Рассчитаем припуски на обработку шейки вала.
ФЕДЕРАЛЬНОЕ АГЕНТСТВО РФ ПО ОБРАЗОВАНИЮ
Государственное образовательное учреждение
высшего профессионального образования
«Тульский государственный университет»
Кафедра «Автомобили и автомобильное хозяйство»
РАЗРАБОТКА ТЕХНОЛОГИЧЕСКИХ ПРОЦЕССОВ
ИЗГОТОВЛЕНИЯ И РЕМОНТА ДЕТАЛЕЙ АВТОМОБИЛЕЙ
Учебное пособие по дипломному проектированию
для студентов специальности
190601 «Автомобили и автомобильное хозяйство»
Тула, 2009
УДК 621.7, 621.9
Дорохин Н.Б., Груничев А.В.
Разработка технологических процессов изготовления и ремонта деталей автомобилей: Учеб. пособ. по дипломному проектированию. /Н.Б. Дорохин, А.В. Груничев. – Тула: Изд-во ТулГУ, 2009. – 143 с.
Рассматриваются все этапы выполнения раздела «Изготовление или ремонт деталей автомобилей» дипломного проекта по специальности 190601 «Автомобили и автомобильное хозяйство», включающие разработку маршрутной и операционной технологии изготовления или ремонта деталей. Изложение материала сопровождается примерами технологического процесса, расчетов припусков и режимов резания.
Табл. 20. Ил. 47. Библиогр.: 55 назв.
Печатается по решению библиотечно-издательского совета Тульского государственного университета.
Рецензент: доктор тех. наук, профессор кафедры «Технология машиностроения» Тульского государственного университета А.С. Ямников
|
|
кандидат тех. наук, доцент кафедры «Сервис и ремонт машин» Орловского государственного технического университета А.Л. Севостьянов
© Дорохин Н.Б., Груничев А.В., 2009 © Издательство ТулГУ, 2009 |
1. ЦЕЛИ И ЗАДАЧИ ВЫПОЛНЕНИЯ
ТЕХНОЛОГИЧЕСКОГО РАЗДЕЛА ДИПЛОМНОГО ПРОЕКТА
Целью выполнения технологического раздела дипломного проекта является закрепление, углубление и систематизация знаний методики проектирования технологических процессов изготовления и ремонта деталей автомобилей по всем ее этапам, включающим:
¾ анализ задания и исходных данных, служебного назначения деталей, технических требований;
¾ разработку маршрутной и операционной технологии изготовления или ремонта деталей.
2. ТЕМАТИКА ТЕХНОЛОГИЧЕСКОГО РАЗДЕЛА
ДИПЛОМНОГО ПРОЕКТА
Темой технологического раздела дипломного проекта является разработка технологического процесса изготовления или ремонта одной из деталей автомобилей для мелкосерийного или единичного производств. Рекомендуются детали средней сложности, средних размеров и массы, с использованием заготовок, получаемых из пруткового или листового проката, литьем или штамповкой, с различными видами механической обработки и с использованием преимущественно универсального металлорежущего оборудования.
|
|
В отдельных случаях по решению руководителя могут выполняться технологические разработки по техническому обслуживанию, текущему ремонту, диагностированию технического состояния узлов и систем автомобиля.
3. ИСХОДНЫЕ ДАННЫЕ ДЛЯ ПРОЕКТИРОВАНИЯ
ТЕХНОЛОГИЧЕСКОГО ПРОЦЕССА
Исходными данными для разработки технологического процесса изготовления детали являются:
– рабочий чертеж, определяющий материал, конструктивные формы и размеры детали;
– технические условия на изготовление детали, характеризующие точность и качество обработки ее поверхностей, а также особые требования (твердость, термическая обработка, подгонка по массе и т.п.);
– программа выпуска;
– сведения о наличии оборудования, производственных площадей и других местных производственных условиях.
Исходными данными для разработки технологического процесса ремонта детали являются:
– рабочий или ремонтный чертеж детали;
– технические условия и карта дефектации, приведенные в руководствах по капитальному ремонту автомобилей отдельных марок;
– перечень из 2-3 дефектов, подлежащих устранению в разрабатываемом технологическом процессе.
|
|
4. СОДЕРЖАНИЕ ТЕХНОЛОГИЧЕСКОГО РАЗДЕЛА ДИПЛОМНОГО ПРОЕКТА
Студент выполняет следующие основные этапы проектирования технологического процесса изготовления детали автомобиля.
1. Анализ чертежа детали и анализ технологичности ее конструкции.
2. Определение типа производства.
3. Выбор метода получения заготовки и выбор маршрута обработки детали.
4. Разработка маршрутной технологии механической обработки детали.
5. Расчет припуска для 2–3-х поверхностей обрабатываемой детали.
6. Нормирование 2–3-x операций механической обработки детали.
В графическую часть выносится рабочий чертеж детали и карта маршрутной технологии изготовления детали.
Если темой технологического раздела ДП является разработка технологического процесса ремонта (восстановления) детали автомобиля, тогда студент выполняет следующие основные этапы проектирования.
1. Анализ различных способов восстановления детали.
2. Выбор одного из способов восстановления детали для каждого из дефектов, указанных в задании.
3. Разработка схем технологических процессов для устранения каждого дефекта.
4. Разработка общей маршрутной технологии восстановления детали с разработкой содержания основных операций (т.е. разработка переходов).
|
|
5. Расчет припусков, операционных размеров и нормирование для 2–3-х операций (например, для операций токарной, вибродуговой наплавки и шлифовальной).
В графическую часть выносится ремонтный чертеж детали и карта маршрутной технологии ремонта детали.
5. ОБЩАЯ МЕТОДИКА И ПОСЛЕДОВАТЕЛЬНОСТЬ
ПРОЕКТИРОВАНИЯ ТЕХНОЛОГИЧЕСКОГО
ПРОЦЕССА ИЗГОТОВЛЕНИЯ ДЕТАЛИ
Процесс проектирования состоит из комплекса взаимосвязанных и выполняемых в определенной последовательности этапов.
1. Выбор метода получения заготовки и установления предъявляемых к ней требований.
2. Выбор технологических баз.
3. Выбор комплекса последовательно выполняемых методов (маршрута) обработки отдельных поверхностей.
4. Составление маршрута обработки детали в целом.
5. Предварительное проектирование операций.
6. Размерный анализ и установление технологических допусков.
7. Расчет промежуточных (операционных) припусков, операционных размеров и размеров заготовки.
8. Уточнение содержание операций и степени концентрации технологических переходов.
9. Выбор оборудования, инструментов и приспособлений.
10. Расчет режима резания.
11. Определение настроечных размеров.
12. Уточнение схем установки и закрепления заготовки для выдачи технического задания для конструирования приспособления.
13. Установление квалификации исполнителей и расчет нормы времени.
14. Оформление технологической документации.
5.1. Анализ конструкции детали на технологичность
Проектированию технологического процесса предшествует подробное изучение рабочего чертежа детали, технических условий на ее изготовление и условий ее работы в изделии. В частности, изучают способ и правильность простановки размеров, требования по точности и шероховатости поверхностей и др.
Нередко конструкторы завышают требования по точности, шероховатости, что усложняет и удорожает изготовление детали. В этом случае технолог предлагает соответствующие коррективы и на совместном обсуждении с конструктором они находят правильное решение.
При контроле чертежа выявляются возможности повышения технологичности конструкции детали, т.е. оценивают в какой мере учтены возможности наиболее экономичных и производительных технологических методов изготовления детали применительно к программе выпуска и условиям производства. Технологичная конструкция детали, в частности, должна отвечать следующим основным требованиям:
1) заготовка должна быть рациональна для данного типа производства;
2) все поверхности должны быть доступны для обработки;
3) возможно применение нормального режущего инструмента;
4) допуски и шероховатости должны быть указаны рационально;
5) конструкция термообрабатываемых деталей не должна иметь резких переходов в объемах металла, что может приводить к появлению концентраций напряжений после термообработки.
5.2. Выбор метода получения заготовок
Конструктор изделия устанавливает материал и его марку по имеющимся стандартам. Он назначает также необходимую термическую обработку детали. Учитывая условия ее работы в машине, он может указать предпочтительный способ получения заготовки (ковка вместо литья, ковка вместо проката и т.д.). На основе этих данных технолог выбирает конкретный метод получения заготовки.
Выбор метода определяется:
1. Технологической характеристикой материала детали, т.е. его литейными свойствами или способностью претерпевать пластические деформации при обработке давлением.
2. Конструктивными формами и размерами детали.
3. Требуемой точностью выполнения заготовки, качеством ее поверхностей.
4. Программой выпуска и сроками ее выполнения.
5. Наличием требуемого оборудования.
Выбранный метод должен обеспечивать наименьшую себестоимость детали, т.е. затраты на материал, изготовление заготовки и последующую механическую обработку вместе с накладными расходами должны быть минимальными.
С повышением точности изготовления заготовки и приближением ее формы к конфигурации готовой детали, объем механической обработки заметно снижается. Однако, при малой программе выпуска не все методы могут оказаться рентабельными из-за того, что расходы на оснастку для заготовительных процессов экономически не окупаются.
