Геометрические параметры сверл
Для нашего случая (пример 1) выбираем марку твердого сплава Т5К10.
3. Определяем паспортное значение подачи, на которой будет осуществляться обтачивание. По табл. 11 с. 266 [2] выбираем интервал подач, на которых можно вести обработку: 0,5÷0,9 мм/об. Теперь необходимо определить паспортные значения подач, входящих в этот интервал, по методике, описанной ранее.
(2.17)
φ 23 = 56, φ = 1,19. (2.18)
Такое значение φне входит в ряд нормализованных знаменателей, приведенных в табл. 13, с. 254 [4], однако иногда станкостроительным заводам дается разрешение на использование промежуточных значений φ,поэтому воспользуемся значением φ = 1,19 (из расчета по паспортным значениям). Тогда:
(2.19)
Для нашего случая этих расчетов достаточно, т. к. S16 = 0,67 мм/об находится в середине рекомендуемого интервала подач.
Итак, принимаем S пасп = 0,67 мм/об.
4. Определяем расчетную скорость резания по формуле (2.20) [2, с. 268]
, (2.20)
где , m , x , y – эмпирический коэффициент и показатели степени, К V – поправочный коэффициент на скорость резания, Т – стойкость инструмента, t – глубина резания, S – паспортное значение подачи мм/об.
Значения , m , x , y определяем в табл. 17, с. 269[2]:
= 350;
m = 0,2; x = 0,15; y = 0,35.
|
|
Стойкость инструмента (Т) при одноинструментной настройке принимаем Т= 45 мин [2, с. 268].
Поправочный коэффициент на скорость резания определяется по формуле (2.21):
(2.21)
где – коэффициент, учитывающий влияние материала заготовки;
– коэффициент, учитывающий состояние поверхности заготовки;
– коэффициент, учитывающий материал инструмента.
Коэффициент определяем по табл. 1, с. 261 [2]:
(2.22)
где – коэффициент, характеризующий группу стали по обрабатываемости;
– временное сопротивление материала заготовки.
По табл. 2, с. 262 [2] принимаем значения = 1,0; nV = 1,0.
Значения можно определить для различных сталей по [6], при этом для стали 45 σв = 610 МПа.
(2.23)
По табл. 5, с. 263 [2] определяем значение коэффициента .
По табл. 6, с. 263 [2] определяем значение коэффициента .
Тогда
(2.24)
Расчетная скорость резания:
(2.25)
5. Определяем расчетное число оборотов шпинделя станка
|
|
(2.26)
6. Определяем паспортное число оборотов по методике, изложенной ранее
(2.27)
Этот показатель входит в число стандартных.
Определяем паспортные значения чисел оборотов:
(2.28)
Между расчетным и паспортным числом оборотов существует разница в 4,13 % (n20 = 1010 об/мин и n расч = 968,3 об/мин) то принимаем
n пасп = 1010 об/мин.
7. Определяем фактическую скорость резания
(2.29)
8. Определяем мощность, потребную на резание [2, с. 271]:
(2.30)
где – тангенциальная составляющая силы резания, Н;
– фактическая скорость резания, м/мин.
(2.31)
где – поправочный коэффициент;
(2.32)
где – поправочный коэффициент для стали и чугуна, учитывающий влияние качества обрабатываемого материала на силовые зависимости;
– поправочные коэффициенты, учитывающие влияние геометрических параметров режущей части инструмента на составляющие силы резания при обработке стали и чугуна;
– коэффициент, учитыва-ющий значение главного угла в плане (φ);
– коэффициент, учитыва-ющий значение переднего угла (γ);
– коэффициент, учитывающий значение угла наклона главного лезвия (λ);
– коэффициент, учитывающий величину радиуса при вершине резца(r).
|
|
По табл. 22, с. 273 [2] определяем значение коэффициента и показателей степени x , y , n
= 300; x = 1,0; y = 0,75; n = – 0,15.
По табл. 9, с. 264 [2] определяем значение коэффициента :
(2.33)
где – предел временного сопротивления, для стали 45 σв = 610 МПа,
n – показатель степени n = 0,75
(2.34)
Перед тем, как принимать значения поправочных коэффициентов, учитывающих геометрические параметры резцов, необходимо учесть следующие рекомендации, приведенные в [18].
Главный угол в плане (φ) на проходных токарных резцах общего назначения затачивают равным 45°. С целью повышения жесткости резца его можно заточить равным 60°. На проходных токарных резцах подрезного типа этот угол затачивается равным 90°. Заточка резцов с φ < 45° практически мало применяется, поскольку это приводит к появлению вибраций и, как следствие, к ухудшению качества обработанной поверхности.
|
|
Передний угол (γ) у проходных резцов, предназначенных для резания с подачами S ≤ 0,15 мм/об, затачивают равным 15°. Передняя поверхность при этом может быть оформлена в виде плоскости.
У резцов, предназначенных для резания металлов с подачами
S > 0,15 мм/об, переднюю плоскость также затачивают под углом γ = 15°, но вдоль лезвия под углом γ = 0° выполняют фаску шириной f = 0,15÷1,0 мм. С увеличением подачи увеличивается динамическая нагрузка на лезвие резца. Чтобы укрепить лезвие при работе с подачами S > 0,25 мм/об, вдоль лезвия затачивается фаска шириной f = 1мм под углом γ = - 5°.
Угол наклона главной режущей кромки (λ)у проходных токарных резцов берут в пределах λ = ±3°. На технологических операциях, выпол-няемых с подачей S ≥ 0,15 мм/об, предпочтительнее λ = +3°. При этом срезаемая стружка отводится от резца направо от рабочего, как предусмотрено правилами охраны труда. На чистовых операциях (для подач S <0,15 мм/об), когда срезаемая стружка мелкая и не представляет опасности нанесения травм, угол λ = - 3°.
