Основные виды дефектов деталей АТ
Дефект | Причина возникновения и характеристики |
Трещины: литейные | Затруднительная усадка в процессе кристаллизации или при охлаждении |
образовавшиеся в процессе прокатки, ковки материала или штамповки | Низкая пластичность обрабатываемого материала |
закалочные | Нарушение технологии закалки. Выявляются в виде извилистых линий |
шлифовочные | Растягивающие напряжения. Характерны для закаленных сталей и сплавов. Чаще всего располагаются на поверхности в виде сетки |
усталостные | Многократные переменные нагрузки |
водородные | Наводораживание поверхности при электрохимической обработке. Выявляются в виде сетки |
контактные | Взаимодействие расплавов с поверхностью (при пайке, наплавке и т. д.). |
рихтовочные и монтажные | Деформирование упрочненных металлов и сплавов |
Коррозия межкристаллическая | Нарушение сплошности в результате коррозионного повреждения границ зерен алюминиевых и магниевых сплавов |
Основные виды дефектов и деталей АТ продолжение
Дефект | Причина возникновения и характеристики |
Раковины, рыхлости, пористость | Плохое заполнение металлом формы при литье. Выявляются в виде открытых или закрытых полостей |
Неметаллические включения | Попадание в тело отливки газа (пузырей), флюса, шлака и т. п. Могут образовываться и при сварке |
Закаты, заковы, волосовины | Расслоения и складки, вытянутые вдоль направления деформации материала. Часто включают в себя неметаллические прослойки |
Подрез, непровар, прожог | Нарушение технологии сварки - температурных режимов, подготовки поверхности и т. д. |
Ликвация | Химическая, структурная, фазовая неоднородность. Характерна для высоколегированных сталей и сплавов. Не характеризуется нарушением сплошности |
Непроклей | Нарушение сплошности микро- и макроскопического порядка в клеевых и клеемеханических соединениях - результат нарушения технологии или старения клеевых материалов |
Остаточная деформация | Перегрузка конструкции, искажение геометрических характеристик деталей и агрегатов |
Повреждение поверхности деталей, работающих в условиях контактных взаимодействий | Допустимые и аварийные процессы изнашивания. Изменение геометрии и физико-химических свойств поверхности |
|
|
Неисправности, возникшие вследствие длительной эксплуатации, обнаруживают и устраняют частично в процессе эксплуатации летательных аппаратов и, главным образом, на авиаремонтных предприятиях в процессе восстановления работоспособности летательного аппарата.
Термины "ремонт" и "восстановление" часто неверно применяют как синонимы. Поэтому остановимся на рассмотрении их сути.
|
|
Восстановить - означает привести что либо в исходное состояние. Восстановить летательный аппарат - означает привести его свойства, утраченные в процессе эксплуатации, в состояние, соответствующее требованиям технических условий на его поставку. Восстанавливают летные данные летательного аппарата, прочностные характеристики его конструкции, надежность, ресурс. Применительно к деталям и сочленениям восстанавливают: размеры, посадки, форму, прочность, жесткость, износостойкость, выносливость.
Для восстановления служебных свойств летательного аппарата необходимо применять такие технологические процессы ремонта его составных частей, которые обеспечивают восстановление их работоспособности и надежности. Так как точно восстановить износостойкость, выносливость и другие эксплуатационные свойства невозможно, то в ремонтное производство обычно внедряются те технологические процессы, которые обеспечивают повышение этих характеристик. Поэтому служебные свойства восстановленного летательного аппарата должны быть не ниже свойств нового.
|
|
В том случае, когда хотя бы одно служебное свойство машины не восстановлено, нельзя говорить, что она восстановлена. Например, послеремонтный пробег автомобиля значительно меньше пробега нового. Поэтому нельзя сказать, что отремонтированный автомобиль восстановлен.