На рис. 1. и 2. показаны зависимости себестоимости заготовки и себестоимости детали от величины допуска на размер заготовки. С увеличением допуска, себестоимость заготовки снижается. На рис. 2 цифрой 0 обозначена себестоимость получения заготовки, а 1,2,3 – соответственно себестоимость выполнения предварительной, чистовой и отделочной механической обработки. Из рис. 2. следует, что минимум себестоимости достигается в данных производственных условиях при комплексном сочетании точности получения заготовки и методов дальнейшей механической обработки.
Рис. 1 ![]() | ![]() |
Зная технологические характеристики заготовительных методов, можно подобрать сравнительно небольшое количество соответствующих конкретным производственным условиям. Предварительных выбор метода может производится по таблицам и графикам (рис. 3. и 4)
![]() |
Рис. 3. График для выбора штампованных заготовок и заготовок из проката: 1 – прокат; 2 – свободная ковка; 3 – штамповка на молотах; 4 – штамповка на горизонтально-ковочной машине (ГКМ); 5 – штамповка выдавливанием; 6 – прокатка на специальных станках.
Рис. 4. График для выбора литых заготовок: 1 – литье в землю при ручной формовке; 2 – тоже при машинной формовке; 3 – литье в оболочковые формы; 4 – литье по выплавляемым моделям; 5 – литье в кокиль; 6 – литье под давлением
5.3. Выбор технологических баз. Составление схем базирования
5.3.1. Основные положения
Заготовка на каждой операции механической обработки устанавливается в приспособление или на стол станка. Физически процесс установки включает в себя этап базирования и закрепления.
Базирование – придание заготовке или изделию требуемого положения относительно выбранной системы координат. Закрепление – приложение к заготовке сил или пар сил для обеспечения постоянства ее положения, достигнутого при базировании.
Различают следующие основные виды поверхностей деталей: рабочие, базовые (основные и вспомогательные) и свободные.
Рабочиеповерхности принимают непосредственное участие в работе детали (рис. 5).
Основные базовые поверхности определяют положение данной детали относительно других деталей в механизме (основные конструкторские базы). С помощью вспомогательных базовых поверхностей определяется положение других деталей, присоединяемых к рассматриваемой детали (вспомогательные конструкторские базы). К рабочим и базовым поверхностям предъявляют высокие требования к точности их изготовления, расположения и качественным показателям поверхностного слоя.
Свободные поверхности — все остальные поверхности, обычно не сопрягаемые с поверхностями других деталей в процессе работы. Они создают конструктивную форму, обеспечивают жесткость, не требуют высокой точности и могут оставаться в состоянии поставки исходной заготовки (т. е. иногда вообще не обрабатываются).
Базовые поверхности обрабатывают первыми, а затем относительно них обрабатывают остальные поверхности заготовок. По базовым поверхностям устанавливают заготовки в приспособления станков при их обработке (технологические базы).
Конструкторская база – база, используемая для определения положения детали или сборочной единицы в изделии. На чертеже детали или изделия чертежной конструкторской базой может быть любая поверхность, линия или точка относительно которых координируется положение любой другой поверхности линии или точки.
Технологическая база – база, используемая для определения относительного положения заготовки или изделия в процессе изготовления или ремонта.
5.3.2. Правило шести точек при базировании детали и правила составления схем базирования
В большинстве случаев деталь, будучи установленной на столе станка или в приспособлении, должна быть лишена всех шести степеней свободы.
Из механики известно, что каждое свободное абсолютно твердое имеет шесть степеней свободы и что его положение вполне определяется шестью координатами относительно трех взаимно перпендикулярных плоскостей.
На рис. 6 показана деталь, которая располагается в координатном пространстве XYZ таким образом, что нижняя плоскость детали параллельна координатной плоскости ZOX, а задняя боковая плоскость параллельна координатной плоскости XOY.
Расположим на нижней плоскости детали три произвольные точки (1, 2, 3). Расстояние их до координатной плоскости ZOX при принятом условии параллельности плоскостей – одинаково. Таким образом, три координаты предопределяют расположение детали призматической формы на плоскости, параллельной координатной плоскости ZOX и, следовательно, лишают деталь трех степеней свободы: перемещения вдоль оси Y и поворота относительно координатных осей Z и X. Поясним это, рассмотрев последовательное приложение этих связей к детали. Первая связь, приложенная к точке 1, лишает заготовку возможности перемещаться вдоль оси Y, приложение второй связи к точке 2 лишает заготовку возможности поворота вокруг оси Z, а третья связь – вокруг оси X.
Связи, приложенные к точкам 4 и 5, расположенным на задней боковой плоскости, лишают деталь еще двух степеней свободы: перемещения вдоль оси Z и поворота относительно оси Y. Последней шестой степени свободы – перемещения вдоль оси Х деталь будет лишена, если приложить связь к точке 6, расположенной на левой торцовой плоскости.
Допустим, что координатные плоскости представляют собой поверхности, принадлежащие приспособлению. Если привести в соприкосновение с этими поверхностями соответствующие поверхности детали, то шесть координат, определяющих ее положение в пространстве, превращаются в шесть опорных точек (рис. 6,б и 7,а).
Для определения положения изделия необходимо и достаточно иметь шесть опорных точек, большее их число приведет к неопределенностибазирования и внесет дополнительные погрешности в определение положения изделия.
На рис. 7,б приведена схема базирования для рассмотренного примера, где каждая базовая точка изображается по правилам ГОСТ 3.1107-81 (рис. 7,в).
| |
а – призматическая деталь в координатной системе | б – призматическая деталь на столе станка |
Рис. 6. Координирование призматической детали |
Рис. 7. Схема базирования детали призматической формы
Базирование цилиндрических деталей имеет некоторые специфические особенности. На рис. 8,а цилиндрическая деталь располагается в координатном пространстве ZYX таким образом, что ее ось параллельна оси OZ. При выполнении этого условия на цилиндрической поверхности детали находятся две образующие, одна из которых (1-2) параллельна координатной плоскости ZOY, а вторая (3-4) – координатной плоскости ZOX.
Рис. 8. Распределение базовых точек на поверхностях цилиндрической детали: а – в координатном пространстве; б – при контакте с координатными плоскостями
Таким образом, четыре координаты, определяющие положение цилиндрической поверхности детали в координатном пространстве, лишают деталь четырех степеней свободы: перемещений вдоль осей X и Y и поворотов относительно тех же осей.
Координата, определяющая положение торца детали относительно координатной плоскости YOX, лишает деталь еще одной степени свободы – перемещения относительно оси Z.
Последней степени свободы деталь должна быть лишена за счет ориентации в угловом положении относительно оси по шпоночному пазу; или, если не важно угловое положение детали, за счет сил трения между цилиндрической поверхностью и зажимными элементами приспособления.
Такая схема базирования цилиндрических деталей характерна для базирования, например в прямоугольной призме, станочных тисках (рис. 9).
Базирование цилиндрических деталей в самоцентрирующих приспособлениях (трехкулачковые патроны, цанговые патроны и др.) имеет некоторые отличия от рассмотренного выше случая.
Сначала рассмотрим базирование длинной цилиндрической заготовки в трехкулачковом патроне с длинными кулачками. Казалось бы, что следует проставить 4 базовые точки на образующие цилиндра, ориентирующие заготовку вдоль оси патрона, (рис. 9). Однако базовые точки неподвижны в системе координат станка и любое изменение диаметра заготовки в обрабатываемой партии вызовет смещение оси заготовки (рис. 10,а). Но в самоцентрирующем приспособлении этого не происходит. Здесь ось заготовки всегда совмещается с осью патрона (рис. 10,б). Значит именно ось заготовки, а не наружная цилиндрическая поверхность будет являться базой. В данном случае она называется скрытой базой. Таким образом, базовые точки следует проставлять на оси заготовки, и схема базирования будет выглядеть так, как показано на рис. 10,б. Базовая точка 6 здесь предотвращает проворот заготовки вокруг своей продольной оси и образуется за счет сил трения между заготовкой и рабочими поверхностями кулачков. Эта точка изображается приложенной к условному рычагу, жестко связанному с поверхностью заготовки. Зачернение базовой точки на половину высоты означает, что она образуется после приложения направленного зажима.
Рис. 9. Схема базирования длинной цилиндрической заготовки в прямоугольной призме
Рис. 10. Отличия схемы базирования цилиндрической заготовки в прямоугольной призме (а) от схемы базирования в трехкулачковом самоцентрирующем патроне (б). При разных диаметрах заготовки на рис а) положения осей всех заготовок различно. На рис б) оси всех заготовок совпадают, поэтому ось заготовки можно считать скрытой базой
Иногда для упрощения изображения схемы базовые точки 2 и 4 на рис. 10,б разворачивают (рис. 11). Однако, рекомендуется придерживаться более корректной, с методической точки зрения, схемы базирования на рис. 10,б.
Рис. 11. Допускается упрощенное изображение схемы базирования, когда базовые точки 2 и 4 развернуты (а). Тонкими линиями с засечками на концах обозначают, по какой реальной поверхности происходит базирование (б)
На рис. 12 приведены примеры других наиболее распространенных схем базирования.