Закругление вершины резца (r) вместе сопряжения главного и вспомогательного лезвия обязательно. Радиус закругления вершины токарных резцов рекомендуется брать в пределах r =0,2÷1,0мм. Чем больше радиус закругления, тем выше стойкость резцов и меньше высота микронеровностей обрабатываемой поверхности. Вместе с тем, чрезмерное увеличение радиуса закругления (r >1мм) при малой глубине резания уменьшает фактическое значение главного угла в плане (φ).
По табл. 23, с. 275 [2] определяем значения коэффициентов:
:
для φ = 30°
для γ = 0°
для λ = 0°
для r = 1,0 мм
Определяем поправочный коэффициент :
(2.35)
Определяем тангенциальную составляющую силы резания:
(2.36)
Определяем мощность, потребную на резание:
(2.37)
Определяем выполнение условия
N рез ≤ η· N эл ; (2.38)
где η – КПД передачи от электродвигателя к шпинделю, η = 0,85÷ 0,95.
3,55 < 0,9·11; 3,55 < 9,9. (2.39)
Условие (2.38) выполняется, следовательно, рассчитанный режим резания принимается.
Пример 2. Сверление (рассверливание)
Пояснения к обработке. При получении отверстия невысокой точности (например, под крепежные болты) операция «сверление» носит свое название только при обработке отверстий d ≤ 7,5 мм. Формообразование отверстий большего диаметра уже осуществляется рассверливанием. Это связано с тем, что на сверле существует поперечная кромка для увеличения его жесткости, и она не является режущей. По справочнику инструментальщика [9] сверла до диаметра 7,5 мм выпускаются без поперечной кромки. Обработка отверстий диаметром больше 7,5 мм проводится операцией «рассверливание», чтобы исключить негативное действие (только трение без всякого резания) поперечной кромки.
В табл. 2.11 приводятся данные о величине поперечной кромки сверл различных диаметров.
Таблица 2.11
Геометрические параметры сверл
Диаметр сверла | Подточка поперечной кромки | |
Длина подточенной поперечной кромки а | Длина подточки l | |
Св. 0,95 до 1,70 | – | |
Св. 1,70 до 3,00 | ||
Св. 3,00 до 7,50 | ||
Св. 7,50 до 9,50 | 1,0 | 2,0 |
Св. 9,50 до 11,80 | 1,2 | 2,5 |
Св. 11,80 до 16,0 | 1,5 | 2,5 |
Св. 16,0 до 20,0 | 2,0 | 3,5 |
Св. 20,0 до 25,0 | 2,5 | 4,5 |
Св. 25,0 до 31,5 | 3,0 | 5,5 |
Св. 31,5 до 40,0 | 3,5 | 6,0 |
Св. 40,0 до 50,0 | 5,0 | 8,0 |
Св. 50,0 до 63,0 | 6,0 | 10,0 |
Св. 63,0 до 71,0 | 7,0 | 12,0 |
Св. 71,0 до 80,0 | 8,0 | 14,0 |
Быстрорежущие стали
Буква Р, с которой начинаются обозначения всех марок быстрорежущих сталей, означает, что это – быстрорежущая сталь. За буквой Р следует цифра, обозначающая содержание вольфрама в процентах. Затем следуют буквы, обозначающие легирующие элементы (М – молибден, Ф – ванадий, А – азот, К – кобальт, Т – титан, Ц – цирконий). За буквой следует цифра, обозначающая среднее массовое содержание элемента в процентах (содержание хрома около 4 % в обозначении марок не указывается). Массовое содержание азота указывается в сотых долях процента. Цифра, стоящая в начале обозначения стали, указывает содержание углерода в десятых долях процента (например, сталь марки 11Р3АМ3Ф2 содержит около 1,1 % С; 3 % W; 3 % Мо и 2 % V). В табл. 2.12 приведены химические составы наиболее распространенных марок быстрорежущих сталей.
Таблица 2.12
Марки, применяемые для изготовления режущих инструментов
Группа (стандарт ИСО 4957-80) | Марка | Средний химический состав, % | |||||
С | W | Мо | Сг | V | Со | ||
Базовая | Р6М5 Р18 | 0,86 0,78 | 6,0 17,75 | 5,0 до 1 | 4,1 | 1,9 1,2 | до 0,5 |
С увеличенным содержанием С и V | Р6М5ФЗ | 1,0 | 6,2 | 5,0 | 4,1 | 2,5 | до 0,5 |
Содержащая Со | Р6М5К5 Р9М4К8 | 0,9 1,05 | 6,2 9,0 | 5,0 4,0 | 4,1 3,3 | 1,9 2,5 | 5,0 8,0 |
Режущие свойства быстрорежущих сталей определяются объемом основных карбидообразующих элементов – вольфрама, молибдена, ванадия и легирующих элементов – кобальта, азота. Ванадий в связи с малым массовым содержанием (до 3 %) обычно не учитывается, и режущие свойства сталей определяются, как правило, вольфрамовым эквивалентом, равным (W + 2Mo) %. В прейскурантах на быстрорежущие стали выделяют три группы сталей: стали 1-й группы с вольфрамовым эквивалентом до
16 % без кобальта, стали 2-й группы – до 18 % и содержанием кобальта около 5 %, стали 3-й группы – до 20 % и содержанием кобальта 5–10 %. Соответственно различаются и режущие свойства этих групп сталей.