Для восстановления служебных свойств летательного аппарата необходимо выполнить большой комплекс мероприятий технического, организационного и экономического характера. Для этого необходимо иметь такие мощные формирования, как авиаремонтные заводы. Они должны быть оснащены специальным оборудованием и технической документацией, а так же системой подготовки высококвалифицированных специалистов. Своевременно должно быть обеспечено снабжение запасными частями, расходными материалами, электроэнергией, предусмотрено финансирование ремонтных работ и т.д. Этот комплекс мероприятий, нацеленный на устранение неисправностей на деталях летательных аппаратов и восстановление его свойств, принято называть ремонтом.
Таким образом, под ремонтом авиационной техники понимается комплекс организационных, технических и экономических мероприятий по предупреждению или устранению неисправностей и повреждений с целью сохранения или восстановления ее работоспособности. Эта формулировка объединяет мероприятия по ремонту как в процессе эксплуатации летательных аппаратов, так и на авиаремонтных предприятиях.
|
|
Эксплуатационные мероприятия преследуют цель обеспечения работоспособности изделий в течение установленного межремонтного ресурса. Это различного рода регулировочные работы и работы по устранению неисправностей, обнаруживаемых в процессе осмотров летательных аппаратов. Они не требуют разработки летательного аппарата и сложного ремонтного оборудования.
Восстановление всех характеристик летательного аппарата, в том числе ресурса и надежности, производится на специализированных авиаремонтных предприятиях.
Такое членение ремонтных работ на две части возникло одновременно с зарождением авиации.
Первым авиационным формированием в России был авиационный отряд военного назначения, организованный в 1910 году. Отряд был укомплектован пятью самолетами и насчитывал 7 летчиков. В последующем, во время первой мировой войны, количество отрядов было доведено до 84.
В числе средств, отводимых на содержание отряда, предусматривалось финансовое обеспечение ремонтных работ. Организация ремонта в отряде, его техническое оснащение и обеспеченность специалистами возлагалась на командира отряда. Эксплуатация первых самолетов показала, что в отряде невозможно выполнить сложные ремонтные работы по восстановлению их работоспособности. Для выполнения работ, связанных с разборкой летательного аппарата, необходимо иметь специальное оборудование и подготовленных специалистов. Иметь такое оборудование и специалистов по ремонту в каждом отряде экономически не выгодно. Большую часть времени такое оборудование будет простаивать, а высококвалифицированные специалисты не смогут быть обеспечены работой по специальности. Более целесообразным оказалось выполнять ремонтные работы в разных местах. Те работы, которые не требуют сложного оборудования и высококвалифицированных специалистов по ремонту следует выполнять в перерывах между полетами, не снимая летательный аппарат с эксплуатации. Для выполнения сложных ремонтных работ необходимы специальные ремонтные подразделения.
Первыми ремонтными формированиями в России были авиационные роты, называвшиеся также авиационными парками. В начале первой мировой войны было сформировано 3 авиационных парка с личным составом 600 ... 700 человек каждый. К 1917 г. число парков было доведено до 8. Они обеспечивали крупным ремонтом 600 летательных аппаратов. Парки ведали всеми видами снабжения авиационных отрядов и обеспечивали восстановление самолетов и двигателей того времени. Такая система позволяла максимально использовать каждый летательный аппарат по прямому назначению. Стоимость же его восстановления на специализированном предприятии была минимальной, акачество ремонта достаточно высокое. Система членения ремонтных работ на 2 части была принята в гражданской авиации и существует по настоящее время.
Во время гражданской войны в авиации Красной Армии насчитывалось около 300 боевых самолетов. Крупный ремонт этих самолетов выполнялся в четырех авиационных парках.
В ноябре 1921 г. были разработаны и утверждены "Положение" и "Штаты" главных авиационных и главных утилизационных мастерских. Этим было положено начало организации и технического оснащения авиационных мастерских. Особое внимание было уделено строительству и модернизации ремонтных мастерских при авиационных школах. Там была наиболее интенсивная эксплуатация летательных аппаратов и вызванная ею потребность в ремонтных работах.
