Требования к грузоподъемным механизмам буровой установки
Управление лебедкой должно осуществляться с пульта бурильщика.
На корпусе оборудования, входящего в состав талевой системы (кронблок, талевый блок, крюк), должна быть указана допускаемая грузоподъемность.
Ходовой и неподвижный концы талевый канатов не должны касаться элементов вышки.
Работы на приемном мосту буровой установки по затаскиванию и выносу труб, а также работы по обслуживанию (замене) гидравлических блоков буровых насосов должны быть механизированы.
Управление грузоподъемными механизмами для работы на приемном мосту должно быть дистанционным.
Конструкция вспомогательной лебедки должна обеспечивать плавное перемещение и надежное удержание груза на весу. С пульта управления лебедкой оператору должен быть обеспечен обзор места работы и перемещения груза. При необходимости должен быть установлен дублирующий пульт управления.
Оборудование для вращения бурильной колонны
Функции оборудования для вращения бурильной колонны
вращение поступательно движущейся бурильной колонны;
подача бурильной колонны с долотом и регулирование ее скорости (в пределах от 0÷100 м/ч) для поддержания на долоте необходимой нагрузки и обеспечения возможной скорости его углубления;
ввод под давлением бурового раствора от буровых насосов через буровой рукав внутрь вращающейся бурильной колонны.
К оборудованию для вращения бурильной колонны относятся: ротор; вертлюг; система верхнего привода (рис. 8.9).
|
|
Рис. 8.9. Оборудование для вращения бурильной колонны: 1 – пол буровой установки; 2 – ротор; 3 – ведущая труба бурильной колонны; 4 – буровой рукав; 5 – переводник; 6 – вертлюг; 7 – стояк; 8 – крюкоблок
Буровой ротор
Ротор предназначен для передачи вращения бурильной колонне при роторном бурении и восприятии реактивного крутящего момента колонны, создаваемого забойными двигателями. Реактивный момент воспринимается квадратными вкладышами, надетыми на ведущую трубу, а также специальным стопорным устройством в столе ротора, при включении которого вращение стола становятся невозможным. Бурильные трубы, находящиеся в стволе скважины, заторможены в роторном столе, а вал забойного двигателя вместе с долотом продолжает вращаться.
Ротор также служит для удержания на весу колонны бурильных и обсадных труб. Он используется при ловильных и каротажных работах. Привод его осуществляется через буровую лебёдку цепной или карданной передачей от коробки перемены передач (КПП), а также в отдельных случаях от индивидуального привода.
Ротор представляет собой зубчатый редуктор, ведомое коническое колесо которого насажено на втулку, соединённую со столом. Вертикальная ось стола расположена по оси скважины. Диаметр отверстия в столе ротора выбирают в зависимости от наибольшего размера пропускаемых через него обсадных или бурильных труб, турбобура или долота. Следует учитывать, что при бурении долотом большим, чем диаметр отверстия в роторе, долото может быть навинчено на колонну труб или на вал турбобура снизу под ротором. Диаметр стола зависит от размеров ротора и устанавливаемых на него клиновых захватов элеваторов; величина его обычно составляет 500 – 1000 мм.
|
|
Для удобства работ часть стола ротора сверху закрывают неподвижным заграждением. Роторы должны обеспечивать надёжную работу на всем диапазоне рабочих чисел оборотов и передачу требуемой мощности и крутящего момента. Прочность ротора и опоры его стола должны быть достаточными, чтобы воспринимать наибольший вес колонны бурильных и обсадных труб, устанавливаемых на ротор.
Конструкция ротора должна допускать привод от карданного вала и от цепной передачи, обеспечивать достаточную герметичность и предохранение механизмов от попадания промывочной жидкости, грязи и пр. Вес ротора и его конфигурация должны допускать транспортировку при помощи транспортных средств и волоком в пределах промысла. Объем масляной ванны ротора должен быть достаточным не только для обеспечения надежной смазки трущихся деталей, но и для отвода тепла, выделяемого при работе.
|
|
Рабочее направление вращения стола ротора всегда должно быть по часовой стрелке, если смотреть сверху, однако , конструкция ротора должна допускать я обратное вращение, применяемое при ловильных и других работах. В главной опоре, воспринимающей осевую статическую и рабочую нагрузки, возникающие при установке колонны на стол ротора и от трения ведущей штанги - квадрата о вкладыши при подаче инструмента, применяют радиально-упорные шариковые или конические подшипники качения.
