппл) х Тф,
где В – изменение производства продукции, тн.;
Пф – фактическая производительность стана в фактические сутки, тн.;
Ппл – плановая производительность стана в фактические сутки, тн.;
Тф – число фактических суток работы станка.
В = ((19032 / 224) – (15035/208,3)) х 224 = (84,96 – 72,18) х 224 = +2863тн.
Изменение суточной производительности в фактические сутки привело к увеличению объема производства в 2008 году.
1.2.3 Анализ выполнения плана по качеству продукции
При формировании ассортимента продукции предприятие должно учитывать, с одной стороны, спрос на данные виды продукции, а с другой – наиболее эффективное использование трудовых, сырьевых, технических, технологических, финансовых и других ресурсов, имеющихся в его распоряжении. В таблице14 представлено выполнение плана цеха обработки по ассортименту.
Таблица14
Выполнение плана цехом по ассортименту.
Вид продукции | Объем производства, 2009г. | % выполнения плана | Объем производства, зачтенный в выполнение плана по ассортименту, тн. | |
План, тн. | Факт, тн. | |||
Запчасти для станочного оборудования | 250 | 260 | 104,0 | 250 |
Запчасти для прокатных станов | 125 | 84 | 67,2 | 84 |
Запчасти для кранов | 228 | 250 | 109,6 | 228 |
Всего по цеху: | 603 | 594 | 98,5 | 562 |
Оценка выполнения плана по ассортименту производится по методу наименьшего числа.
Из таблицы 1.15 видно, что план по ассортименту продукции выполнен на 93,2% = (562 / 603 х 100).
1.2.4 Анализ выполнения плана по заработной плате
В данном разделе необходимо проанализировать обеспеченность цеха трудовыми ресурсами, определить показатели текучести кадров, производительности труда, трудоемкости ее выполнения. Анализ использования трудовых ресурсов на предприятии, уровня производительности труда необходимо рассматривать в тесной связи с оплатой труда. В процессе его следует осуществлять систематический контроль за исполнением фонда заработной платы (оплаты труда), выявлять возможности экономии средств за счет роста производительности труда и снижения трудоемкости продукции.
Анализ трудовых ресурсов.
К трудовым ресурсам относится та часть населения, которая обладает необходимыми физическими данными, знаниями и навыками труда в соответствующей отрасли. Достаточная обеспеченность предприятия трудовыми ресурсами, их рациональное использование, высокий уровень производительности труда имеют большое значение для увеличения объемов продукции и повышения эффективности производства. Основными задачами анализа являются:
Изучение и оценка обеспеченности цеха трудовыми ресурсами;
Определение и изучение показателей текучести кадров;
Выявление резервов трудовых ресурсов, более полного и эффективного их использования. Источниками информации для анализа служат план по труду, статистическая отчетность “Отчет по труду”, данные табельного учета и отдела кадров. Анализ численности работающих представлен в таблице15
Таблица15 - Выполнение плана по численности персонала.
Категория работающих | 2008 год (отчет) | 2009 год | Абсолютное отклонение от плана, чел. | ||
План | Факт | ||||
Всего работающих, | 115 | 103 | 100 | -3 | |
в том числе: рабочие | 100 | 90 | 87 | -3 | |
руководители и специалисты | 15 | 10 | 10 | - | |
служащие | 7 | 3 | 3 | - |
Анализ обеспеченности рабочей силой осуществляется путем сравнения фактических данных о численности работающих по категориям с запланированными. Важными характеристиками стабильности кадрового состава являются коэффициенты оборота по приему, увольнению, коэффициент текучести, расчет которых представлен в таблице 16.
Таблица 16 Движение рабочих в цехе.
Показатели | 2008 год (отчет) | 2009 год (отчет) | Отклонение (+,-) |
Среднесписочное число рабочих, чел. | 115 | 100 | -15 |
Принято на работу | - | 8 | +8 |
Уволено с работы, в том числе: по собственному желанию за прогулы за нарушение трудовой дисциплины | 10 5 - 4 | 9 4 - 1 | -1 -1 - -3 |
Коэффициент оборота, % по приему по увольнению | - 8,7 | 8 9 | +8 -0,3 |
Коэффициент текучести, % | 7,8 | 5 | -2,8 |
Анализ качества продукции. Основным из показателей работы цеха является ритмичность. Главной задачей анализа ритмичной работы является выяснение причин нарушения производственного ритма. Данные анализа ритмичности приводятся в таблице 17
Таблица 17 Ритмичность работы цеха по декадам.
