Усталостная повреждаемость авиационных деталей и соединений
В процессе эксплуатации летательных аппаратов все еще встречаются случаи усталостного разрушения авиационных деталей и конструктивных элементов. Во время дефектации прибывших в ремонт летательных аппаратов на ряде деталей обнаруживают усталостные трещины. В отдельных случаях встречаются усталостные разрушения деталей и соединений. Такие разрушения обычно неожиданны для авиационной службы и часто приводят к летным происшествиям.
В силу каких же причин происходит усталостное разрушение авиационных деталей и соединений. К таким причинам можно отнести следующие:
1. Неточности расчетов на выносливость.
2. Неправильно выбранная технология изготовления или ремонта авиационной техники.
3. Случайные, кратковременные нарушения технологических процессов изготовления и ремонта авиационной техники.
4. Случайные завышенные по сравнению с расчетными коэффициентами концентрации напряжений.
5. Непредусмотренные конструкцией случайные концентраторы напряжений.
6. Изменения асимметрии циклов нагружения, вызванные эксплуатационными, технологическими и монтажными причинами.
7. Возникновение резонансных режимов работы.
8. Изменения посадок болтовых и заклепочных соединений.
9. Изменения жесткости силовых элементов планера в процессе ремонта летательных аппаратов,
10. Случайные дефекты материала авиационных изделий.
Большинство перечисленных причин носят случайный характер, т.е. вызывают усталостное повреждение только отдельных деталей (соединений) из большого количества одноименных одновременно эксплуатирующихся на разных бортовых номерах одного типа летательных аппаратов. В таких случаях очень трудно, а часто и невозможно, установить истинную причину усталостного разрушения. В таких условиях единственной гарантией отсутствия усталостных разрушений может быть только строгое соблюдение требований технических условий на изготовление авиационных изделий, включая режимы технологических процессов изготовления или ремонта, монтажа систем летательных аппаратов или авиадвигателей, а так же правил эксплуатации, хранения и транспортировки авиационной техники.
|
|
Первые две причины вызывают систематическое возникновение усталостных повреждений одноименных деталей, установленных на разных бортовых номерах летательных аппаратов. В этом случае нужно уяснить причину возникновения усталостных повреждений и изменить технологию или конструкцию недостаточно надежных деталей или соединений.
Рассмотрим подробнее влияние на выносливость авиационных деталей и соединений случайных, приведенных выше причин.
|
|
Существенное влияние на выносливость авиационных деталей оказывает как завышенная, так и не предусмотренная конструкцией концентрация напряжений.
Концентрацией напряжений называется резкое их увеличение в местах изменения формы детали. Схема концентрации напряжений в пластине с боковым вырезом радиусом r представлена на рис. 2.21. При отсутствии выреза напряжения от растягивающей нагрузки распределены по сечению равномерно (прямая 1, рис. 2.21). Их величина равна , где
- растягивающая нагрузка, приложенная к пластине, а
- площадь поперечного сечения пластины в рассматриваемом месте.
Рис. 2.21.
При наличии надреза напряжения в сечении пластины изменяются по кривой 2, достигая максимума на дне выреза. Отношение максимального напряжения к среднему значению
называется коэффициентом концентрации
.
Закон изменения напряжений в месте надреза (прямая 2)зависит только от геометрических характеристик детали в этом месте и не зависит от ее материала. Главное влияние на величину оказывают глубина и радиус надреза. Чем больше глубина надреза и чем меньше его радиус, тем больше коэффициент концентрации
и тем ниже выносливость деталей, работающих при переменных нагрузках.
|
|
Снижение выносливости тем больше, чем больше величина и чем выше чувствительность материала к концентрации напряжений. Высокопрочные авиационные сплавы отличаются высокой чувствительностью к концентрации напряжений. Это можно видеть из схемы изменения пределов выносливости в зависимости от величины коэффициента концентрации напряжений и предела прочности материала (рис. 2.22).
Рис. 2.22.