Базовая группа (стали нормальной производительности) предназначена в основном для обработки конструкционных сталей с твердостью до 280 НВ, феррито-перлитных чугунов с твердостью до 220 НВ и цветных сплавов. Основной маркой этой группы является сталь Р6М5, которая предназначена для изготовления большинства режущих инструментов: резцов, фрез, сверл, зенкеров, разверток, протяжек, метчиков, резьбовых плашек, а также значительной части зуборезных инструментов. Режущие свойства инструментов из сталей Р6М5 и Р18 практически равноценны для подавляющего большинства видов инструментов и областей их применения. Сталь Р18 обладает лучшей шлифуемостью и поэтому применяется, когда изготовление инструментов из стали Р6М5 затруднено.
Производственный опыт показывает, что из стали Р18 изготавливают инструменты, при производстве которых осуществляются сложные и точные шлифовальные операции, а именно: корригированные шеверы, зуборезные долбяки для чистовой обработки, шлицевые протяжки, мелкоразмерные метчики.
Инструменты из быстрорежущих сталей с увеличенным содержанием углерода и ванадия составляют группу повышенной износостойкости. Сталь Р6М5ФЗ обладает износостойкостью на 30...40 % больше, чем Р6М5, но уступает этой стали по шлифуемости. Сталь Р6М5ФЗ применяется с целью повышения стойкости инструментов, таких как резцы, сверла, зенкеры и т. п.
Быстрорежущие стали повышенной производительности, содержащие кобальт, предназначены для обработки конструкционных сталей
и перлитных чугунов с твердостью более 280 НВ. Применение стали Р6М5К5 обеспечивает по сравнению с Р6М5 рост скорости резания в среднем на 20 %, или увеличение количества периодов стойкости инструментов в 1,5...3 раза. Сталь Р9М4К8 обладает повышенной износостойкостью по сравнению с Р6М5К5, но уступает ей по прочности, шлифуемости и является более дорогой. Она применяется, когда режущие свойства стали Р6М5К5 недостаточны. В отдельных случаях обработка деталей высокой твердости осуществляется с применением стали Р12МЗФ2К8. Эта сталь превосходит по износостойкости Р9М4К8, но уступает ей по прочности
и шлифуемости и значительно дороже. Целесообразность применения стали Р12МЗФ2К8 на конкретных операциях определяется предварительным испытанием.
Основной наиболее применяемой кобальтсодержащей быстрорежущей сталью является сталь Р6М5К5.
При обработке конструкционных сталей и перлитных чугунов с твер-достью до 280 НВ применение кобальтовых быстрорежущих сталей на режиме резания, характерного для стали Р6М5, не рекомендуется, так как не обеспечивает повышение стойкости инструмента. Кобальтовые быстрорежущие стали оказываются эффективными при повышенных значениях режима резания. Например, применение фасонных резцов из стали Р6М5К5 обеспечивает при обработке автоматных сталей со скоростями более 30 м/мин повышение стойкости в 1,5...2 раза по сравнению со сталью Р6М5 или позволяет повысить скорость резания на 15...20 %. Зубофрезерование червячными фрезами из сталей Р6М5К5 и Р9М4К8 может осуществляться со скоростями резания, которые по сравнению со сталью Р6М5 больше на 30 %.
Существуют марки порошковых быстрорежущих сталей: Р6М6ФЗ-МП, Р7М2Ф6-МП, Р12МФ5-МП, Р6М5К5-МП, Р9М4К8МП, Р12МЗК5Ф2-МП. Они имеют однородную структуру, значительно прочнее и лучше шлифуются по сравнению со сталями того же химического состава, изготовленными по обычной технологии. Это позволяет изменить легирование порошковых быстрорежущих сталей, увеличив в них содержание углерода и ванадия и повысив таким образом износостойкость инструментов при достаточной прочности и удовлетворительной шлифуемости. Порошковые быстрорежущие стали позволяют повысить стойкость инструментов в 1,3...2 раза по сравнению с аналогами, получаемыми по обычной технологии (например, Р6М5ФЗ-МП – Р6М5ФЗ; Р6М5К5-МП – Р6М5К5 и др.).
Российские быстрорежущие стали, их зарубежный аналог и химический состав показаны в табл. 2.13.
Таблица 2.13
Российские быстрорежущие стали,
их зарубежный аналог и химический состав
Марка по | Зарубежный аналог | Средний химический состав, % | ||||
Стандарт (страна) | Марка | С | W | V | Со | |
Р6М5 Р18 Р6М5ФЗ | ATM; AIS1 (США) | М2 Т1 М3 | 0,9 0,75 1,0 | 6,4 18 6,4 | 1,9 1,0 2,5 | – – – |
Р6М5 Р6М5ФЗ Р6М5К5 | DIN 17350-80 (Германия) | S6-5-2 S6-5-3 S6-5-2-5 | 0,9 1,0 0,9 | 6,4 6,4 6,4 | 1,9 2,5 1,9 | – – 4,8 |
Р6М5 Р18 Р6М5К5 | NFA 35-590-78 (Франция) | 6-5-2 18-0-1 6-5-2-5 | 0,85 0,8 0,85 | 6,0 18 6,0 | 2,0 1,0 2,0 | – – 5,0 |
Р6М5 Р6М5ФЗ Р18 Р6М5К5 | JIS 4403-83 (Япония) | КН-9 КН-52 КН-2 КН-55 | 0,75 1,0 0,8 0,86 | 6,0 6,0 18 6,0 | 2,0 2,5 1,0 2,0 | – – – 5,0 |
Примечание. Во всех сталях содержание, %: Мо – 5 (за исключением сталей Т1, 18-0-1 и КН-2); Сг – 4.