а) | ![]() |
![]() | |
г) |
Рис. 12. Схемы базирования: а) – в трехкулачковом патроне для дисковой заготовки; б) – цилиндрической детали в центрах; в) – в призме; г) – корпусной детали по плоскости и двум пальцам, один из которых срезан для облегчения установки детали
5.3.3. Взаимосвязь конструкторских и технологических баз
В ряде случаев конструкторские базы оказываются неудобными для использования их в качестве технологических. Переходя к новым базам, технолог обязан ввести новые технологические размеры и назначить на них допуски с таким расчетом, чтобы выдерживались с требуемой точностью заданные конструктором размеры. Это необходимо, когда обработка партии деталей будет проводиться на настроенном оборудовании.
Из приводимого ниже примера видно, что для обеспечения необходимой посадки ползуна вполне оправданной является простановка размера 10+0,1 мм (рис. 13). Конструкторской базой при этом является поверхность, на которую садится замыкающая планка. Использование конструкторской базы в качестве технологической при обработке паза под ползун приводит к "неудобной" установке – деталь закрепляется снизу и сила резания воспринимается зажимом.
Рис. 13. Пример взаимосвязи конструкторской и технологической базы
Допустим теперь, что при выполнении той же операции обработки паза деталь устанавливается на нижнюю плоскость. Настройка положения инструмента производится в этом случае относительно не меняющей своего положения технологической базы. Следовательно, выдерживается размер 25. Размер же 35, связывающий технологическую базу с конструкторской, был получен на одной из предыдущих операций. Интересующий нас размер 10 получается автоматически последним, т. е. он является замыкающим в трехзвенной размерной цепи, где допуски размеров связаны равенством:
Если принять допуск то
.
Таки образом, допуски вновь вводимых производных технологических размеров оказываются значительно более жесткими, чем ранее назначенные допуски конструкторских размеров.
На основании приведенного примера можно сделать следующие выводы.
1. Замена конструкторских баз технологическими и связанный с этим пересчет размеров и допусков приводит к значительному ужесточению допусков на вновь вводимые технологические размеры.
2. Пересчет размеров и допусков следует приводить с помощью размерных цепей. При этом конструкторский размер является замыкающим звеном цепи, а вновь вводимые технологические размеры – составляющими звеньями.
3. Отходить от конструкторских баз целесообразно лишь в случае, если это дает заметное преимущество, например с точки зрения установки и закрепления детали, или если это будет способствовать в целом общему повышению качества и точности изделия.
5.3.4. Использование настроечных баз
При работе на настроенных станках наивысшая точность размеров обрабатываемой заготовки получается тогда, когда эти размеры проставлены непосредственно от тех поверхностей заготовки, относительно которых может быть произведена настройка станка, т. е. могут быть выставлены упоры станка или режущие инструменты. К таким поверхностям (занимающим неизменное положение на станке) относятся в первую очередь опорные поверхности заготовки, что и предопределяет широкое их использование в крупносерийном производстве в качестве технологических баз.
Поверхности, образуемые при обработке заготовки на данном установе и связанные с другими обрабатываемыми поверхностями непосредственными размерами, также являются базами. Они называются настроечными базами.
При построении операции обработки заготовки с использованием настроечной базы опорная поверхность заготовки является технологической базой только для обработки самой настроечной базы (см. рис. 14, поверхность А), с которой она связана непосредственно размером. Технологической базой для обработки всех остальных поверхностей заготовок в этом случае служит не опорная, а настроечная база заготовки.
![]() | ![]() |
Рис. 14. Использование настроечной базы: а – при одновременном фрезеровании нескольких плоскостей (поверхность В ориентируется от настроечной базы А); б – при обработке заготовки на револьверном станке (настроечная база А – обрабатываемый на первом переходе торец) |
К наилучшим способам обработки поверхностей А и В заготовки (рис. 14, а), связанных между собой размером b, следует отнести такой, когда обе эти поверхности фрезеруются одновременно за один установ. При этом настройка станка, обеспечивающая выполнение интересующего нас размера, осуществляется относительно одной из обрабатываемых поверхностей заготовки (безразлично А или В) путем подбора размеров фрез. Поверхность А будет служить для поверхности В настроечной базой.
Другим примером использования поверхности, обрабатываемой за один и тот же установ, в качестве настроечной базы может служить обработка заготовки на револьверном станке (рис. 14, б). Заготовка опирается поверхностью М на соответствующий упор зажимного устройства станка; однако эта поверхность, являясь опорной технологической базой для обработки торца А заготовки на размер h, не будет таковой для всех остальных торцовых поверхностей заготовки (В, С, D, Е), обрабатываемых на размеры b, с, d, а. Положение поверхностей В, С, D и Е определяется при настройке станка не положением поверхности М, а положением поверхности А, относительно которой производится установка упоров.
Особенно ярко выявляются преимущества настроечных баз при использовании автоматов, многорезцовых станков, станков с копировальными устройствами и станков с числовым программным управлением и обрабатывающих центров.
5.3.5. Рекомендации по выбору технологических баз
При проектировании технологического процесса изготовления детали необходимо стремиться к тому, чтобы, по возможности, все поверхности детали обработать и измерить от одних и тех же технологических баз, т. е. обеспечить принцип постоянства баз.
Лучшим вариантом можно считать полную обработку заготовки с одного установа. В большинстве случаев практически невозможно и экономически не выгодно полностью обрабатывать деталь от одних и тех же технологических баз, но следует стремиться весь технологический процесс обработки детали производить с минимальным числом смены баз.
Ниже приведены общие рекомендации по выбору технологических баз.
1. В качестве технологических следует использовать конструкторские базы (принцип единства баз).
2. Следует стремиться к использованию на различных установках одних и тех же баз (принцип постоянства баз).
3. Для обеспечения неподвижности заготовки или изделия в избранной системе координат на них необходимо наложить шесть связей – шесть точек, для размещения которых необходим комплект из трех базовых поверхностей.
4. Принятые базы не должны по возможности давать погрешностей базирования. При наличии погрешностей базирования необходимо расчетом проверить их влияние на точность получаемого размера.
5.3.6. Выбор баз при выполнении первой операции
1. Для обеспечения правильного расположения системы обработанных поверхностей относительно необработанных рекомендуется в качестве баз на первой операции использовать поверхности, которые в готовой детали останутся черными, необработанными.
2. Если по условиям обработки детали или ее эксплуатации требуются снять с какой-либо поверхности, подлежащей обработке, минимальный припуск, то именно эту поверхность и следует принять в качестве базы (черновой) на первой операции.
3. В качестве установочной базы (черновой) на первой операции следует принять поверхность наибольших размеров.
Черновая база используется только один раз на первой операции. Повторный установ деталей на черновые базы не допустим.
5.4. Выбор маршрута обработки отдельных поверхностей детали
Выбор маршрута производят исходя из требований рабочего чертежа и принятой заготовки.
По заданным квалитетам точности и качеству поверхностей детали и с учетом ее размера, массы и конфигурации, выбирают один или несколько возможных методов окончательной обработки, а также тип соответствующего оборудования.
Зная вид заготовки, решают задачу о выборе первого метода маршрута. Если, например, точность заготовки невысока, то обработку данной поверхности начинают с использования чернового метода. При точной заготовке сразу можно назначить чистовую, а в некоторых случаях и отделочную обработку.
Исходя из завершающего и первого методов маршрута обработки, устанавливают промежуточные методы. При этом исходя из того, что каждому методу окончательной обработки предшествует один или несколько возможных предварительных, менее точных методов. Так, чистовому развертыванию предшествует предварительное, а предварительному развертыванию – чистовое зенкерование, а ему – сверление.
После чернового растачивания нельзя, например, применять развертывание, т.к. для устранения всех погрешностей предшествующей обработки, зубья развертки работали бы с недопустимо большой глубиной резания.
Таким образом, технологический допуск на промежуточный размер и качество поверхности, полученной на предыдущей ступени обработки, должны находится в тех пределах, при которых возможно нормальное использование намеченного последующего метода обработки.
При составлении маршрута обработки в целом необходимо учитывать следующие рекомендации.
1. Сначала обрабатывают поверхности, которые на последующих операциях будут использоваться в качестве технологических баз (центровые отверстия, базовые торцы, шейки, плоскости и т.п.).
2. Затем обрабатывают остальные поверхности в последовательности, обратной степени их точности, т.е. чем точнее должна быть обработана поверхность, тем позднее она обрабатывается.
3. Заканчивается обработка той рабочей поверхности, которая является наиболее точной и имеет наибольшее значение для детали с точки зрения ее функционирования.
4. В конец маршрута часто выносят обработку легкоповреждаемых поверхностей, к которым, например, относят резьбы, особенно наружные, и т.п.
5. Операция термообработки (закалка или цементация и закалка), если она предусмотрена, должна располагаться после лезвийной обработки (точение, сверление, нарезание резьбы и пр.) и перед операциями с абразивными методами отделочной обработки поверхностей (шлифование, полирование и др.).
