Пример расчета режимов резания и определения основного времени при протягивании
На горизонтально-протяжном станке 7А510 производится протягивание предварительно обработанного отверстия шириной b = 6 мм и длиной l = 27 мм.
Инструмент: шпоночная протяжка, изготовленная из стали Р18. подача черновых зубьев на сторону S 0 = 0,02 мм/зуб. Шаг режущих зубьев черновых t 0 = 8 мм, число зубьев в секции Zc = 1, длина протяжки до первого зуба l 1 = 265 мм; общая длина протяжки l = 510 мм.
Геометрические параметры:
Передний угол γ = 15°; задний угол на черновых зубьях α = 3°; на чистовых зубьях α = 2°, на комбинирующих зубьях α = 1°.
Назначаем режимы резания при заданной протяжке. Подача является элементом конструкции протяжки и рассчитывается конструктором.
1. Определение силы резания:
Sz-подача на зуб от 0,005-0,12 мм/зуб; выбираем 0,12 мм/зуб [2, стр.173].
2. Мощность станка: , где η = 0,75÷0.9 КПД, выбираем η = 0,9;
3. Определяем силу протягивания: , где
p - сила резания на 1 мм длины кромки;
- наибольшая суммарная длина кромок всех одновременно работающих зубьев;
, где
Zc = 1-число зубьев в секции;
Zi = + 1 – наибольшее число, одновременно работающих зубьев;
l 0 = 27 мм – длина протягивания;
tp = 7,8 мм – шаг зубьев
- принимаем число одновременно работающих зубьев равным 4.
мм
Средняя стойкость Tиз T для стали марки Р18 Т = 120 - 270мин. Выбираем T=120 мм.
Частоту вращения шпинделя определяем по формуле:
Скорость резания: , где
Cv – коэффициент, характеризующий условие обработки;
|
|
m , y – показатели степени при стойкости и подаче, зависящие от обрабатываемого материала, материала протяжек и других условий [2, стр.269].
мм/мин
об/мин
Н
кH
Вт
Вт
4. Определим основное (машинное) время:
где
q – количество одновременно обрабатываемых заготовок, q = 1 дет;
длина рабочего хода протяжки где
ln – длина рабочей части протяжки; мм;
l доп = 30 ÷ 50 мм, принимаем l доп = 30 мм.
мм
мин.
5. Определяем коэффициент k 1 , учитывающий обратный ускоренный ход:
У станка 7А510 скорость обратного хода o . x . = 25 м/мин
Число проходов i = 2, тогда мин.
Пример расчета режимов резания и определения основного времени при шлифовании
Исходные данные: деталь – валик; материал детали сталь 18ХНВА, HRC 22-30, длина шлифования L д = 145 мм; диаметр заготовки D д = 30.5 мм; припуск на диаметр 2π = 0,5 мм. Квалитет IT7 (второй класс точности), допустимая шероховатость обработанной поверхности RZ = 0,63. Масса детали m д = 0,7 кг.
Содержание операции: круглое наружное шлифование с продольной подачей. Установка – в центрах с хомутиком, закрепленным на обработанной шейке меньшего диаметра, т.е. обработка выполняется со сбегом круга в обе стороны.
Оборудование: станок круглошлифовальный 3А151. мощность двигателя шлифовального круга 7,8 кВт. Срок эксплуатации 8лет. Число деталей в партии n = 5 шт.
|
|
Выполним нормирование данной операции с использованием общемашиностроительных нормативов. [1. Общемашиностроительные нормативы режимов резания для технологических нормированных работ на металлорежущих станках. Ч. 3. – М.: НИИ Труда, 1978. 360 с. 2. Общемашиностроительные нормативы времени вспомогательного, на обслуживающих рабочих местах и П-3 на работы, выполняемые на металлорежущих станках: среднесерийное, крупносерийное производство. – М.: НИИ Труда, 1984. 469 с.]
1. Выбор характеристики круга и режима резания:
При работе с продольной подачей (скорость круга к = 50 м/с обрабатываемый материал – сталь 18ХНВА, HRC 22-30, шероховатость поверхности RZ = 0,63; квалитет IT7) по карте 3 [1] выбираем круг с характеристикой 24А40С16 – К.
По карте 6 [1] диаметр шлифования до 32 мм; ширина круга Вк = 50 мм; частота вращения nп = 205 об/мин; продольная минутная подача S м = 4420 мм/мин; поперечная подача = 0,0065 мм/ход.
Поправочные коэффициенты на поперечную подачу:
1) от обрабатываемого материала и квалитета ;
2) от припуска на диаметр ;
|
|
3) от размера и скорости шлифовального круга ;
4) от способа шлифования и контроля размера ;
5) от формы поверхности и жесткости детали ;
С учетом поправочных коэффициентов мм/ход.