Декада | Выпуск продукции за год, тыс руб. | Удельный вес продукции % | Выполнение плана, коэффициент | Объем продукции, зачтенный в выполнение плана по ритмичности, тыс.руб. | ||
План | Факт | План | Факт | |||
Первая | 200 | 180 | 33,2 | 30,3 | 0,90 | 180 |
Вторая | 200 | 205 | 33,2 | 34,5 | 1,025 | 200 |
Третья | 203 | 209 | 33,6 | 35,2 | 1,029 | 203 |
Всего за год | 603 | 594 | 100,0 | 100,0 | 0,985 | 583 |
Показателем ритмичности является коэффициент ритмичности производства, определяемый методом наименьшего числа
Критм. = 583 / 603 х 100% = 96,5%
Также к показателям ритмичности относится и коэффициент вариации (Кв), который определяется как отношение среднеквадратического отклонения от планового задания за декаду к среднедекадному плановому выпуску продукции:
Квар.=(∑∆Х/n)/Xnn
где х2 – квадратическое отклонение от среднедекадного задания;
n – число суммируемых плановых заданий;
хпл – среднедекадное задание по графику.
Кв = ((180 – 200)2 + (205 – 200)2 + (209 – 203)2) / 200 = 0,17%
Коэффициент вариации составляет 0,17. Это значит, что выпуск продукции по декадам отклоняется от графика в среднем на 17%.
Упущенные возможности цеха по выпуску продукции в связи с неритмичной работой определяются как разность между фактическим и возможным выпуском продукции, исчисленным исходя из наибольшего среднедекадного объема производства:
594 – 209 х 3 = -33 тыс. рублей
Причинами, мешающими ритмичной работе цеха являются:
Несвоевременное выполнение плана ремонтных работ;
Несвоевременная поставка сырья и материалов поставщиками;
Недостаток энергоресурсов не по вине предприятия.
Неритмичная работа оказывает неблагоприятное влияние на результат хозяйственной деятельности цеха:
Ухудшается использование трудовых ресурсов;
Основных фондов (увеличиваются простои оборудования, снижается качество продукции);
Возрастают внепроизводственные расходы (оплата простоев и сверхурочных часов).
Качество продукции – это понятие, которое характеризует параметрические, эксплуатационные, потребительские, технологические, дизайнерские свойства изделия, уровень его стандартизации и унификации, надежность и долговечность.
Различают индивидуальные и косвенные показатели качества продукции.
Одним из косвенных показателей является брак. Он делится на исправимый и неисправимый, внешний и внутренний. Выпуск брака ведет к повышению себестоимости, снижению прибыли и рентабельности, качества продукции.
В результате анализа качества изготовляемой продукции должны быть установлены типовые причины брака, степень достоверности данных о браке и влияние изменения качества продукции на выполнение производственной программы.
Исходными данными для анализа служат сводки о браке и акты о браке (таблица18.)
Таблица18 Потери от брака по цеху за 2009 год.
Показатели | 2008 год | 2009 год | Отклонение | |
Абсолютное | в % к 2008г. | |||
1 | 2 | 3 | 4 | 5 |
Себестоимость окончательно забракованной продукции, млн. руб. | 213,8 | 50,8 | -163,0 | 76,24 |
Расходы по исправлению брака, млн.руб. | - | - | - | - |
Реализация брака по цене использования, млн.руб. | 6,8 | 2,35 | -4,45 | 65,44 |
Взыскано с поставщиков за поставку недоброкачественной продукции, тыс.руб. | - | 1,45 | +1,45 | - |
Удержано с виновников брака, тыс. руб. | - | - | - | - |
Потери от брака, млн. руб. | 207,0 | 47,0 | -160,0 | 77,3 |
Производственная себестоимость валовой продукции, млн. руб. | 21812,3 | 27876,2 | +6063,9 | 27,8 |
Потери от брака, %производственной себестоимости валовой продукции. | 0,95 | 0,17 | -0,78 |
Снижение качества продукции вызывает различные потери, что сокращает ее выпуск. Неритмичная работа цеха сказалась на величине потерь от брака.