В производстве точных машин обработку деталей часто разделяют на три последовательные стадии: черновую, чистовую и отделочную (чистовую). Такое расчленение маршрута производят по следующим соображениям. На черновой стадии имеют место сравнительно большие погрешности, вызванные деформациями технологической системы от сил резания и закрепления заготовки, а также ее интенсивным нагревом. Чередование в этих условиях черновой и чистовой обработки не обеспечивает заданную точность. Такой принцип построения маршрута не во всех случаях является обязательным. Так при большей жесткости технологической системы и малых размерах обрабатываемых поверхностей окончательная обработка отдельных элементов может выполняться и в начале маршрута. Данный принцип в определенной степени противоречит также принципу концентрации переходов, когда в одной операции могут выполняться переходы черновой и чистовой обработки (например, изготовление деталей из прутка на полуавтомате).
Если деталь подвергают термической обработке, то техпроцесс расчленяют на две части: до термической обработки и после. Для устранения возможных короблений часто приходится предусматривать правку деталей или повторную обработку отдельных поверхностей для обеспечения заданной точности и шероховатости.
Последовательность обработки в определенной степени зависит от способа простановки размеров. В первую очередь следует обрабатывать те поверхности, относительно которых на чертеже координировано большое количество других поверхностей. Так, на детали на рис. 15. сначала обрабатывают поверхность А, а затем в произвольном порядке поверхности Б, В и Г.
Операции вспомогательного или второстепенного характера (сверление мелких отверстий, наложение фасок, прорезка мелких канавок, зачистка заусенцев и т.п.) обычно выполняют на стадии чистовой обработки. На данном этапе маршрута последовательность выполнения этих операций часто может меняться: она не влияет на качественные и экономические показатели процесса.
Операции технического контроля намечаются после тех этапов механической обработки, на которых вероятно появление большого количества бракованных деталей, перед сложными и дорогостоящими операциями, а также в конце обработки.
5.5. Построение операций механической обработки
При проектировании операции уточняют ее содержание, намеченное ранее при составлении маршрута, устанавливают последовательность переходов, выбирают оборудование, инструменты, приспособления или дают задание на их проектирование, назначают режимы резания, определяют норму времени.
Для проектирования операций необходимо знать:
1) маршрут обработки заготовки;
2) схему ее базирования и закрепления;
3) обрабатываемые поверхности и точность их обработки;
4) поверхности, обработанные на предшествующих операциях, и точность их обработки;
5) припуск на обработку.
Разделение маршрута на отдельные операции выполняется исходя из определения, что операция – это законченная часть технологического процесса, выполняемая на отдельном рабочем месте, одним или несколькими рабочими. Таким образом, все работы, выполняемые на одном станке, будут включены в одну операцию.
Операции могут делиться на два и более установов. Установом называется часть операции, выполняемая при неизменном закреплении обрабатываемой заготовки или собираемого узла. Поэтому, если на токарной операции заготовка вала перезакрепляется на станке для обточки сначала с одной, а затем с другой стороны, то в этой операции выделяют два установа, обозначаемые: установ А и установ Б. Для операций с одним установом обозначение «установ А» в операционных картах не указывают.
5.6. Разработка маршрутной технологии
Первоначально следует определить модель используемого на каждой операции станка. Затем разработать структуру операции, то есть разделить ее на установы, позиции и переходы, наметить или подобрать вид станочного приспособления (трехкулачковый патрон, цанговый патрон, центры с поводковым патроном, кондуктор, самоцентрирующие тиски и т.п.), подобрать необходимый режущий инструмент, определить средства контроля.
Результаты разработки маршрутной технологии заносятся в табл. 1.
Таблица 1
Карта маршрутной технологии
Номер | Наименование операции и содержание перехода | Эскиз обработки | Оборудование | Приспособле-ние | Режу-щий инструмент | Средства измерения | |
операции | перехода | ||||||
1 | 2 | 3 | 4 | 5 | 6 | 7 | 8 |
При заполнении табл. 1 необходимо соблюдать следующие основные требования.
Карта должна содержать все операции по изготовлению рассматриваемой детали, включая и термическую обработку, мойку и т.д. Для последних следует заполнять только графы 1, 2 и 3 в табл. 1.
В графе 1 должны быть указаны порядковые номера операций (05, 10, 15 и т.д., кратный 5)
В графе 3 следует приводить полную структуру операции. Если операция состоит из двух и более установов, то после наименования операции следует указать "Установ А" и рассматривать затем содержание этой части операции. После ее завершения надо указать "Установ Б" и рассматривать его содержание. В общем случае заполненная графа 3 имеет вид:
Номер | Наименование операции и содержание перехода | |
опе-ра-ции | пере-хода | |
05 | 1 2 3 | Наименование операции (например Токарная) Установ А Выполнить определенные действия, составляющие вспомогательный или технологический переход. Выполнить следующий переход. . . . . . . . . . следующий переход. |
|
7 8
| Установ Б . . . . . . . . . . . . . . . . . . . . . . . . . . . . . . . . . . . . . . . . . . . . . . . . . . . . . . . . . . . . . . . . .
и так далее. |
Содержание перехода должно быть изложено в повелительном наклонении со ссылкой на номер поверхностей, обрабатываемых на данном переходе. Допускается полная или сокращенная форма записи содержания операции [21]. Полную запись следует использовать при отсутствии эскиза обработки или для отражения всех действий, выполняемых на черновых переходах, когда на эскизе обработки изображены размеры, получаемые после чистовой обработки на данной операции. Во всех остальных случаях следует использовать сокращенную запись, при условии, что эскиз обработки достаточно полно отражают всю необходимую информацию по обработке резанием. Например, полная запись:
Сверлить 4 сквозных отверстия с последующим зенкованием фасок, выдерживая d = 10+0,2, l =40±0,05, Ð 90 ° ±30 ¢ и 1 ´ 45 ° , согласно чертежу.
Сокращенная запись ссылается на эскиз с обозначенной поверхностью 1:
Сверлить 4 отв. 1.
В графе 4 должен быть изображен эскиз обработки, проводимой на данной операции. Если операция не разделяется на установы и позиции, то для нее изображается только один эскиз. На нем должны быть указаны:
¾ обрабатываемые на операции поверхности, выделенные красным цветом (или утолщенными линиями) и обозначенные соответствующим номером;
¾ технологические базы, обозначенные по соответствующим правилам;
¾ размеры, выдерживаемые при обработке. Они должны быть заданы обязательно с допусками в цифровом виде и от технологических баз или от обработанных ранее поверхностей на этом же установе. Если операционные размеры еще не известны, так как не определены припуски на обработку, то на данном этапе следует провести размерные линии и указать допуски на размеры. Значения размеров надо проставить после расчета припусков или их назначения по таблицам и определения операционных размеров;
¾ шероховатость обрабатываемых поверхностей.
Эскиз должен содержать необходимое количество проекций, видов, размеров для полной передачи всей информации: размеры и шероховатости для тех поверхностей, которые обрабатываются на данной операции и на данном установе; схему базирования заготовки по правилу 6 базовых точек (см. п. 5.3.2).
Если операция разделяется на установы, то для каждого установа должен приводиться самостоятельный эскиз, выполненный по изложенным требованиям.
Если операция или установ разделяются на позиции, то изображается общий эскиз для всей операции или каждого установа по всем вышеприведенным требованиям, а затем эскизы для каждой позиции с указанием обрабатываемых на позиции поверхностей, размеров и шероховатости (без обозначения баз).
В графе 5 указываются тип и модель станка. Например: "Токарно-винторезный широкоуниверсальный станок 1К62".
В графе 6 – вид приспособления. Например: "Самоцентрирующие тиски с призматическими губками".
В графе 7 указывается вид инструмента (например: "Фреза трехсторонняя дисковая") с основными характеристиками: диаметром, числом режущих зубьев, маркой материала режущей части. Следует обязательно указывать ГОСТ на выбранный для данной обработки инструмент.
В графе 8 указываются контрольно-измерительная оснастка и те размеры или параметры, которые проверяются с ее помощью (например, пробка на разм. Æ 45+0,2).
5.7. Пример разработки маршрутного технологического процесса механической обработки
Необходимо разработать маршрутный технологический процесс обработки ступенчатого вала-шестерни в условиях мелкосерийного или единичного производства. Материал детали – Сталь 45 ГОСТ 1050-88, твердость HRCЭ 40...45.
Эскиз детали показан на рис. 16:
- модуль зубьев – 5,5 мм;
- число зубьев – 12;
- точность зубчатого колеса по 7 степени, шероховатость зубьев R а 1,25;
- неуказанные предельные отклонения
Рис. 16. Рабочий чертеж вала-шестерни
Анализ чертежа показывает, что наиболее высокие требования по точности и качеству предъявляются к опорным шейкам, прилегающим к ним торцам и зубчатым поверхностям.
Конструкция детали в основном отработана на технологичность, она обладает высокой жесткостью, обеспечивается свободный доступ инструмента к обрабатываемым поверхностям, допускает использование нормального режущего инструмента.
Учитывая конфигурацию, размеры вала и мелкосерийный масштаб производства, в качестве исходной выбираем заготовку из пруткового проката.
