Режущий инструмент и режимы механообработки
Развитие характеристик режущих материалов направлено в сторону увеличения твердости, стойкости, износостойкости, что не всегда соответствует требованиям идеального инструментального материала (рис. 4.1).
В сортаменте марок углеродистых инструментальных сталей и инструментальных легированных сталей за последние 20 лет существенных изменений не произошло. Наблюдается устойчивая тенденция снижения их доли в общем объеме используемых инструментальных материалов.
Быстрорежущие стали. Развитие быстрорежущих материалов происходит в сторону увеличения доли комплексно-легированных вольфрамомолибденованадиевых и вольфрамомолибденованадиекобальтовых сталей повышенной производительности (Р6М5К5, Р9М4К8, Р12М3Ф2К8) с высокими технологическими свойствами, обеспечивающими повышение стойкости инструмента в 3–5 раз, уменьшение основного времени обработки на 25–40% по сравнению с обработкой инструментами из стали Р18. Стали марок 10Р6М5 и Р9М4К8 рекомендуются для безударной и чистовой обработки, стали марок Р6М5К5 и Р6М5К5ЭШП (электрошлакового переплава) – для черновых операций с ударными нагрузками.
Ведутся работы по созданию и использованию «сверхбыстрорежущих» сталей высокой вторичной твердости (68…70 HRCэ) и теплостойкости (640…650 °С), а также сталей с интерметаллидным упрочнением и теплостойкостью 680…700 °С [9].
Перспективно применение резцов, сверл из быстрорежущих сталей, полученных методом порошковой металлургии и позволяющих увеличить скорость резания на 20–25%.
|
|
Применение быстрорежущей стали с покрытием позволяет повысить стойкость режущего инструмента в 2–5 раз, скорость резания на 15–40%, заменить стали Р18 и Р9К5 на стали Р6М5 и Р6М3.
Переход от инструмента из быстрорежущих сталей к твердосплавному позволяет существенно увеличить скорость резания и сократить примерно в 2–3 раза основное время обработки.
Развитие твердых сплавов связано с разработкой сплавов особомелкозернистой и ультрамелкозернистой структуры, с развитием технологии изготовления сплавов, а также с внедрением дополнительных операций по доуплотнению структуры сплавов на специальных установках.
Упрочнение связки в твердых сплавах позволяет увеличить прочность и сопротивляемость высокотемпературной ползучести. Упрочнение инструментального материала производят за счет внедрения Со–Re или Со–Ru-связок, а также менее дорогих – Fe–Co, Fe–Ni, Co–Ni, Fe–Co–Ni, Fe–Mo [9].
Отмечается тенденция замены карбида тантала более эффективными карбидами гафния, ниобия, хрома, ванадия. Наиболее радикально совершенствуются безвольфрамовые твердые сплавы (БВТС) на основе TiC и TiC–TiN. Эти сплавы в ряде случаев полностью вытесняют вольфрамосодержащие сплавы.
|
|
Весьма прогрессивным является применение твердосплавного инструмента, имеющим износостойкое покрытие из карбида титана, нитрида титана, окиси алюминия и др. Пластины с покрытием для черновых и получистовых работ имеют в 2–3 раза большую стойкость, чем пластины без покрытия, что позволяет повысить скорость резания на 25–30%.
Режущая керамика. Большое значение имеет освоение выпуска пластин из режущей керамики на основе окиси алюминия типа ВШ-46, ВШ-75, ВО-13, керамики оксидно-карбидного класса типа В-3, ВОК-60, ВОК-63, оксидно-нитридной типа ОНТ-20, нитридной – РК-30.
Режущая оксидная керамика, упрочненная волокнами из карбида кремния, используется для обработки сплавов, содержащих никель, цементованных и термообработанных сталей, а также серого чугуна. Керамика на основе нитрида кремния дает возможность вести обработку в широком (до 1000 м/мин) диапазоне скоростей резания. Нитридная керамика в настоящее время применяется при обработке серого чугуна и суперсплавов, т.к. она имеет высокую степень диффузионного износа.
