Выбор объекта моделирования и постановка задачи
В качестве объекта исследования в данном дипломном проекте выбрана камера сгорания газовой турбины промышленного типа, на примере агрегата фирмы "Siemens" модели V64.3A [20]. Данная ГТУ относится к классу средних по мощности промышленных турбин с непрерывной кольцевой камерой сгорания.
Камеры сгорания в ГТУ играют главенствующую роль. Остановимся подробнее на её основных функциях и конструктивных особенностях.
В камере сгорания ГТУ осуществляется нагрев рабочего тела до заданной температуры за счет сжигания топлива в потоке сжатого воздуха [5].
К камерам сгорания предъявляются следующие требования:
в них должно происходить устойчивое горение топлива на всех режимах работы ГТУ, без срывов, опасных пульсаций и затухания пламени;
поле температур в газовом потока перед турбиной должно быть достаточно равномерным во избежание местных перегревов и повреждений сопел и лопаток;
для увеличения срока службы они должны иметь надежное охлаждение, особенно наиболее нагретых частей;
высокая экономичность на всех режимах работы ГТУ;
возможно меньшее гидравлическое сопротивление;
надежный запуск;
по конструкции они должны быть удобными и безопасными в эксплуатации, технологичными в недорогими в изготовлении;
камеры сгорания ГТУ передвижных и транспортабельных электростанций, кроме того, должны иметь еще возможно меньшую массу и габариты.
|
|
Камеры сгорания современных ГТУ работают на газообразном топливе (в основном это природные газы) и на различных сортах жидкого топлива: газойле, керосине, дизельном топливе, солярном масле, дистилляте. Проблема сжигания в камерах сгорания твердого топлива пока не решена, но в этом направлении ведутся исследовательские работы.
Интересно хотя бы вкратце проанализировать соображения, которыми обычно руководствуются при выборе конфигурации и основных размеров традиционных камер сгорания. Такого рода данные позволяют понять, как определяются конструктивные основные характеристики, обеспечивающие работу камеры сгорания.
На рисунке 1.2 (а) показана схема простейшей камеры сгорания - прямой цилиндрический канал, соединяющий компрессор с турбиной. К сожалению, такое простое устройство непригодно из-за недопустимо больших потерь давления.
Рисунок 1.2 - Стадии развития схемы традиционной камеры сгорания газотурбинного двигателя
Потери давления пропорциональны квадрату скорости воздушного потока. Поскольку скорость воздуха на выходе из компрессора близка к 150 (м/с), потери давления при этом могут достигать четвертой части общего повышения давления в компрессоре. Для снижения потерь давления до приемлемого уровня используют, как показано на рисунке 1.2 (б) диффузор, с помощью которого скорость воздуха уменьшают приблизительно в 5 раз.
|
|
Однако этого недостаточно, так как для предотвращения срыва пламени и поддержания устойчивого процесса горения необходимо с помощью обратных токов создать зону малых скоростей. На рисунке 1.2 (в) показано, как этого можно достичь посредством простой пластины. Такое устройство имеет, однако, один недостаток, который заключается в том, что необходимое для получения заданной величины повышения температуры отношение топливо-воздух существенно превышает предел воспламеняемости смесей углеводородов с воздухом. В идеальном случае коэффициент избытка воздуха a близок к 1,25, хотя, например, при желании снизить выбросы окислов азота, эта величина может быть увеличена до 1,6. Указанный недостаток может быть устранен, если простой стабилизатор заменить, как показано на рисунке 1.2 (г), перфорированной жаровой трубой. В жаровой трубе создается зона малых скоростей, в которой процесс горения поддерживается циркуляционным потоком продуктов сгорания, непрерывно поджигающим поступающую в камеру свежую топливовоздушную смесь. Избыточная (ненужная для горения) часть воздуха вводится в жаровую трубу за зоной горения, где она перемешивается с горячими продуктами сгорания, понижая, таким образом, их температуру до приемлемого для турбины уровня.
|
|
Существующие камеры сгорания можно разделить на следующие основные типы:
а) индивидуальные;
б) секционные (многотрубчатые);
в) кольцевые;
г) трубчато-кольцевые.
Кроме того, камеры сгорания делятся на прямоточные и противоточные. В прямоточных камерах охлаждающий (вторичный) воздух движется в кольцевом канале между пламенной трубой и корпусом в том же направлении, что и продукты сгорания. В противоточных камерах поток охлаждающего воздуха направлен навстречу потоку продуктов сгорания в пламенной трубе. Применение противоточных камер в ряде случаев упрощает общую компоновку ГТУ и позволяет сократить длину камеры, но потери давления в них обычно больше, чем в прямоточных камерах.