Первые авиаремонтные заводы ГА были построены в начале 30-х годов. Для разработки проектов этих заводов, ремонтного оборудования и технологии ремонта авиационной техники были привлечены такие крупные организации, как ЦАГИ, ЦИАМ, Гиправиапром и др.
Бурное развитие авиационной техники после Великой Отечественной войны привело к созданию в системе ГА крупных авиаремонтных заводов, оснащенных современным технологическим оборудованием и укомплектованных квалифицированным инженерно-техническим составом.
Авиаремонтные заводы, кроме своевременного восстановления авиационной техники, решают большие и сложные задачи, по ее модернизации, обеспечивающей повышение надежности и эффективности использования отремонтированной техники.
Большая роль в деле совершенствования ремонта отводится инженеру авиаремонтного производства. Он по роду деятельности объединяет в одном лице организатора работ, воспитателя подчиненного состава, педагога и технолога. Как технолог он должен в совершенстве владеть современными методами определения технического состояния работавших авиационных деталей, уметь находить причины утраты их работоспособности, знать и правильно назначать современные технологические методы восстановления авиационной техники. Он обязан также знать и уметь правильно реализовать современные методы организации управления авиаремонтным производством. Только при успешном решении перечисленных задач возможно своевременное восстановление отходящих в ремонт летательных аппаратов и авиационных двигателей и обеспечение высокой надежности отремонтированных изделий в процессе последующей эксплуатации.
2.0. Эксплуатационная повреждаемость авиационных деталей и соединений. 13
2.1. Основные виды и закономерности изнашивания авиационных деталей при трении скольжения. 13
В процессе эксплуатации деталей, главным образом в материале их поверхностных слоев, возникают различного рода повреждения, накопление которых может привести к нарушению работоспособности авиационного изделия в целом. Основными причинами таких повреждений являются: изнашивание, коррозия, усталость материала, старение, деформации и механические повреждения деталей.
Под изнашиванием понимается процесс постепенного изменения размеров деталей при трении, проявляющийся в отделении с поверхности трения материала или (и) его остаточной деформации.
Износом называют результат изнашивания. Мерой износа u является изменение размеров деталей в направлении, перпендикулярном изнашиваемой поверхности.
Производная по времени величины износа называется скоростью изнашивания, а по относительному пути, пройденному одной из деталей пары трения по отношению к сопряженной,
- интенсивностью изнашивания.
Изнашивание является следствием сложных многочисленных процессов, происходящих на поверхностях трения сопряженных деталей. К этим процессам относятся: механические зацепления микровыступов и молекулярное взаимодействие металлов поверхностного слоя пары трения, многократное упругое и упругопластическое деформирование металла тонких поверхностных слоев контактирующих деталей, химическое воздействие среды, электрические разряды статического электричества, наведенного в материале деталей вследствие трения, изменение структуры и свойств материала тонких поверхностных слоев из-за их нагрева при трении, микрорезание материала поверхностного слоя при попадании на поверхности трения абразивных частиц и т.п. В зависимости от преобладания того или иного процесса различают три вида механического изнашивания: механическое, молекулярно-механическое и коррозионно-механическое.
Под механическим изнашиванием понимается процесс постепенного изменения размеров деталей вследствие механического воздействия сопряженной детали или среды. В зависимости от характера такого воздействия механическое изнашивание подразделяется на абразивное, гидроабразивное, газоабразивное, эрозионное, кавитационное и усталостное.
Абразивное изнашивание возникает при наличии абразивной среды на поверхностях трения контактирующих деталей. Острые абразивные частицы осуществляют микрорезание поверхностного слоя материала детали со снятием микроскопической стружки. Затупленные абразивные частицы вызывают образование рисок с пластическим оттеснением металла без снятия стружки. По сторонам риски образуются наплывы материала детали в виде валиков. Степень пластической деформации в момент их образования настолько велика, что возникают микроразрывы поверхностного слоя в этом месте. Многократное повторение упруго-пластической деформации тонкого поверхностного слоя металла приводит к резкому снижению его пластичности и шелушению.