Условие примера 2. Необходимо обработать отверстие в листовой заготовке из стали 45 Ø12 мм. Диаметр сверла выбирает конструктор из стандартного ряда размеров сверл по ГОСТ885-77. Этот ряд включает 340 размеров в интервале 0,25–80 мм [9, табл. 10.2, с. 362]. Заготовка имеет размеры 300×300, толщиной 25 мм. Подобрать оборудование, режущий инструмент и режим обработки.
Решение. Принимаем по [2, табл. 11, с. 20] вертикально-сверлиль-ный станок модели 2Н125 со следующими паспортными данными: nmin =
= 45 об/мин; nmах = 2000 об/мин, число скоростей шпинделя КП = 12;
Smin = 0,1 мм/об; Smах = 1,6 мм/об; число подач шпинделя – KS = 9, мощность электродвигателя привода главного движения – 2,2 кВт. Обработка отверстия может осуществляться в два перехода (операция одна, т. к. выполняется на одном рабочем месте, а переходов два, т. к. изменятся режимы обработки и инструмент).
Первый переход. Производим сверление отверстия диаметром 5 мм. Глубина резания при этом переходе определяется по формуле:
, (2.40)
где – диаметр обрабатываемого отверстия,
.
Для нашего случая t = 2,5 мм.
Определяем интервал подач для обработки отверстия по [2, табл. 25, с. 277]:
S = 0,07 – 0,11 мм/об.
Определяем паспортное значение подачи, лежащее в этом интервале, для выбранного станка. Определяем знаменатель ряда j для выбранного станка
(2.41)
(2.42)
Принимаем паспортное значение подачи
S пасп = 0,1 мм/об.
Определяем расчетную скорость резания при сверлении отверстия Ø5 мм [2, с. 276]:
, (2.43)
где D – диаметр отверстия, D = 5 мм; Т – стойкость сверла, Т = 15мин [2, табл. 30, с. 279]; – общий поправочный коэффициент на скорость резания, учитывающий фактические условия резания; S – подача, мм/об.
(2.44)
где – коэффициент на обрабатываемый материал;
– коэффициент на инструментальный материал;
– коэффициент, учитывающий глубину сверления;
(2.45)
= 1,0 [2, табл. 2, с. 262]
nV = 1,05 [2, табл. 2, с. 262]
(2.46)
(для материала сверла Р6М5) [2, табл. 6, с. 263]
[2, табл. 31, с. 280]
(2.47)
Определяем расчетную скорость резания.
По [2, табл. 28, с. 278] определяем:
С V = 7,0; q = 0,4; y = 0,7; m = 0,2.
(2.48)
Определяем расчетное число оборотов шпинделя
(2.49)
Принимаем по паспорту число оборотов n пасп = 2000 об/мин.
Определяем фактическую скорость резания:
(2.50)
Определяем мощность, потребную на резание, по формуле [2, с. 280]:
(2.51)
где – крутящий момент, определяемый по формуле [2, с. 277]:
(2.52)
(2.53)
n = 0,75 [2, табл. 9, с. 264]
(2.54)
По [2, табл. 32, с. 281] определяем значения коэффициента и показателей степени:
СМ = 0,0345; q = 2,0; y = 0,8.
(2.55)
(2.56)
Поскольку условие
N рез <η· N эл ;
0,24 < 0,9·2,2; 0,24 < 1,98. (2.57)
выполняется, то рассчитанный режим обработки принимается.
Для обработки отверстия Ø12 мм осуществляем второй переход – рассверливание с диаметра 5 мм до диаметра 12 мм.
Подачу принимаем S пасп = 0,1 мм/об (как при сверлении).
Определяем расчетную скорость резания при рассверливании по формуле [2, с. 276]:
(2.58)
где t –глубина резания при рассверливании определяется по формуле:
, (2.59)
где – диаметр окончательно обработанного отверстия (в нашем примере
);
– диаметр отверстия в заготовке, т. е. диаметр предварительно обработанного отверстия (в нашем примере
);
, (2.60)
Определяем значение коэффициента и показателей степени по [2, табл. 29, с. 279]:
С V = 16,2; q = 0,4; x = 0,2; y = 0,5; m = 0,2; KV = 1,24
(определен ранее по формуле 5.37).
(2.61)
Определяем расчетное число оборотов шпинделя
(2.62)
Принимаем по паспорту число оборотов n пасп = nmax = 2000 об/мин.
Определяем фактическую скорость резания:
(2.63)
Определяем крутящий момент при рассверливании по формуле [2, с. 277]:
(2.64)
Принимаем значения коэффициента и показателей степени по [2, табл. 32, с. 281]:
СМ = 0,09; q = 1,0; x = 0,9; y = 0,8;
(определен ранее по формуле 2.54)
(2.65)
Определяем мощность резания по формуле [2, с. 280]:
(2.66)
Условие
N рез <η· N эл ;
0,93 < 0,9·2,2; 0,93 < 2 (кВт) (2.67)
выполняется, следовательно, рассчитанный режим обработки принимается.
Пример 3. Фрезерование торцевой фрезой
Необходимо профрезеровать плоскость шириной 200мм длиной 400мм при глубине резания t = 1,5 мм. Заготовка – отливка корпуса коробки скоростей редуктора из серого чугуна СЧ21. Подобрать оборудование, режущий инструмент и режим резания.
Решение.
По [2, табл. 37, с. 51] принимаем вертикально – фрезерный консольный станок модели 6Р11 со следующими паспортными данными: nmin = 50 об/мин; nmах = 1600 об/мин, число скоростей шпинделя Кп = 16; Smin = 35 мм/мин; Smах = 1020 мм/мин; число подач стола – KS = 16, мощность электродвигателя привода главного движения – N эл = 5,5 кВт.