Индивидуальные камеры, в свою очередь, бывают выносными и встроенными. Выносная камера в отдельно скомпонованном корпусе устанавливается в ГТУ рядом с турбокомпрессором. Применяют эти камеры в основном в стационарных и значительно реже в передвижных установках. У встроенных камер корпус опирается непосредственно на общий корпус турбокомпрессора или конструктивно с ним совмещён.
|
|
Существуют две разновидности индивидуальных камер сгорания: цилиндрические и угловые. В цилиндрической камере сгорания, изображенной на рисунке 1.3, воздух разделяется на два потока: первичный и вторичный. Первичный воздух поступает через воздухо-направляющее устройство 1 в пламенную трубу 4, куда через форсунку 2 (или горелку) подается топливо. Расход первичного воздуха регулируется в зависимости от расхода топлива поворотом лопаток воздухо-направляющего устройства 1, что осуществляется посредством специальных рычагов управления. Вторичный (охлаждающий) воздух пропускается через кольцевое пространство между пламенной трубой 4 и корпусом 3 камеры сгорания. При движении он интенсивно охлаждает стенки трубы и корпуса. Выходя из кольцевого пространства, вторичный воздух попадает в объем А, где он смешивается с продуктами сгорания, понижая тем самым их температуру до заданного значения.
Рисунок 1.3 - Схема цилиндрической камеры сгорания
Для уменьшения закрутки газового потока на выходе из камеры и для лучшего перемешивания вторичного воздуха с продуктами сгорания к пламенной трубе приварены лопатки 5, закручивающие поток вторичного воздуха в направлении, обратном тому, которое придается первичному воздуху.
В цилиндрических камерах можно установить не одну, а несколько форсунок, что увеличивает надёжность работы и позволяет регулировать тепловую мощность камеры сгорания изменением числа работающих форсунок. Объемная теплонапряженность этих камер составляет 20000-30000 кВт/м3 при давлении 0,4-0,45 МПа, а тепловая мощность камеры сгорания достигает 3000 кДж/ч, расход воздуха - 2,5·105 м3/ч,
К преимуществам индивидуальных цилиндрических камер сгорания относятся простота конструкции и сравнительно малые потери давления, достигающие 1,5-3,0 %. Основными недостатками этих камер являются большие масса и габариты.
Секционные (многотрубчатые) камеры сгорания представляют собой конструкцию, в которой объединено несколько (6-16) параллельно работающих цилиндрических камер (секций), часто связанных между собой пламяпередающими патрубками.
Секция многотрубчатой камеры сгорания, в соответствии с рисунком 1.4, состоит из пламенной трубы и кожуха 8. Пламенная труба включает в себя головку, состоящую из лопаточного завихрителя 3, тарелки 2 и конуса 4, и корпус, состоящий из цилиндрической части 5 и двух конических участков, соединенных между собой конусным кольцом 6.
Первичный воздух поступает через входной кожух 1 в головку пламенной трубы. Часть его направляется в зону горения через лопаточный завихритель 3, а оставшаяся часть идет туда через многочисленные отверстия в тарелке 2 и конусе 4. Кроме того, на цилиндрической части пламенной трубы 5 имеется еще два ряда отверстий, через которые дополнительно поступает воздух, необходимый для горения при полной нагрузке ГТУ. Вторичный воздух идет по кольцевому пространству между пламенной трубой и кожухом 8 и затем поступает в зону смешения через четыре ряда отверстий в конической части пламенной трубы 7. Наибольшая часть охлаждаемого воздуха входит внутрь пламенной трубы через большое число отверстий малого диаметра в конусном кольце 6.
Рисунок 1.4 - Секция многотрубчатой камеры сгорания
Секционные камеры сгорания выполняют обычно в виде единого моноблока, в котором все секции заключены в общий корпус. Каждая секция имеет одну форсунку, впрыскивающую топливо по направлению потока. Секционные камеры сгорания отличаются компактностью, обеспечивают высокую полноту сгорания топлива и устойчиво работают в различных эксплуатационных условиях. Недостатком их является сравнительно большие потери давления (2,5-7,5%). Тепловая мощность отдельной секции составляет в среднем (0,7-1,7) ·103 кВт, а иногда достигает 3,5·103 кВт. Объемная теплонапряженность у камер этого типа высокая - (100-160) ·103 кВт/м3.
В кольцевых камерах сгорания, в соответствии с рисунком 1.5, зона горения I имеет форму кольцевой полости обычно шириной 150-200 м, которая образуется цилиндрами 1 и 2. Два других соосно-расположенных цилиндра (9 и 8) составляют кожух камеры. Первичный воздух через воздухопроводящее устройство 4 поступает в зону горения I. Вторичный воздух направляется по кольцевым зазорам 6 и 7 к смесительным насадкам 5, через которые поступает в зону II, где смешивается с продуктами сгорания, понижая тем самым их температуру. В воздухоподводящем устройстве 4, на входе в зону горения I по всей окружности расположены форсунки 3. За счет этого обеспечивается хорошее перемешивание топлива с воздухом и горение по всему кольцевому пространству. Число форсунок может достигать 10-20, но иногда это бывает одна вращающаяся форсунка.
Рисунок 1.5 - Схема кольцевой камеры сгорания
Объемная теплонапряженность у кольцевых камер примерно такая же, как и у секционных, но потери давления несколько больше (до 10 %). По сравнению с секционными камерами они имеют меньший рабочий объем и более равномерное поле температур газа на выходе. Зато кольцевые камеры сложнее в изготовлении и доводке, труднодоступны для осмотра в ходе эксплуатации.