Во вспомогательной опоре, воспринимающей радиальные нагрузки от зубчатой передачи и удары вверх при бурении и подъеме инструмента, применяют либо радиально-упорные подшипники качения, либо подшипники скольжения с упорным буртом. Большинство конструкций роторов изготовляют с приводом стола непосредственно конической передачей.
Выбор той или иной конструктивной схемы зависит от назначения, требований, размера и типа ротора, а также технологических возможностей завода-изготовителя. Конструктивно лучшей схемой является та, в которой ведомое колесо расположено между опорами, вследствие чего обеспечивается большее расстояние между опарами.
|
|
Например, ротор Р -560 (рис. 8.10) состоит из следующих основных узлов и элементов; станина (1) – основной элемент ротора, внутри которой смонтированы основные узлы и детали. Внутренняя полая часть станины – масляная ванна для смазки конической зубчатой пары и подшипников опор стола ротора и приводного вала.
Стол ротора (3) – основная вращающаяся часть, приводящая во вращение через разъемные вкладыши (5) и зажимы (6) ведущую трубу и соединенную с ней спущенную в скважину бурильную колонну. Стол ротора монтируется на двух шаровых опорах – главной (4) и вспомогательной (9). Главная опора (4) воспринимает динамические циклически действующие нагрузки – радиальную от передаваемого крутящего момента и осевые – от трения ведущей трубы о зажимы
(6) ротора при подаче колонны и от веса стола ротора, а также статическую нагрузку от веса колонны труб и других элементов при установке их на стол ротора,
Вспомогательная опора (9) стола служит для восприятия радиальных нагрузок от зубчатой передачи и осевых ударов при бурении или подъеме колонны. Периферийный зазор между станиной (1) и столом (3) ротора выполнен в виде лабиринта, предупреждающего проникновение бурового раствора и грязи внутрь станины и выбрасывании смазки из ротора при вращении стола. Сверху стол ротора закрыт ограждением (2), служащим для установки на нем элеваторов и другого оборудования при СПО и защиты работников.
Горизонтальный приводной вал (7) выполняется обычно в виде отдельной сборки, в которой вал с ведущей конической шестерней, насаженной на нем, монтируется на роликоподшипниках во втулке . Сдвоенный радиально-упорный подшипник, воспринимающий радиальные и осевые нагрузки от зубчатой передачи, устанавливается рядом с конической шестерней. Вторая опора вала – цилиндрический роликоподшипник. На внешнем конце вала монтируется либо цепная звездочка (10) при приводе ротора цепной передачей от лебедки, либо шарнир карданного вала.
Разъемные вкладыши (5), состоящие из двух половин устанавливают в проходное отверстие ротора, верхняя часть которого снабжена квадратной вышкой. Верхняя часть вкладышей также имеет квадратную форму , в которую входят выступы верхней части зажимов (6) ведущей трубы или роликового зажима при бурении. При СПО в отверстие вкладышей вставляют конусную втулку для клинового захвата. При бурении зажимы (6) или роликовые зажимы закрепляют болтами , оставляют на ведущей трубе и вместе с ней опускают в отверстие вкладыша (5).
Рис. 8.10. Ротор с конической зубчатой передачей Р-560: 1 – станина; 2 – осаждение стола; 3 – стол ротора; 4 – главная опора стола; 5 – разъемные вкладыши; 6 – зажимы; 7 – приводной вал; 8 – сепаратор подшипника; 9 – вспомогательная опора стола; 10 – цепная звездочка; 11 – стопорное устройство
Стопорное устройство (11) служит для фиксации стола ротора. Рукоятка управления стопорным устройством расположена в углублении верхней ограды ротора. В углублении она защищена от повреждений, кроме того, не мешает работать. При переводе рукоятки в рабочее положение выдвигается упор, входящий в одну из специальных прорезей на наружной поверхности стола, и препятствует вращению.