Поправочные коэффициенты на минутную подачу в зависимости от шероховатости поверхности и формы поверхности
.
2. Расчет основного времени
По карте 6 [2]: , где
Кж = 1,0 – коэффициент, зависящий от точности и жесткости станка (карта 2).
К1 = 1,0 – коэффициент, зависящий от твердости круга С1 (карта 3, примечание А).
Для определения длины стола L [мм] используем формулу:
, где
K – коэффициент при сбеге круга в обе стороны, K = 2;
K = 1, при сбеге круга в одну сторону;
K = 0, при обработке «закрытой» поверхности, т.е. без сбега;
m – сбег круга в долях его ширины.
В данном случае K = 2, принимаем m = 0,5; тогда
мм.
Основное время мин.
3. Расчет вспомогательного времени
Поправочный коэффициент при длительности обработки партии деталей менее 0,25 рабочей смены [2, карта1] .
Время на установку и снятие детали ( карта 6, поз. 1ж) t в. уст. = 0,26 мин.
Время, связанное с обработкой поверхности (обработка цилиндрической поверхности с продольной подачей, наибольший диаметр детали, устанавливаемой на станке, до 360 мм, длина обрабатываемой поверхности до 200 мм, шлифование с измерением жесткой скобой, квалитет IT7) 0,49 мин (карта 34, поз. 29г).
|
|
Вспомогательное время с учетом коэффициента серийности: мин.
4. Расчет штучного времени
Время на техническое обслуживание рабочего места , где
Тпр = 2,3 мин – время на одну правку; по карте 45, поз. 3г, при установке правящего инструмента на станке, правящем инструменте – алмазе, шероховатости поверхности Rz = 0,63; ширине круга Вк до 80 мм.
Т = 33 мин – период стойкости круга по нормативам режимов резания; материал – электрокорунд, чистовое шлифование по квалитету IT7 (по второму классу точности);
мин
Время на организационное обслуживание: t орг = 1,0% (карта 45, лист 12)
Время перерывов на отдых и личные потребности (карта 45, поз. 3г):
t отл = 5% от оперативного времени – поперечная подача ручная;
Оперативное время : t оп = 1,0 мин при m д до 1,0 кг.
Машинно-ручное время в оперативном:
Штучное время Тш-к мин
Подготовительно-заключительное время на партию деталей (карта 60) включает затраты по группам:
Тнал.ст. = 10 мин – время на наладку станка, инструмента и приспособлений (поз. 1б)
Тполуч.и сд. ин. = 7 мин – время на получение и сдачу инструмента и приспособлений (поз. 3)
Тдоп.. = 6 мин – дополнительное время при установке шлифовального круга (поз. 7б)
Суммарноеподготовительно-заключительноевремя: мин.
Расчет усилий зажима
При проектировании станочного приспособления необходимо особое внимание уделить выбору зажимных устройств и расчету силы зажима обрабатываемых заготовок. Сила зажима должна обеспечить надежное закрепление заготовок в приспособлении и не допускать сдвига, поворота или вибрации заготовки при обработке.
Величину сил зажима определяют в зависимости от сил резания и их моментов, действующих в процессе обработки.
Силу зажима заготовки в приспособлении определяют с учетом метода обработки, состояния обрабатываемого материала, системы СПИД (станок-приспособление-инструмент-деталь)и других факторов. Чтобы обеспечить надежность зажима обрабатываемой заготовки, применяют коэффициент запаса, которые зависят от состояния поверхности заготовки в процессе ее обработки, процесса затупления режущего инструмента и других факторов, которые возникают в процессе обработки.
Коэффициент запаса: , где
К0 – настоящий коэффициент запаса, при всех случаях обработки;
К0 = 1,5
К1 – коэффициент, учитывающий состояние поверхности заготовки (обработанная или необработанная, табл. 3.1);
К2 - коэффициент, учитывающий увеличение силы резания при затоплении режущего инструмента;
К3 - коэффициент, учитывающий увеличение сил резания при обработке прерывистых поверхностей на детали;
К4 - коэффициент, учитывающий постоянство силы зажима, развиваемой приводом приспособления;
К5 - коэффициент, учитывающий удобное расположение рукоятки для ручных зажимных устройств;
К6 - коэффициент, учитывающий при наличии моментов, стремящихся повернуть обрабатываемую деталь вокруг ее оси.
Коэффициенты запаса К2 - К6 выбирают по таблицам 3.2. Величину необходимых сил зажима следует рассчитывать с наибольшей точностью. При завышенном ее значении увеличивается стоимость изготовления приспособления за счет металлоемкости и расхода сжатого воздуха, а заниженные значения сил нее обеспечивают надежного зажима заготовки.
