Цифровой сервопривод Hitec RCD HS-7954SH.HV
Рисунок 3.7 - Цифровой сервопривод Hitec RCD HS-7954SH.HV
Мощный цифровой сервопривод для использования в авиамоделях большого масштаба, больших вертолетах, автомоделей масштаба 1/8. Сервопривод может быть безопасно использован при напряжении до 12 В. В сервоприводе используется бесколлекторный двигатель. Основные параметры сервопривода могут быть запрограммированы с помощью программатора [13].
Это ультрамощное серво, рассчитанное на высокое напряжение. Оно может быть запрограммировано с помощью программаторов HFP-20, HPP-21 либо HPP-21+. Особенности: идеально для авиамоделей гигантского масштаба, больших вертолётов, краулеров, монстр-траков, траков масштаба 1/8микроконтроллер схема двигательМотор без сердечника для чёткого центрирования микроконтроллер схема двигательПрограммируемая цифровая цепь G2, включены следующие программируемые свойства: ширина мёртвой зоны, регулировка скорости, микроконтроллер схема двигательпозиция Fail Safe, Вкл/Выкл Fail Safe, направление (по ЧС/против ЧС), конечные точки.
Защита от перегрузки, разрешение большое/малое, стальные шестерни для увеличения срока службы по сравнению с серво с металлическими шестернями, девять О - образных прокладок для экстра - защиты от влаги и пыли. Характеристики: Габариты: 40 х 20 х 37мм (стандарт), Вес: 68 грамм Скорость поворота на 60° при 12В составляет 0,12сек, Усилие на валу 29.0кг/см, шарикоподшипник: двойной.
|
|
4. Структурная схема адаптивной системы управления выпускным трактом двухтактного двигателя
Рисунок 4.1 - Структурная схема адаптивной системы изменения геометрии выхлопного тракта двухтактных двигателей
Подача питания на микроконтроллер происходит в момент включения зажигания. Далее система переходит в режим диагностики, в котором проверяются датчики и исполнительные механизмы, такие как датчик оборотов коленчатого вала, датчик положения ГДН, датчик температуры выхлопных газов, датчик силы тока.
В зависимости от оборотов двигателя происходит смещение конуса ГДН, что позволяет повысить эффективность и экономичность двигателя во всем диапазоне его работы.
Датчик положения ГДН предназначен для проверки соответствия концевых точек системы сдвижки, для предотвращения его некорректной работы в случае повреждения механизма сдвижки.
Датчик температуры выхлопных газов предназначен для контроля качества горения топливовоздушной смеси для дальнейшей корректировки положения конуса ГДН с целью улучшения экономических и экологических показателей, а также с целью перевода системы в доездной режим в случае обнаружения неисправностей в работе ДВС, которые могут повлечь за собой разрушения ДВС.
|
|
Датчик силы тока служит для предотвращения неисправностей механизма сдвижки и сервопривода, в случае возникновения усилия необходимого для сдвижки конуса превышающего установленное.
Управление сервоприводом происходит с помощью микроконтроллера с целью изменения геометрии выхлопного тракта путем смещения запорного конуса.
Разъем программирования и диагностики служит для настройки системы под конкретный тип ДВС, обновления прошивок, а также с целью проведения диагностических работ.
5. Алгоритм работы адаптивной системы управления выпускным трактом двухтактного двигателя
При включении зажигания адаптивная система изменения выхлопного тракта переходит в режим диагностики, отображенный на рисунке 5.2, при успешном завершении которого переходит в рабочий режим, который функционирует согласно алгоритму указанному на рисунке 5.1,а в случае некорректной работы системы выводит информацию на приборную панель, запуск двигателя и переход в доездной режим, после чего следует проверка номинальным параметрам считанным с датчиков. В случае если ошибка не исчезла система остается в доездном режиме. В случае исчезновения ошибки система переходит в рабочий режим, в котором после прохождения диагностики происходит запуск двигателя. Далее начинается циклическая часть алгоритма в начале которой происходит считывание показаний датчика частоты вращения коленчатого вала, опираясь на которые происходит позиционирование ГДН, после чего снимаются показания с датчика температуры выхлопа, которые в дальнейшем проверяются на соответствие номинальным параметрам. При их соответствии система продолжает работать циклически до выключения зажигания[16].
|
|
В случае несущественного отклонения показателей происходит смещение ГДН в пределах 10% от общего хода системы сдвижки. В случае превышения температурных показателей свыше 700 градусов цельсия информация об ошибке выводится на приборную панель и система переходит в доездной режим во время работы которого периодически осуществляется анализ показаний датчика температуры выхлопа.