Для обеспечения труда рабочих и ускорения СПО работы комплектуют пневматическими клиновидными захватами, для чего на роторе предусмотрен кронштейн, к которому присоединяется механизм подъема и опускания в отверстии ротора клиньев. Диаметр отверстий в столе ротора и максимальная статическая нагрузка на столе ротора – основные классификационные параметры. Они определяют максимальный диаметр долота и максимальный диаметр и вес обсадной колонны, которая может быть опущена в скважину. В таблице 8.7 представлены технические характеристики роторов.
Таблица 8.7
Техническая характеристика роторов
Параметры | Р-460 | Р-560 | Р-700 | Р-950 | Р-1260 |
Допускаемая нагрузка на стол ротора, МН: | |||||
статическая | 2 | 3,2 | 5 | 6,3 | 8 |
при частоте вращения 100 | 1 | 1,78 | 2,3 | 3,2 | 3,2 |
Наибольшая частота вращения стола, об/мин | 200 | 250 | 250 | 250 | 200 |
Диаметр отверстия в столе, мм | 460 | 560 | 700 | 950 | 1260 |
Условный диапазон глубин бурения, м | 600- 1250 | 2500- 4000 | 3200- 5000 | 4000- 8000 | 6500- 12500 |
Передаточное число конической пары | 2,77 | 3,61 | 3,13 | 3,81 | 3,96 |
Наибольшая передаваемая мощность, кВт | 185 | 370 | 370 | 500 | 600 |
Масса, т | 5,85 | 4,8 | 7 | 10,27 |
8.3.2 Буровой вертлюг
Вертлюг предназначен для подвода промывочной жидкости к колонне бурильных труб при обеспечении свободного ее вращения. Он является промежуточным звеном между талевой системой и вращающимся бурильным инструментом. В процессе бурения вертлюг подвешивается к крюку талевого механизма и посредством гибкого шланга соединяется со стояком напорного трубопровода буровых насосов. При этом ведущая труба бурильной колонны соединяется с помощью резьбы с вращающимся стволом вертлюга, снабженным проходным отверстием для бурового раствора. Во время спуско- подъемных операций вертлюг с ведущей трубой и гибким шлангом отводится в шурф и отсоединяется от талевого блока. При бурении забойными двигателями вертлюг используется для периодического проворачивания бурильной колонны с целью предотвращения прихватов.
В процессе эксплуатации вертлюг испытывает статические осевые нагрузки от действия веса бурильной колонны и динамические нагрузки, создаваемые продольными колебаниями долота и пульсацией промывочной жидкости. Детали вертлюга, контактирующие с раствором, подвергаются абразивному износу. Износостойкость трущихся деталей вертлюга снижается в результате нагрева при трении.
Вертлюги, применяемые при бурении эксплуатационных и глубоких разведочных скважин, имеют общую конструктивную схему и различаются в основном по допускаемой осевой нагрузке. Конструктивные отличия некоторых узлов и деталей отечественных и зарубежных вертлюгов обусловлены требованиями изготовления и сборки, разрабатываемой с учетом производственных возможностей заводов-изготовителей, а также периодической модернизацией вертлюгов с целью повышения их надежности и долговечности.
Детали вертлюгов можно подразделить на две группы: невращающиеся, связанные с корпусом вертлюга крюком и буровым рукавом; вращающиеся, связанные со стволом вертлюга и бурильной колонной.
На рисунке 8.11 схематично показано устройство вертлюга для бурения глубоких скважин. Основная вращающаяся деталь вертлюга – полый ствол, воспринимающий вес колонны. Ствол, смонтированный в корпусе на радиальных и упорных или радиально-упорных подшипниках качения, снабжён фланцем, передающим вес колонны через главный опорный подшипник на корпус и далее на штроп. Опоры ствола вертлюга фиксируют его положение в корпусе, препятствуя осевым вертикальным и радиальным перемещениям и обеспечивая его устойчивое положение при вращении.