Иногда абразивные частицы внедряются в поверхностный слой одной из деталей, как правило, из более пластичного материала, и вызывают абразивное изнашивание сопряженной детали из более прочного и твердого материала.
Примером абразивного изнашивания более твердого металла может служить износ вала турбины реактивного двигателя при соприкосновении с гребешками лабиринтного уплотнения корпуса из алюминиевого сплава. В случае выбора до нуля зазора и возникшего соприкосновения вала о гребешками уплотнения в место контакта в процессе работы двигателя выделяется большое количество тепла. В результате тонкий поверхностный слой металла разогревается до большой температуры. На лабиринтном уплотнении из алюминиевого сплава образуется толстая пленка окиси алюминия , обладающая очень высокой твердостью. При последующей работе и соприкосновении вала с лабиринтом эта пленка вызывает глубокие надиры на поверхности стального вала.
Абразивные частицы попадают на поверхности трения из внешней среды, заносятся в системы в процессе производства и ремонта или образуются в процессе эксплуатации. К ним относятся: пыль, твердые окислы алюминия и олова, нагар, продукты износа и коррозии.
Образующиеся в результате износа риски и царапины являются концентраторами напряжения и приводят к резкому снижению долговечности деталей, работающих при переменных нагрузках.
Детали газовоздушного тракта авиационных ТРД подвержены газоабразивному изнашиванию. Наличие в потоке газа абразивных частиц пыли вызывает микрорезание и микроцарапание материала поверхностного слоя деталей ударяющимися о них этими частицами. Повреждения поверхностного слоя каждой абразивной частицей при таком изнашивании значительно меньше, чем при чисто абразивном, описанным ранее. Но так как этих частиц много, то в результате этого вида изнашивания шероховатость поверхности лопаток компрессора и турбины резко увеличивается. Иногда лопатки компрессора изнашиваются до такой степени, что задняя кромка становится острой как бритва.
Наибольшему износу подвержены лопатки последних ступеней компрессора. По-видимому это связано с уменьшением поверхности лопаток, подверженной абразивному изнашиванию и увеличением числа абразивных частиц за счет их дробления на лопатках первых ступеней.
В большей степени изнашиваются лопатки компрессора двигателей, установленных на вертолетах. Объясняется это тем, что при работе вертолета у земли поток воздуха от винта поднимает пыль. Облако пыли долгое время удерживается в воздухе.
Для самолетных двигателей абразивное изнашивание компрессоров проявляется тем резче, чем ближе расположены двигатели к земле. Этот вид изнашивания зависит от времени года и места эксплуатации летательного аппарата. Летом количество пыли в воздухе значительно больше, чем зимой. В Средней Азии песка и пыли больше, чем в центральной России.
Повышенная шероховатость поверхностей проточной части ТРД вызывает увеличение аэродинамического сопротивления и, как следствие, расхода топлива. Выносливость лопаток из-за увеличения шероховатости поверхности снижается. Возможно так же изменение частоты собственных колебаний лопаток. При совпадении измененной частоты колебаний с вынужденной наступает резонансный режим работы и быстрое усталостное разрушение лопаток.
Для предупреждения возникновения аварийных ситуаций из-за перечисленных недостатков необходимо досрочно снимать двигатели с эксплуатации. Например, вертолетные двигатели американских авиакомпаний при эксплуатации в пыльных условиях Южного Вьетнама из-за газоабразивного изнашивания досрочно снимались с эксплуатации при отработке лишь 25 ... 30% установленного им ресурса.
Из-за газоабразивного изнашивания повреждается лакокрасочное покрытие на передних кромках крыла и оперения ЛА.