Подсчитаем влияние брака на выполнение производственной программы. Если доля потерь в производственной себестоимости продукции составляет 0,17, а объем произведенной товарной продукции в отчетном году равен 594 тыс рублей, то возможно увеличение продукции путем ликвидации брака
594 х 0,17 / 100 = 1,01 тыс. рублей.
Из таблицы 1.17. видно, что в 2008 году значительно снизились потери от брака на 160 тыс. рублей или на 77,3%.
Выводы
Проведенный анализ производственно-хозяйственной деятельности предприятия показал, что финансовое состояние предприятия является устойчивым. Наблюдается повышение коэффициента платежеспособности (ликвидности) предприятия, что указывает на то, что оборотные активы не будут использованы для погашения краткосрочных обязательств в полной мере. В 2008 г. рентабельность продаж увеличилась на 10%, что говорит об увеличении эффективности использования текущих затрат, увеличение оборачиваемости капитала на 0,3 оборот свидетельствует о повышении эффективности его использования. За 2008г. валовая прибыль возросла на 194681 тыс. руб. и составила 688076 тыс. руб., таким образом, темп прироста составил 40%. Из этого следует, что у предприятия имеются средства оплаты долгов, формирования фондов развития. Затраты на производство возросли на 30%, а товарная продукция на 50%. Превышение темпа прироста объёма товарной продукции над темпом прироста затрат на производство обеспечило снижение затрат на 1 руб. ТП на 10 коп., что привело к дополнительному росту прибыли. Темп прироста средней заработной платы превышает темп прироста производительности труда, также темп прироста товарной продукции превышает темп прироста материальных затрат, все это характеризует прогрессивную тенденцию развития предприятия.
На основании проведённого анализа можно сделать вывод, что на ОАО «Русполимет» в РМЦ есть возможность запустить в производство новый вид детали - «Крышка». Она применяется в опорных катках тракторов в количестве 2 штук. Производственные площади располагают для модернизации нового парка оборудования для производства данной детали. Так же это делается с целью экономия средств на её приобретения на стороне, и получения дополнительной прибыли при продаже данного изделия заказчикам. Минимальный выпуск изделия планируется в 2009 году 14000 шт. или 7000 пар «Крышек» в год.
Технологическая часть
2. 1 Описание условий работы и анализ технологичности конструкции детали «крышка» (по госту 14.201-83)
Назначение детали.
Предложен чертеж детали крышка. Марка материала крышки: сталь 45ФЛ ГОСТ 977-7 и допускается замена на стали: стали: 40Л, 45Л.
Детали №403-21—299(298) применяются в опорных катках тракторов, детали №25.01-21-360(361) – в поддерживающих катках. Рассмотрим сборочный узел опорного катка , в котором расположена крышка рисунок 1.
Крышка 1 поджимает уплотнения в виде притертых металлических колец 11 с микроконусом, которые, в свою очередь уплотнены резиновыми кольцами 10. Штифт 2, расположенный в глухом отверстии крышки Ø12Н8 удерживает ось 5 от проворота. Крышки 1 зафиксированы на оси стопорными кольцами 4, осевые усилия , действующие на каток, передаются на ось через фланцы 8, закрепленные болтами на торцах ступицы катка. Чертёж комплексной детали представлен в (приложении 7 )
Конструкция детали
Детали имеют ассиметричную форму, представляющую собой совокупность тела вращения и плоской поверхности, их габаритные размеры составляют:
1. №1- 403-21-299 Ø167х120
2. №2- 403-21-298 Ø167х120
3. №3- 25.01-21-360 Ø130х103
4. №4- 25.01-21-361 Ø130х103.
Анализ поверхностей деталей сведен в таблице 1.1.
Крышки имеют сходную конфигурацию и типоразмеры, что предполагает однотипный вариант механической обработки.
Рисунок 1. Опорный каток.