Принимаем режущий инструмент по [2, табл. 94, с. 187]: торцевая насадная фреза со вставными ножами, оснащенными пластинами из твердого сплава (ВК8 т. к. обработка ведется по чугуну) по ГОСТ 9473-80.
Диаметр фрезы D = 315 мм; высота фрезы – 66 мм; диаметр посадочного отверстия d = 60 мм; число зубьев Z = 30.
По [2, табл. 34, с. 283] принимаем подачу при фрезеровании торцевой фрезой при средней жесткости системы «заготовка – приспособление» 0,2÷0,4 мм/зуб. Принимаем подачу S = 0,3 мм/зуб.
Определяем расчетную скорость резания по формуле [2, с. 282]:
, (2.68)
где D – диаметр фрезы, D = 315 мм; Т – стойкость фрезы, мин; t – глубина резания, мм; Sz – подача на зуб фрезы (Sz =0,3 мм/зуб); В – ширина обрабатываемой поверхности (В = 200 мм); Z – число зубьев фрезы (Z = 30); – общий поправочный коэффициент на скорость резания
(2.69)
[3, табл. 1, с. 261] (2.70)
nV = 1,0 [2, табл. 1, с. 262]
(2.71)
[2, табл. 5, с. 263]
[2, табл. 6, с. 263]
(2.72)
Т = 300 мин [2, табл. 40, с. 290]
Определяем значение коэффициента и показателей степени по [2, табл. 39, с. 288]:
С V = 445; q = 0,2; x = 0,15; y = 0,35; u = 0,2; p = 0; m = 0,32.
(2.73)
Определяем расчетное число оборотов фрезы
(2.74)
Определяем паспортное число оборотов фрезы:
Определим нормализованный знаменатель ряда φ:
(2.75)
n1= nmin = 50 об/мин;
n2= n1· φ = 50· 1,26 = 63 об/мин;
Принимаем паспортное значение числа оборотов фрезы n пасп = 63 об/мин;
Определяем фактическую скорость резания:
(2.76)
Определяем мощность, потребную на резание при фрезеровании, по формуле [2, с. 290]:
(2.77)
где – главная составляющая силы резания (окружная сила), определяемая по формуле [2, с. 282]:
(2.78)
где значения коэффициента и показателей степени определяются в [2, табл. 41, с. 291]:
СР = 54,5; x = 0,9; y = 0,74; n = 1,0; q = 1,0; w = 0.
[2, табл. 9, с. 264] (2.79)
(2.80)
(2.81)
(2.82)
Проверим выполнение условия:
N рез <η· N эл ; 3,1 < 0,85·5,5; 3,1 < 4,7 (2.83)
Поскольку условие выполняется, то рассчитанный режим обработки принимается.
Пример 4. Шлифование
Необходимо подобрать абразивный инструмент и режимы резания для окончательной обработки шейки вала из стали 40Х, закаленной до твердости HRC 50-53. Диаметр шейки вала – 40h6(-0,016)мм, длина L – 210 мм, общая длина вала L 1 – 260 мм, требуемая высота микронеровностей
Ra = 0,8 мкм, припуск на обработку – h = 0,2 мм.
Решение.По [10, табл. 2.62, с. 132] принимаем характеристику круга:
23А 40-Н СМ2 К8. Структуру круга принимаем по [9, табл. 14.6, с. 713] – № 5. по [9, табл. 14.10, с. 721] принимаем форму круга ПП (прямой профиль). Точность изготовления круга – класс А, класс неуравновешенности круга – 2-ой. По [2, табл. 18, с. 29] выбираем для обработки станок круглошлифовальный модели 3М150 со следующими характеристиками:
Максимальный диаметр обрабатываемой заготовки, мм …….....………..100
Максимальная длина заготовки, мм………………….…………………….360
Наибольший размер шлифовального круга, мм…………………… ……..400
Высота круга, мм………………………… …………………………………..40
Частота вращения шлифовального круга, мин-1………………....2350 и 1670
Мощность электродвигателя привода главного движения, кВт……………4
Скорость вращения заготовки, мин-1…………………………….…..100–1000
Для круга диаметром 400 мм скорости вращения на станке:
(2.84)
(2.85)
Несмотря на то, что выбранный нами круг допускает работу на скоростях вращения 35 м/с и 50 м/с, принимаем , так как мощность электродвигателя привода главного движения выбранного станка не велика. Кроме того, мы еще не определили мощность, необходимую для обработки. Таким образом, полная характеристика круга будет следующей:
ПП 400×40×127 23А 40-Н СМ2 5 К8А 2 кл. 35м/с ГОСТ 2424-83.
Назначаем режимы резания.
1) Скорость главного движения резания (шлифовального круга) , тогда число оборотов круга nкр=1670 мин-1.
2) Скорость вращения заготовки [2, табл. 55, с. 301]. Принимаем среднее значение
.
3) Определяем частоту вращения заготовки:
(2.86)
Получаем:
Так как на выбранном станке бесступенчатое регулирование скоростей вращения заготовки, то принимаем расчетное число оборотов.
4) Поперечная подача круга (в справочнике [2] эта величина названа глубиной шлифования) S х =0,005-0,015мм/ход стола [2, табл. 55, с. 301]. Учитывая высокие требования, предъявляемые к точности обработки (поле допуска по h 6 и шероховатости поверхности Ra = 0,8 мкм) принимаем
S х = 0,005 мм/ход.