Кавитационное изнашивание возникает на отдельных участках трубопроводов и агрегатов систем летательных аппаратов и авиадвигателей, омываемых жидкостью, протекающей с большой скоростью. Обычно это изнашивание возникает на участке местного увеличения скорости течения жидкости за счет сужения или изменения направления потока. На омываемой жидкостью площади в один квадратный сантиметр в одну секунду может образоваться до 30 мил. кавитационных каверн. В образовавшуюся каверну устремляются частицы окружающей жидкости, что приводит к микроскопическому гидроудару. За счет гидроударов кратковременные, порядка 0,001 с., пики местного давления достигают 10000 атмосфер.
Ориентировочно, разрыхление материала поверхностного слоя детали осуществляется одной из 30 тыс. каверн. Следовательно, в 1 с. на площади 1 см будет возникать до 1000 разрушающих микроударов. Многократные микроскопические гидроудары вызывают перенаклеп материала поверхностного слоя, сопровождающийся потерей его пластичности. При последующих микроударах в перенаклепанном материале зарождаются микротрещины и начинается шелушение поверхностного слоя металла. При одновременном действии переменных внешних нагрузок может произойти усталостное разрушение детали. Данному виду изнашивания подвержены отсечные кромки золотников прецезионных пар, детали проточной части топливных форсунок, топливные трубопроводы.
Эрозионным изнашиванием называется процесс постепенного разрушения поверхностных слоев металла деталей, находящихся в скоростном потоке газа или жидкости. Величина и скорость изнашивания зависят от механических характеристик материала детали, шероховатости поверхности, направления, скорости, давления и температуры потока газа или жидкости. Разрушение поверхностных слоев металла происходит вследствие механического воздействия на деталь частиц потока, химического взаимодействия и электрических разрядов, возникающих вследствие трения жидкости о деталь. При электрическом разряде в жидкости образуется гидравлический удар. Многократное повторение таких ударов разрушает материал поверхностного слоя.
В чистом виде эрозионное изнашивание практически встречается очень редко. Этому виду изнашивания сопутствует кавитационное, гидроабразивное и газоабразивное изнашивания..
Молекулярно-механическое изнашивание возникает в условиях плотного контакта чистых металлов, свободных от окисной пленки, и малых скоростей скольжения. В результате молекулярного взаимодействия возникают металлические связи (схватывание первого рода). Следующим этапом изнашивания, при смещении одной детали относительно другой, является глубинное вырывание частицы материала из поверхностного слоя одной из этих деталей.
Молекулярно-механическое изнашивание возникает при трении скольжения с малыми скоростями относительного перемещения при больших удельных давлениях. В этом случае возможно выдавливание смазки и разрушение пленки окислов на поверхности деталей. При штатном контакте чистых металлов возникают местные металлические связи (схватывание 1 рода, холодная сварка), вызванные молекулярным взаимодействием чистых металлов сопряженных деталей.
Взаимное последующее перемещение деталей приводит к глубинному вырыву небольших частиц металла поверхностного слоя одной из деталей. На поверхности сопряженной детали происходит наращивание таких частиц. Образующиеся наросты могут вызвать заедание при взаимном перемещении деталей пары трения, действуют как абразив и часто являются причиной заклинивания, приводящего к выходу агрегатов из строя. В результате такого изнашивания создаются резкие концентраторы напряжения, приводящие к значительному снижению выносливости изношенных деталей при переменных нагрузках.
Причинами молекулярно-механического изнашивания могут явиться искажения геометрической формы деталей и перекосы, возникающие вследствие неправильной сборки деталей и нарушения обработки деталей. Большие удельные давления, возникающие в местах контакта на малых площадях, приводят к выдавливанию смазки и разрушению окисной пленки.
Причиной схватывания могут быть абразивные частицы, попавшие на поверхность трения. При вдавливании абразивной частицы в поверхность металла происходит его пластическое деформирование. По краям образующейся риски возникают наплывы деформированного металла. В точке контакта этих наплывов с поверхностью сопряженной детали возникают условия, способствующие развитию молекулярно-механического изнашивания.
По этой причине происходило заклинивание золотниковой пары всережимного регулятора частоты вращения плунжерного топливного насоса. Начавшееся схватывание имело прогрессирующий характер и завершилось разрушением золотника при работе двигателя. Аналогичные разрушения зафиксированы ив других прецезионных парах.