Выбор технологических баз производим, исходя из основных положений базирования. При обработке валов, как правило, следует выбирать в качестве баз центровые отверстия вала и один из торцов, т.к. центровые отверстия обеспечивают высокую точность базирования при шлифовании шеек вала и зубьев.
Последовательность и характер обработки каждой из поверхностей определим, исходя из предъявляемых к ней требований по точности и шероховатости.
Общий план обработки может быть принят следующим:
¾ черновое обтачивание всех поверхностей;
¾ чистовое обтачивание всех поверхностей;
¾ обработка фасонных поверхностей: зубчатого венца и шпоночного паза;
¾ термическая обработка;
¾ шлифование шеек Æ48h6 и Æ40k6 и прилигающих к ним торцов;
¾ шлифование зубьев.
Требования к зубчатым поверхностям могут быть выполнены зубофрезерованием н шевингованием. Однако, учитывая потерю точности, ухудшение шероховатости после термической обработки, а также высокую твердость материала детали, целесообразно заменить шевингование зубьев на шлифование.
Тип производства и конфигурация детали определяет выбор универсального оборудования: токарно-винторезные, зубо-фрезерные, зубошлифовальные и круглошлифовальные станки.
После расчета припусков, режимов резания и решения других технологических задач маршрут технологического процесса сводим в таблицу (см. ниже). Эту таблицу вместе с рабочим чертежом выносят в графическую часть дипломного проекта на 1 лист формата А1. В этом случае лист делят (но не разрезают) на 3 формата: 1 лист А3 с рабочим чертежом детали; 1 лист А3 и 1 лист А2 с картой маршрутной технологии.
Ниже представлено то, как могут выглядеть эти форматы, применительно к рассмотренному примеру техпроцесса.
5.8. Припуски на механическую обработку
Припуском называют слой материала, удаляемый в процессе механической обработки с заготовки в целях достижения заданной точности и качества обработанной поверхности.
Установление оптимальных припусков на обработку и технологических допусков на размеры заготовок по всем переходам имеет существенное технико-экономическое значение. Необоснованное увеличение припусков ведёт к перерасходу материала на изготовление деталей, вызывает необходимость введения дополнительных технологических переходов, увеличивает трудоёмкость процессов обработки, затраты энергии и режущего инструмента. В результате недостаточных припусков возрастает вероятность получения брака, что также повышает себестоимость выпускаемой продукции.
5.8.1. Методы определения припусков
В машиностроении широко применяют два метода определения припуска на механическую обработку: опытно-статистический и расчётно-аналитический.
Первый метод основан на использовании опытно-статистических данных, часто стандартизованных, которые составляются на основе обобщения и систематизации производственного опыта. Недостаток этого метода заключается в том, что припуск назначают без учёта конкретных условий построения технологических процессов. Так общие припуски назначают без учёта маршрута обработки данной поверхности, а промежуточные – без учета схемы установки заготовки и погрешностей предшествующей обработки. В результате припуски часто необоснованно завышены, так как они ориентированны на условия обработки, при которых припуск должен быть наибольшим во избежание брака. Данный метод, позволяющий существенно сократить сроки проектирования заготовки, используется преимущественно в условиях единичного и мелкосерийного производства.
Согласно расчётно-аналитическому методу величина припуска должна быть такой, чтобы при его срезании устранялись погрешности обработки и дефекты поверхностного слоя, на предшествующих технологических переходах, а также погрешности установки заготовки, возникающие на данной операции. Данный метод основан на учёте конкретных условий выполнения технологического процесса обработки. Он выявляет возможности экономии материала заготовки и снижения трудоёмкости механической обработки при проектировании новых и анализе существующих технологических процессов. Имея большую трудоёмкость по сравнению с опытно-статистическим методом, расчётно-аналитический метод преимуществен, но используется в условиях серийного и массового производств.
5.8.2. Виды припусков
Припуски на механическую обработку разделяют на операционные (промежуточные) и общие.
Операционным припуском называют слой материала, который необходимо срезать для выполнения только одной операции (одного перехода).
Величина операционного припуска, измеряемого в направлении, перпендикулярном обработанной поверхности, определяется разностью размеров, получаемых на предшествующей и выполняемой ступенях обработки какой-либо элементарной поверхности. Так, для поверхности деталей, обработанной в 3 перехода (рис. 17), операционные припуски определяют следующим образом:
Рис. 17. Схема снятия операционных припусков
Общим припуском называют слой материала, который необходимо срезать с заготовки при выполнении всех операций для получения поверхности деталей.
Для рассматриваемого случая
Для охватывающих поверхностей
Различают одностороннее и двустороннее расположение припусков.
Пример одностороннего расположения припуска показан на рис. 17.
Двустороннее расположение припусков может быть симметричным и асимметричным.
Симметричное расположение припуска имеет место, например при бесцентровом шлифовании (рис. 18), развёртывании, чистовом точении и шлифовке в центрах, нарезании резьбы метчиком и т. п.
Рис. 18. Симметричное расположение припуска
Согласно рис. 18 припуск на сторону
Двусторонний припуск
.
Асимметричным припуском является такой двусторонний припуск, составляющие которого на противоположных сторонах заготовки имеют различную величину, что может иметь место как при последовательной, так и при одновременной обработке двух сторон детали.
Примером асимметричного припуска может служить неравномерный припуск при обтачивании заготовок с биением. В качестве примера рассмотрим также одновременное фрезерование двух торцов валика на фрезерно-центровальном полуавтомате. Заготовку устанавливают в самоцентрирующие призмы с базированием в осевом направлении по левому торцу (рис. 19) посредством откидного упора.
Припуск на обработку правого торца Припуск на обработку левого торца
При этом
Рис. 19. Схема снятия ассиметричного припуска при обработке торцов вала на фрезерно-центровальном станке
Припуск на обработку правого торца в рассматриваемом случае будет больше, чем на обработку левого, поскольку положение правого торца будет иметь неопределённость положения относительно базирующей поверхности в пределах поля допуска на длину заготовки. Эта неопределённость, являющаяся частью погрешности обработки, полученной на предшествующей операции, должна быть устранена, т. е. являться составной частью припуска на обработку правого торца. Левый, базирующий торец, такой неопределённости положения иметь не будет и для него данная составляющая припуска равна нулю.
Операционный припуск
5.8.3. Схемы снятия операционного припуска
Операционные размеры как на предшествующей, так и на выполняемой ступенях обработки не могут быть выдержаны абсолютно точно. Поэтому фактическая величина припуска может колебаться в некоторых пределах.
На величину фактического припуска в ряде случаев оказывает существенное влияние податливость технологической системы. Рассмотрим случай фрезерования плоской поверхности торцовой фрезой (рис. 20)
Рис. 20. Влияние податливости технологической системы на величину фактического припуска
При наибольшем предельном размере заготовки наибольшая глубина резания вызывает появление наибольшей силы резания, а значит, более значительные деформации технологической системы, чем при наименьшем предельном размере заготовки
. В первом случае с поверхности заготовки будет срезан слой материала глубиной
, во втором –
.
Величина – общая составляющая величин
и
называется абсолютно минимальным припуском.
Колебание фактических величин операционного припуска для рассмотренного случая определится выражением:
т. е.
Таким образом, колебание величины фактического операционного припуска с учётом упругих деформаций технологической системы численно равно разности допусков на размеры, полученные на предшествующей и выполняемой ступенях обработки.
При обработке отверстий мерным инструментом (свёрлами при рассверливании, зенкерами, развёртками, протяжками) размер обработанной поверхности не зависит от упругих деформаций технологической системы, а следовательно не зависит от размеров заготовки. В основном он обуславливается погрешностью самого мерного инструмента.
Рассмотрим обработку отверстия (рис. 21). Здесь damax и damin – наибольший и наименьший возможные диаметры отверстия, полученного на предшествующем переходе; d в u – размер, полученный, на выполняемой ступени обработки без учета износа инструмента.
Рис. 21. Схема расчета операционного припуска при обработке
отверстия
Тогда максимальная и минимальная величины фактического припуска
z’ вmax = d в u – damin,
z’ вmin = d в u – damax:
Колебание величины фактического припуска
Dz в = z ’вmax – z ’вmin = damax – damin
т.е.
Dz в=d da
Таким образом, при использовании мерных инструментов колебание величины фактического операционного припуска на рассматриваемую ступень обработки равно допуску на размер, полученному на предшествующей ступени обработки.
При осуществлении отделочных операций (шлифование, хонингование и т.д.), независимо от того, имеет ли заготовка максимальный или минимальный в пределах допуска размеры, на выполняемой ступени обработки могут быть получены как максимальный, так и минимальный размеры заготовки.
Отметим особенность отделочных операций. В отличие от ранее рассмотренных примеров, такие методы обработки как шлифование, хонингование и т.п., являются многопереходными, что и обеспечивает, например, нивелирование действия на получаемый размер разности размеров заготовки и разности сил резания.