Тенденции развития керамических материалов связаны с совершенствованием технологии производства, оптимизацией состава традиционных марок керамики, широким применением армированной керамики и расширением области применения инструмента на основе нитрида кремния.
|
|
Сверхтвердые синтетические поликристаллические инструментальные материалы (ПСТМ). Для финишной обработки термически упрочненных до высокой твердости сталей и чугунов эффективны инструменты из синтетических сверхтвердых материалов (ПСТМ) на основе кубического нитрида бора. Применение инструмента из ПСТМ (S=0,2–0,12 мм/об, V до 1100 м/мин) позволяет изменить традиционный технологический процесс изготовления деталей из закаленных сталей и производить механическую обработку после термической. Синтетические сверхтвердые материалы на основе кубического нитрида бора, который внедряется в виде вставок в пластины из твердого сплава, могут быть использованы для обработки твердых (до 68 HRCЭ), хромоникелевых и хромоникелемолибденовых сталей со скоростью 130 м/мин.
Высокоскоростная обработка. Все отчетливее проявляется тенденция повышения скоростей резания до 10 000 м/мин с повышенным съемом металла в единицу времени.
Различают резание с обычными скоростями, высокоскоростное резание (ВСО) и сверхвысокоскоростное резание (СВО), причем для ВСО скорости возрастают на порядок, а для СВО на два порядка по сравнению с обычной обработкой.
|
|
Высокоскоростное резание особенно широко применяется при изготовлении сложных цельнометаллических изделий, в процессе обработки которых в стружку уходит до 80…90% массы заготовки. Производительность возрастает в 3–10 раз. Повышается качество поверхности и точность, что связано с повышенным демпфированием в зоне резания, лучшими условиями образования и отвода стружки, уменьшением сил резания (вследствие изменения характера разрушения материала и преобладания хрупкого разрушения) [6].
Высокоскоростное резание стало возможным в результате освоения прогрессивного режущего инструмента на основе мелкозернистого твердого сплава с покрытиями, керамики, кубического нитрида бора, алмазного инструмента.
Высокие скорости (300–900 м/мин) применяют при токарной обработке изделий из чугуна инструментами с минералокерамическими пластинами; из стали – инструментами с пластинами из минералокерамики, твердого сплава, в том числе с различными покрытиями, алмазными инструментами со скоростью резания 600–3600 м/мин.
Сверление чугуна и стали твердосплавным инструментом может проводиться со скоростью до 150 м/мин, а токарная обработка этих материалов режущей керамикой до 1400 м/мин.
Применение высокоскоростного фрезерования позволяет упростить управление процессом достижения размера и качества поверхности, обеспечить обработку тонкостенных деталей.
Высокая термостойкость минералокерамики позволяет применять ее в качестве режущего инструмента для ВСО, хотя возможно использование твердых сплавов с карбидом вольфрама, а также с титановым покрытием.
При обработке нетрадиционных материалов эффективно применение высокоскоростного фрезерования (скорость резания до 10 000 м/мин и подача до 30 м/мин). Например, при обработке алюминия и пластмасс производительность обработки возрастает на 200…600%, а при обработке других легких металлов и сплавов – на 150…400%. Скоростная токарная обработка нашла свое применение при изготовлении деталей малых размеров. При обработке волокнистых, полимерных композитов целесообразно применение скоростного сверления.
Скоростное зубофрезерование твердосплавными червячными фрезами эффективно при получистовой и чистовой обработке закаленных зубчатых колес. Перспективно также скоростное предварительное нарезание зубьев на незакаленной заготовке.
При обработке абразивных и легкометаллических и неметаллических материалов применяются поликристаллические (зернистые) алмазы.
Необходимость повышения производительности и точности обработки, снижения ее стоимости предопределяют расширение областей применения абразивной обработки (шлифования) вместо операций точения, фрезерования, строгания. Прогнозы показывают, что в ближайшие 20 лет 25% процессов, выполняемых в настоящее время лезвийными инструментами, и около 50% процессов чистовой обработки будут заменять шлифованием.
Повышение производительности и снижение трудоемкости шлифования достигается:
· интенсификацией обработки и применением новых абразивных материалов (скоростное и силовое шлифование);
· концентрацией кругов, совмещением операций и переходов (многокруговые, торцекруглошлифовальные станки и т.п.);
· полной автоматизацией загрузки-выгрузки обрабатываемых деталей;
· сокращением времени на промежуточные контрольные замеры деталей в результате оснащения станков приборами активного контроля.
В будущем перспективно внедрение ленточного шлифования, обеспечивающего повышение производительности в 3–7 раз по сравнению с обычным шлифованием, при этом обеспечивается более высокая износостойкость изделий при эксплуатации.
Расширяется область применения кругов из нитрида бора и алмазных шлифовальных кругов. Так, производительность при шлифовании кругами из нитрида бора повышается в 5 раз по сравнению со шлифованием кругами из карбида кремния.