Вероятность попадания абразивных частиц на поверхности трения зависит от качества очистки жидкости и формы кромок золотниковых поясков. Попадание частиц загрязнения между пояском золотника и гильзой облегчается при наличии закругления или скоса кромок. В этом случае в зазор будут вклиниваться частицы загрязнения, размер которых даже превышает его величину. Поэтому для уменьшения вероятности заклинивания золотников в гильзе, кромки их поясков должны быть "острыми": торцевая и боковая поверхности пояска должны быть строго перпендикулярны. Выполнение этого требования улучшает характеристики регулирования топливного агрегата.
Попадание абразивных частиц в топливо может вызвать заклинивание плунжера топливного насоса. Проведенный анализ отказов топливных насосов по этой причине показал, что источником абразивных частиц являлись выкрашивания материала поверхностного слоя колец подшипников, сфер плунжеров ирабочей дорожки наклонной шайбы.
Аналогичное повреждение может быть вызвано загрязнением зазора относительно мягкими отложениями, которые непосредственно сами не деформируют материал поверхностного слоя пары трения. Одностороннее скопление таких частиц может вызвать металлический контакт с противоположной стороны, особенно при наличии искажений поверхности типа волнистости или повышенной шероховатости, возникшей при механической обработке деталей, вследствие коррозии или изнашивания.
Изнашивание в коррозионной среде называется коррозионно-механическим.
Коррозионно-механическое изнашивание возникает при трении деталей в условиях коррозионной среды. На деталях авиационной техники встречаются два вида такого изнашивания: окислительное и фреттинг-коррозия.
Окислительному виду изнашивания подвержено большинство авиационных деталей, работающих в условиях скольжения.
Данный вид изнашивания назван окислительным потому, что материал поверхностного слоя и продукты износа оказываются сильно окисленными за счет взаимодействия с кислородом воздуха. Особенно интенсивно кислород диффундирует в те участки металла, где возникает пластическая деформация. Проникший кислород вступает с металлом в химические соединения и образует с ним твердые растворы. Твердость материала и износостойкость образованного нового поверхностного слоя резко увеличиваются.
Вследствие пластических деформаций материала поверхностного слоя при трении скольжения и увеличении его объема за счет проникновения кислорода и образования химических соединений в нем возникают напряжения сжатия. В результате выносливость деталей, подверженных окислительному изнашиванию,
значительно увеличивается. Этому способствует уменьшение шероховатости изнашиваемой поверхности.
По внешнему виду участки деталей, работавших в условиях окислительного изнашивания, напоминают тщательно полированные. Их поверхность покрыта стекловидной пленкой, представляющей собой тонкий, насыщенный кислородом слой металла.
Для обеспечения дальнейшей надежной работы деталей, подверженных окислительному изнашиванию, не рекомендуется их разукомплектовывать и снимать при ремонте приработанный, обладающий повышенной износостойкостью и выносливостью поверхностный слой материала. Однако следует иметь в виду, что в процессе длительного окислительного изнашивания возможно образование толстых хрупких окисных пленок на поверхности деталей (вторая фаза изнашивания). Такие пленки выкрашиваются, что ведет к увеличению скорости и создания условий абразивного изнашивания. Абразивом являются продукты изнашивания (окисленные частицы металла).
Вид изнашивания и величина износа u зависят от скорости взаимного проскальзывания поверхностей трения. При малых скоростях проскальзывания, не превышающих величины V1 (рис. 2.1), и большом давлении в месте контакта наиболее характерным является молекулярно-механическое изнашивание, обладающее большой интенсивностью. При больших скоростях (при V > V1) наступает окислительное изнашивание, отличающееся значительно меньшими величинами износа. При большом увеличении скорости (V>V2)возникает новый вид изнашивания, вызванный изменением структуры и свойств материала тонкого поверхностного слоя вследствие его нагревания до большой температуры за счет тепла, выделяемого при трении. Интенсивность изнашивания резко возрастает. Из-за тепловой природы изнашивания его называют тепловым или изнашиванием схватывания 2 рода.