Силу зажима рассчитывают в зависимости от действия на заготовку сил резания и конструкции установочных и зажимных устройств по формулам соответствующей учебной и справочной технической литературы. При определении силы резания необходимо учитывать установленные нормативные коэффициенты трения.
1. Расчет винтовых зажимов
Винтовые зажимы являются наиболее простыми универсальными устройствами для станочных приспособлений. Они широко применяются в единичном и серийном типах производства. Недостатками винтовых зажимов являются медлительность действия, большие потери на трение и непостоянство зажимной силы.
Крутящий момент, приложенный к гайке или головке винта, ,
где, F рук – сила, приложенная на конце рукоятки или гаечному ключу [Н]; F рук =140 ÷ 200Н;
L рук ≈ 14 Dp – длина рукоятка ключа,
Dp – номинальный наружный диаметр резьбы, мм.
Номинальные диаметры метрической резьбы выбирают в зависимости от силы зажима обрабатываемой заготовки:
Диметр резьбы Dp, мм | 4 | 5 | 6 | 8 | 10 | |
Допускаемая сила зажима Wв, Н | 500 | 750 | 1000 | 2000 | 3000 | |
Диаметр резьбы Dp, мм | 12 | 16 | 20 | 24 | ||
Допускаемая сила зажима Wв, Н | 4500 | 8000 | 12000 | 17000 | ||
Таблица 3.2.
Значение коэффициента К2
Методы обработки | Компоненты усилия резания | К2 |
Сверление | Крутящий момент Осевая сила | 1,15 1,10 |
Зенкерование предварительное | Крутящий момент Осевая сила | 1,3 1,2 |
Зенкерование чистовое | Крутящий момент Осевая сила | 1,2 1,2 |
Точение и растачивание предварительное | Рz | 1,0 (сталь) 1,0 (чугун) |
Рy | 1,4 (сталь) 1,2 (чугун) | |
Рx | 1,6 (сталь) 1,25 (чугун) | |
Точение и растачивание чистовое | Рz | 0,95 (сталь) 1,05 (чугун) |
Рy | 1,05 (сталь) 1,75 (чугун) | |
Рx | 1,0 (сталь) 1,5 (чугун) | |
Фрезерование цилиндрическое предварительное и чистовое | Окружная сила | 1,75…1,9 (вязкие стали) 1,2…1,7 (твердые стали) (чугун) |
Торцевое фрезерование | Тангенциальная сила | То же |
Шлифование | Окружная сила | 1,15…1,20 |
Протягивание | Сила протягивания | 1,55 |
Величину необходимой силы зажима следует рассчитывать с наибольшей точностью, т.к. при завышенном ее значении увеличиваются диаметр пневмоцелиндра, расход воздуха, габариты, вес и стоимость приспособления; при заниженном значении сил зажима не обеспечивается надежный зажим детали.
Рассмотри основные случаи воздействия на заготовку сил резани, сил зажима и их моментов
Сила зажима Qзаж и сила резания Ррез действуют в одном направлении и прижимают заготовку I к опорам приспособления. Если Ррез при этом не вызывает сдвигающих сил, то Qзаж = 0. это наиболее благоприятный случай расположения сил
Например, при протягивании отверстий на протяжном станке деталь не требует крепления при обработке.
Действие силы зажима Qзаж и силы резания Ррез прямо противоположны, т.е. заготовка при обработке удерживается силами зажима. С учетом коэффициента надежности
Такой вариант расчета встречается при строгании, фрезеровании, но довольно редко, т.к. приведенное направление усилий противоречит одному из главных правил проектирования приспособлений о том, что силы резания должны прижимать деталь к опорам.
При конструировании зажимных приспособления необходимо определять силу зажима обрабатываемой заготовки.
Сила зажима ,
где, r ср - средний радиус резьбы (устанавливается по таблицам;
αп - угол подъема витка резьбы (у стандартных метрических резьб с крупным шагом αп = 2˚30΄);
φт - угол трения в резьбовом соединении (для метрических резьб φт = 6˚34΄);
Кф - коэффициент, зависящий от формы и размеров поверхности соприкосновения зажимного элемента с зажимной поверхностью (рис. 1), для винта со сферическим опорным торцом Кф = 0, с плоским опорным торцом (рис. 1а, б)
,
где f т – коэффициент трения на торце винта и гайки; f т = 0,1÷0,15
r т = 0,40 dвн.резьбы – радиус опорного торца винта, мм.
Коэффициент Кф для винта со сферическим опорным торцом, соприкасающимся с конусным углублением (рис. 1в)
,
r с – радиус сферы опорного торца винта, мм,
β = 120˚ - угол при вершине конусного углубления.