Рассмотрим на примере отделочных операций различные виды припусков (рис. 22):
Рис. 22. Различные виды припусков при выполнении отделочных операций
Z вmin – абсолютно минимальный припуск – слой материала, подлежащий срезанию в той ситуации, когда на предшествующей ступени обработки использован весь допуск, а на данной – совсем не использован;
Z вгар – гарантированный припуск, превышающий абсолютно минимальный на величину слоя материала, соответствующего допуску на выполняемую ступень обработки:
z вгар = z вmin + d в
Z вном – номинальный припуск, имеющий место, когда допуск на предшествующей ступени обработки не был использован, а на выполняемой ступени получена деталь с максимальным (номинальным) размером:
z вном = z вmin + d а
Z вmax – максимальный припуск:
z вном = z вmin + d а + d в
Колебание величины фактического операционного припуска при отделочных операциях равно сумме допусков на размеры предшествующей и выполняемой ступеней обработки.
DZ в = z вmax – z вmin = d а + d в
Конечной целью определения припусков на выполнение отдельных ступеней обработки является установление операционных размеров и размеров заготовки, которые задаются их номинальными размерами с указанием допустимых отклонений.
В качестве расчетного операционного припуска следует принимать величину номинального припуска, численно равного разности номинальных размеров, получаемых на предшествующей и выполняемой ступенях обработки. Далее в изложении термин "припуск" будет относиться к величине расчетного (номинального) припуска.
5.8.4. Схемы снятия общего припуска
При определении общего и операционных припусков в зависимости от вида обрабатываемой поверхности нужно различать два случая:
1. При обработке охватываемых поверхностей, когда размеры уменьшаются, следует использовать "схему вала" (рис. 23).
2. При обработке охватывающих поверхностей, когда размеры увеличиваются, следует использовать "схему отверстия" (рис. 24)
Рис. 23. Простановку допусков при обработке охватываемых поверхностей, когда размеры уменьшаются, выполняют по "схеме вала"
Рис. 24. Простановку допусков при обработке охватывающих поверхностей выполняют по "схеме отверстия"
3. Размеры заготовок, получаемых методами литья, пластического деформирования, обычно выдерживают с отклонениями в обе стороны от номинала. При определении величины операционного припуска на первую ступень обработки в качестве d а следует принимать только нижнее отклонение d заг размера заготовки от номинала при расчете по "схеме вала" у только верхнее отклонение – при расчете по "схеме отверстия".
5.8.5. Расчетно-аналитический метод определения припусков
5.8.5.1. Составляющие операционного припуска
В целях достижения требуемых точности и качества обработанной поверхности необходимо для каждого перехода предусмотреть припуск, компенсирующей как погрешности предшествующего перехода, так и некоторые погрешности, имеющие место на выполняемом переходе. Очевидно, эти погрешности и должны рассматриваться как составляющие операционного припуска.
Все составляющие можно разбить на две группы:
1) характеризующие состояние элементарной поверхности заготовки, подлежащей обработке, т.е. составляющие, характеризующие микрогеометрию обрабатываемой поверхности и глубину ее дефектного слоя;
2) характеризующие неопределенность положения обрабатываемой поверхности на данном переходе.
Рассмотрим составляющие припуска, сохраняя их традиционные обозначения [27].
На – составляющая припуска, характеризующая высоту микронеровностей, полученных при обработке рассматриваемой поверхности на предшествующей операции (переходе).
Для определения численной величины составляющей припуска На следует пользоваться значениями Rz высоты микронеровностей по соответствующему ГОСТу.
Для каждого способа обработки и режима резания существуют рекомендации по определению Rz. Например, для получистового точения с подачами 0,5 – 0,6 мм/об шероховатость обрабатываемой поверхности составляет Rz 80. Что касается высоты микронеровностей поверхности заготовок, полученных литьем или методами пластичного деформирования, то для их прогнозирования также существуют определенные рекомендации для различных конструкционных материалов.
Ta – cоставляющая припуска, характеризующая глубину дефектного слоя, полученного при выполнении предшествующей операции (переходе).
На первой операции глубина дефектного слоя зависит от метода получения заготовки. Например, литые заготовки из чугуна имеют твердый "отбеленный" слой. Для предотвращения поломок инструмента глубина резания должна быть больше глубины отбеленного слоя. Кроме того, на поверхности как литых так и штампованных заготовок могут быть раковины, трещины, волосовины, окалина. На заготовках, полученных горячей штамповкой, имеются обезуглероженный слой. Такой же слой иногда образуется после нагрева под термическую обработку. Дефектный слой на заготовках, длительное время хранящихся под открытым небом, может так же состоять из скорродировавшегося металла. При механической обработке на поверхности стальных деталей также может образоваться дефектный слой в виде наклепа, но его толщина, как правило, на порядок меньше.
При механической обработке слой, включающий в себя микронеровности и дефекты обрабатываемой поверхности, должен быть срезан.
Если не принимать во внимание никаких других погрешностей, величина припуска на обработку поверхности должна быть не ниже суммы высоты микронеровностей и глубины дефектного слоя, полученных на предшествующей ступени обработки данной поверхности.
Таким образом, припуск, при односторонней обработке Z в ³ На + Та, при двусторонней обработке Z в ³ 2(На + Та).
d а – составляющая припуска, характеризующая возможное отклонение в положении обрабатываемой поверхности относительно режущего инструмента из-за колебания размера самой поверхности, обусловленного неточностью ее обработки на предшествующей операции (переходе).
В качестве численного значения составляющей припуска d а следует принимать допуск на размер поверхности, полученной на предшествующей ступени обработки.
Составляющую d а учитывают только при расчете двусторонних симметричных припусков. Напомним, что в случае допусков с отклонениями в обе стороны от номинала, следует брать лишь нижние отклонения при расчетах по "схеме вала" и только верхние отклонения при расчетах по "схеме отверстия".
r а – составляющая припуска, учитывающая неопределенность положения обрабатываемой поверхности из-за пространственных геометрических отклонений, не имеющих непосредственной связи с допуском. Обычно это коробление и другие пространственные деформации обрабатываемой поверхности.
Рассмотрим примеры учета составляющей припуска r а .
Рис. 25. Погрешность коробления литой заготовки
Пусть необходимо фрезеровать плоскость заготовки, полученной литьем и имеющей коробление (рис. 25). Рассматриваемая составляющая определяется по формуле
,
где r 0 – удельное коробление, мкм/мм.
Для корпусных литых заготовок r 0 = 1.4 – 2 мкм/мм.
Рассмотрим обточку и подрезку торца заготовки, полученной штамповкой (рис. 26). Из-за смещения матриц по плоскости разъема штампа образуется погрешность, которую и относят к рассматриваемой (на правой части рис. 26 показана лишь часть припуска, состоящие из погрешности r а).
Рассмотрим обточку детали из прутка, полученного методом горячего проката, имеющего искривление оси в пределах допуска (рис. 27). Точка К будет наиболее удаленной от режущего лезвия точкой. Рассматриваемая составляющая припуска
r а = r кр = ОО’.
Рис. 26. Погрешность, образуемая смещением матриц
по плоскости разъема штампа
Устранение погрешности заготовки возможно при выполнении условия
или
d в £ da – 2 r a .
Рис. 27. Обточка детали из прутка, имеющего искривление оси
Следовательно припускZ в ³ 2r а .
При обработке в центрах r a = r кр = r 0 L /2,
где r 0 – удельная кривизна, мкм/мм.
При консольном закреплении r a = r кр = r 0 L .
Следовательно, выбор схемы базирования в данном случае предопределяет величину припуска.
Если заготовка имеет несколько отклонений в положении обрабатываемой поверхности, причем эти отклонения носят пространственный характер, то для определения суммарной величины r a ее составляющие следует складывать как векторы. Например, при черновой обточке поковок вала величина r a складывается из кривизны оси заготовки и смещения по плоскости разъема матриц штампа.
Тогда
Необходимо учитывать, что после каждой ступени обработки происходит копирование погрешностей обработки в уменьшенном виде. Расчет скопированных погрешностей производят при помощи коэффициента уменьшения погрешности. Так, после первой ступени обработки
,
после второй ступени ,
после третьей ступени – как правило r a » 0.
D а – составляющая припуска, определяющая возможное смещение обрабатываемой поверхности относительно базирующих поверхностей самой заготовки.
Обрабатываемая поверхность может занимать различные положения относительно базирующей поверхности. Возможны четыре варианта:
1. Обрабатываемая поверхность является базирующей поверхностью. В этом случае Δа=0.
2. Положение обрабатываемой поверхности относительно базирующей определяется одной координатой (т.е. одним или несколькими размерами в направлении одной из координат). В этом случае, Δа≠0.
3. Положение обрабатываемой поверхности относительно базирующих поверхностей определяется двумя координатами. В этом случае ∆а1≠0, ∆а2≠0.
4. То же самое для трех координат: ∆а1≠0, ∆а2≠0, ∆а3≠0.
Рассмотрим второй вариант. При этом возможно два случая: назначение одностороннего и двустороннего припусков.
Рассмотрим пример назначения одностороннего припуска (рис. 28). Пусть необходимо подрезать торец валика, обрабатываемого в центрах. Размер Б ∑ , образующейся при этом, является замыкающим в размерной цепи, и его допуск равен сумме допусков составляющих звеньев
δБΣ=δБ1+δБ2.
Рис. 28. К расчету допуска на размер
Величина, рассматриваемой погрешности Δа= f (δБΣ).