Близкая к линейной зависимость (линия 1) характеризует изменение предела выносливости материала при отсутствии концентрации напряжений ( =1). Кривые 2 и 3 характеризуют изменение пределов выносливости при величинах
, равных
и
, при условии
. Потеря выносливости характеризуется отрезками между линией 1, кривой 2 (при
) и кривой 3 (при
).
Из схемы видно, что чем больше прочность материала и величина , тем больше снижается его исходная выносливость.
Для оценки степени влияния концентрации напряжений на долговечность авиационной стали 30ХГСНА при переменной нагрузке был проведен следующий эксперимент. Стандартные полированные образцы из этой стали, термически обработанной на предел прочности 1600 МПа, были разрушены при симметричном цикле изгибных нагружений с величиной, переменной амплитуды напряжений, равной 0,7 ... 0,75 предела прочности. Среднее число циклов до разрушения было принято равным 100%.
|
|
На остальных образцах был сделан круговой поперечный надрез (риска) глубиной 30 мкм. Образцы с риской выдержали при том же нагружении в среднем только 7% циклов до разрушения. В этом случае 93% долговечности было утрачено из-за поперечной риски. Анализ разрушенных при переменных нагрузках авиационных деталей свидетельствует о том, что во многих случаях основной причиной усталостного разрушения является то, что фактический коэффициент концентрации напряжений превышает расчетный. Это возможно в случае нарушения требований технической документации на изготовление деталей, а также при возникновении дополнительной концентрации напряжений (концентратор на концентратор). Несоблюдение требований технической документации чаще всего сводится к уменьшению радиуса перехода в местах конструктивной концентрации напряжений (галтели, пазы, выточки и т.п.) по сравнению с заданной (по чертежу). Уменьшение радиуса перехода ведет к увеличению концентрации напряжений.
Дополнительные концентраторы напряжении, не предусмотренные конструкцией детали, могут быть технологического и эксплуатационного происхождения.
К технологическим концентраторам напряжений относятся различного рода дефекты металла технологического происхождения: микрорастрескивание материала поверхностного слоя деталей вследствие неправильно назначенных или при нарушении технологических процессов обработки (механической или термической), повышенная шероховатость поверхности после механической обработки, дефекты сварки (подрезы, непровары) и т.п.
В качестве примера на рис. 2.23 приведена схема изменения пределов выносливости образцов в зависимости от прочности материала и метода обработки. По оси абсцисс отложено значение предела прочности материала, а по оси ординат коэффициент , равный отношению предела выносливости образца с заданной обработкой поверхности к пределу выносливости тщательно полированного образца. Индексом 1 обозначено значение
при тщательном полировании поверхностного слоя образца, 2 - при шлифовании, 3 - при тонком точении и 4 - при грубом точении.
Рис. 2.23.
Из схемы видно, что чем выше прочность материала и чем грубее обработана поверхность (чем больше ее шероховатость), тем больше снижается предел выносливости материала. Для высокопрочной авиационной стали при тонком шлифовании коэффициент , т.е. тонкое шлифование снижает выносливость примерно на 30%. Поэтому, при механической обработке стальных авиационных деталей в процессе их ремонта необходимо обеспечивать такую же шероховатость их поверхностей, которая была установлена в процессе изготовления этих деталей. При соблюдении этого условия обеспечивается восстановление исходной выносливости деталей после их ремонта.
Эксплуатационные концентраторы вызваны повреждениями поверхностных слоев материала деталей в процессе эксплуатации: риски, царапины, забоины, питтинги, коррозионные раковины, повышенная шероховатость поверхности в результате изнашивания абразивных видов и т.п.
Технологические и эксплуатационные концентраторы опасны в наиболее напряженных местах деталей. Такими местами у большинства авиационных деталей являются конструктивные концентраторы напряжений. Следовательно, опасным с точки зрения снижения выносливости деталей, работающих при переменных нагрузках, является наложение непредусмотренного (технологического или эксплуатационного) концентратора напряжений на конструктивный – “концентратор на концентратор”.