Рисунок 5.1 - Алгоритм работы адаптивной системы управления выпускным трактом двухтактного двигателя
5.1 Алгоритм диагностики адаптивной системы управления выпускным трактом двухтактного двигателя
В режиме диагностики показанном на рисунке 5.2 считываются показания со всех датчиков системы и сравниваются с их номинальными параметрами, если параметры хотя бы одного из датчиков отличаются от должных, то микроконтроллер записывает в память ошибку, зажигает индикатор на приборной панели и переходит в доездной режим. Если показания датчиков совпадают с номинальными, то далее подается питание на сервопривод для проверки соответствия концевых точек после чего происходит запуск двигателя и показания датчиков проверяются еще раз. Если показания не выходят за рамки номинальных параметров, то система осуществляет смещение ГДН в соответствии с режимом работы двигателя и переходит в рабочий режим. В ином случае система отключается до устранения неисправности.
|
|
Рисунок 5.2 – алгоритм диагностики адаптивной системы управления выпускным трактом двухтактного двигателя
6. Принципиальная схема адаптивной системы управления выпускным трактом двухтактного двигателя
Рисунок 6.1 - Принципиальная схема адаптивной системы управления выпускным трактом двухтактного двигателя
В принципиальной схеме адаптивной системы управления выпускным трактом двухтактного двигателя, построенной на плате Arduino, на базе микроконтроллера ATmega 1280 используются:
- Фильтры в виде керамического и электролитического конденсаторов, подключенные на входы VCC и GND;
- D1, D2 и D3 –стандартные датчики частоты вращения коленчатого вала, положения ГДН (датчик Хола) и температуры выпускных газов не требующие специального подключения к МК, которые подключены к выводам PF1 (ADC1), PF3 (ADC3) и PF0 (ADC0);
- Также отображено подключение питания МК к входу RESET, который подсоединяется через резистор и конденсатор для запуска контроллера с задержкой для надежного запуска.
- К входу PF2 (ADC2) подключен датчик силы тока, работающий по принципу преобразования тока в напряжение, что позволяет сделать измеритель с практически нулевым падением напряжения.
- На выходы PJ7 и PJ6 подключены два светодиода с включенными в разрыв резисторами.
- Цифровой сервопривод подключен к выходу PB7 генерирующему ШИМ сигнал.
- Также в системе предусмотрен понижающий преобразователь напряжения из 12 В в 5 В для обеспечения корректной работы управляющей платы.
- D4 Преобразователь Arduino
7. Исследования и тесты
7.1 Общие сведения
Универсальная система работающая при помощи сервоприводов позволяла быстро переналаживать геометрию трубы для каждого двигателя и во время эксперимента плавно менять длину трубы без изменения объема или объем без изменения длины, или оба параметра одновременно при этом контролируя величины. По шесть резонансных труб для каждого типа двигателя. Это дало возможность «конструировать» множество геометрий для каждого двигателя и при этом плавно менять соотношения некоторых параметров труб. За основу была взята геометрия трубы Вишневского применительно к каждому двигателю и модификации в большую и в меньшую сторону геометрических параметров. Штатные трубы к итальянским двигателям CMB X15 и A90 имели несколько другие соотношения, но за основу была выбрана труба Власова, так как с его трубой и CMB X15 и A90 работали заметно лучше.
Трубы испытывались последовательно по одной и той же методике:
Достижение максимальной мощности.
Максимальный крутящий момент с трубой при скорости вращения вала соответствующего оптимальным оборотам двигателя без трубы.
Расход топлива с трубой при мощности на валу соответствующей максимальной мощности двигателя без трубы.
Повышение мощности стандартных двигателей путем постепенной модернизации:
а) изменения объемов камеры сгорания;
б) изменение геометрии футерки карбюратора;
в) изменение высоты выхлопных каналов;
г) изменение высоты перепускных каналов.