5) Определяем продольную подачу на оборот заготовки . Для окончательного шлифования принимаем [2, табл. 55, с. 301]
ширина круга Вк равна 40 мм, тогда
6) Определяем скорость движения продольной подачи (скорость продольного хода стола):
(2.87)
На выбранном нами станке предусмотрено бесступенчатое регулирование скорости продольного хода стола в пределах 0,02–4 м/мин, поэтому принимаем
7) Определяем мощность, затрачиваемую на резание [2, с. 300]:
(2.88)
По [2, табл. 56, с. 303] принимаем значения коэффициентов:
r = 0,5; x = 0,5; y = 0,55; q = 0;
(2.89)
8) Проверяем, достаточна ли мощность двигателя шлифовальной бабки. У станка 3М150 N шп = N м· η = 4·0,8 = 3,2 кВт. N рез > N шп , т. е. обработка невозможна (обработка возможна лишь при условии N рез ≤ N шп). Исходя из формулы N рез , можно снизить значение и (или)
. Уменьшим скорость вращения заготовки
из условия N рез = N шп:
(2.90)
Примем
Тогда частота вращения заготовки станет равной 215 мин-1; скорость движения продольной подачи
станет равной 2,58 м/мин. При таких значениях
обработка возможна, так как условие N рез ≤ N шп выполняется.
9) Определяем основное время обработки:
(2.91)
где – длина хода стола, при перебеге круга на каждую сторону равном
– припуск на сторону, по заданию
К – коэффициент точности, учитывающий время на выхаживание, т. е. шлифование без поперечной подачи; при окончательном шлифовании К=1,4.
(2.92)
Пример 5.На внутришлифовальном станке 3К228В шлифуется сквозное отверстие диаметром D з = 60Н7(+0,03) и длиной L = 60 мм. Высота микронеровностей обрабатываемой поверхности Ra = 0,63 мкм. Припуск на сторону h = 0,2 мм. Материал заготовки – сталь 45, закаленная до твердости HRC 45-48. Станок оснащен устройством для активного контроля. Необходимо: выбрать шлифовальный круг, назначить режимы резания, определить основное время.
Решение.По [9, табл. 14.10, с. 721] выбираем круг формы ПВ. При внутреннем шлифовании рекомендуется принимать отношение диаметра круга к диаметру заготовки D к / D з = 0,8–0,9. Принимаем D к / D з = 0,85, тогда D к = 0,85 · 60 = 51 мм. Высоту круга для обрабатываемых отверстий длиной L = 25…75 мм принимают меньшей на 10–15 мм, т. е.
По ГОСТ 2424-83 принимаем круг с параметрами: D к = 50мм;
диаметр посадочного отверстия d = 16 мм. Такой круг в соответствии с паспортными данными станка 3К228В [2, табл. 20, с. 35] установить на станке можно (D к max = 180 мм,
). По [10, табл. 2.62, с. 132] принимаем круг с параметрами: 23А16-НС2К. Номер структуры круга – № 7 – принимаем по [9, табл. 14.6, с. 713]; устанавливаем для выбранного круга класс точности изготовления А и второй класс неуравновешенности. По паспорту станка круг может вращаться с числом оборотов: n1 = 4500 мин-1, n2 = 6000 мин-1, n3 = 9000 мин-1, n4 = 12000 мин-1. Определим скорости главного движения резания для этих чисел оборотов:
(2.93)
(2.94)
(2.95)
(2.96)
В соответствии с ГОСТ 2424-83 (табл. 24, с. 24) круги формы ПВ могут работать на скоростях резания 25 м/с, 35 м/с, 50 м/с. Принимаем
n к = n4 = 12000 мин-1. Тогда полное обозначение выбранного шлифовального круга будет следующим:
ПВ 50×50×16 23А 16-Н С27 К А 2кл. 35м/с ГОСТ 2424-83.
Назначаем режимы резания.
1) частота вращения круга n к = 12000 мин-1.
2) Определяем частоту вращения заготовки. По [2, табл. 55, с. 301] скорость вращения заготовки Примем
Тогда:
(2.97)
На станке 3К228В предусмотрено бесступенчатое регулирование частоты вращения шпинделя, поэтому принимаем Таким образом, скорость движения окружной подачи
3) Определяем скорость движения продольной подачи (или продольная минутная подача – S м). По [2, табл. 55, с. 301]:
(2.98)
(2.99)
На станке предусмотрено бесступенчатое регулирование скорости продольного хода шлифовальной бабки, поэтому принимаем
4) Определяем поперечную подачу круга (По стандарту этот параметр обозначается
).
По [11, карта 15, лист 1, с. 172–173] принимаем Учитываем поправочные коэффициенты на поперечную подачу. В зависимости от обрабатываемого материала и точности обработки [11, карта 15, лист 1, с. 175]. Коэффициент
В зависимости от величины припуска [11, карта 15, с. 176] поправочный коэффициент (найден методом интерполяции значений
для припуска 0,3 мм и
для припуска 0,5 мм). Это припуск на диаметр. Наш припуск на диаметр равен 2h = 0,4 мм.
В зависимости от диаметра шлифовального круга поправочный коэффициент [11, карта 15, с. 176].
В зависимости от способа контроля размера [11, карта 15, с. 177] (активный контроль).
В зависимости от жесткости заготовки и формы поверхности [11, карта 15, с. 177] .
В зависимости от точности обработки и жесткости станка [11, карта 2, с. 110] .