Развитие абразивных инструментов и материалов связано:
· с совершенствованием существующих и созданием новых абразивных материалов и инструментов;
· повышением стабильности качества материалов и инструментов;
· расширением использования инструментов из высокотвердых материалов, новых структур шлифовальных кругов с применением тонких волокон из искусственных кристаллов;
· с применением шлифовальных кругов, которые имеют тройное увеличение эластичности по сравнению с существующими в настоящее время, а также кругов с дефинированной геометрией зерен, постоянством положения и неизменяющимся качеством по всему объему круга.
Совершенствование электрокорунда намечается путем увеличения выпуска белого электрокорунда новых марок 15А и 16А, белого электрокорунда повышенного качества марок 44А и 25А, сложнолегированного корунда марки 91А, применение которого позволит повысить производительность на 10–20%.
Предусматривается расширение области применения алмазно-абразивного инструмента, работающего при шлифовании со скоростью 60–80 м/сек, а при резке металла – со скоростью 100–120 м/с.
Предполагается, что внедрение новых конструкционных материалов повышенной прочности и твердости, стойких к стиранию и износу, может оказать стимулирующее воздействие на развитие шлифования в большей степени, чем на токарную обработку. При обработке материалов, в том числе искусственных, более интенсивно стали применяться хонингование и притирка.
Шлифовальные круги из кубического нитрида бора с керамической связкой, высокопористые круги, круги для станков с ЧПУ отличаются высокой стойкостью и стабильностью шлифующих свойств. Для шлифования перспективно использование кругов из легированных высококачественных электрокорундов, сферокорунда и монокорунда высокой чистоты, синтетических монокристаллических высокопрочных термостойких алмазов, новых видов поликристаллических синтетических алмазов и алмазосодержащих композитных материалов. Новые связки для абразивных материалов расширяют возможности высокоскоростного шлифования.
Технологическое оборудование
При создании нового технологического оборудования получили развитие три направления: создание высокоскоростного и высокопроизводительного оборудования, поиск конструктивных решений сверхточных станков, совершенствование мехатронных систем.
При создании новых станков используются следующие направления в проектировании (табл. 4.1).
При определении технических характеристик проектируемых высокоскоростных станков руководствуются следующим [6]:
· частота вращения шпиндельных узлов должна составлять
100 000 об/мин и более при точности 1…2 мкм;
· улучшение динамических характеристик станков и уменьшение тепловых деформаций;
· создание надежной микропроцессорной системы контроля состояния режущего инструмента;
· повышение эффективности отвода стружки из зоны резания (например, при фрезеровании алюминиевых сплавов со скоро-
Таблица 4.1
Тенденции развития станкостроения
Требования к металлорежущему оборудованию | Свойства оборудования и организационные меры, обеспечивающие выполнение требований |
1 | 2 |
Гибкость, позволяющая соответствовать изменяющимся требованиям рынка | Гибкость оборудования и системы управления. Легкость и возможность оперативного изменения структуры производственной системы и отдельных единиц оборудования. Интеграция сведений о работе оборудования, качестве продукции и других данных на всех уровнях управления. Совместимость программного обеспечения для разных CAD/CAM/CAE-систем. |
Постоянное повышение производительности путем совершенствования процессов, связанных с работой оборудования, персонала и систем управления | «Дружественность» программного обеспечения к обслуживающему персоналу. Доступность данных, собранных системами контроля, управления и другими, для анализа и выработки управленческих решений. Агрегатно-модульный принцип построения оборудования и систем управления для возможности диверсификации производства. Возможность быстрой интеграции производства. Легкость и простота обслуживания. Сокращение сроков обучения персонала и внедрение новой техники. Обеспечение эффективного использования оборудования, сокращение эксплуатационных затрат. |
Сокращение стоимости изготовления едини- цы продукции, т.е. повышение прибыли от капиталовложений в производство | Приобретение оборудования только с необходимыми техническими параметрами и технологическими возможностями. Увеличение среднего времени наработки на отказ и минимизация среднего времени ремонта оборудования. Повышение производительности оборудования. Максимальное использование основных фондов. Получение максимальной прибыли от капиталовложений в технологию, оборудование, организацию производства и управление. |
Продолжение табл. 4.1
1 | 2 |
Повышение конкурентоспособности используемых технологий, оборудования, систем управления, что дает уверенность в поставке заказчику высококачественной продукции и обеспечение сервисных услуг | Оказание заказчику услуг при изменении технологий и организации производства. Поддержка заказчика в течение всего периода жизненного цикла оборудования (CALS-технологии). Оперативная поддержка заказчика и готовность к сотрудничеству. Разработка проблемно-ориентированных систем проектирования изделий и комплексных требований к их внедрению. Стратегия агрегатно-модульного построения оборудования и открытой архитектуры систем управления. Объединение технического и финансового управления проектом при решении комплексных задач реструктуризации производства. |
стью 3000 м/мин при мощности привода 100 кВт выход стружки составляет 1000 кг/ч);
· длительное сохранение точности основных узлов, что предполагает новые подходы к выбору материалов и основных подсистем станка;
· ужесточение требований к технике безопасности в целях исключения травмирования обслуживающего персонала и повреждения станка летящей стружкой, осколками инструмента и т. п. В связи с этим изменяются подходы к выбору механизмов зажима (геометрическое замыкание вместо силового) и к балансировке быстровращающегося инструмента или заготовки;
· оснащение станков приводами и системами управления с повышенным быстродействием;
· оптимизация геометрических параметров инструмента в зависимости от свойств обрабатываемого материала.
