Конструкции и характеристики турбобуров
Односекционные турбобуры
Односекционные турбобуры предназначены для бурения верхних интервалов вертикальных и наклонно направленных скважин, а также для комплектации реактивно-турбинных буров (РТБ ), используемых для проходки скважин и шахтных стволов диаметром более 394 мм.
Односекционными принято считать турбобуры, состоящие из одной турбинной секции. Они выпускаются как в шпиндельном (турбобур ТВ1-240), так и в безшпиндельном (турбобур Т12РТ-240) исполнении.
Односекционный турбобур (рис. 7.8), состоит из двух длинномерных деталей – корпуса и вала.
Рис. 7.8. Односекционный турбобур:
1 – переводник вала; 2 – вал; 3 – ниппель; 4 – упор; 5 – ротор; 6 – статор; 7 – опора средняя; 8 – гайка роторная; 9 – контргайка; 10 – корпус; 11 – переводник верхний
Технические параметры и энергетические характеристики односекционных турбобуров представлены в табл. 7.1.
На валу турбобура устанавливаются роторы турбины и вращающиеся детали радиальных и осевых опор (втулки средних опор , диски и кольца резинометаллической пяты, втулки нижней опоры). Детали на валу закрепляются гайкой с конической резьбой. В корпусе турбобура с помощью резьбового ниппеля закрепляются невращающиеся детали турбобура – статоры турбины, средние (радиальные) опоры и подпятники. Закрепление деталей по валу и корпусу турбобура осуществляется путем сжатия пакетов этих деталей осевым усилием порядка 800 кН. Понятно, что вал и корпус турбобура испытывают при этом напряжение растяжения. Это усилие необходимо для того, чтобы создать момент трения между сжатыми деталями, превышающий тормозной момент турбобура не менее чем в 2 раза. Такое фрикционное крепление деталей турбины и опор в турбобуре гарантирует от проворота систем статора и ротора в процессе работы.
|
|
Таблица 7.1
Технические характеристики турбобуров
Примечания. Энергетические параметры турбобуров даны при плотности бурового раствора1000кг/м³ (техническая вода).ГТ–ступени гидродинамическоготорможения.
Собранные таким образом детали представляют собой две сжатые системы, в поперечном разрезе напоминающие две гребенки, вставленные друг в друга. При этом детали осевой опоры соприкасаются между собой, а лопатки статоров и роторов ступеней турбины имеют между собой осевой зазор, называемый люфтом турбины. Распределение осевого зазора турбины (положение ротора относительно статора) обеспечивается регулировочным кольцом, установленным между подпятником осевой опоры и статором турбины.
В процессе работы турбобура детали осевой опоры изнашиваются и между ними образуется зазор – люфт осевой опоры. Из-за появления люфта в осевой опоре положение ротора турбины относительно статора изменяется, и когда этот люфт достигнет критических значений, может произойти соприкосновение (посадка) лопаток статора и ротора. В результате такого контакта турбина может выйти из строя, и турбобур откажет в работе. Чтобы не допустить этого, в процессе эксплуатации турбобура величину осевого люфта постоянно контролируют.
|
|
Секционные шпиндельные турбобуры
Секционные шпиндельные турбобуры являются наиболее распространенным типом гидротурбинного забойного двигателя, применяемого для бурения скважин. В настоящее время преимущественное распространение получила унифицированная конструкция турбобура с раздельным размещением в секциях турбинных и опорных узлов, которое благоприятно отражается на показателях надежности, упрощает монтаж и ремонтные работы (рис. 8.9). Раздельное размещение в секциях турбины и осевой опоры позволяет при эксплуатации заменять быстроизнашивающиеся детали непосредственно на буровой путем замены шпиндельной секции.