В зависимости от твердости шлифовального круга [11, карта 14, с. 169] . С учетом поправочных коэффициентов определим подачу:
(2.100)
Принимаем по паспортным данным станка 3К228В поперечную подачу
5) Определяем мощность, затрачиваемую на резание. Материалом обрабатываемой заготовки является конструкционная углеродистая сталь, и она относится к 1-й группе обрабатываемого материала [11, карта 1, с. 109] и тогда по [11, карта 16, с. 179] N табл. =3,3 кВт. Учитываем поправочный коэффициент на мощность К N 1 = 1.16 [11, карта 16, с. 180], тогда
(2.101)
6) Проверяем, достаточна ли мощность привода шлифовального шпинделя. У станка 3К228В где
– КПД привода станка. Так как (3,83<4,7), то
– обработка возможна.
7) Проверяем, выполняется ли условие бесприжогового шлифования. При окончательном шлифовании заготовок из закаленной стали нельзя допускать, чтобы установленный режим шлифования приводил к образованию прижогов на обрабатываемой поверхности, т. е. нельзя допускать чрезмерного возрастания температуры в зоне шлифования. Для того чтобы проверить, выполняется ли условие бесприжогового шлифования, подсчитывают удельную мощность шлифования Nуд, т. е. мощность, приходящуюся на 1мм ширины шлифовального круга (N уд – обобщенная характеристика режима шлифования)
(2.102)
Далее определяем предельное значение N уд, при котором обеспечивается бесприжоговое шлифование закаленной стали. Для твердости круга С2, скорость движения окружной подачи до 63 м/мин, предельное значение
Так как 0,0766 < 0,13, то условие бесприжогового шлифования выполнены.
8) Определяем основное время на обработку по [12, с. 360]:
(2.103)
где – длина хода стола, при перебеге круга на каждую сторону равном
равно
– припуск на сторону,
– скорость движения продольной подачи, мм/мин;
– поперечная подача, мм/дв. ход.
Обычно в формулах для определения основного времени при шлифовании имеется коэффициент точности К1, учитывающий время на «выхаживание». В данной формуле этот коэффициент отсутствует, так как в нормативах [11] приведены средние значения , рассчитанный исходя из полного времени цикла шлифования, включая выхаживание [11, с. 107].
(2.104)
Пример 6.На плоскошлифовальном станке модели 3П722 с прямоугольным столом шлифуется плоская поверхность планки шириной
В = 110 мм, длиной L = 280 мм, высотой h 1 = 20-0,05 мм. Припуск на сторону h = 0,35 мм, параметр шероховатости поверхности Ra = 1,25 мкм. Материал заготовки – сталь 45ХН, закаленная до твердости HRC 51,5. На магнитном столе станка установлено шесть заготовок (в 2 ряда по 3 заготовки в каждом). Необходимо выбрать шлифовальный круг, назначить режимы резания, определить основное время.
Решение.Выбираем шлифовальный круг. По [9, табл. 14.10, с. 721] принимаем форму круга ПП, по [10, табл. 2.62, с. 132] принимаем следующие характеристики круга: 15А25-ПСМ2К, по [9, табл. 14.6, с. 713] принимаем структуру круга № 6, количество основной фракции режущих зерен в объеме круга – повышенное – П, класс точности изготовления круга – А, класс неуравновешенности – 2-й. У станка 3П722 можно устанавливать круг с наружным диаметром D к = 450 мм, . По ГОСТ 2424-83 принимаем круг с посадочным отверстием диаметром 127 мм. Принимаем допустимую скорость вращения круга – 35 м/с. Таким образом, полная характеристика шлифовального круга будет следующей:
ПП 450×80×127 15А 25-П СМ2 6 К1 А 2кл. 35м/с ГОСТ 2424-83.
Назначаем режимы резания [12].
1) Определяем частоту вращения шлифовального круга по принятой скорости
(2.105)
Принимаем по паспорту станка [2, табл. 23, с. 38] n к = 1500 мин-1.
2) Определяем скорость движения продольной подачи (в [11] эта скорость названа скоростью заготовки
) по [11, карта 19, с. 194]
3) Определяем поперечную подачу круга по [11, карта 19, с. 194]. По величине Ra = 1,25 мкм и ,
стола.
4) Определяем подачу на глубину напроход [11, карта 19, с. 194–195]. Движение подачи на глубину напроход, или вертикальная подача круга, осуществляется в момент реверсирования поперечной подачи. Принимаем Учитываем поправочные коэффициенты на это значение подачи [11, карта 19, л. 4, с. 196–197].
В зависимости от обрабатываемого материала и точности обработки: сталь 45ХН относится к II группе обрабатываемого материала; для этой группы величины допускаемого отклонения высоты планки – 0,05 мм и Ra=1,25 мкм, поправочный коэффициент
В зависимости от размера шлифовального круга и степени заполнения стола станка заготовками, определяем степень заполнения стола. На столе установлено шесть заготовок прямоугольной формы в два ряда, следовательно, ширина расположения шлифуемых заготовок на столе станка длина расположения шлифуемых заготовок на столе станка
суммарная площадь шлифуемой поверхности
т. е. отношение:
(2.106)
Это значение меньше единицы при шлифовании заготовок типа колец, втулок, планок, плит с отверстиями и т. п. Для отношения, равного единице, и диаметра круга D к = 450 мм поправочный коэффициент
В зависимости от точности обработки и жесткости станка [11, карта 2, с. 110] .
В зависимости от твердости шлифовального круга [11, карта 18, с. 190] поправочный коэффициент .