Опасно также возникновение непредусмотренного концентратора на наиболее напряженных участках деталей без концентрации напряжений. Например, для лопасти воздушного винта в наиболее напряженном состоянии находится поверхностный слой, набегающей на воздушный поток поверхности. В этом слое растягивающие напряжения от центробежных сил складываются с растягивающими же напряжениями от изгиба лопасти. С противоположной же стороны от изгиба лопасти возникают сжимающие напряжения. Они снижают уровень растягивающих напряжений от центробежных сил. Поэтому непредусмотренные концентраторы напряжений в первую очередь не допустимы на набегающей на воздушный поток поверхности, а именно там они и возникают при эксплуатации самолетов на запыленных аэродромах из-за газоабразивного изнашивания.
В процессе эксплуатации многие детали, работающие при переменных нагрузках, одновременно воспринимают два вида нагрузки - статическую и динамическую. Статическая остается неизменной во время работы детали, динамическая непрерывно изменяется.
Сопротивление усталости в значительной степени зависит от соотношения статической и переменной составляющих напряжений.
Обычно в условиях лабораторных испытаний изменение напряжений во времени происходит периодически с периодом Т (рис. 2.24). Однократное изменение напряжений в течение периода Т называется циклом напряжений. Цикл характеризуется максимальными и минимальными
величинами напряжений, средним напряжением цикла
, амплитудой
и коэффициентом асимметрии цикла
.
Рис. 2.24.
Различают три типа циклов: симметричный, пульсирующий и асимметричный. Симметричным циклом называют такой, при котором и
равны по величине, но противоположны по знаку. Среднее значение напряжения цикла
, а амплитуда
и коэффициент асимметрии
. Определенный при таком цикле продел выносливости обозначают через
, где индекс -1 обозначает коэффициент асимметрии.
Пульсирующий цикл характеризуется периодическим изменением напряжений от нуля ( ) до
. Коэффициент асимметрии r =0,
.
Асимметричный цикл характеризуется коэффициентом :
и
(рис. 2.24).
Выносливость как материала, так и деталей в значительной степени зависит от асимметрии цикла. Чем больше величина среднего напряжения , тем меньше амплитуда переменного напряжения
, вызывающая усталостное разрушение.
Схема зависимости между величиной среднего напряжения , предельным значениям амплитуды переменных напряжений
и числом циклов до разрушения представлена но рис. 2.25. По оси абсцисс отложена безразмерная величина
, а по оси ординат
,где
- предел прочности материала. Прямая 1 характеризует статическую прочность детали. Для нее справедливо равенство
или
.
Рис. 2.25.
Однократное приложение нагрузки, вызывающее в материале детали напряжение, равное пределу его прочности , должно привести к разрушению детали. Поэтому прямая 1 соответствует числу циклов до разрушения
.
Ниже линии 1 расположены еще три кривые. Каждая из них является кривой, равной выносливости, т.е. характеризуется одним и тем же числом нагружений, выдерживаемых материалом до разрушения. Например, число циклов до разрушения в любой точке кривой 2 будет ровно . Для кривой 3 это число равно
и т.д. Чем ниже расположена кривая, тем больше число циклов до разрушения выдерживает материал. Иначе говоря,
.
Если число циклов до разрушения соответствует базе испытаний на выносливость, равной 107 циклов, то ниже кривой 4 будет расположена зона неограниченной выносливости, любая комбинация статической и динамической составляющих нагрузки в этой области но должно приводить к усталостному разрушению материала или детали.
Для оценки влияния среднего напряжения цикла на долговечность материала пли детали при переменных нагрузках следует перемещаться по горизонтальной прямой, параллельной оси абсцисс. Каждая такая прямая характеризует неизменную величину переменной составляющей цикла нагрузки увеличение среднего значения цикла
при перемещении вправо. Перемещаясь по горизонтальной прямой слева направо, мы пересекаем кривые равной выносливости в порядке убывания их номеров. Но чем меньше номер кривой, тем меньше соответствующая ей выносливость при переменных нагрузках. Следовательно, увеличение среднего значения напряжений цикла нагрузки ведет к снижению выносливости при переменных нагрузках.
