IV. Тенденции развития технологии
Механообрабатывающего производства
Потребности рынка диктуют переход к более высокой точности обработки на станках. Ранее точность обработки, например, автомобильных деталей, составляла 10 мкм, а у сверхточных деталей достигала 1 мкм. В настоящее время точность чистовой обработки возросла до 0,1 мкм и даже 0,01 мкм. Наряду с традиционными точными изделиями (детали оптической техники, диски памяти компьютеров, аэростатические и жидкостные подшипники, детали насосов и т.п.) в номенклатуру изготавливаемых изделий входят детали медицинской техники, оптических систем, устройств для биологических исследований и др. Допускаемая погрешность формы таких деталей составляет 0,01…0,1 мкм (10…100 нм), а шероховатость Ra = 0,002…0,01 мкм (2…10 нм).
Одновременно с увеличением точности обработки должна возра-стать производительность оборудования.
В настоящее время актуальными становятся тенденции в развитии технологии, оборудования, оснастки, режимов обработки.
Технология механообработки
В мелкосерийном механообрабатывающем производстве получают распространение принципы построения технологии, характерные для серийного и крупносерийного производств. Это способствует концентрации операций, расширению области применения многошпиндельных и многопозиционных станков, выполняющих различные по характеру операции.
Для современного этапа развития машиностроительного производства наряду с обработкой резанием характерно широкое применение электро- и физико-химических, а также комбинированных методов обработки особенно для изготовления деталей из труднообрабатываемых материалов и деталей сложной формы. Прогресс в этой области связан с совершенствованием лазерной, электроэрозионной, ультразвуковой, абразивно-эрозионной, абразивно-электрохимической, абразивно-струй-ной обработки и др. [6]. Наиболее часто применяют лазерную и электроэрозионную обработку, получение деталей из порошковых материалов.
|
|
Рациональными областями применения нетрадиционных методов обработки являются операции, для которых использование резания экономически неэффективно или технически невозможно.
Совершенствование лазерной обработки происходит в области линейного и контурного разрезания хрупких и твердых материалов – стекла, керамики, кварца, а также текстиля, бумаги, картона, пластмасс толщиной 3…5 мм. В этих случаях лазерная обработка значительно эффективнее обработки резанием.
Использование лазера для получения сквозных отверстий в листовой стали толщиной до 12 мм не приведет к значительному сокращению парка сверлильных станков. Однако в долгосрочной перспективе ожидается, что на операциях прошивки сквозных отверстий лазер сможет полностью заменить сверлильные станки.
|
|
Медь и благородные металлы, обладающие высокой теплопроводностью, пригодны для резки лазером при толщине материала до 0,2–0,5 мм. Для обработки алюминиевых сплавов, имеющих высокую отражающую способность и теплопроводность, используются лазеры большой мощности. Титан, с трудом поддающийся обработке резанием, успешно обрабатывается лазером. В свете последних научных открытий и создания новых технологических методов использования лазера не только для резки материала, но и для формообразования изготавливаемых деталей, становится ясно видно, что лазерная технология обработки материалов имеет все большее распространение. При этом технологические комплексы для лазерной обработки оснащаются автоматическими системами, позволяющими создавать на базе этих комплексов гибкие автоматизированные модули. Такие модули можно встраивать в ГПС механообработки.
Обработка лазером имеет достаточно широкие перспективы, позволяющие ей в скором будущем заменить вырезку деталей по контуру и сверление сквозных отверстий.
|
|
Электроэрозионная обработка эффективна при обработке металлических малогабаритных заготовок сложной формы и высокой точности (5…6 квалитет), в том числе закаленных. Для уменьшения энергозатрат и повышения производительности электроэрозионную обработку сочетают с другими видами обработки – резанием, химической и др.
Порошковая металлургия в некоторых областях промышленного производства занимает лидирующее положение, например при производстве твердосплавных пластин или твердосплавного режущего инструмента. Революционный прорыв в порошковой металлургии связывают с внедрением нанопорошковых технологий. Свойства изделий из нанопорошков будут намного превосходить свойства изделий, полученных из обычных порошков.
В последние годы обработку резанием для повышения производительности заменяют обработкой давлением, например для получения заготовок малогабаритных зубчатых колес.
Расширяется область применения нетрадиционного метода обработки – метода тонкого (размерного) пластического деформирования.
Таким образом, при анализе методов обработки можно сделать следующий вывод: электрические методы обработки, обработка давлением, холодное и горячее прессование, методы порошковой металлургии лишь частично заменят обработку резанием, и, как правило, в специальных областях.
Обработка резанием вследствие ее широких технологических возможностей сохранит приоритет среди других методов обработки.
Дата добавления: 2019-02-12; просмотров: 194; Мы поможем в написании вашей работы! |
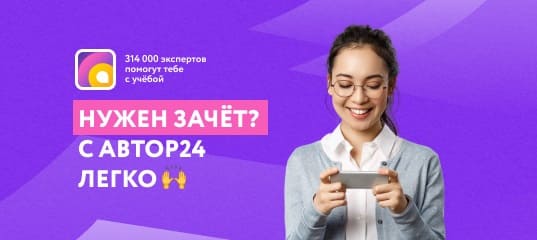
Мы поможем в написании ваших работ!