Контроль технического состояния (дефектация) деталей и сборочных единиц электровозов
4.1. Дефектация деталей и сборочных единиц производится с целью определения пригодности к дальнейшей эксплуатации в соответствии с нормами допусков и износа деталей и узлов механического оборудования, нормами допусков и износов электрических аппаратов согласно приложениям 1 и 2 к настоящему Руководству, а также возможности восстановления дефектных и поврежденных деталей или необходимости их браковки.
Детали или отдельные части деталей, подлежащие дефектации, предварительно очищаются, а детали, подлежащие дефектации для обнаружения трещин, очищаются до и после проверки.
4.2. Выявление трещин у деталей и в сборочных единицах в зависимости от их габаритов и материала, характера и предполагаемого расположения дефекта или повреждения производится следующими методами неразрушающего контроля: оптико-визуальным, магнитопорошковым, электромагнитным (вихретоковым дефектоскопом), цветным и люминесцентным, ультразвуковым, ударно-звуковым (простукивание), компрессионным (опрессовкой жидкостью или воздухом).
4.3. При оптико-визуальном контроле с применением в необходимых случаях луп, эндоскопов, перископов, перископических дефектоскопов и других средств особое внимание уделяется поверхностям, расположенным в зонах высоких тепловых и механических нагрузок, а также в зонах концентрации напряжений.
4.4. Цветной и люминесцентный методы применяются для отыскания поверхностных трещин у демонтированных деталей и деталей, находящихся в сборочных единицах, изготовленных из магнитных и немагнитных материалов.
|
|
4.5. Магнитопорошковый метод применяется для контроля состояния стальных и чугунных деталей, выявления усталостных и закалочных трещин, волосовин, включений и других пороков металла, выходящих на поверхность.
После магнитной дефектоскопии детали подшипников качения, скольжения и любых трущихся пар подвергаются размагничиванию.
4.6. Ультразвуковая дефектоскопия (метод отраженного излучения) применяется для выявления глубинных пороков металлов (волосовин, трещин, усадочных раковин, пористости, шлаковых включений и непроваренных мест в сварочных швах), не выходящих на поверхность, у отдельных демонтированных деталей или деталей, находящихся в собранном виде, независимо от материалов, из которых они изготовлены.
4.7. Электромагнитный метод (с использованием вихретоковых дефектоскопов) применяется для выявления пороков магнитных и диамагнитных металлов (трещин, раковин, рыхлот, пор), выходящих на поверхность или находящихся у поверхностного слоя демонтированных или собранных деталей.
4.8. Величина и характер износа деталей в зависимости от их конструкции определяются путем микрометража согласно требованиям, карт измерения основных деталей или по истечению воздуха или жидкости.
|
|
4.9. Уменьшение сечений деталей, изготовленных из проката и поковок, от действия коррозии и зачистки в местах, не подверженных износу от трения и не нормированных отдельными предписаниями, допускается не более чем на 15 % против чертежных размеров.
Организация диагностирования электровозов
5.1. Локомотивные депо, специализирующиеся на ремонте электровозов, как правило, должны организовывать участки диагностирования оборудования, в целях проверки технического состояния, выяснения причин неисправностей и отказов систем и установления по результатам диагностирования вида, объема, места ремонтно-восстановительных работ.
5.2. Для достижения цели технического диагностирования следует решить основные задачи:
5.2.1. Проверка исправности (работоспособности) локомотивов или их составных частей с достаточной достоверностью.
5.2.2. Поиск дефектов с определением количественной величиной этих дефектов.
5.2.3. Сбор исходных данных для прогнозирования остаточного ресурса составных частей локомотивов.
|
|
5.2.4. Выдача рекомендаций по результатам диагностирования о виде, объеме, конкретном месте ремонтно-восстановительных работ.
5.2.5. Для каждого диагностируемого локомотива должны быть установлены нормативные показатели исправности (работоспособности) в эксплуатации, при ТО и ТР.
5.2.6. При проверке исправности (работоспособности) устанавливают отсутствие всех дефектов оборудования или его составных частей.
5.2.7. Диагностирование локомотива осуществляет специалист-диагност, назначенный из числа наиболее опытных и квалифицированных работников. Он должен хорошо знать конструкцию и работу локомотива, устройство диагностического оборудования и правила использования.
5.2.8. В помощь специалисту-диагносту выделяют слесаря. При диагностировании слесарь под руководством специалиста-диагноста выполняет испытания контрольно-диагностические, регулировочные и вспомогательные операции.
5.3. Диагностирование подразделяют на плановое и заявленное. Плановое проводят при текущем ремонте, заявленное – при появлении косвенных признаков неисправностей перед плановым и неплановым ремонтом.
5.4. Целью планового диагностирования служит определение технического состояния, остаточного ресурса узлов и агрегатов, их потребности в регулировании, замене или ремонте. При этом назначаются объемы ремонтно-восстановительных работ, обеспечивающих безотказную работу локомотива до следующего планового ремонта.
|
|
Цель заявленного диагностирования – определение конкретной неисправности, выявление и устранение отказов оборудования.
5.5. При наличии компьютерных систем, в процессе диагностирования следует широко использовать компьютерные программы: планирование ТО и ТР; экспертные системы поиска неисправностей; определение остаточного ресурса составных частей, узлов и агрегатов локомотива; определение вида, объема и места ремонтно-восстановительных работ; оптимизация технических требований на допуски при производстве ТР.
5.6. Процесс диагностирования состоит из подготовительного, основного и заключительного этапов.
К подготовительному этапу относятся: изучение книг повреждений и неисправностей локомотивов, моторвагонного подвижного состава и их оборудования формы ТУ-29 или ТУ-29ВЦ, книги записи ремонта локомотива формы ТУ-28, журнала технического состояния локомотива формы ТУ-152; внешний осмотр контрольных точек и устранение помех, препятствующих доступу к ним; подготовка диагностических приборов к работе.
К основному этапу относится установление режима работы локомотива, способствующего проведению диагностических операций, измерение параметров технического состояния, оформления результатов диагностирования.
К заключительному этапу относится прогнозирование остаточного ресурса составных частей, агрегатов и локомотива в целом, постановка диагноза, назначение вида, объема, а также снятие диагностических средств с локомотива.
5.7. При оборудовании локомотива встроенной системой диагностирования (бортовой) результаты диагностирования накопленные в эксплуатации по специальному интерфейсу передаются в компьютер участка диагностирования.
5.8. По окончании диагностирования специалист-диагност обязан уведомить старшего мастера участка об окончании работ и предъявить результаты для сведения и принятия мер.
5.9. Результаты диагностирования должны храниться в электронной базе данных технического состояния локомотивного парка и в форме утвержденного протокола должны быть вложены в книгу формы ТУ-28.
Дата добавления: 2019-02-12; просмотров: 610; Мы поможем в написании вашей работы! |
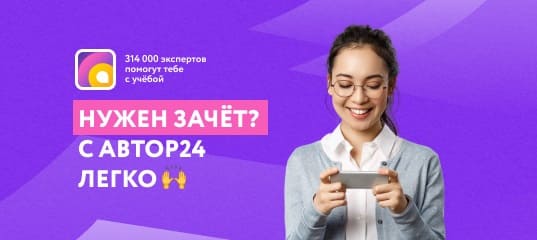
Мы поможем в написании ваших работ!