Допустим, деталь работает при симметричном цикле нагружения и выдерживает циклов нагружения до разрушения. На диаграмме это состояние отражено точкой а на оси ординат (рис. 2.25). Переход к асимметричному циклу нагружения со средним напряжением растяжения
сдвигает эту точку в положение а1 на кривой 2. Следовательно, число циклов до разрушения детали уменьшится до величины
.
Асимметричный цикл с величиной среднего напряжения сжатия , равного по абсолютной величине
, характеризуется точкой а2. Число циклов до разрушения детали при той же амплитуде переменной составляющей цикла увеличивается до
.
Таким образом, растягивающие напряжения вызывают снижение долговечности при переменных нагрузках, а сжимающие - увеличение.
Ориентировочно ,
и
представленные на схеме (рис. 2.25), можно принять равными
,
и
циклов. Тогда из этой схемы видно, что переход от симметричного нагружения (точка а) к асимметричному (точка а1)
приводит к снижению выносливости в 100 раз. Аналогичное смещение в сторону напряжений сжатия (точка а2) (
) вызывает увеличение выносливости приблизительно на один порядок.
В процессе изготовления, эксплуатации и ремонта авиационных деталей в них могут быть наведены остаточные напряжения. Из вышеизложенного следует, что эти напряжения изменяют асимметрию циклов нагружения. При наведении растягивающих напряжений изменение симметрии цикла нагружений приводит к резкому уменьшению долговечности, т.е. оно может явиться причиной усталостного разрушения деталей.
Рассмотрим физическую сущность возникновения остаточных напряжений в материале авиационных деталей в процессе их изготовления, ремонта и эксплуатации. Вначале выясним, что произойдет с длиной стального элемента при его нагреве с последующим охлаждением в свободном и стесненном положениях.
При нагреве длина l0 стального элемента увеличивается по закону , где
- температура нагрева,
- исходная температура и
- коэффициент линейного расширения. После охлаждения до первоначальной температуры этот элемент укоротится до исходной длины.
Если удлинение элемента невозможно, например, из-за неподвижных стенок, в которые упираются его торцы, то в процессе нагрева на элемент действует усилие сжатия. В процессе нагрева за счет пластической деформации от возникшего усилия сжатия происходит уменьшение длины рассматриваемого элемента. Иначе говоря, в процессе нагрева элемент укорачивается.
В случае отсутствия связи элемента с неподвижными при нагреве и охлаждении стенками его длина после охлаждения до исходной температуры окажется меньше первоначальной: .
Если же торцы элемента прочно соединены с неподвижными стенками, то после охлаждения в материале рассматриваемого элемента возникнут остаточные растягивающие напряжения, равные , где Е - модуль упругости материала этого элемента при исходной температуре.
Нечто подобное происходит при нарушении режимов шлифования при ремонте стальных авиационных деталей. Шлифованием устраняют эксплуатационные повреждения материала поверхностного слоя работавших деталей. В отличие от изготовления этих деталей при ремонте шлифуют детали, материал которых получил окончательную термическую обработку, обеспечивающую их высокие эксплуатационные свойства. После такого шлифования повторная термообработка не производится.
Если в процессе шлифования при ремонте будет хотя бы кратковременно нарушен режим охлаждения, то материал тонкого поверхностного слоя быстро нагреется до большой температуры. Окружающие холодные участки материала шлифуемой детали служат ограничением увеличения длины разогретого участка, т.е. выполняют роль стенок в только что рассмотренном примере. В результате в процессе нагрева длина участка уменьшается. Следовательно, после охлаждения в нем будут наведены остаточные растягивающие напряжения, изменяющие цикл переменного нагружения, что вызывает снижение выносливости детали.
Кроме того, тонкий поверхностный слой в процессе шлифования мог нагреваться до температуры, значительно превышающей температуру отпуска при изготовлении детали. Поэтому одновременно с наведением остаточных растягивающих напряжений снижаются механические характеристики материала поверхностного слоя. То и другое вызывает снижение выносливости детали.