Вес корпуса вертлюга, толчки и удары от колонны снизу вверх воспринимаются вспомогательной осевой опорой, устанавливаемой обычно над главной. Ствол вертлюга является ведомым элементом. При принятом в бурении нормальном направлении вращения бурильной колонны (по часовой стрелке, если смотреть сверху на ротор) ствол и все связанные с ним детали во избежание самоотвинчивания имеют стандартные конические левые резьбы. Исключения составляют устройства, в которых совмещены вертлюг и ротор. Ствол такого вертлюга является ведущим элементом и имеет правую резьбу. Вертлюг имеет штроп для подвески его на крюках различной конструкции. Штроп крепится к корпусу на осях и должен иметь возможность поворачиваться на угол до 40°. Корпус имеет приливы, которые исключают консольный монтаж осей штропа, ограничивают поворот и устанавливают его в положение, удобное для захвата крюком, когда вертлюг с ведущей трубой находятся в шурфе.
В верхней крышке корпуса прикреплен изогнутый патрубок-подвод (гусак) резьбой или фланцем, к которому присоединяется напорный буровой рукав. Напорный сальник во время роторного бурения эксплуатируется в тяжелых условиях, срок его службы значительно меньше срока службы остальных деталей вертлюга, поэтому сальник выполняется быстросменным.
Рис. 8.11. Вертлюг буровой: 1 – ствол; 2, 8 – нижний и верхний масляные сальники; 3 – корпус; 4 ,6 – подшипники радиальные нижний и верхний; 5 – опора главная; 7 – опора вспомогательная; 9 – уплотнение быстросменное; 11 – труба напорная; 12 – крышка; 13 – подвод; 14 – штроп
Проточную часть вертлюга выполняют обтекаемой формы для обеспечения минимальных гидравлических потерь и износа абразивными частицами, содержащимися в буровом растворе, движущемся со скоростью до 6 м/с. Размеры корпуса и конструкция вертлюга выполняются с учетом обеспечения надежной смазки всех опор и отвода от них тепла.
В верхней и нижней частях корпуса для уплотнения зазора между корпусом и вращающимся стволом устанавливают самоуплотняющиеся манжетные сальники, которые защищают внутреннюю полость корпуса с масляной ванной от попадания в них влаги и грязи извне и удерживают масло от вытекания из нее при вертикальном рабочем и горизонтальном нерабочем положении вертлюга во время транспортировки и хранения.
Вертлюги снабжаются устройствами для заливки, спуска и контроля уровня масла, а также сапунами с отверстиями для уравновешивания с атмосферным давления воздуха, создающегося внутри корпуса при нагреве в процессе работы. Корпуса выполняются обтекаемой формы для того, чтобы вертлюг не цеплялся за детали вышки при перемещениях. Детали предохраняются от самоотвинчивания.
Основные рабочие элементы и подшипниковые сборки, особенно главный опорный подшипник, воспринимающий наибольшие нагрузки, должны обеспечивать длительную работу на всех режимах. Конструктивно детали вертлюга должны быть технологичны и просты в сборке. Как и другое буровое оборудование, вертлюги должны быть приспособлены к транспортировке любыми транспортными средствами без упаковки.
Для уменьшения числа типоразмеров оборудования в отечественной и зарубежной практике бурения вертлюги классифицируют по допустимой нагрузке на ствол и глубине бурения. Для всего диапазона статических нагрузок и глубин бурения обычно применяют 6 – 8 классов вертлюгов по следующему ряду нагрузок: 0,6; 1,0; 1,6; 2,5; 3,2; 4,0; 6,3; 8,0 МН для глубин бурения 600…12500 м.
Основная техническая характеристика вертлюгов основных российских производителей приведена в таблицах 8.8 и 8.9. Уменьшение числа классов вертлюгов в ряду по сравнению с числом классов буровых установок объясняется тем, что в процессе бурения вертлюг можно легко сменить, и часто при бурении глубоких скважин применяют вертлюги двух-трех классов. В начале цикла бурения применяют вертлюг, рассчитанный на меньшую нагрузку, а по достижении определенной глубины скважины, когда вес бурильной колонны увеличится, используют вертлюг, рассчитанный на большую нагрузку.
