Типы основных файлов, создаваемых программой
В процессе моделирования программа ANSYS может создавать следующие типы файлов [10]:
а) . log - протокольный (журнальный) файл, хранящий историю работы в виде ANSYS-команд, т.е. полная запись программы (текстовый файл) на всех этапах решения задачи (препроцессор, решение, постпроцессор);
б) .inpили .dаt - файл ввода программы при пакетном (batch) режиме работы;
в) .db или .dbb - база данных программы (бинарный, в кодировке ANSYS),сохраняет геометрию модели, граничные условия, решение;
г) .emat - файл матрицы элементов;
д) .grph - файл графики;
е) .err - файл ошибок, содержит все ошибки и предупреждения, выданные программой впроцессе решения;
ж) .mac - файл с макрокомандами;
з) .nod - файл с узлами сетки;
и) .elm - файл с элементами сетки;
к) .rst - бинарный файл, содержащий результаты прочностного анализа;
л) .rth - бинарный файл, содержащий результаты теплового анализа;
м) .rmg - бинарный файл, содержащий результаты электромагнитного анализа;
н) .rfl - бинарный файл, содержащий результаты гидродинамического анализа;
о) .SI_MPL - файл - библиотека, в котором хранятся заданные пользователем свойства материала.
Проектирование модели исследуемого объекта
В данном проекте, основной задачей моделирование является газодинамический расчет различных режимов работы камеры сгорания. Расчет производился в модуле Multiphysics, обладающем более полными возможностями моделирования процессов термодинамики газов и жидкостей с возможностью решения сопряженных задач. В качестве решателя использовался FLOTRAN.
|
|
Программа FLOTRAN и модуль FLOTRAN CFD (расчетная гидрогазодинамика) программы ANSYS предлагают всесторонние инструментальные средства для анализа двумерных и трехмерных полей потока жидкости или газа.
Численный анализ требует некоторой идеализации модели, что в конечном итоге приводит к погрешностям расчетов. Эти погрешности тем ниже, чем более правильно и подробно создана модель - если при моделировании учтено максимальное число известных фактов о поведении исследуемой конструкции под нагрузкой. Использование вычислительной техники в роли черного ящика, без понимания основных процессов и этапов вычислений может привести к значительным ошибкам. Приступая к исследованиям, инженер должен понять, к какой области анализа относится данная задача, какая часть всей конструкции должна исследоваться подробно, какие упрощения можно допустить.
При проектировании модели камеры сгорания в ANSYS, задачу можно разделить на следующие этапы:
проектирование графической модели объекта;
выбор вида конечно-элементной сетки и её наложение на графическую модель;
определение граничных условий и нагрузок;
|
|
определение вида и параметров решения;
проведение решения и вывод результатов;
анализ полученных результатов решения.
Ниже приведено детальное описание всех этапов создания и решения конечно-элементной модели.
Построение графической модели
Графическая модель камеры сгорания была разработана в прикладном графическом пакете SolidWorks 2004. Она представляет собой двумерную конструкцию линий, являющихся границами плоскостей радиального сечения форсунки горелочного устройства и рабочей области камеры сгорания. Для того чтобы иметь возможность применять модель в пакете ANSYS, она была сохранена в форме IGES - объекта.
После импортирования файла модели она будет выглядеть, как показано на рисунке 3.1 Необходимо доработать графическую модель средствами пакета. Применение графических возможностей препроцессора ANSYS делает построенную модель более "дружелюбной" к другим компонентам инженерного пакета, в том числе, исключает возможные проблемы при импортировании плоскостей из других графических процессоров (SolidWorks, 3D Max Studio, AutoCAD и других).
Доработка включает в себя:
масштабирование импортированных линий, для соответствия реальных размеров камеры сгорания, размерам графической модели, выраженных в единицах СИ;
|
|
создание плоскостей, необходимых для последующего нанесения конечно-элементной сетки;
сжатие номеров графических элементов, для устранения возможных ошибок при перечислениях или обращениях к ним в дальнейшем.
Создаются две плоскости, в соответствии с рисунком 3.2: одна из них статическая, не участвует в анализе, представляет собой разрез форсунки горелочного устройства; другая - рабочая плоскость, радиальный разрез внутренней полости кольцевой камеры сгорания. Именно на рабочую область будет в последующем наложена конечно-элементная сетка.
Рисунок 3.1 - Импортированная SolidWorks в ANSYS графическая модель камеры сгорания
Рисунок 3.2 - Плоскости, созданные средствами препроцессора ANSYS
Сама по себе, рабочая плоскость является нерегулярной, с точки зрения геометрии, что является решающим критерием при выборе формы расчетных элементов.
Дата добавления: 2018-09-22; просмотров: 212; Мы поможем в написании вашей работы! |
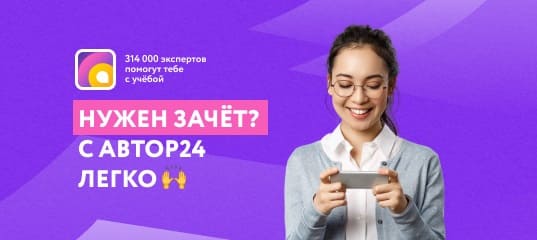
Мы поможем в написании ваших работ!