турбинных секциях устанавливают ступени турбины (статоры и роторы)
равномерно распределенные по длине вала радиальные (средние) опоры с втулками. Обычно в одной турбинной секции устанавливается 110–120 ступеней турбин и 4 средние опоры. В шпиндельной секции устанавливают пакет осевой опоры и две радиальные опоры с втулками. Как в турбинных, так и в шпиндельных секциях таких турбобуров применено фрикционное крепление деталей, устанавливаемых на валах и корпусах, реализуемое путем их осевого сжатия с помощью конических резьбовых соединений.
|
|
Корпусы секций соединяются между собой также при помощи резьбовых соединений, а валы – с помощью конусно-шлицевых полумуфт. Использование таких соединений обеспечивает стабилизацию осевого взаиморасположения валов соединяемых секции в условиях вибраций.
Рис. 7.9. Секционный шпиндельный турбобур:
I – шпиндель; II – секция нижняя; III – секция средняя; IV – секция верхняя. 1 – вал нижней секции ; 2, 13, 25 – переводники; 3, 14, 26 – ротор ; 4, 15, 27 – статор; 5, 16, 18, 28 – опора средняя; 6, 19, 29 – гайка роторная; 7, 21, 31 – корпусы секций; 8, 20, 32, 41 – контргайка; 9, 22, 42 – полумуфта нижняя; 10, 23, 43 – переводник корпуса; 12 – вал средней секции; 17 – втулка средней опоры; 33 – переводник верхний; 24 – вал верхней секции; 30 – колпак; 34 – переводник вала; 35 – вал шпинделя; 36 – ниппель; 37 – осевая опора; 38 – радиальная опора; 39 – втулка корпуса; 40 – гайка шпинделя
|
|
Принцип унификации предусматривает возможность использования в турбобуре турбин одного диаметрального габарита и осевых опор любого необходимого по условиям бурения типа. В турбинной секции наряду с активной турбиной могут устанавливаться ступени гидродинамического торможения ГТ.
Технические параметры и энергетические характеристики секционных шпиндельных турбобуров представлены в табл. 7.1. Стандартные секционные шпиндельные турбобуры обычно состоят из одной шпиндельной секции длиной около 3,5 м и двух-трех турбинных секций длиной каждая по 8 м. Общая длина трехсекционного турбобура – около 28 м. В практике бурения применялись и многосекционные турбинные сборки, когда турбобуры имели четыре, пять или шесть турбинных секций. Общая длина таких турбобуров превышала 50 м.
Распределение и регулировка осевого зазора турбины (положение ротора относительно статора) в секционных шпиндельных турбобурах аналогичны распределению и регулировке зазоров в односекционных машинах. Однако при сборке этих турбобуров, особенно в многосекционных вариантах, следует учитывать влияние дополнительных осевых деформаций и погрешностей.
Турбобуры-отклонители
Для строительства наклонно направленных и горизонтальных скважин необходимо пробурить ствол в соответствии с проектным профилем, который обычно представляет собой кривую линию в трехмерном пространстве. При реализации проектного профиля возникает необходимость изменить траекторию ствола и направить его в заданном направлении. Искривление ствола скважины обеспечивается специальными компоновками низа бурильной колонны ( КНБК), вызывающими постоянно действующую на долото отклоняющую силу, перпендикулярную к оси скважины. Отклоняющая сила возникает в результате появления момента упругих сил из-за искусственного искривления одного из элементов КНБК. При бурении скважин гидравлическими забойными двигателями таким элементом обычно является сам забойный двигатель, называемый отклонителем.
Первыми забойными двигателями-отклонителями были односекционные турбобуры. Непосредственно над корпусом турбобура устанавливались изогнутая толстостенная бурильная труба или переводник с пересекающимися осями концевых резьбовых соединений. Эти компоновки и сегодня применяются при турбинном бурении наклонно направленных скважин.
Величина отклоняющей силы зависит от жесткости элементов КНБК и от расстояния между долотом и местом создания момента упругих сил, т.е. от места искривления или перекоса. Чем это расстояние меньше, тем больше будет отклоняющая сила на долоте. Поэтому применение односекционных турбобуров длиной около 9 м не всегда позволяет получать достаточное отклоняющее усилие для интенсификации темпа набора зенитного угла. Для решения этой задачи разработаны специальные турбобуры-отклонители типа ТО и шпиндели-отклонители типа ШО.