Последующее усталостное разрушение наиболее вероятно тогда, когда наведение остаточных растягивающих напряжений и ухудшение механических характеристик материала поверхностного слоя за счет его нагрева при шлифовании происходят в наиболее напряженных местах деталей. К ним в первую очередь относятся конструктивные концентраторы напряжений и наиболее удаленные от нейтральной оси волокна материала в случае роботы деталей на изгиб или кручение.
При значительном перегреве материала поверхностного слоя в процессе шлифования поврежденные участки можно обнаружить по цветам побежалости. Однако при меньшем нагреве такие признаки отсутствуют. В этом случае определить ослабленное место без разрушения детали невозможно. Поэтому единственной гарантией получения надежных деталей является точное соблюдение технологии шлицевания деталей при их ремонте.
Растягивающие остаточные напряжения образуются в процессе ремонта деталей сваркой. Расплавленный материал затвердевает при большой температуре. Для стали эта температура превышает 1200°С. В этот момент температура материала ремонтируемой детали мало отличается от комнатной. При охлаждении наплавленный материал укорачивается. Так как сварной шов соединен с материалом детали, указанное укорочение вызывает возникновение остаточных растягивающих напряжений как в материале шва, так и в материале околошовной зоны.
Переход от наплавленного материала к основному является резким концентратором напряжений. Кроме того, структура материала вблизи сварного шва крупнозернистая. Все эти три фактора (растягивающие напряжения, концентрация напряжений и крупнозернистая структура материала) приводят к резкому снижению выносливости и требуют специальных мер по ее повышению.
Одной из причин усталостных разрушений является наведение монтажных растягивающих напряжений в материалах деталей. Возникают эти напряжения вследствие неточного изготовления деталей или при нарушении технологического процесса сборки изделия. Например, монтажные напряжения образуются при несоблюдении требований на совпадение стыков соединяющих трубопроводов.
Схема соединения трубопроводов приведена на рис. 2.26. Торцы соединяемых трубопроводов обозначены буквами А и Б. Размеры и форма трубопроводов должны обеспечивать точное совпадение торцов (рис. 2.26 а). При линейном (рис. 2.26 б), угловом (рис. 2.26 в) или любом другом отклонении торца Б от торца А после их соединения в материале трубопроводов будут возникать остаточные напряжения. В одних местах трубопровода возникнут растягивающие, а в других - сжимающие. В примере, приведенном на рис. 2.26 б, наибольшая величина растягивающих напряжении будет наведена у торца В с правой стороны трубопровода. С противоположной его стороны у того же торца образуются напряжения сжатия.
Рис. 2.26.
Опасны растягивающие напряжения в местах резких изменений формы трубопроводов, являющихся концентраторами напряжений. Таким местом является например, переход от трубопровода к ниппелю. В этом месте, при наложении остаточных растягивающих напряжений, возможно усталостное разрушение трубопровода.
Существенное влияние на выносливость крепежных элементов может оказать нарушение последовательности и технологии затяжки гаек болтовых соединений. Такое нарушение может привести к перегрузке болтов или шпилек за счет затяжки гаек. Это можно видеть на примере затяжки гаек соединения, представленного на рис. 2.27.
Рис. 2.27
Стальная пластина 3 соединяется с корпусом 4 с помощью двух шпилек 1 и 2. Если произвести полную затяжку гайки на шпильке 1, то пластина 3 упруго деформируется и займет положение, показанное пунктиром. Последующая затяжка гайки на шпильке 2, с тем же усилием, что и на шпильке 1, приведет к увеличению растягивающей нагрузки, воспринимаемой шпилькой 1. Нагрузка на шпильку 1 будет больше нагрузки на шпильку 2, хотя обе гайки затянуты с одним и тем же усилием.
Для предупреждения большой неравномерности усилий, действующих на шпильки после затяжки гаек, рекомендуют такую затяжку выполнять в два приема. Вначале выполняют затяжку гаек в рекомендуемой последовательности на величину, равную 0,6 ... 0,7 от номинальной. Затем в той же последовательности осуществляют полную затяжку гаек, т.е. с номинальным усилием.
