Маркировка твердости в соответствии с ГОСТ 52587-2006
Новая | Старая | Степень твердости |
F | ВМ1 | Весьма мягкий |
G | ВМ2 | |
H | М1 | Мягкий |
I | М2 | |
J | М3 | |
K | СМ1 | Среднемягкий |
L | СМ2 | |
M | С1 | Средний |
N | С2 | |
O | СТ1 | Среднетвердый |
P | СТ2 | |
Q | СТ3 | |
R | Т1 | Твердый |
S | Т2 | |
T,U | ВТ | Весьма твердые |
V,W,X,Y,Z | ЧТ | Чрезвычайно твердые |
Таблица 2.20
Обозначение структуры [42]
1-2-3-4 | Закрытая |
5-6-7 | Средняя |
8-9-10 | Открытая |
11-12-13 | Высокопористая |
Таблица 2.21
Маркировка связок в соответствии с ГОСТ 52588-2006 [5]
Новая | Старая | Тип связки |
V | K | Керамическая |
B | Б | Бакелитовая |
BF | БУ | Бакелитовая с наличием упрочняющих элементов |
B4 | Б4 | Бакелитовая с графитовым наполнителем |
Н ормирование операций
Техническое нормирование в широком смысле этого понятия представляет собой установление технически обоснованных норм расхода производственных ресурсов: энергии, сырья, материалов, инструмента и рабочего времени.
Особенно важной задачей, решаемой при проектировании технологических процессов, является задача технического нормирования рабочего времени.
Задачами технического нормирования являются выявление резервов рабочего времени и улучшение организации труда на предприятии, установление правильной меры труда(т.е. определение нормы времени) и в конечном счете – повышение производительности труда и увеличение объема производства [17].
|
|
Технически обоснованная норма времени – это время, необходимое для выполнения единицы работы, установленное расчетом исходя из рационального использования в данных производственных условиях труда рабочего (живого труда) и орудий труда(овеществленного труда) с учетом передового производственного опыта.
Техническое нормирование (аналитический метод определения нормы времени) – это совокупность методов и приемов по выполнению резервов рабочего времени и улучшения организации труда технологической операции.
Разработка технологических операций и процессов – задача многовариантная. Выбор оптимального варианта производится сравнительным анализом технико-экономических показателей. Одним из таких показателей является технически обоснованная норма времени.
При техническом нормировании технологическая операция делится на переходы, приемы и движения машинные, машинно-ручные и ручные. Перед расчетом времени производится анализ структуры операции с целью ее улучшения путем: исключения всех лишних приемов и движений, без которых может быть успешно выполнена; сокращения пути движения рабочего; замены утомительных приемов более легкими; обеспечения выполнения ручных приемов работы во время автоматической подачи; освобождения рабочего от выполнения подсобных работ (подаче заготовок на рабочее место, заточки инструмента); применения многоместных и быстродействующих приспособлений; прогрессивных режимов резания.
|
|
Норма времени рассчитывается на каждую операцию отдельно, в зависимости от организационно-технических условий (тип производства, организационные формы операций и процесса, режущий инструмент и режимы резания, конструкции приспособления и способ установки заготовки, методы и средства контроля).
Во всех типах производства (единичном, серийном и массовом) определяется норма штучного времени – Тшт.
В серийном производстве определяются дополнительно еще две нормы времени: норма подготовительно-заключительного времени и норма штучно-калькуляционного времени.
Рассмотрим каждую из них. Норма штучного времени (Тшт) или просто штучное время определяется в полной форме по следующей формуле:
(2.128)
где tосн – основное время, мин; tвсп – вспомогательное время, мин; tорг.обс – время на организационное обслуживание, мин; tтех.обс – время на техническое обслуживание, мин; tотд. – время на отдых и естественные надобности, мин. [5].
|
|
Для сокращения формулы (2.128) вводятся следующие определения:
, (2.129)
где tоп – оперативное время, мин.
, (2.130)
где Tдоп – дополнительное время, мин.
Время основное tосн определяют за каждый технологический переход исходя из наиболее рациональных режимов резания.
, мин (2.131)
где Lр.х. – длина рабочего хода инструмента или стола станка в направлении подачи.
, мм (2.132)
где l – длина обрабатываемой поверхности, определяемая по чертежу детали, мм; lвр, lп – соответственно дополнительная длина на врезание (расстояние от обрабатываемой поверхности, с которой режущий инструмент переключается на рабочую подачу) и перебег (расстояние для схода инструмента с обрабатываемой поверхности, после чего инструмент отводится с ускоренной подачей), определяемая геометрией режущего инструмента [5], [табл. 4.1–4.3]; i – число рабочих ходов.
|
|
Минутная подача (мм/мин)
, (2.133)
где Sо, мм/об – подача на оборот детали или режущего инструмента (точение, сверление, зенкерование, развертывание); S z, мм/зуб – подача на зуб для многолезвийного инструмента (фрезерование всеми видами фрез); z – число зубьев; n, мин-1 – число оборотов.
Длины на врезание и перебег для каждого вида обработки приведены в [18], а их значения в [5]. При обработке методом пробных рабочих ходов со взятием пробных стружек длина хода на взятие пробной стружки
(lпр. стр.) также входит в длину рабочего хода и определяется по [5].