Таблица 19 Анализ конструкции детали
Поверхность | Требования , предъявляемые к поверхности |
Ø167, Ø130,120,103-левые торцы, внешняя поверхность деталей | Не подвергаются обработке, шероховатость литейная, точность –по 14 квалитету |
120,103-правые торцы, | Rа-6,3, точность по 12 квалитету, |
плоские выступы 185х76,160х77 | Rа-20,50 точность по 12 квалитету, требования параллельности выступов 0,2мм относительно базового отверстия |
2 отверстия Ø29,5и Ø27 | Rа-1,6 предназначены для стяжки болтового соединения; имеется требования к симметричности расположения центров отверстий с зависимым допуском в диаметральном выражении, по новому варианту являются технологической базой |
Для деталей №1,№4: Ø12Н8 | Rа-1,6 ; имеется требование к непересечению осей 0,4мм относительно указанной базы, допуск зависимый |
1)Ø80Н9, Ø65Н9 2) Ø95Н9, Ø75Н9 | Rа-6,3 ;3,2 соответственно, поверхности выполнены точно ввиду того , что они сопряжены в сборке с осью , имеется требование по соосности отверстий |
1)Ø100 , Ø85 | Rа-50 выполнены по 12 квалитету , торцевая поверхность доведена до Rа-6,3 –она сопряжена со стопорным кольцом |
Внутренний контур с конусной поверхностью 10 º ±30' и канавки Ø101- Ø124 , Ø79- Ø95 | Предназначены для уплотнений , конусная поверхность имеет требования по радиальному биению 0,08 мм относительно базового отверстия |
Изготовление такого типа деталей целесообразнее производить групповым методом. Поэтому я предлагаю применить в дипломном проекте групповой технологический процесс для обработки группы деталей аналогичного типа. Из этих четырех деталей выберем деталь- представитель, комплексную деталь.
Анализ технологичности детали «крышка»
Деталь можно считать технологичной, так как:
1. обрабатываемые поверхности в основном открыты и доступны для прохода режущих инструментов;
2. материал 45ФЛ имеет хорошую жидкотекучесть, среднюю линейную усадку, склонность к трещинообразованию-это позволяет применять рациональные методы получения заготовки с размерами и формами наиболее близкими к готовой детали, следовательно возрастает коэффициент использования металла и снижается трудоемкость механической обработки детали;
3. она прочная и жесткая, что позволяет обрабатывать ее с наиболее производительными режимами резания;
4. имеется возможность производить финишную обработку от одной базы всех поверхностей, которые связаны между собой условиями соосности, симметричности, параллельности
Количественная оценка технологичности
Количественная оценка технологичности определяется по ГОСТ 14201-84Е.
Таблица 20 Точность обработки детали
Квалитеты | 14 | 12 | 10 | 9 | 8 | Всего поверхностей |
Количество поверхностей | 6 | 19 | 2 | 2 | 3 | 32 |
Таблица 21 Точность поверхностей детали
Шероховатость, Ra | 80 | 50 | 25 | 20 | 12,5 | 6,3 | 3,2 | 1,6 | Всего поверхностей |
Количество поверхностей | 6 | 2 | 2 | 10 | 8 | 3 | 3 | 3 | 32 |
Таблица 22 Показатели технологичности конструкции крышки
Показатели | Норма | Значение | |
Коэффициент точности обработки | Ктн | 0,91 > 0,8. | 0,91 |
Коэффициент шероховатости | Кш | 0,96£ 1,6. | 0,96 |
Коэффициент унификации | Ку.э | 0,78 | |
Коэффициент использования материала | Ки.м | 0,78 | |
Коэффициент обрабатываемости стали | Км | 0,95 | |
Квалитета обработки | JT12. |
Выбор типа производства
Коэффициент закрепления операций определяется по формуле 1.7:
, (1.7)
где Р- число рабочих мест,
О- количество операций ,выполняемых на рабочем месте за месяц, определяется по формуле 1.8;
, (1.8)
где ηзн-нормативный коэффициент загрузки оборудования
ηзф-фактический коэффициент загрузки рабочего места, определяется по формуле 1.9:
, (1.9)
где mр- расчетное количество станков, определяется по формуле 1.10:
, (1.10)
где N-годовая программа выпуска (14000 шт.)