Пусть необходимо обработать поверхности 1 и 2 детали (рис. 29).
Составляющая припуска (рис. 29,а)
¾ для поверхности 1 Δа1=f(δА1):
¾ для поверхности 2 Δа2=f(δА2).
Для рис. 29,б:
¾ для поверхности 1: Δа1=f(δВ1)=f(δА1):
¾ для поверхности 2: Δа2=f(δВΣ), где δВΣ=δВ1+δВ2.
Рис. 29. Зависимость величины Δа от способа
простановки размеров при обработке поверхностей 1и 2
Следовательно, для рис. 29,б: Δа1<Δа2. Таким образом, на величину Δа оказывает влияние как выбор схемы базирования, так и способ простановки размеров.
Рассмотрим назначение двустороннего припуска для второго варианта. Пусть обтачивается вал в центрах (рис. 30). Положение обрабатываемой поверхности относительно базирующих поверхностей – центровых отверстий – определяется диаметром d заготовки и погрешностью зацентровки ц, т.е.
Δа= ц,
Рис. 30. Погрешность зацентровки
Погрешность зацентровки рекомендуют рассчитывать по формуле
ц=0,25
мм,
где – допуск на диаметр заготовки.
Paссмотрим другие примеры обработки (рис. 31). Во всех случаях (несоосность или эксцентриситет) рассматриваемая составляющая припуска Δа= .
Рис. 31. Погрешность эксцентриситета поверхностей
Рассмотрим более сложный случай (рис. 32), когда имеется несоосность и погрешность зацентровки
. В этом случае рассматриваемая составляющая припуска
.
Рис. 32. Наличие несоосности и погрешности зацентровки
Рассмотрим назначение двустороннего припуска. Пусть необходимо обработать отверстие (рис. 33), ось которого определяется относительно базирующих поверхностей двумя координатами.
Рис. 33. К расчету составляющей припуска, зависящей от смещения оси отверстия вдоль двух осей
Смещение оси отверстия от настроенного инструмента зависит от допусков на размеры Г и В, т. е.
Рассматриваемая составляющая припуска.
Расчёты величины Δа для варианта, когда положение обрабатываемой поверхности определяется тремя координатами, производят аналогичным образом.
– погрешность установки. Она являющаяся комплексной погрешностью, так как в общем случае может складываться их трёх видов погрешностей:
– погрешности базирования;
– погрешности закрепления;
– погрешности положения установочных элементов приспособления.
Данные погрешности относят к одной группе, так как они связаны со способом установки заготовки в приспособлении. В отличие от уже рассмотренных погрешностей, обусловленных погрешностями обработки на предшествующих операциях, погрешность установки связаны с выполняемым переходом.
Все составляющие погрешности установки определяются величиной и направлением в пространстве. Поэтому они суммируются как векторные величины.
Рассмотрим сущность и методы определения отдельных составляющих погрешности установки.
Погрешность базирования При установке заготовок (деталей) в приспособлении в целях их обработки в некоторых случаях может иметь место погрешность базирования. Она определяет величину возможного отхода рассматриваемой поверхности от режущих кромок настроенного на размер инструмента из-за несовпадения установочной базы детали с установочной базой приспособления.
При совпадении этих баз погрешность базирования равна нулю, например при использовании самоцентрирующих приспособлений (трехкулачковые токарные патроны, токарные центра и пр.).
Установочной базой детали называют поверхность или совокупность поверхностей, линий или точек детали, определяющих положение детали при ее установке в приспособлении или на станке.
Установочной базой приспособления называют поверхность пли совокупность поверхностей установочных элементов приспособления, определяющих положение детали при ее установке для обработки.
Установочные технологические базы могут быть реальными (материальные поверхности деталей и установочных элементов приспособлении) и условными (такие геометрические элементы, как оси цилиндрических поверхностей, плоскости симметрии и т.д.).
Рассмотрим пример определения погрешности базирования и ее влияние на величину операционного припуска. На рис. 34 показана схема установки детали в приспособлении для обработки ее левого торца на предварительно настроенном фрезерном станке.
Рис. 34. Определение погрешности базирования заготовки в приспособлении
Условной установочной базой приспособления, ориентирующей заготовку в горизонтальном направлении, является ось срезанного пальца УБпр которая одновременно является и настроечной базой. Установочной базой детали является ось технологического отверстия УБд. В идеальном случае (рис. 34, а) эти базы (ось пальца и ось отверстия) совпадают, при этом
Допустим, что у всех устанавливаемых в приспособлении заготовок расстояние от торца, подлежащего обработке, до оси установочного отверстия остается постоянным, то есть А = const Но так как между поверхностью отверстия детали и поверхностью установочного пальца всегда имеется зазор, то при установке в одно и то же приспособление последовательно обрабатываемые заготовки могут занимать относительно пальца различное положение.
Смещение установочной базы детали относительно установочной базы приспособления приводит и к смещению поверхности, подлежащей обработке, относительно режущего инструмента, настроенного на заданный размер.
Смещение заготовки от поминального положения влево (рис. 34, б) приводит к увеличению глубины резания и снижению стойкости режущего инструмента, поэтому оно может не учитываться при назначении припуска на обработку.
Смещение заготовки вправо от номинального положения (pис. 34, а) вызывает отход подлежащей обработке поверхности от режущих кромок инструмента. Величина этого смещения (погрешность базирования) должна быть учтена в качестве отдельной составляющей операционного припуска Следовательно, даже при отсутствии каких-либо других погрешностей необходимо на обработку торца назначить припуск
Максимальное смещение установочной базы детали относительно установочной базы приспособления может быть определена из выражения
или
где Smax – максимальная величина зазора между отверстием детали и установочным пальцем приспособлением.
Погрешность закрепления возникает в результате смещения обрабатываемой поверхности заготовки относительно настроенного инструмента под действием зажимного усилия.
Она возникает по двум основным причинам:
1. В результате деформации контактирующих поверхностей заготовки и приспособления –
2. Из-за отрыва заготовки от установочных элементов приспособления –
Рассмотрим первый случай. Пусть необходимо фрезеровать плоскую поверхность заготовки (рис. 35) фрезой, настроенной на размер Hconst относительно установочных элементов приспособления. Под воздействием зажимного усилия Q заготовка на твёрдых установочных элементах будет деформирована на величину Y. При этом деформация под воздействием минимального усилия будет равна Y , а максимального – Y
. В результате размер заготовки в первом случае будет
, а во втором –
.
Рис. 35. Погрешность закрепления, возникающая в результате деформации контактирующих поверхностей заготовки
Различие деформации Y вызывает колебания глубины резания, которое надо учесть при расчёте припуска. Оно и будет равно рассматриваемой составляющей припуска, т. е.
Погрешность закрепления , возникающая в результате отрыва заготовки от установочных элементов приспособления возникает, прежде всего, в результате избыточных связей, наложенных на заготовку. Неопределённость базирования возникает в результате ошибок технолога. На неё иногда идут сознательно вследствие специфики схемы закрепления заготовки.
Результирующую величину погрешности закрепления рассчитывают по формуле
Для типовых установок обычно используют опытно-статистические данные о величинах в зависимости от типа зажимного приспособления, размеров заготовки и характера поверхностей, воспринимающих зажимное усилие.
Расчёт погрешности положения установочных элементов приспособления рассмотрим на примере (рис. 36). Пусть осуществляется фрезерование заготовок в многоместном приспособлении инструментом, настроенном на размер Нconst. Высота установочных элементов приспособления П различна и колеблется в пределах поля допуска. Следовательно, заготовки относительно установочных элементов будут иметь различный вылет, что и необходимо учесть. Величина рассматриваемой составляющей припуска в данном случае будет равна
Рис. 36. Погрешность положения установочных элементов
в многоместном приспособлении
Различие в высоте приспособлений между и
в данном случае не принимаем во внимание по тем же соображениям, что в случае, когда в качестве составляющей припуска принимаем во внимание только нижнее отклонение поля допуска при расчете по “схеме вала”.
При отсутствии данных о точности приспособлений следует при обработке по 6–8 квалитетам точности принимать =0,25–0,35 поля допуска на выдерживаемый размер; при обработке с меньшей точностью –
=0,05–0,1 поля допуска.
К составляющей также относят погрешности индексации, имеющие место при обработке на станках с поворотными столами, барабанами, револьверными головками. При отсутствии паспортных данных на погрешность индексации её следует принимать равной 0,05 мм.
5.8.5.2. Суммирование составляющих операционного припуска
Влияние различных факторов на величину операционного припуска выражают следующими функциональными зависимостями:
–для одностороннего припуска
–для двустороннего припуска
.
В большинстве случаев все составляющие являются величинами случайными и достаточно независимыми друг от друга. Используя вероятностный метод расчета, применяют следующие зависимости:
–для одностороннего припуска
–для двустороннего припуска
где К – коэффициент, учитывающий отличие законов распределения составляющих припуска от нормального. Рекомендуют принимать К=1,2–1,3.
При расчётах в каждом конкретном случае необходимо решать, какие составляющие припуска следует учитывать, а какими можно пренебречь. Например, при получистовой обточке вала в центрах погрешностью закрепления 0,02 мм можно пренебречь в виду её малости по сравнению с другими составляющими припуска.
