ОСОБЕННОСТИ РАСЧЕТА ПОТОКОВ РАЗЛИЧНЫХ ТИПОВ
Особенности расчета АГП
Выбор моделей.
Разница в трудоемкости моделей (∆Т) до 15% (если модели запускаются в один поток). Для моделей разной сложности можно предусмотреть несколько потоков.
Нормирование времени – с учетом работы пачкой, дополнительные операции по комплектованию деталей и доставка полуфабриката.
Основное условие согласования (ОУС)
для одномодельных потоков
Σ tр = (0,9 ÷ 1,15)*τ* к
для многомодельных потоков
последовательный запуск ΣtA = (0,9 ÷1,15)*τA*к
ΣtБ = (0,9 ÷1,15)*τБ*к
цикличный запуск Σ tрA + Σ tрБ = (0,9 ÷1,15)*τср* к*С
Комплектование операций – внутри группы (возможно комплектование внутри двух групп)
Кратность операций
к =1÷8 (мах 10)
В потоках с ручной передачей полуфабриката большая кратность нежелательна.
Возвраты – возможны на 1-2 рабочих места.
Характер питания: в заготовительной секции целесообразней применять пачковый запуск, в монтажной – поштучный.
Все секции подчиняются одному единому такту, каждая секция рассчитывается отдельно.
Коэффициент согласования, график синхронности, монтажный график рассчитываются и строятся по каждой секции в отдельности.
Размещение рабочих мест произвольное. Главный принцип размещения – сокращение пути движения изделий и время выполнения вспомогательных приёмов.
Запас незавершённого производства (НП)
|
|
Необходимо предусмотреть запас НП между секциями:
- заготовительной и монтажной
- монтажной и отделочной.
Составление почасового графика запуска.
Время на обработку пачки, мин
tп = tо * nд / 60 , мин, где (31)
tо – время на обработку детали , с
nд – количество деталей в пачке.
Количество пачек, которое нужно запустить на каждое рабочее место в час:
nn = 60 / tп
Особенности расчёта ПМС (с применением напольной транспортной системы с автоматическим адресованием коробок типа ТКТ)
Выбор моделей.
Разница в трудоёмкости моделей обычно ΔТ≤5÷7%.
Допускается различная последовательность обработки и сборки, но требуется
использование однотипного оборудования.
Численность рабочих – 18-30 человек
Нормирование времени – с учётом времени работы с коробкой (взять,
отставить), и количества подходов коробки.
Основные условия согласования.
одномодельный Σ tр = (0,9÷1,15)* τ * к
многомодельный
последовательный Σ tр А= (0,9÷1,15)*τА* к
запуск Σ tр Б= (0,9÷1,15)*τБ * к
цикличный запуск Σ tр А + Σ tр Б = (0,9 ÷1,15)*τср* к *С
Комплектование операций.
Возможно нарушение технологической последовательности (за счёт многократных подходов коробки к одному и тому же рабочему месту). Важно соблюдение принципа специализации оборудования.
|
|
Вид запуска – в основном последовательный. Число изделий в коробке зависит
от размеров деталей, их веса, размеров коробки (обычно 5÷15).
При цикличном запуске в одну коробку укладываются одновременно 2-3 модели (в соотношении А: Б: В) одной расцветки, нумерация деталей должна отличаться.
Можно располагать вдоль транспортёра 2 бригады, изготавливающие ручные изделия (используя разный цвет коробок) общими могут быть рабочие места, на которых обмётывают петли, пришивают пуговицы.
Расчет потока как несекционный (если отделочная секция не выделяется)
Расположение рабочих мест – поперечное. Полуфабрикат должен поступать
слева. Запуск и выпуск лучше производить с противоположных сторон.
Окончательную ВТО целесообразнее располагать вне транспортной системы.
Расчёт скорости транспортёра.
Vтр = (Lкор / (n* τ))*1.5 , м./мин., где (32)
Lкор – путь коробки, м.
n – число изделий в коробке
τ – такт, мин
1,5 – коэффициент запаса
Lкор = l р.м * N * f + π*Д , м , где (33)
l р.м – шаг рабочих мест, м
|
|
N – число рабочих, чел.
f – коэффициент, учитывающий количество рабочих мест
Д – диаметр натяжного устройства, м
Проверка ритмичности
t оп = t обр.кор (34)
t оп = t min * n * (m – 1), мин (35)
t обр.кор = Lкор / Vтр, мин, где (36)
t оп – время выполнения операции, мин
t обр.кор – время обращения коробки, мин
t min – время выполнения операции на одном изделии, мин
при одном подходе коробки t min = τ
при двух подходах коробки t min = τ / 2
при трех подходах коробки t min = τ / 3
n – число изделий в коробке
m – число коробок на рабочем месте
Lкор – путь коробки по транспортеру, м
Vтр – скорость транспортера, м/мин
Если равенство t оп = t обр.кор не соблюдается, регулируется число изделий в коробке, скорость транспортера до достижения равенства.
Число коробок (незавершенное производство) 2 коробки на каждом рабочем месте, 25 – 30 коробок у запускальщицы на спецстеллажах.
Составление почасового графика (см. выше).
Дата добавления: 2019-01-14; просмотров: 203; Мы поможем в написании вашей работы! |
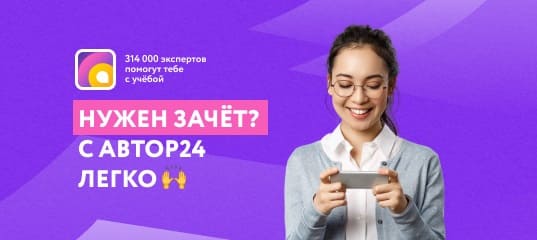
Мы поможем в написании ваших работ!