Трубчато-кольцевая камера сгорания представляет собой конструктивное совмещение элементов секционной и кольцевой камер. Так же, как и у кольцевой камеры, кожух её образуется наружным и внутренним соосно-расположенными цилиндрами. А в кольцевом пространстве между этими цилиндрами размещается ряд отдельных пламенных труб, снабженных форсунками. Трубы соединяются друг с другом пламяпередающими патрубками, которые предназначены для передачи пламени, зажигания и выравнивания давления между трубами. Трубчато-кольцевые камеры имеют теплонапряженность и потери давления приблизительно такие же, как секционные камеры. Они компактнее кольцевых камер и более просты в доводке. Небольшие размеры пламенных труб упрощают их изготовление и разборку.
Для работы на жидком топливе в камерах сгорания обычно применяют центробежные форсунки, изображенные на рисунке 1.6. Они просты по конструкции, надежны в работе и обеспечивают хорошее распыливание топлива. К форсунке топливо подаётся насосом 5 под давлением не менее 1,0-1,5 МПа. Поступает оно сначала в кольцевую полость 1, а затем через ряд тангенциально расположенных каналов 2 направляется в вихревую камеру 3, в которой приобретает вращательно-поступательное движение. При выходе из форсунки топливо распыляется под действием центробежных сил.
В центробежных форсунках регулировать расход топлива за счет изменения его давления можно не более чем в 2-2,5 раза. Для обеспечения более широкого диапазона регулирования применяют двухступенчатые форсунки и форсунки с перепуском топлива. У двухступенчатых (двухконтурных) форсунок на малых расходах работает лишь одна первая ступень. Для увеличения расхода топлива к ней подключается вторая ступень. У форсунок с перепуском топлива вихревая камера 3 соединена с регулируемым клапаном 4, который перепускает часть топлива обратно в подводящий трубопровод или же в расходный бак 6.
Рисунок 1.6 - Центробежная форсунка с перепуском топлива
Из представленного обзора можно сделать вывод, что кольцевые камеры сгорания, рассматриваемые в данном проекте, являются компактными и технологичными, но в то же время сложными в изготовлении и доводке. Под технологичностью в данном случае понимается равномерность потока, которая приводит к большей экологичности турбины и тепловой устойчивости камеры.
Сложность в изготовлении и доводке диктует применение новых технологий при проектировании агрегата. От классического пути необходимо переходить к программным средствам и методологиям, создавать виртуальные модели конструкций, которые позволяют провести практически любой вид анализа без каких либо технических затруднений и затрат. За рубежом, программные средства такого рода весьма распространены и используются в основном фирмами, которые привыкли отвечать за качество своей продукции и могут гарантировать его.
На сегодняшний день время подготовки производства и себестоимость продукции пристально изучаются с целью их сокращения для поддержания конкурентоспособности изделий и лидерства предприятий на рынке, поскольку требования, предъявляемые к предприятиям, постоянно возрастают. Наиболее короткий цикл подготовки производства в сочетании с низкими производственными затратами может быть реализован путем сокращения традиционных методов моделирования и испытаний. С внедрением методов компьютерного моделирования и анализа исключается необходимость повторного создания опытных образцов и проведения их испытаний вследствие корректировки конструкции по результатам предыдущих испытаний, так как корректировка конструкции осуществляется после компьютерного анализа, а испытание опытных образцов носит верификационный характер, как показано на рисунке 1.7 [15].
Рисунок 1.7 - Жизненные циклы изделий, основанные на традиционных методах моделирования и компьютерном анализе
Для камер сгорания основными исследуемыми параметрами являются:
а) геометрия камеры сгорания (акустический анализ);
б) тепловой поток (термодинамический анализ);
в) режимы работы горелочного устройства (сопряженный анализ).
В данном дипломном проекте предложена методика, позволяющая производить конечно-элементный расчет по всем перечисленным пунктам. Такого рода виртуальные эксперименты и расчеты существенно облегчают проектирование камер сгорания и приносят неоспоримый экономический эффект.
Существуют и аналитические методы, позволяющие провести расчет камер сгорания, в том числе физико-химические и математические, учитывающие реагирующие потоки и турбулентность. Но затраты при таком подходе могут быть значительно ниже, если он гармонично сочетается с виртуальными расчетами.
Дата добавления: 2018-09-22; просмотров: 249; Мы поможем в написании вашей работы! |
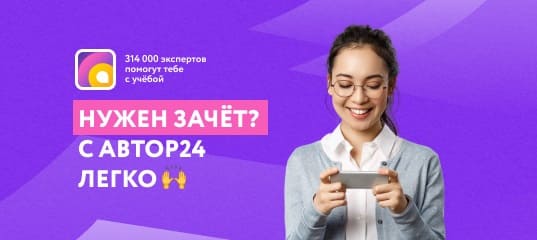
Мы поможем в написании ваших работ!