С учетом поправочных коэффициентов:
(2.107)
5) Определяем мощность, затрачиваемую на резание. По [11, карта 20, с. 198] N табл. = 8,4 кВт. Учитываем поправочный коэффициент на мощность [11, карта 20, л. 2, с. 180] К N =1.05 (найден интерполированием значений К N =1,05 для и К N =1,12 для
), тогда:
(2.108)
6) Проверяем, достаточна ли мощность привода шлифовального шпинделя . У станка 3П722 с мощностью двигателя
(2.109)
Таким образом: (8,65 < 12,75), т.е. обработка возможна. (5.101)
7) Проверяем, выполняется ли условие бесприжогового шлифования. определяем удельную мощность шлифования:
(2.110)
По [11, карта 20, л. 2, с. 200] определяем предельное значение Nуд при котором обеспечивается бесприжоговое шлифование закаленной стали. Для твердости круга СМ2 и скорости движения продольной подачи до 20 м/мин, предельное значение
Так как 0,105 < 0,11, то условие бесприжогового шлифования выполнено.
8) Определяем основное время
(2.111)
где – припуск на сторону, по заданию
– число заготовок, одновременно установленных на столе станка,
– длина продольного хода стола, при перебеге круга на каждую сторону равном
равно
– скорость движения продольной подачи стола, м/мин;
– подача на глубину напроход (вертикальная подача), мм; S – поперечная подача круга, мм/ход стола; L з – суммарная длина шлифуемых поверхностей заготовок; Н – перемещение шлифовального круга в направлении поперечной подачи;
(2.112)
где – суммарная ширина шлифуемых поверхностей заготовок, установленных на столе;
– высота круга.
Получим основное время на обработку:
(2.113)
Пример 7.Необходимо окончательно хонинговать отверстие гильзы двигателя внутреннего сгорания, материалом которой является серый чугун незакаленный.Диаметр отверстияDO – 80 мм; длина гильзы L з = 110 мм; требуемая высота микронеровностей Ra = 0,16 мкм; припуск на диаметр – 0,01 мм. Требуется подобрать станок, инструмент, режимы резания, определить основное время.
Решение.
1) Определяем характеристику инструмента.
По [10, табл. 3.5, с. 218–219] выбираем брусок со следующими характеристиками: 63С М14 СТ2 К; принимаем структуру № 7, класс точности изготовления бруска А. Длину бруска принимаем по соотношению [15, карта III-6, с. 211] L бр = (0,3…0,75) L з= (33…82,5) мм. По [13] принимаем прямоугольный брусок (БП) с размерами: длина – 75 мм; ширина – 15 мм, высота – 5 мм. Таким образом, полное обозначение будет следующим:
БП 15×5×75 63С М14 СТ2-51 7 КА ГОСТ 2456-82.
Число 51 после обозначения твердости бруска в соответствии [14, приложение 2, табл. 2, с. 20] отображает звуковой индекс (ЗИ).
2) Определяем тип станка. Для этого определяем величину хода шпиндельной бабки (длина рабочего хода) по соотношению [15, карта III-6, с. 211]:
(2.114)
где – длина хонингования
мм;
– длина бруска, мм;
– длина выхода брусков, мм.
(2.115)
Принимаем
(2.116)
По [16, табл. 31, с. 72–73] принимаем вертикально-хонинговальный станок ОФ-38А. Технические характеристики станка следующие:
Максимальный диаметр обрабатываемого отверстия, мм ……………..….80
Минимальный диаметр обрабатываемого отверстия, мм ………...………20
Длина хода шпиндельной головки, мм………..………...…………………320
Частота вращения шпинделя, мин-1…………………..............200,315,500,800
Скорость возвратно-поступательного движения, мин-1….……………..0–12
Давление разжима брусков, МПа……………………………………...0,2–1,2
Мощность электродвигателя привода вращения шпинделя, кВт…………1,7
3) Определяем частоту вращения хонинговальной головки. По [15, карта III-6, с. 217] рекомендуемая скорость вращения хонинговальной головки лежит в пределах 30–50 м/мин. Определяем минимальное и максимальное число оборотов хонголовки:
(2.117)
(2.118)
Принимаем по паспорту
Фактическая скорость резания:
(2.119)
4) Определяем скорость возвратно-поступательного движения хонголовки. Рекомендуемая скорость возвратно-поступательного движения хонинговальной головки V в-п лежит в пределах 10–15 м/мин [15, карта III-6, с. 217]. На станке ОФ-38А предусмотрено бесступенчатое регулирование скорости возвратно-поступательного движения хонголовки, поэтому принимаем V в-п = 11 м/мин.
5) Определяем давление разжима брусков. Давление разжима брусков в хонголовке рекомендуется в пределах 0,3…0,5 мПа [15, карта III-6, с. 217]. На станке также предусмотрено бесступенчатое регулирование давления разжима, поэтому принимаем Рразж = 0,4 мПа.
6) Определим основное время на обработку. Время обработки при таких режимах резания лежит в пределах 0,3…0,4 мин, [15, карта III-6, с. 217], но существующая на станке система активного контроля позволяет точно знать время при обработке каждой детали. Если на станке отсутствует система активного контроля, то основное время можно рассчитать по формулам, приведенным в [5, с. 742, 743].
Система маркировки абразивного инструмента,
принятая с 2009 г. [41].
Таблица 2.14
Дата добавления: 2019-02-12; просмотров: 479; Мы поможем в написании вашей работы! |
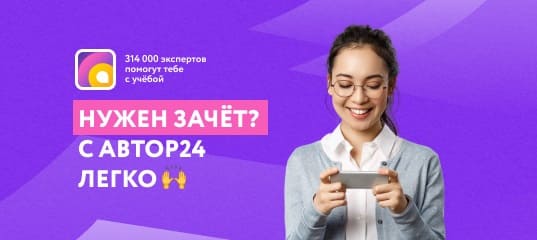
Мы поможем в написании ваших работ!