Турбобур-отклонитель ТО (рис. 7.10) состоит из турбинной секции и секции отклонителя (шпиндельной секции), соединенных между собой по корпусу с помощью искривленного переводника. Валы секций соединяются между собой одинарным шарниром, позволяющим передавать вращающий момент при их угловом смещении. Турбинная секция выполнена по схеме независимой подвески и имеет упорно-радиальный шарикоподшипник, установленный в верхней части. Благодаря этой схеме шарнир не нагружен осевыми силами.
Рис. 7.10. Турбобур-отклонитель ТО:
1 – переводник; 2, 15 – полумуфты; 3, 4, 12, 18, 19, 24 – кольца регулировочные; 5, 7 – фонари; 6, 22 – упорно-радиальные шарикоподшипники; 8 – статор; 9 – ротор; 10 – опора средняя; 11, 13 – корпус и вал турбинной секции; 14, 16 – соединительный и искривленный переводники; 17 – шарнирное соединение; 20 – опора нижняя; 21 – пята-сальник; 23, 26 – корпус и вал шпиндельной секции; 25 – гайка ниппельная; 27 – переводник вала
Основные технические характеристики турбобуров-отклонителей ТО представлены в табл. 7.2.
Таблица 7.2 | |||||
Технические характеристики турбобуров-отклонителей | |||||
| |||||
Характеристики турбобура | ТО-172 | ТО2-195 | ТО2-240 | ||
| |||||
Наружный диаметр, мм | 172 | 195 | 240 |
| |
| |||||
Длина, м | 10,7 | 10,1 | 10,2 |
| |
Масса , кг | 1500 | 1850 | 2595 |
| |
Число ступеней турбины | 109 | 95 | 106 |
| |
Длина нижнего плеча отклонителя, мм | 2000 | 2020 | 2350 |
| |
Присоединительная замковая резьба: |
| ||||
к долоту (муфта) | 3-117 | 3-117 | 3-152 |
| |
к бурильным трубам (муфта ) | 3-147 | > 3-147 | 3-171 |
| |
Расход жидкости ( вода), л /с | 25 | 30 | 50 |
| |
Частота вр ащения на раб. режиме, об/мин | 670 | 660 | 660 |
| |
Крутящий момент на раб. режиме, Нм | 650 | 810 | 2040 |
| |
Перепад давления, МПа | 3,8 | 3,3 | 4,1 |
| |
Шпиндель-отклонитель ШО-195 предназначен для работы в компоновке с одной, двумя или тремя стандартными турбинными секциями от серийных турбобуров 3ТСШ 1-195 или А7Ш. Шпиндель состоит из двух узлов, собранных в одном корпусе с помощью искривленного переводника. Два вала шпинделя (верхний и нижний) соединены между собой с помощью двойного шарнира и имеют два упорно-радиальных шарикоподшипника.
Шпиндели турбобуров
Одним из важнейших узлов гидравлического забойного двигателя является его опорный узел, содержащий осевую опору, посредством которой вращающийся вал «подвешивается» в невращающемся корпусе двигателя. У большинства современных конструкций турбобуров опорный узел вынесен в отдельную секцию – шпиндель.
Шпиндель состоит из корпуса и вала. Верхняя часть корпуса шпинделя с помощью конической резьбы соединяется с нижней частью корпуса турбинной секции. Верхний конец вала шпинделя соединяется с нижним концом вала турбинной секции с помощью конусно-шлицевых полумуфт. В средней части шпиндельной секции устанавливается осевая опора, а по краям – радиальные опоры. Кроме того, в шпиндельной секции может быть установлено сальниковое уплотнение вала – с целью уменьшения утечки промывочной жидкости и направления большей части бурового раствора, отработавшего в турбобуре, в промывочные отверстия долота.
Осевая опора является наиболее быстро изнашиваемым узлом турбобура. Срок износа осевой опоры до максимально допустимой величины осевого люфта (5-6 мм) обычно считается главным показателем наработки на отказ забойного двигателя. В современных турбобурах применяются два основных типа осевых опор:
– многоступенчатая резинометаллическая осевая опора скольжения;
– многорядный радиально-упорный шарикоподшипник качения.