При обработке на токарных многорезцовых станках и копировальных полуавтоматах последовательным действием продольного (Lр.х.прод, Sпрод) и поперечного (Lр.х.поп, Sпоп) суппортов tосн технологического перехода определяется суммированием основного времени суппортов. Причем Lр.х. суппорта назначается по наиболее протяженной поверхности.
При шлифовании абразивный инструмент (деталь) совершает продольное возвратно-поступательное (L, S, мм/мин) и поперечное (L, S, мм/дв.х) движения. Причем Lдв.х = 2Lр.х..
Число двойных ходов
. (2.134)
При нарезании резьбы гребенчатой резьбовой фрезой
, (2.135)
где d – наружный диаметр резьбовой поверхности, мм, Sм – минутная подача, мм/мин.
Вспомогательное время (tвсп) назначается на все приемы рабочего, связанные с обработкой каждой детали:
, (2.136)
где tуст –время на установку, выверку, закрепление заготовки и снятие детали поле выполнения операции механической обработки на данном станке; tупр –время на управление станком: включение и выключение станка, СОЖ; tподв – время на подвод и отвод инструмента или детали; tизм – время на контрольные измерения результатов обработки, зависит от величины
и точности исполнительного размера и типа измерительного инструмента, мин (табл. 2.29); tпер – время, связанное с переходом.
Напомним, что переход – это часть технологической операции, связанная с постоянством пяти признаков: обрабатываемая поверхность, режущий инструмент, скорость, подача и глубина резания. Если при выполнении технологической операции изменяется хотя бы один признак из вышеперечисленных, то речь идет о новом технологическом переходе. Появление нового перехода всегда связано с затратами времени.
Пример 1. Если после обтачивания наружной поверхности вала на каком-либо участке необходимо прорезать канавку, то необходимо отвести резцедержатель после обточки поверхности в исходное положение, повернуть его, приготовив канавочный резец, установленный в резцедержателе, в положение, пригодное для обработки, и подвести к намеченной к обработке канавке. Если для прорезания канавки необходимо изменить режимы обработки, то после обтачивания надо остановить вращение шпинделя, изменить число оборотов, установить значение поперечной подачи и снова включить вращение шпинделя. Все эти затраты времени входят в tпер .
Для различных методов обработки при оценке составляющих tпер можно воспользоваться данными, приведенными в табл. 2.30–2.33 настоящего пособия и в [5].
Различные схемы построения станочных операций (одно- и многоместные; последовательного, параллельного, параллельно-последовательного выполнения) дают возможность перекрытия (совмещения) вспомогательного времени или его составных частей основным(машинным) временем.
В этом случае tвсп и его составляющие нормируются, но в штучное время не входят.
Перекрытие составляющих вспомогательного времени основным возможно при выполнении следующих мероприятий. Например, tуст при обработке на многопозиционном станке с отдельной загрузочной позицией; при обработке на автоматических линиях с загрузкой заготовки при непрерывном процессе и др.; tизм, если время обработки значительно превышает время на измерение и при использовании средств активного контроля; tупр и tсм.ин в большинстве случаев не удается перекрыть основным временем, однако снизить его можно выбором типов станков, организационными формами инструментальной наладки и смены инструмента с учетом стойкости каждого инструмента.
Дополнительное время, мин
, (2.137)
где tорг.обс – время организационного обслуживания рабочего места, которое включает в себя следующие затраты времени:
– осмотр и опробывание оборудования перед началом смены (проверка заземления, включение и выключение станка и т. д.);
– раскладка инструмента в начале смены и уборка его по окончании смены;
– получение инструктажа и наряд-заказа от мастера в начале и в течение смены;
– уборка стружки в конце смены, смазка и очистка станка в конце смены, уборка рабочего места в конце смены;
tтех.обс – время технического обслуживания рабочего места, которое включает в себя следующие затраты времени:
– смена затупившегося инструмента или правка шлифовального инструмента;
– регулировка и подналадка станка в процессе работы(в течение смены);
– заправка инструмента оселком(снятие нароста на режущих поверхностях);
– уборка стружки в течение смены (в большинстве случаев речь идет о периодическом удалении сливной стружки из поддона токарного станка, со стола сверлильного, фрезерного, строгального станков);
– загрузка СОЖ, маслом и др.;
tотд – время кратковременного отдыха и личные надобности оператора, принимается 2,5 % tоп.
В укрупненных расчетах время организационного и технического обслуживания принимается суммарным временем обслуживания
. (2.138)
Оперативное время . Таким образом, штучное время обработки одной детали
, (2.139)
где аобс = (6–8) и аотд = 2,5 – соответственно коэффициенты, определяющие процентное соотношение времени обслуживания и отдыха от tоп.
Таблица 2.22
Дата добавления: 2019-02-12; просмотров: 556; Мы поможем в написании вашей работы! |
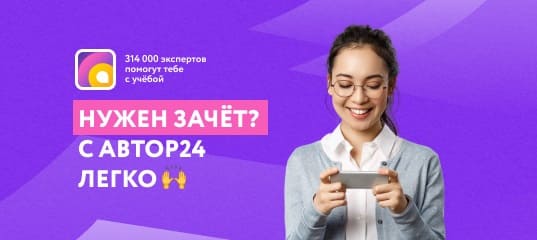
Мы поможем в написании ваших работ!