Рис. 2.1.
Вторым видом коррозионно-механического изнашивания является фреттинг-коррозия. Этот вид изнашивания характерен для деталей с малоподвижными или неподвижными посадками, работающих в окислительной среде при переменных нагрузках.
Вследствие упругой деформации конструкции, вызываемой переменными нагрузками, возникают переменные по направлению и малые по величине относительные перемещения микроскопических участков материала поверхностных слоев в местах контакта сопряженных деталей. Эти перемещения вызывают усталостные повреждения материала вблизи точек контакта поверхностей. Постепенное накопление таких повреждений вызывает усталостное разрушение микрообъемов материала в месте контакта. Отделившиеся частицы окисляются кислородом воздуха и скапливаются в полостях между деталями, где нет непосредственного контакта поверхностей. Про-дукты износа интенсифицируют коррозионный процесс материалов контактирующих деталей.
Модель разрушения поверхности при фреттинг-коррозии:
а – стадия упрочнения поверхностных слоев;
б – стадия накопления усталостных повреждений;
в – стадия усталостно-коррозионного разрушения поверхности;
1 – высокодисперсный слой;
2 – зона повреждаемости первого типа;
3 – металлические частицы;
4 – окислы;
5 – зона повреждаемости второго типа;
6 – зона фактического контакта (зона повреждаемости первого типа);
7 – сопряженная поверхность.
Коррозионное повреждение ускоряет процесс усталостного повреждения, а оно - интенсивность коррозии. Таким образом, оба процесса (коррозия и усталостное повреждение) усиливают друг друга. В этих условиях скорость изнашивания материала поверхностных слоев сопряженных деталей резко возрастает. Дальнейшее развитие процесса изнашивания может привести к усталостному разрушению одной из деталей.
Все вышеперечисленные виды изнашивания, за исключением первой фазы окислительного, являются аварийными. Они вызывают резкое снижение выносливости и износостойкости авиационных деталей. Такое снижение тем больше, чем больше величина концентрации напряжений, вызванная изнашиванием, и прочность материала детали. Авиационные же материалы обладают высокой прочностью и чувствительны к концентрации напряжений.
Для ориентировочной оценки количественного влияния повреждений поверхностного слоя типа рисок на долговечность изделий из высокопрочной авиационной стали З0ХГСН2А был выполнен следующий эксперимент. Стандартные образцы из этой стали диаметром 10 мм изготавливались и термически обрабатывались по технологии изготовления деталей шасси и испытывались на выносливость при чистом изгибе. Максимальные напряжения в материале поверхностного слоя в процессе испытаний были равны 0,7 ... 0,75 предела прочности (временного сопротивления) указанной стали. Долговечность образцов (среднее число циклов до разрушения) была принята за 100%.
На оставшейся половике образцов были нанесены алмазным резцом кольцевые надрезы глубиной 30 мкм. Долговечность этих образцов составила лишь 7%от исходной. Царапина глубиной меньше толщины человеческого волоса снизила исходную долговечность в этих условиях более чем в 10 раз. Поэтому детали с явными признаками значительной концентрации напряжений (риски, царапины, коррозионные раковины и т.п.) подлежат замене на пригодные к дальнейшей эксплуатации.
Закономерности изменения величины износа большинства перечисленных видов изнашивания имеют вид, представленный на рис. 2.2. По оси абсцисс отложена наработка рассматриваемой пары трения. Сплошная кривая характеризует изменение величины износа, а пунктирная - скорости изнашивания. В интервале наработки от 0 до происходит накопление повреждений материала поверхностного слоя. В этот период износа деталей не наблюдается. Начиная с
, износ и скорость изнашивания резко увеличиваются.
Рис. 2.2.