Тшт- штучное время , мин.
Fд- действительный годовой фонд времени ,ч определяется по формуле 1.11:
, (1.11)
где Fн- номинальный фонд времени работы оборудования ,мин, определяется по формуле 1.12 :
, (1.12)
где Ккд, Кпд – календарные и праздничные дни соответственно,
S- количество смен , 2,
d – продолжительность смены 8 ч.
Fн=250*2*8=4000
ηзн=0,75…0,85.
Примем ηзн=0,85 ,все полученные данные сводим в таблицу 23.
Таблица 23 Коэффициент закрепления операций
Операция | Тштк | mp | P | ηзф | О |
005 | 20,4 | 1,79 | 2 | 0,89 | 0,95 |
010 | 7,2 | 0,53 | 1 | 0,53 | 1,6 |
015 | 3,73 | - | - | - | - |
020 | 1,91 | 0,071 | 1 | 0,071 | 10,6 |
Итого | 4 | 2,99 |
Если 10≥Кзо>1- крупносерийное,
20≥Кзо>10- производство среднесерийное,
40≥Кзо>20-производство мелкосерийное
Кзо=2,99-следовательно, производство крупносерийное.
ВЫБОР ИСХОДНОЙ ЗАГОТОВКИ
Заготовка является сложной геометрической фигурой, то для нахождения объема заготовки необходимо разбить заготовку на элементарные геометрические фигуры. Тогда объем заготовки будет складываться из объема элементарных геометрических фигур, см3 :
Для стали 45ФЛ g=7,81г/см3
Масса заготовки, г:
.
Для отливки
S=(360/1000* 10,87*1,05*1*0,87*0,5)-(10,87-8,5)25/1000=1,72 руб.
Для штамповки
S=(373/1000*11,2*1*1*0,8*1*1)-(11,2-8,5)25/1000=3,27 руб,
Коэффициент использования материала:
для отливки
Ки.м.=8,5/10,87=0,78
для штамповки
Ки.м.=8,5/11,2=0,75
Значит штамповка по сравнению с отливкой дорога, а также менее экономична по использованию материала.
Ввиду того, что крышка не является телом вращения и имеет сложную конфигурацию, заготовку для нее можно получить из отливки.
Чертеж заготовки представлен в (приложении 8 )
Материал детали - литейная сталь 45ФЛ, которая хорошо обрабатывается всеми видами лезвийного инструмента, применяется для изготовления станин , корпусов , муфт , тормозных дисков, вилок ,звездочек и других деталей , работающих при температуре до 400ºС . Некоторые механические свойства стали 45ФЛ рассмотрены в таблице 24 .
Таблица 24 Механические свойства стали 45ФЛ
Диаметр сечения, 1мм | т, Мпа | B, МПа | 5, % | , % | HB |
До400 | 320 | 550 | 14 | 25 | 167-207 |
Таблица 25 Массовая доля элементов и легированных добавок в стали 45ФЛ ГОСТ 977-75
Марка материала | C,% | V,% | Si,% | Mn,% | Cr,% | S,% | P,% | Cu,% | Ni,% |
45ФЛ ГОСТ 977-75 | 0,37-0,45 | 0,06-0,15 | 0,2-0,52 | 0,4-0,9 | 0,3 | 0,045 | 0,04 | 0,3 | 0,3 |
Для заготовки данной массы и конфигурации целесообразно предварительно принять литые отливки, особенно если учесть, что материал детали – литейная сталь.
При этом заготовка имела 11 степень точности( припуски в среднем составляли по 4 мм на сторону) и Rа 80мкм.
Целесообразно снизить припуски на механообработку детали , поэтому я предлагаю в качестве метода получения заготовки использовать литье в песчаные формы, отверждаемые в контакте с оснасткой, при этом припуски сокращаются в 2 раза, степень точности получаемой отливки-8.
При получении заготовки более высокой точности стоимость ее изготовления возрастет, однако, сформировав отливку иным образом, чем в действующем технологическом процессе (сэкономив ≈15% металла) снижаем стоимость механической обработки деталей.