В последние годы широкое распространение получила модернизированная осевая резинометаллическая опора, у которой эластичная обкладка подпятника выполнена заподлицо с металлическим остовом, т.н. пята с «утопленной» резиной (рис. 7.11).
В этой опоре практически отсутствует продольная и поперечная деформация резиновой обкладки, благодаря чему снижение прочности резины от внутреннего трения и разогрева из-за циклических деформаций значительно замедляется.
Рис. 7.11. Резинометаллическая осевая опора с «утопленной» резиной (одна ступень): 1 – подпятник; 2 – кольцо наружное; 3 – кольцо внутреннее; 4 – диск
Многорядные шарикоподшипники (рис. 7.12) применяются в шпинделях турбобуров, предназначенных для работы с утяжеленными буровыми растворами и при высокой забойной температуре (более 100 °C).
Рис. 7.12. Упорно-радиальная шаровая осевая опора:
1 – кольцо наружное; 2 – кольцо внутреннее; 3 – шар; 4, 5 – проставочные кольца.
Осевая опора оказывает существенное влияние на выходную характеристику турбобура. При холостом режиме работы осевая опора нагружена сверху гидравлической силой, возникающей от перепада давления, действующего на турбину, и силой тяжести вала (ротора). С увеличением осевой нагрузки на долото происходит разгрузка осевой опоры от действия силы реакции забоя, направленной снизу вверх. Соответственно , снижается и момент трения в осевой опоре шпинделя. Это продолжается до тех пор, пока силы, действующие сверху вниз и снизу вверх, не уравновесятся. В этот момент осевая опора шпинделя полностью разгружена от осевых сил и момент трения в ней минимален, а теоретически равен нулю. Дальнейшее увеличение осевой нагрузки на долото приводит к превосходству силы реакции забоя над суммой сил от перепада давления и веса вала (ротора). Момент трения в опоре, соответственно, возрастает.
Потери на трение в резинометаллической осевой опоре скольжения превышают потери на трение в шаровой осевой опоре качения. При расчетах характеристики турбобура, имеющего шпиндель с резинометаллической опорой, потери крутящего момента от трения в зависимости от плотности раствора и содержания в нем песка ориентировочно составляют 15–30 Н·м на 1 кН суммы гидравлической нагрузки и веса вала. У турбобура, оснащенного шпинделем с шаровой опорой, потери крутящего момента от трения составляют около 10 Н·м на 1 кН гидравлической нагрузки.
При практических расчетах характеристики нового (неизношенного) турбобура допускается не учитывать потери крутящего момента из-за трения для рабочего режима, т.к. стандартные турбобуры обычно работают в зоне, близкой к разгрузке осевой опоры, где эти потери не являются определяющими.
РЕЖИМ ТУРБИННОГО БУРЕНИЯ
Рабочий режим турбобура
Турбина турбобура обладает так называемой мягкой моментной характеристикой, однако это не означает, что бурение турбобуром может осуще-ствляться на всех режимах – от холостого до тормозного. На практике при увеличении осевой нагрузки и крутящего момента на долоте частота вращения вала турбобура вначале снижается, затем турбобур начинает неустойчиво работать, а потом резко останавливается – «срывается». Частота вращения при этом, как правило, бывает не ниже 0,4nx (рис. 7.13).
«Срыв» турбобура объясняется многими факторами, основными из которых являются: нелинейный рост момента сопротивления на долоте и в опорах турбобура при увеличении осевой нагрузки и снижении частоты вращения, низкочастотные колебания момента сопротивления из-за вибраций и неравномерной подачи бурильного инструмента, перемежаемость разбуриваемых горных пород по твердости.
На устойчивость работы турбобура существенно влияет так называемая крутизна линии моментов, т.е. отношение Mт/nx. Для обеспечения устойчивого низкооборотного режима бурения турбобур должен иметь пониженную частоту вращения на холостом режиме, а запас тормозного крутящего момента должен быть существенно увеличен.