Таблица 8.8
Технические характеристики вертлюгов, выпускаемых Волгоградским заводом буровой техники
Параметры | М10.56.00.000 | Б1.56.00.000 | ВВ-250 |
Статическая грузоподъемность, кН (тс) | 1250 (125) | 1600 (160) | 2500 (250) |
Грузоподъемность при 100 об/мин ствола, кН (тс) | 750 (75) | 960 (96) | 2000 (200) |
Максимальное число оборотов, об/мин | 200 | 250 | 220 |
Диаметр проходного отверстия ствола, мм | 76 | 76 | 76 |
Присоединительная резьба с обеих концов переводника и нижнего конца ствола | З-147Л ГОСТ5286-75 | 3-147Л ГОСТ5286-75 | З-152Л ГОСТ5286-75 |
Максимально допустимое давление промывочной жидкости, прокачиваемое через вертлюг, МПа | 25 | 25 | 32 |
Габаритные размеры, мм (l х b х h) | 760х640х2970 | 760х640х2980 | 1070х910х2860 |
Масса, кг | 1290 | 1310 | 2415 |
Таблица 8.9
Технические характеристики вертлюгов ОАО «Уралмаш»
Параметры/ модель | УВ160МА | УВ175МА | УВ250МА | УВ270МА | УВ320МА | УВ450МА | УВ500МА |
1 | 2 | 3 | 4 | 5 | 6 | 7 | 8 |
Грузоподъемность, тс | 160 | 175 | 250 | 270 | 320 | 450 | 500 |
Динамическая грузоподъем-ность (по нормам API), тс | 100 | 66 | 145 | 145 | 200 | 260 | 300 |
Наибольшее рабочее давление, Мпа | 35 | 35 | 35 | 35 | 35 | 35 | 35 |
Диаметр проходного отверстия, мм | 75 | 75 | 75 | 75 | 75 | 75 | 75 |
Резьба переводника для соединения с ведущей трубой (левая) | З -152Л | З -152Л | З -152Л | З -152Л | З -152Л | З -152Л | З -152Л |
Присоединительная резьба ствола (левая) | З -152Л | З -152Л | З -152Л | З -152Л | З-177Л | З-177Л | З-177Л |
Высота (без переводника) | 2228 | 2228 | 2411 | 2411 | 2627 | 2990 | 3230 |
Ширина по пальцам штропа, мм | 990 | 950 | 1090 | 1090 | 1212 | 1375 | 1380 |
Масса,кг | 1620 | 1590 | 2200 | 2200 | 2980 | 4100 | 5670 |
Система верхнего привода
Назначение:
¾ Вращение бурильной колонны с регулированием частоты при бурении, проработке и расширении ствола скважины, при подъеме/спуске бурильной колонны.
¾ Торможение бурильной колонны и её удержание в заданном положении. Обеспечение проведения спускоподъемных операций в том числе:
¾ наращивание/разборка бурильной колонны свечами и одиночными трубами;
¾ свинчивание/развинчивание бурильных труб, докрепление/раскрепление резьбовых соединений переводников и шаровых кранов;
¾ подача бурильных труб к стволу/удаление от ствола вертлюга.
¾ Проведение операций по спуску обсадных колонн в скважину.
¾ Промывка скважины и одновременное проворачивание бурильной колонны.
¾ Задание и обеспечение величин крутящего момента и частоты вращения, их измерение и вывод показаний на дисплей шкафа управления, выносной дисплей, пульт управления и на станцию геолого-технических исследований.
¾ Дистанционное управление.
¾ Герметизация внутритрубного пространства шаровыми кранами.
¾ Расхаживание бурильных колонн и промывку скважины при ликвидации аварий и осложнений.
Буровая установка должна оснащаться верхним силовым приводом в следующих случаях:
o при бурении скважин глубиной более 4500 мм;
o при вскрытии пласта с ожидаемым содержанием в пластовом флюиде сероводорода свыше 6% (объемных);
oпри наборе угла с радиусом кривизны менее 30 м в наклонно-направленной скважине;
o при бурении горизонтального участка ствола скважины длиной более 300 м в скважине глубиной по вертикали более 3000 м.
Дата добавления: 2019-02-22; просмотров: 1048; Мы поможем в написании вашей работы! |
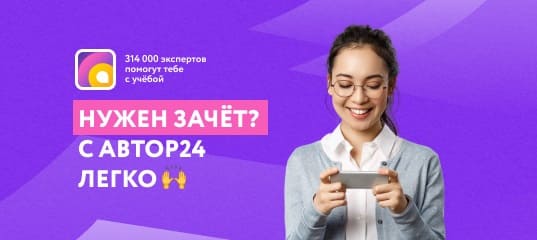
Мы поможем в написании ваших работ!