Возникновение остаточных напряжений в материале авиационных деталей возможно в процессе эксплуатации летательного аппарата. Происходит это тогда, когда эксплуатационная нагрузка Р, по тем или иным причинам, превышает максимально допустимую. Для летательного аппарата это грубая посадка или превышение максимально допустимой, нагрузки во время полета.
Если Р превышает допустимую, то в наиболее напряженных участках детали в момент нагружения возможно возникновение пластической деформации. При нагружении по схеме, представленной на рис. 2.28, максимальные напряжения возникают в галтели. В точке 1 галтели действуют растягивающие напряжения, а в точке 2 - сжимающие. Следовательно, при пластическом деформировании в точке 1 происходит удлинение материала поверхностного слоя, а в точке 2 - укорочение.
Рис. 2.28.
Так как объем пластически деформируемого материала очень мал, то после снятия нагрузки Р деталь возвратится практически в исходное положение. Поэтому в тех местах, в которых материал под нагрузкой пластически удлинился, возникнут остаточные напряжения сжатия. В тех же местах, в которых материал под нагрузкой пластически укоротился - напряжения растяжения. Для примера, приведенного на рис. 28, после снятия нагрузки в точке 1 будут наведены напряжения сжатия, а в точке 2 - растяжения. Следовательно, выносливость детали в точке 1 возрастает, а в точке 2 - снизится.
К резкому снижению выносливости болтовых соединений приводит уменьшение радиальных натягов болтов в соединяемых элементах. Схема изменений числа циклов N до разрушения болтового соединения в зависимости, от радиального натяга , где
- диаметр болта , а
- диаметр отверстия, в которое запрессовывают болт, представлена на рис. 29.
При увеличении натяга от i=0 до i = i1 число циклов до разрушения болтового соединения увеличивается в 3 ... 5 раз. Разрушение происходит по соединяемому элементу и носит усталостный характер. Для обеспечения надежной работы болтового соединения необходимо обеспечить натяг в пределах от i1 до i2 (рис. 2.29).
Рис. 2.29.
В процессе эксплуатации на болтовое соединение действуют переменные нагрузки. В результате упругих перемещений болта относительно отверстия материал тонкого поверхностного слоя этих частей соединения пластически деформируется. Это ведет к уменьшению диаметра болта и увеличению диаметра отверстия, т.е. к уменьшению натяга. При холодной распрессовке в процессе разборки болтовых соединении в вышеуказанных местах дополнительно проводят пластическое деформирование. В ряде случаев это приводит к уменьшению натяга до i<i1 (рис. 2.29), т.е. к снижению выносливости болтовых соединений. Для предупреждения этого необходимо при ремонте болтовых соединений восстановить радиальный натяг болтов.
В процессе эксплуатации и ремонта авиационной техники возможно изменение частоты собственных колебаний деталей и конструктивных участков изделий. При совпадении измененной частоты собственных колебании с частотой воздействия внешних нагрузок наступает резонансный режим работы с резким возрастанием величины напряжений в узлах колебаний. В таких условиях наиболее вероятно усталостное разрушение авиационных деталей за очень короткий период эксплуатации ЛА.
В качестве примера может служить разрушение рабочих лопаток компрессора одного из авиационных ТРД. При работе на пыльных аэродромах проточная часть лопаток подвержена газоабразивному изнашиванию. За счет конструктивных особенностей проточной части воздушно-газового тракта двигателя возможно фокусирование попадания абразивных частиц но рабочую поверхность лопатки.
В результате этого наблюдается преимущественно местное изнашивание лопаток (рис. 2.20). Изнашивание в зоне 2 сопровождается повышением собственной частоты колебаний лопатки, а в зоне 1 - уменьшением. На одном из типов ТРД снижение частоты собственных колебаний вследствие местного изнашивания в зоне 1 приводило к возникновению резонансных колебаний таких лопаток и их усталостному разрушению.
