ОБРАБОТКА НОВЫХ И СТАРОГОДНЫХ ЦЕЛЬНОКАТАНЫХ КОЛЕС И ИХ БАЛАНСИРОВКА
12.1 Размеры новых колес должны соответствовать указанным в таблице 3.1 и конструкторской документации разработчика.
12.2 Расточить отверстия в ступицах новых и старогодных цельнокатаных колес на станке до размера учитывающего диаметр подступичной части оси и натяга необходимого для запрессовки колеса на ось
12.3 Величины допускаемых отклонений отверстий в ступицах новых и старогодных цельнокатаных колес должны быть:
а) допуск круглости (овальность) отверстия - 0,025 мм;.
б) допуск профиля продольного сечения (конусообразность) -0,05 мм при условии расположения большего диаметра отверстия ступицы с внутренней стороны колеса.
12.4 Во избежание задиров при запрессовке и распрессовке, а также для снижения концентрации напряжений в осях наружные и внутренние кромки отверстий ступиц колес должны иметь закругления радиусом 4—5 мм. Переходы закруглений кромок к цилиндрической части ступицы должны быть плавными, без уступов.
12.5 Отверстия ступиц колес должны быть цилиндрическими, без вмятин и забоин, концентричные ободу, а их ось перпендикулярна наружному торцу ступицы и внутренним граням обода.
12.6 Отклонения, возникающие при обработке поверхности отверстий ступиц, не должны превышать норм, указанных в таблице 6.1.
12.7 Балансировать поступающие на вагоноремонтное предприятие цельнокатаные колеса предназначенные для вагонов со скоростями более 160 км/час – статически или динамически. Допускаемый дисбаланс колеса – не более 0,07 кг м (0,7 Нм).
|
|
12.7.1 Балансировать статически цельнокатаные колеса:
а) закрепить цельнокатаные колеса на специальной оправке по отверстию;
б) установить колесо с оправкой на ножи стенда, при этом колесо с оправкой должно легко, от руки, вращаться на ножах;
в) после самостоятельной остановки цельнокатаного колеса, зона повышенного дисбаланса колеса окажется внизу;
г) установить на верхнюю часть боковой поверхности обода колеса мерные магниты, уравновешивая тем самым повышенный дисбаланс цельнокатаного колеса;
д) определить по сумме мерных магнитов величину дисбаланса колеса;
е) установить метку на обод в зоне большего дисбаланса колеса.
12.7.2 Балансировать динамически цельнокатаное колесо на специальных балансировочных станках:
а) установить цельнокатаное колесо по отверстию на оправку станка;
б) включить станок, раскрутить колесо до заданных оборотов: место и величина дисбаланса колеса определяются в автоматическом режиме;
в) установить метку на обод цельнокатаного колеса;
г) допускаемый дисбаланс цельнокатаного колеса ~ не более 0,07 кг м (0,7 Нм).
12.7.3 Устранить повышенный дисбаланс цельнокатаного колеса:
|
|
12.7.3.1 Снять металл с нижней поверхности обода с внутренней стороны колеса механическим путем – фрезерованием, точением. Переход в зоне снятия металла должен быть плавным, без ступеней. Величину снимаемого металла необходимо определить экспериментально при отладке технологического процесса балансировки на каждом предприятии.
12.7.3.2 Балансировать цельнокатаное колесо повторно согласно п. 12.7.1- 12.7.2 до остаточного дисбаланса ~ 0,07 кг м или точнее.
12.7.3.3 Поставить мелом метку на ободе колеса в зоне большего дисбаланса для ориентации колеса при прессовании колесной пары.
12.8 Знак балансировки - клеймо «Б» нанести на наружную боковую поверхность обода колеса при клеймении колесной пары согласно
рис. 21.4.
12.10 Старогодные цельнокатаные колеса, подготовленные к прессованию на ось без расточки отверстия, допускается балансировке не подвергать (с учетом того, что они балансировались перед предыдущим формированием колесной пары).
РЕМОНТ ПОДСТУПИЧНЫХ И ПРЕДПОДСТУПИЧНЫХ ЧАСТЕЙ, ШЕЕК И РЕЗЬБОВЫХ ОТВЕРСТИЙ СТАРОГОДНЫХ ОСЕЙ
13.1 Для обеспечения установленной шероховатости поверхностей оси после механической обработки и строгого соблюдения геометрических размеров, а также для удаления следов коррозии, наминов, рисок и других дефектов, выявленных после распрессовки колесных пар, подступичные части осей должны механически обрабатываться с последующим упрочняющим накатыванием роликами в соответствии с инструкцией № ТИ-32-ЦВ-ВНИИЖТ-86.
|
|
13.2 Усилия на ролик при упрочняющем накатывании подступичных частей осей указаны в таблице 13.1.
Таблица 13.1
13.3 Разрешается удалять путем обточки поперечные и относящиеся к ним наклонные трещины на подступичных частях осей при условии, что диаметры подступичных частей после обточки под колеса будут не менее 182 мм, под тормозные диски – не менее 184 мм. При этом обточка подступичных частей этих осей должна производиться в глубину за пределы трещины не менее чем на
0,5 мм.