Данный проект представляет разработку группового технологического процесса механообработки деталей. Считаем, что на производство заготовок также распространяется групповая технология, причем для каждой детали группы формируется своя отливка.
Метод получения заготовки -литье в песчаные формы, отверждаемые в контакте с отливкой.
Согласно [4] таблица 1.1, для вышеуказанного метода получения отливки :
1. степень точности отливки 6-11 , принимаем 8;
2. группа припусков 2-4 , принимаем 3.
Припуски назначаются исходя из допуска на размер и группы припуска , все полученные данные сведем в таблицу 26 (приложение 9)
АНАЛИЗ СУЩЕСТВУЮЩЕГО ТЕХНОЛОГИЧЕСКОГО ПРОЦЕССА И ПРЕДПОЛАГАЕМОГО ВАРИАНТА
Базовый вариант маршрута представлен в таблице 27:
Таблица 27 Базовый вариант маршрута
№ Операции | Содержание операции | Оборудование | То | Тшт |
000 | Заготовительная | |||
005 | Токарная | 16К20М | 2,1 | 4,2 |
010 | Токарная | 16К20 | 9,52 | 13,6 |
015 | Токарная | 1К282 | 7,5 | 12,5 |
020 | Токарная | 1К282 | 8,7 | 11,2 |
025 | Токарная с ЧПУ | 16К20Т1 | 4,4 | 5,8 |
030 | Токарная с ЧПУ | 16А20Ф3 | 13 | 16,2 |
035 | Фрезерная | Вертикально-фрезерный 65А60Ф1-11 | 10 | 13,8 |
040 | Слесарная | Верстак Н873.010 | 1,5 | 0,8 |
045 | Фрезерная | FA5В-V | 1,0 | 8,12 |
050 | Слесарная | Верстак Н873.010 | 1,5 | 3,7 |
055 | Сверлильная | Радиально-сверлильный 2А554 | 2,18 | 4,2 |
060 | Сверлильная | Вертикально-сверлильный СС20143 | 1,71 | 2,9 |
065 | Сверлильная | Радиально-сверлильный 2А554 | 1,15 | 5,8 |
070 | Сверлильная | Радиально-сверлильный 2А554 | 0,36 | 3,5 |
075 | Слесарная | Верстак Н873.010 | 1,5 | 0,15 |
080 | Моечная | Моечная машина Н840 023 | 4,5 | 2,7 |
085 | Контрольная | Стол ОТК Н873 | 1,5 | 6,8 |
Итого | 101,82 |
Анализ базового варианта ТП изготовления детали
Как видно из приведенного маршрута, он предполагает достаточное количество дорогостоящего оборудования :
1. восьмишпиндельный станок для токарной обработки 1К282, причем, т.к. этот станок используется на нескольких операциях , то таких станков применяется несколько, ввиду неудобства переналадки каждой отдельной технологической единицы ;
2. 16К20Ф3 и 16К20Т1, также применяются на 2-х различных операциях, следовательно их количество как минимум 2-е единицы :
3. Фрезерные станки 65А60Ф1-11, FA5В-V .
Согласно действующему технологическому процессу изготовления крышки первые 2 операции предназначены для подготовки чистовой базы :
1. 005- растачивается фаска под центр;
2. 010- деталь устанавливается в центрах , происходит обработка технологической базы Ø 167, к которому не предъявляются особые требования по точности, шероховатости и который, согласно рабочему чертежу, не подлежит механообработке .
Следующие 2-е операции (015,020) – это черновая обработка внутреннего контура детали. Операции 025 и 030 –чистовая расточка внутреннего контура детали (сложный контур типа « бутылка» возможно обработать только на станке с ЧПУ).
Фрезерная операция 035- это съем цилиндрической бобышки заготовки, расположенной над плоскими выступами детали. Фрезерная операция 040-предполагает обработку тех же плоских выступов, но с противоположной стороны детали.
Операции сверления :
1. 055, 060-последовательное сверление 2-х отверстий Ø 29,5;
2. 065-выполняется только для деталей №299 и №361 обрабатывается самая точная поверхность детали - по Н8 ;
3. 070- получение цековок Ø 52.