5.8.5.3. Порядок определения операционных припусков, операционных размеров и размеров заготовки
Определение операционных припусков, операционных размеров и размеров заготовки ведут в следующем порядке.
1. Выбирают конструкцию заготовки, устанавливают способ её получения и точность её размеров – в зависимости от конструкции детали, её материала, программы выпуска и возможностей предприятия.
2. Намечают технологический процесс механической обработки с учётом требований чертежа детали и существующих рекомендаций по выбору технологических баз.
3. Определяют последовательность обработки и число переходов (операций), необходимых для выполнения требований чертежа по точности и шероховатости обработанных поверхностей. Для каждого из переходов устанавливают ожидаемую точность и шероховатость. Необходимые для расчета операционных припусков и промежуточных размеров допуски на выполнение переходов определяют по нормативам.
4. Устанавливают численные значения составляющих припуска для каждого перехода (операции) обработки данной элементарной поверхности.
5. Рассчитывают величины операционных припусков на отдельные ступени обработки, начиная с черновой.
6. Устанавливают операционные размеры и размеры заготовки.
5.8.5.4. Особенности расчета припусков
Особенности расчета припусков при изготовлении
деталей из круглого проката
Расчет припусков на диаметральные размеры деталей ведут для ступени вала с наибольшим диаметром. При равных диаметрах расчет ведут для ступени, к которой предъявляют наиболее высокие требования по точности и качеству поверхности.
Напуск, имеющийся на остальных ступенях вала, если это допустимо по условиям жесткости технологической системы, срезают при черновой обработке за один рабочий ход. Больший напуск удаляют за два рабочих хода: 70–60 % за первый и 30–40 % за второй.
Металлургическая промышленность выпускает три вида проката: высокой, повышенной и обычной точности. При расчете диаметра заготовки его округляют в большую сторону до ближайшего по сортаменту диаметра прутка.
Прокат высокой точности для лезвийной обработки не используют. Его после термической обработки подвергают шлифованию.
Особенности расчета припусков при изготовлении
деталей из отливок
При расчете припусков для деталей из отливок следует учитывать, что базирование на первой операции осуществляется по необработанной поверхности. С целью гарантирования полной проливки, обеспечения большей прочности формы на заготовке, местные переходы, углубления и уступы сглаживаются. В результате глубина резания при обработке таких элементов увеличивается.
Для верхних по положению при заливке поверхностей отливок расчетные значения общих припусков Zо' или значения припусков в первую ступень обработки в целях получения заданного качества поверхности следует увеличивать на добавочные значения (На + Та)доп, которые приводятся в справочной литературе, т.е.:
Zо = Zо + (На + Та)доп.
Особенности расчета припусков при изготовлении
деталей из поковок
При расчете припусков следует учитывать, что у поковок назначают технологические напуски для крепления заготовок при термической обработке, а также напуски, упрощающие конфигурацию, переходы и уступы. Радиусы закруглений рассчитывают из соотношения
R3 = Rд + Zо,
где Rд – соответствующий радиус детали.
Базирование поковок по необработанной поверхности целесообразно лишь на первой операции.
Численность значения допусков на высоту (толщину), длину и ширину штампованных заготовок из стали устанавливают в зависимости от массы, габаритных размеров и требуемой точности. Положения, которыми при этом руководствуются, рассмотрим на примере рис. 37.
Рис. 37. Эскиз заготовки поковки
1. Недоштамповка и двусторонний износ штампов обуславливают колебания размеров А. Допуски на эти размеры определяются в зависимости от массы заготовки с прибавлением допусков на температурный интервал штамповки в зависимости от габаритных размеров заготовки.
2. Односторонний износ штампа обуславливает колебание размеров Б. Допуски на эти размеры определяются половинными значениями допусков, рассмотренных в пункте 1.
3. Допуски на размеры В между осями бобышек или других схожих элементов, а также на размеры Г, определяются как независящие от износа штампов, с прибавлением допусков на температурный интервал штамповки.
4. Для внутренних размеров штампованных заготовок следует применять тот же метод расчета, но устанавливать допуски с обратными знаками.
Установленные размеры обрабатываемых поверхностей должны округляться в сторону увеличения припусков:
¾ в поковках первой группы точности – до 0,1 мм;
¾ в поковках второй группы точности – до 0,5 мм;
¾ в поковках третьей группы точности – до 1,0 мм.
5.8.6. Примеры расчета припусков
1. Произвести расчет припусков на механическую обработку торцов вала (рис. 38) и его шейки Æ60h7 расчетно-аналитическим методом. Рассчитать промежуточные размеры для выполнения каждой операции и размеры заготовки.
2. Назначить опытно-статистическим методом промежуточные размеры на обработку отверстия Æ20 H8.
Рис. 38. Вал
Заготовку получают горячей штамповкой на молотах второй группы точности. Масса заготовки 18 кг. Материал заготовки – Сталь 45 ГОСТ 1050–88.
При расчете припусков на обработку торцов и шейки вала будем пользоваться методикой, изложенной в книге И.А. Коганова, А.А. Станкеева. "Расчет припусков на механическую обработку" [27].
Обработку торцов с точностью по 12 квалитету и шероховатостью Rz80, а также зацентровку для последующей обработки вала в центрах можно производить на фрезерно-центровальном полуавтомате с использованием торцовых фрез (табл. 4, с. 90).
Рассмотрим расчет припуска на обработку торцов. Заготовка базируется согласно схеме на рис. 39 с установкой по внешней поверхности в самоцентрирующие призмы с упором в левый торец.
Рис. 39. Заготовка вала, полученная горячей штамповкой
Односторонний припуск определяем по формуле
.
Принимаем К = 1,2.
Рассчитаем припуск на обработку левого торца.
1. Составляющая припуска, характеризующая отклонение обрабатываемой поверхности относительно базирующей равна нулю, так как левый торец является базой заготовки, т.е.
Dа = 0.
2. Из табл. 49, с. 132 [27] находим высоту микронеровностей и глубину дефектного слоя штампованной поковки массой 18 кг (от 2,5 до 251 кг):
На = 150 мкм, Та = 250 мкм.
3. Находим составляющую, характеризующую пространственные отклонения поверхностей заготовки, не связанные с допуском. Для штампованной на молотах заготовки величина смещения по линии разъема (табл. 42, графа 4, с. 124) для заготовки массой 18 кг:
rа = 1400 мкм.
4. Составляющие погрешности установки:
- погрешность базирования ed = 0 – табл. 80, пункт 5, с.156;
- погрешность закрепления e3 = 0, поскольку зажимное усилие направлено перпендикулярно возможному направлению отхода заготовки от базирующей поверхности приспособления;
- погрешность положения установочных элементов приспособления рассматривать здесь и далее не будем, поскольку обработка ведется в одноместных приспособлениях.
Таким образом
eв = 0.
Припуск на обработку левого торца
мкм.
Рассчитаем припуск на обработку правого торца.
1. Величина Dа будет равна нижнему отклонению поля допуска на длину заготовки. Для массы заготовки 18 кг из табл. 42, с. 124 имеем отклонения на недоштамповку или износ штампов мм. С учетом отклонений ±1,0 мм на температурный интервал штамповки для длины заготовки 480 мм (графа 10 табл. 42]) имеем суммарный допуск
мм. Тогда
Dа = 2100 мкм.
2. Величины
На = 150 мкм, Та = 250 мкм – табл. 49, с. 132.
3. Величину rа для правого торца (рис. 40) принимаем равной нулю по тем же соображениям, что и в случае, когда в качестве Dа принимают нижнее отклонение поля допуска на длину заготовки. Таким образом,
rа = 0.
Рис. 40. Составляющая припуска rа , зависящая от погрешности,
образуемой смещением матриц по плоскости разъема штампа
4. Погрешность установки по изложенным причинам
eв = 0.
Припуск на обработку правого торца
мкм.
Операционных припуск
мм.
Длина заготовки
мм.
Рассчитаем припуски на обработку шейки вала.
Исходя из возможности различных способов обработки, их точности и шероховатости обработанной поверхности, которую они обеспечивают (табл. 4, с. 90 [23]), а также типовых технологических процессов, обработать рассматриваемую шейку вала можно путем последовательных операции или переходов:
- получистовое точение (h12, Rz40);
- чистовое точение (h10, Rz20);
- получистовое шлифование (h9, Rz10);
- чистовое шлифование (h7, Rz0,63).
Обработку на всех переходах осуществляют в центрах с приводом от хомутика с поводком.
Двусторонний припуск рассчитывают по формуле
.
Дата добавления: 2018-10-27; просмотров: 802; Мы поможем в написании вашей работы! |
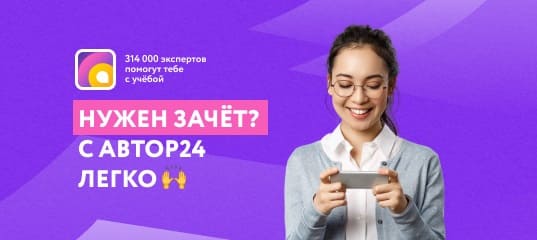
Мы поможем в написании ваших работ!