Рис. 7.13. Область рабочего режима турбобура: M – крутящий момент; n – частота вращения
Динамическая составляющая осевой нагрузки на долото также оказывает существенное влияние на амплитуду колебаний частоты вращения вала турбобура. Причем это влияние тем больше, чем меньше частота изменения осевой нагрузки и чем меньше момент инерции вращающейся массы вала турбобура. Низкочастотные возмущения могут значительно увеличить амплитуду колебаний частоты вращения и даже привести к остановке турбобура – «срыву».
Рассмотренные факторы способствуют тому, что устойчивая работа турбобура может осуществляться с не менее чем двукратным запасом крутящего момента, т.е. на режимах, располагающихся около режима максимальной мощности и КПД.
Режим максимальной мощности, соответствующий 0,5Mт и 0,5n x, считается основным рабочим режимом турбобура, так как он обычно совпадает с режимом максимальной механической скорости проходки. Поскольку у турбобура частота вращения связана обратно пропорциональной зависимостью с крутящим моментом и осевой нагрузкой, то при турбинном бурении зависимость механической скорости проходки от осевой нагрузки на долото носит нелинейный характер (рис. 7.14).
Определение максимальной механической скорости проходки при бурении турбобуром проводится экспериментальным методом. За переменный фактор принимается осевая нагрузка на долото, которая в процессе бурения контролируется индикатором веса, а за исследуемый параметр – механическая скорость проходки, определяемая соответствующим прибором. Бурильщик опытным путем определяет то значение осевой нагрузки, при котором турбобур начинает работать в экстремальном (оптимальном) режиме. Основным визуальным фактором, по которому устанавливается этот режим, является темп углубления скважины. Обычно бурильщик ориентируется на максимальное значение углубления ведущей трубы в единицу времени. Бурение ведется при постоянных значениях – уровнях – осевой нагрузки на долото с шагом 20–30 кН.
Рис. 7.16. Зависимость механической скорости проходки V от осевой нагрузки на долото G при турбинном бурении
Для каждого уровня определяется механическая скорость проходки. Выбор значений нагрузки осуществляется таким образом, чтобы получить перегиб кривой механической скорости проходки (см. рис. 7.14). Точка перегиба Go приблизительно соответствует экстремальному (оптимальному) режиму работы турбобура.
После запуска турбобура над забоем скважины буровики стараются нагружать турбобур таким образом, чтобы вывести его на рабочий режим, ориентируясь только на темп углубления ведущей трубы. Когда этот темп становится максимальным, увеличение осевой нагрузки прекращают и дальнейшее бурение продолжается при ее установившемся значении. При этом считается, что турбобур работает в рабочем режиме, т.е. при 0,5Mт и 0,5nx.
Если в процессе бурения при рабочей осевой нагрузке происходит внезапная остановка турбобура, то бурильщик вынужден приподнять турбобур от забоя, дать ему вновь запуститься и повторить операцию вывода турбобура на рабочий режим. Поэтому понятно, что субъективно буровики стараются нагружать турбобур при меньшей величине осевой нагрузки, т.е. работать на режимах, расположенных правее 0,5Mт и 0,5nx по характеристике турбобура. И это отклонение вправо от расчетного рабочего режима становится тем больше, чем глубже забой скважины, чем больше отход ствола от вертикали, чем выше уровень низкочастотных вибраций и чем меньше запас крутящего момента турбобура. Таким образом, неустойчивая работа турбобура приводит к тому, что реальные режимы турбинного бурения во многих случаях соответствуют более высоким частотам вращения, чем это принято считать.
Время окончания механического бурения и подъема изношенного долота с забоя при турбинном бурении определяется по снижению уровня механической скорости проходки в 2,5–3 раза по сравнению с первоначальным уровнем.
Дата добавления: 2019-02-22; просмотров: 2812; Мы поможем в написании вашей работы! |
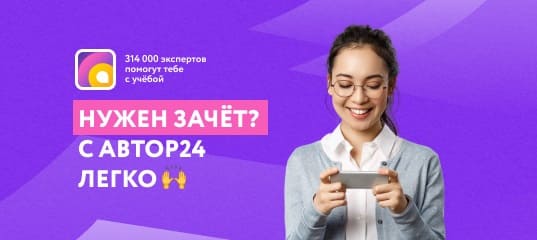
Мы поможем в написании ваших работ!