Из рассмотренных выше видов износа только первая фаза окислительного изнашивания вызывает увеличение выносливости и износостойкости деталей. Закономерности изнашивания в этом случае значительно отличаются от вариантов, представленных на рис. 2.2. Такие закономерности, характерные для первой фазы окислительного изнашивания, представлены на рис. 2.3. Изменение величины износа представлено сплошной кривой, а скорости изнашивания - пунктирной. Различают три периода изнашивания.
Рис. 2.3.
Начальный период, при , характеризуется изменением исходного микрорельефа поверхностей трения и называется периодом приработки. Микронеровности, полученные при механической обработке деталей, постепенно разрушаются. Шероховатость поверхности приобретает специфическое строение, зависящее от режима работы трения и условий смазки.
Скорость изнашивания в начале приработки максимальна, затем уменьшается, достигая минимального значения к концу приработки ( ). Такое изменение скорости изнашивания определяется постепенным увеличением площади контакта поверхностей трения, т.е. уменьшением фактического давления в месте контакта. Шероховатость и свойства материала поверхностного слоя изменяются, приспосабливаясь к условиям изнашивания и обеспечивая минимальную его скорость.
Следующий период, соответствующий наработке в пределах от до
называется периодом установившегося изнашивания. Скорость изнашивания в этот период близка к минимальной и постепенно увеличивается к моменту перехода к следующему этапу. Величина износа u накапливается по закону, близкому к линейному.
Для ряда пар трения при наступает период аварийного изнашивания, характеризуемый резким увеличением скорости и величины износа. Переход к аварийному изнашиванию сопровождается изменением физической картины взаимодействия материалов поверхностных слоев деталей пары трения, т.е. к другому качественному процессу, возникшему вследствие накопившегося количественного изменения в процессе предыдущего изнашивания. При изнашивании в условиях смазки постепенное увеличение зазора между контактирующими деталями приводит в конечном счете к изменению вида трения и к увеличению скорости изнашивания. Вид трения изменяется от жидкостного к полужидкостному и к полусухому.
Сохранение зависимости изменения величин u и в период установившегося изнашивания, близкой к линейной (рис. 2.3), возможно только при неизменности всех факторов, влияющих на этот процесс. К этим факторам в первую очередь следует отнести давление в месте контакта деталей, скорость скольжения и условия смазки.
Если в момент (рис. 2.4) изменяется хотя бы один из этих факторов, то вновь начинается период приработки к новым условиям изнашивания. Износ увеличивается, а его закономерность характеризуется участком 1-2. Новое изменение основных факторов, влияющих на изнашивание, в момент
(даже возвращение к исходным значениям) приводит к изменению изнашивания по кривой 2-3.
Рис. 2.4.
Из приведенного примера видно, что из двух машин наиболее интенсивно изнашивается та, у которой чаще всего изменяется режим работы. Поэтому после одинаковой наработки минимальное изнашивание однотипных деталей будет у двигателей, установленных на дальнемагистральных самолетах, а максимальное - у двигателей, установленных на самолетах местных линий.
Проведенные исследования установившегося механического изнашивания материалов позволили получить, аналитическую зависимость величины износа , где р - давление в месте контакта деталей; l - путь трения и к - коэффициент, зависящий от свойств материалов пары трения и условий изнашивания, к которым в первую очередь относится смазка поверхностей. Определив значение коэффициента к в начальный период установившегося изнашивания, можно прогнозировать величину износа при последующей эксплуатации пары трения.
Дата добавления: 2018-11-24; просмотров: 842; Мы поможем в написании вашей работы! |
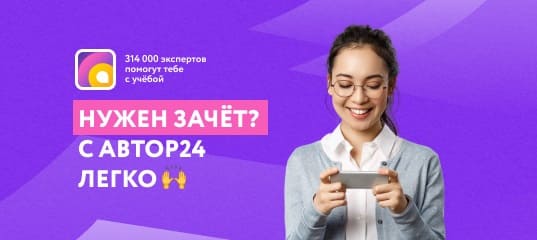
Мы поможем в написании ваших работ!