В связи с развитием технологий, реализующих нанотехнологии, производится поиск конструктивных решений сверхточных станков.
Для фрезерных станков на современном этапе характерно повышение уровня автоматизации, превращение их во фрезерные обрабатывающие центры, выполняющие комплексную обработку заготовок (фрезерование, сверление, растачивание, строгание) с пяти сторон за один установ. В этом случае операция точения деталей больших размеров, выпускаемых мелкими партиями, может быть заменена операцией фрезерования на таких станках.
На обрабатывающих центрах выполняют операции сверления деталей, выпускаемых большими партиями, с небольшим объемом сверлильных переходов. При оснащении станка автоматической многошпиндельной сменной сверлильной головкой производят сверление деталей и с большим объемом сверлильных переходов. Шлифовальная операция (как переход) также может быть выполнена на фрезерной операции (с помощью шлифовальной головки, интегрированной в обрабатывающий центр).
Перспективы развития шлифовальных станков связаны с концентрацией выполняемых на станке операций. Для этого применяются шлифовальные обрабатывающие центры, оснащенные автоматической сменой шлифовальных кругов и автоматической системой контроля за настройкой станка и процессом шлифования при помощи встроенных контрольно-измерительных устройств.
Наметилась тенденция оснащения координатно-шлифовальных станков двухшпиндельными бабками, превращая тем самым их в обрабатывающие центры.
Оснащение шлифовальных станков графическими дисплеями и многопроцессорными устройствами с развитым программным обеспечением значительно повышает уровень их автоматизации.
В перспективе ожидается интенсивная модернизация и повышение уровня автоматизации фасонно-отрезных станков, широкое применение программного управления, уменьшение вибрации при отрезке за счет использования полимербетона для станин отрезных станков с ленточными пилами.
Применение станков с ЧПУ
Для развития станков с ЧПУ характерно:
· расширение функциональных возможностей систем ЧПУ, приводящее к использованию модулей диагностирования, измерения размеров детали, контроля состояния инструментов, анализа результатов и автоматической коррекции управляющей программы в процессе обработки и т.д.;
· повышение уровня автоматизации различных типов станков, концентрация операций и использование на одном станке различных технологий обработки;
· расширение области применения переналаживаемых автоматических линий и агрегатных станков, управляемых УЧПУ типа CNC, что обеспечивает быструю переналадку оборудования.
Продолжается создание многошпиндельных обрабатывающих центров, оснащение их независимыми (вертикальной и горизонтальной) шпиндельными бабками, программно-управляемыми встроенными или накладными глобусными столами. В данном случае предполагается, что темпы роста технологических возможностей новых металлорежущих станков, их производительности, точности, надежности и т.п. будут опережать темпы роста стоимости станков. При этом ускорение процесса смены моделей выпускаемых машин и сроков освоения новых моделей, способность изготовителя приспосабливаться к требованиям потребителя играет бόльшую роль для конкурентоспособности станков, чем только рост их производительности.
Дата добавления: 2019-02-12; просмотров: 321; Мы поможем в написании вашей работы! |
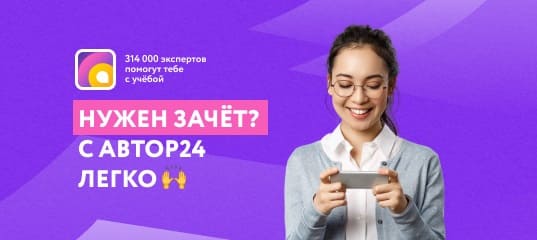
Мы поможем в написании ваших работ!