Вторым примером резонансного разрушения является разрушение аэродинамического гребня на крыле истребителя МИГ-17. После длительной эксплуатации самолета на аэродинамическом гребне возникала единичная трещина, распространяющаяся от торца гребня. Поврежденный участок отремонтировали в соответствии со стандартными рекомендациями по ремонту обшивки при наличии трещин. Конец трещины засверлили (для снижения концентрации напряжений в вершине трещины). Для усиления поврежденного участка на аэродинамический гребень потайной клепкой приклепали накладку, перекрывающую трещину. После такого ремонта самолет совершил один кратковременный полет. При осмотре после полета на гребне были обнаружены многочисленные трещины усталостного характера. Это могло произойти только вследствие изменения собственной частоты колебаний аэродинамического гребня, вызванной постановкой "усиливающей" накладки. Измененная частота совпала с частотой колебания аэродинамических нагрузок, действующих на гребень во время полета. Возник резонансный режим работы, следствием которого явились многочисленные усталостные разрушения аэродинамического гребня.
Известны также случаи, когда ремонт отдельных участков обшивки планера приводил к такому изменению их собственной частоты колебаний, которая значительно отличается от частоты приложения внешних нагрузок. Выносливость таких участков повышается.
В хвостовой части планера одного типа истребителей вследствие акустических нагрузок зафиксировано усталостное разрушение обшивки. Исследования показали, что разрушение вызвано резонансным режимом работы, при которой частота собственных колебаний участка обшивки совпадала с частотой акустических нагрузок, вызванных работой авиадвигателей. Ремонт поврежденных участков производился сваркой по схеме, приведенной на рис. 2.30.
![]() |
Рис. 2.30. |
Концы трещины засверливались и вдоль трещины обшивка 1 пропиливалась на всю толщину. В пропил вставлялась пластинка 3 из того же материала, что и обшивка. Пластина приваривалась к обшивке сварным швом 2.
Длительная эксплуатация ряда самолетов, отремонтированных по схеме на рис. 2.30 показала, что ни на одном из них повторное усталостное разрушение в области ремонта не возникало. Это вызвано тем, что ремонт по приведенной схеме изменил частоту собственных колебаний участка обшивки. Измененная частота значительно отличается от частоты вынужденных колебаний, что исключает резонансный режим работы.
Резонансный режим работы и усталостное разрушение авиационных деталей могут возникнуть вследствие изменения частоты приложения внешней нагрузки. Это возможно при совпадении измененной частоты приложения внешней нагрузки с частотой собственных колебаний авиационных деталей. Такое совпадение частот было зафиксировано на одном из авиационных двигателей. При неравномерном изнашивании проточной части сопел топливных форсунок изменяется равномерность их производительности. Это ведет к неравномерности скоростей истечения газа в области турбины, что, в свою очередь, вызывает изменение частоты аэродинамических сил, действующих на лопатки турбины. Совпадение частот аэродинамического воздействия с частотами собственных колебаний лопаток турбин вызывает усталостное разрушение последних. В таких случаях усталостные трещины возникают не на одной, а на нескольких лопатках одного ротора.
При ремонте поврежденных участков планера, часто прибегают к постановке усиливающих накладок. Каждая накладка увеличивает жесткость отремонтированного элемента. Для силового элемента, работающего в системе аналогичных элементов (например, стрингера крыла), увеличение жесткости сопровождается увеличением воспринимаемого им усилия в процессе нагружения. В этом случае эксплуатационная нагрузка в первом сечении соединения накладки с силовыми элементами будет увеличиваться пропорционально жесткости. Многократное ее повторение может привести к усталостному разрушению отремонтируемого силового элемента в место его соединения с усиливающей накладкой.
Уменьшение жесткости в процессе ремонта ведет к перегрузке соседних, параллельных ремонтируемому, элементов.
Дата добавления: 2018-11-24; просмотров: 2307; Мы поможем в написании вашей работы! |
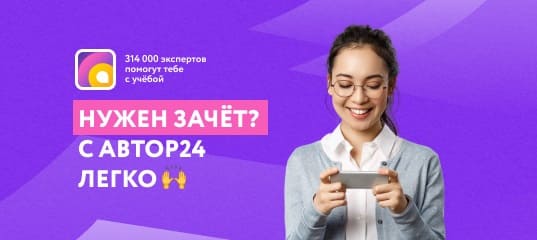
Мы поможем в написании ваших работ!