а) б) в) г) д)
Рис. 1. Виды опорных поверхностей зажимных механизмов приспособлений
Коэффициент Кф для винта с кольцевым опорным торцом или гайкой (рис. 1г, д)
,
где D нар и D вн – наружный и внутренний диаметр опорного кольцевого торца винта или гайки, мм.
Если принять f т = 0,15, то для основной метрической резьбы можно с достаточной точностью определить силу зажима:
,
где D нар.р. – наружный диаметр резьбы, мм.
Наружный диаметр винта в зависимости от требуемой силы зажима и допускаемого напряжения винта на растяжение:
,
где [δ]р – допускаемое напряжение на временное сопротивление материала винта при переменной нагрузке [Н/м]; [δ]р =58 ÷ 98 Н/м (подробнее о зажимах [8])
Задача
Определить силу зажима W в, создаваемую винтом М20 со сферическим опорным торцом при действии на плоскость. Сила, прилагаемая к рукоятке ключа F рук = 140 Н.
Решение:
Определим крутящий момент, приложенный к головке винта, .
Длину рукоятки ключа определим из отношения L рук ≈ 14 Dpез.
Силу, приложенную к рукоятке ключа, принимаем F рук = 140 Н,
L рук = 14·20 = 280 мм.
Сила зажима, создаваемая винтом,
Устанавливаем средний радиус винта по справочным таблицам на типы резьб, r ср = 9,19 мм. Угол подъема витка для метрических резьб составляет п = 2˚30΄. Угол трения в резьбовом соединении принимаем φт = 6˚34΄.
Коэффициент, зависящий от формы поверхности соприкосновения зажимного элемента с зажимной поверхностью, принимаем f ф = 0 (для сферической поверхности). Коэффициент трения на торце винта принимаем
f т = 0,15.
2. Расчет эксцентриковых зажимов
Эксцентриковые зажимные устройства являются быстродействующими и широко применяются в крупносерийном и массовом производствах при небольших силах зажима (рис. 2) Для определения основных размеров конструкции эксцентрика необходимо иметь: допуск на базовую поверхность обрабатываемой детали в процессе ее установки; силу, приложенную на конце рукоятки F рук, и длину рукоятки L рук.
,
где F рук – сила, приложенная на рукоятке эксцентрика, Н;
e – эксцентриситет, мм;
f т.п. – коэффициент трения на поверхности эксцентрика;
f т.о. = 0,12 ÷ 0,15 – коэффициент трения на поверхности оси;
r о – радиус оси, мм.
Ход эксцентрика .
Наиболее удобный для рабочего угол поворота βп = 90˚ ÷ 120˚.
Ход эксцентрика можно определить по соотношению .
Наружный диаметр эксцентрика определяют из условия , а радиус оси r о выбирают в зависимости от ширины рабочей части эксцентрика по конструктивным соображениям или рассчитывают по формуле.
Самоторможение эксцентрикового зажима должно соответствовать условию , где отношение
является характеристикой эксцентрика.
Все расчетные параметры круглого эксцентрика необходимо принимать с учетом ГОСТ 9061-68*, где
Рис. 2. Элементы кругового эксцентрика,
применяемые при расчетах
Задача
Определить конструктивные элементы круглого эксцентрика для зажима заготовки по размерам рабочего чертежа и рассчитать силу зажима обрабатываемой заготовки.
Решение:
Определим допуск базовой поверхности обрабатываемой заготовки, где
δ = 0,34 мм. Установим ход эксцентрика
Принимаем эксцентриситет e = 2 мм. Определим диаметр круглого эксцентрика .
Определим силу зажима эксцентриком:
Длину рукоятки эксцентрика L рук = 2,5D = 2,5 · 40 = 100 мм.
Угол поворота принимаем βп = 90˚. Коэффициент трения на поверхности эксцентрика f т.п. = 0,12. Коэффициент трения на поверхности оси f т.о. = 0,15. Радиус оси принимаем конструктивно r о =6 мм. Самоторможение эксцентрикового зажима проверяем по условию (где
). Самоторможение удовлетворяет нашему условию.
Для круглого эксцентрика выбираем сталь 20Х ГОСТ 4543-71 с последующей цементацией на глубину h = 0,8 …1,2 мм и закалкой до твердости HRCэ 55÷60
Дата добавления: 2019-02-12; просмотров: 4800; Мы поможем в написании вашей работы! |
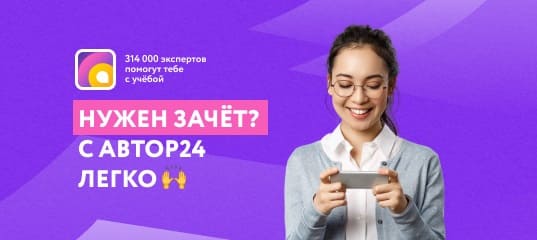
Мы поможем в написании ваших работ!