Вывод:
1. большое количество дорогостоящего оборудования ;
2. неудобство закрепления детали – необходимость подготовки технологической база (операции 005,010 );
3. большое количество единиц технологического оборудования (например, 2-а однотипных станка 16К20Ф3 и 16К20Т1:
4. нерациональная заготовка и, как следствие,- дополнительная операция (фрезерная 035)
В качестве нового варианта технологического процесса изготовления крышки, предлагаю следующий маршрут (таблица 28):
Таблица 28 Новый вариант маршрута
№ операции | Содержание операции | Оборудование | Тца | Тшт |
000 | Заготовительная | |||
005 | Фрезерно-сверлильная | 2204ВМФ4 | 10,37 | 20,4 |
010 | Токарная | 16К20Ф3 | 4,7 | 7,2 |
015 | Расточная | 2204ВМФ4 | 1,2 | 3,73 |
020 | Сверлильная | 2Р135Ф2 | 0,52 | 1,91 |
025 | Моечная | Моечная машина Н840 023 | ||
Итого | 33,24 |
На операции 005- фрезеруется плоскость 185 , причем станок, на котором ведется обработка, обладает поворотным столом и 30-и позиционным барабаном инструментов, что позволяет :
1) фрезеровать три взаимоперпендекулярные плоскости, не переустанавливая деталь;
2) сверлить 2 отверстия (отверстия доводятся до 8 квалитета , т.к. они служат базовой поверхностью) , фрезеровать 2 цековки; на этом этапе подготавливается единая технологическая база , относительно которой происходит почти вся дальнейшая обработка- отверстия Ø 29,5 Н8.
На операции 010 предполагается обработка всего внутреннего контура детали, кроме растачивания до 9 квалитета Ø 80 и Ø 95.
На операции 015 выполняется чистовая обработка Ø 80 и Ø 95, а также растачивание Ø100 –возможна за счет наличия у станка поворотного стола.
На операции 020 сверлиться отверстии Ø12Н8 , т.к. для этого необходимо несколько единиц осевого инструмента применяется станок с ЧПУ.
Анализ предлагаемого варианта ТП изготовления детали
1. Как видно из таблицы 7, все станки имеют устройство ЧПУ: с одной стороны это невыгодно с экономической точки зрения, однако выбранное оборудования – гибкое , а это значит , что станки легко переналаживаются на выпуск иной продукции. Таким образом экономический эффект оказывается положительным.
2. Номенклатура и количество единиц технологического оборудования сведено к минимуму.
3. Создается технологическая база, относительно которой ведется вся обработка детали
4. Применяется рациональная заготовка (степень точности, которой выше-8, т.е. с одной стороны ее себестоимость выше, но, с другой стороны, стоимость механообработки значительно сокращается).
5. Предполагаемое оборудование позволяет сократить количество операций.
Проведем оптимизацию технологического процесса изготовления крышек. Оптимизация производится при наличии ТП обработки изделия по рабочему чертежу детали. Рабочий чертеж детали представлен в эскизном варианте на рисунках 1.2, 1.3 и 1.3а :
Рисунок 1.2. Эскиз детали (вид спереди).
Рисунок 1.3. Эскиз детали (разрез Н-Н).
Рисунок 1.3а. Эскиз детали (вид Л).
Представим ТП в виде последовательности обработки каждой отдельной поверхности. Для этого представим технологический процесс обработки : базовый и новый - в виде последовательных переходов для получения каждой конкретной поверхности. Данные о механообработке каждой поверхности сведем в таблицу 29, таблицу 30 (приложение 10 и 11) соответственно для базового и предлагаемого ТП.
Дата добавления: 2019-07-15; просмотров: 5570; Мы поможем в написании вашей работы! |
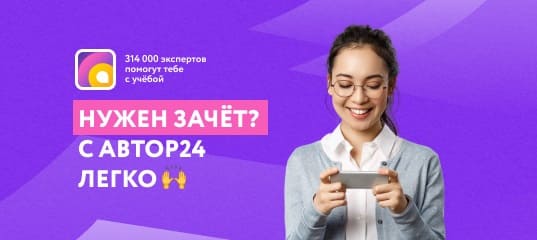
Мы поможем в написании ваших работ!