13.4 Допускается шлифовка подступичных частей оси после накатки, при этом снимаемый слой металла должен быть не более 0,4 мм. Чистота обработки подступичных частей оси должна быть не менее Ra 1,25.
13.5 Разница в диаметрах подступичных частей с одной и другой стороны оси не регламентируется.
13.6 Подступичные части осей после обработки должны быть цилиндрическими без вмятин и забоин по всей длине. Отклонения, возникающие при обработке, не должны превышать требований согласно таблице 6.1.
|
|
13.7 Для плавного захода оси в ступицу при запрессовке наружный конец подступичной части обтачивается на конус с разностью диаметров не более 1 мм и длиной 7÷15 мм.
13.8 Переходы от запрессовочного конуса к цилиндрической подступичной части оси и от подступичной части к средней должны выполняться плавными, без уступов. Середина оси обозначается керном.
13.9 При ремонте со сменой элементов следы коррозии, риски и другие дефекты на шейках и предподступичных частях оси удалять полировкой шкуркой № 6 ГОСТ 5009-82 с маслом машинным ГОСТ 1707-51 в пределах допустимых размеров согласно таблице 6.1.
13.10 После окончательного ремонта оси, перед запрессовкой, подступичные, предподступичные части и шейки осей должны быть испытаны магнитным дефектоскопом, а также проведен ультразвуковой контроль оси.
13.11 В отверстиях М20 допускается срыв резьбовых ниток - суммарно не более трех резьбовых ниток в одном отверстии.
При наличии прослабленной, забитой или смятой резьбы отверстия М20 восстанавливают заваркой с последующей механической обработкой.
При наличии оборванных болтов в резьбовых отверстиях:
а) болты высверливают, выбивают или выжигают;
б) резьбу восстанавливают прогонкой метчиком.
ОБРАБОТКА НОВЫХ ОСЕЙ
14.1 Для восполнения изъятых из эксплуатации бракованных осей производится обработка новых осей. Заготовка оси и окончательно обработанная ось подлежат сертификации.
14.2 На наружной поверхности кованной заготовки должны быть нанесены знаки маркировки горячим способом – номер оси, номер плавки, дата изготовления и условный номер завода-изготовителя, а также приемочные клейма заказчика. Высота знаков маркировки 10 мм, глубина 1-3 мм.
14.3 После отрезки заготовки по длине и обработке центровых отверстий, заготовки осей поступают на вагоноремонтное предприятие. К каждой партии прикладывается сертификат соответствия с указанием номера плавки каждой оси, даты и места изготовления оси.
14.4 В технологический процесс обработки оси входят следующие операции:
а) токарная черновая обдирочная;
б) чистовая обработка торцов;
в) ультразвуковой контроль;
г) токарная чистовая;
д) обработка резьбовых отверстий М20 на торцах;
е) накатка оси по всей длине;
ж) приточка или шлифовка подступичных частей оси;
з) шлифовка шеек и предподступичных частей оси;
и) неразрушающий контроль и контроль ОТК.
14.5 Шероховатость обработанных поверхностей должна соответствовать указанным в таблице 6.2.
14.6 Размеры осей должны соответствовать размерам, указанным в конструкторской документации ОАО «ТВЗ» по чертежам №№ 4075.10.011, 4096.10.011, 4096.10.012.
14.7 Произвести упрочняющую накатку роликами оси по всей длине в соответствии с инструкцией № ТИ-32-ЦВ-ВНИИЖТ-86 и ГОСТ 31334-2007 при изготовлении новых осей после механической обработки.
Изготовить образцы на каждые 500 накатанных осей для обеспечения контроля твердости накатываемого слоя в соответствии с вышеуказанной инструкцией. Образцы и заключение лаборатории о твердости накатанного слоя оси сохраняются в течение пяти лет.
14.8 При шлифовке шеек, предподступичных и подступичных частей оси припуск на обработку (снимаемый слой металла) должен быть не более 0,3 мм на радиус.
14.9 Провести неразрушающий контроль оси: при входном контроле, перед прессованием колес и дисков, и после запрессовки в составе колесной пары.
14.10 Произвести перенос клейм после чистовой обработки торцов при участии контролеров ОТК с наружной поверхности оси на торец оси ударным методом металлическими клеймами согласно раздела 21. Перенос клейм удостоверяют клеймом на торце оси: условным номером завода, производившего обработку оси и перенесшего клейма.
Дата добавления: 2019-02-22; просмотров: 920; Мы поможем в написании вашей работы! |
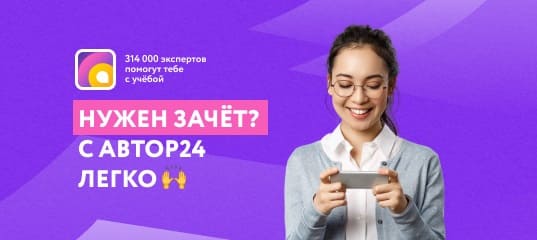
Мы поможем в написании ваших работ!