Рисунок 7.1 - Резонансная труба (ГДН)
На рисунке входное отверстие трубы равно выпускному. Это сделано для изучения влияния диаметра и длины выпускного патрубка. В выпускное отверстие вставлялись насадки с различными отверстиями по диаметру и профилю (с конусами, кривыми Лаваля, блендами и так далие) [6].
В дальнейшем успешно эксплуатировался двигатель с такой же, но изготовленной из нержавеющей стали, а не алюминиевой трубой на судомодели класса FSR-V15. Труба была настолько хороша, что двигатели (2 штуки) больше одной получасовой гонки не выдерживали. Приходилось менять шатуны и коренные подшипники. Поломались два вала. Это еще раз доказывает то, что высокофорсированный двигатель с трубой должен проектироваться как единное целое с учетом всех особенностей.
При первых опытах была собрана система с механизмом пантографа, но потом от этого отказались из-за сложности переналадки. Простые рычажные механизмы работают корректно при достаточном удалении управляющего рычага, т.е. когда длины шатунов плеч и одного порядка.
Система работоспособна и при более коротком выпускном канале, но тогда резко реагирует на изменения температуры и эжекции (изменении скорости спутной струи) и нагрузки. Увеличение длины канала никаких отрицательных последствий не вызывало, более того, если возникает проблема с шумом от выхлопной системы, то наиболее эффективно можно его глушить устанавливая поглотитель шума демпферного или резонансного типа на выхлопном патрубке, на удалении от зеркала поршня двигателя на расстоянии кратном ¼ длины звуковой волны конкретного спектра.
После отработки определенного количества топлива можно определить качество настройки, так как при неправильной настройке в трубе накапливается рабочая смесь (под правильностью, на режиме экономии, имеется в виду соотношение топлива с объемом камеры сгорания). При длительном накапливании происходит детонация. Данный опыт нужно проводить не более 30 секунд на больших кубатурах, а на 2,5-3,5 см3 не более 1 минуты.
По заказу было изготовлено по 3 трубы к каждому типу двигателей, все одинакового объема но разной длины +10%. На каждой из трёх труб двигатель показывал одинаковую предельную мощность, разница по оборотам и крутящему моменту в установившемся режиме не отличалась, отклонения были только: а) разное качество запуска (на укороченных-хуже, по мере удлинения-лучше); б) с одной из трех труб (расчетной длины) двигатели стабильно перезапускались без изменения регулировок. Удлиненная труба запускалась при более обогащенном топливе (игла открывалась на 15-300 затем возвращалась в прежнее положение), укороченная – на оборот на обедненном, (игла закрывалась на 10-200) [9].
При этом идентичный установившийся режим обеспечивался при индивидуальном подборе диаметра выпускного отверстия. Меньше отверстие для длинной трубы, большое для короткой.
На установившийся режим работы влияли температура трубы (и при охлаждении и при перегреве более чем на 200С) и изменение проходного сечения выпускного отверстия, не зависимо от длины. Это наблюдение привело к выводу, что в резонансной трубе происходят не только акустические процессы, но и другие, в большей мере связанные с упругими свойствами среды, а может это акустика, но для другого уровня испытаний.
После чего было принято решение переименовать «резонансный глушитель для ДВС» в «ГДН для ДВС» (газодинамический насос).
Отсутствие специальных устройств не позволило получить желаемую информацию в полном объеме. Что четко наблюдалось не зависимо от продолжительности, это упорядочение, ламинаризация потока при уменьшении сечений и хаотичность при увеличении. И очень важное наблюдение, в районе стыка конфузора с выхлопным патрубком наблюдалась наибольшая плотность (оптическая) газов, то же самое происходило и в зоне телескопического соединения диффузора с входным патрубком. Эти наблюдения привели к выводу, что начальный (входной) диаметр резонансной трубы правильнее делать по площади не более площади выхлопного окна, а при наклонном выхлопном канале в картере двигателя, можно довести до 0,75 площади выхлопа.
Такая особенность диффузора вместе с эспоненциальным распределением расширяющейся части обеспечивает однородность потока (среды выбрасываемой из двигателя рабочей смеси), и поэтому улучшает качество возвращаемой в камеру сгорания смеси и, разумеется, снижает энергетические потери движущихся масс.
Так же вызвало интерес сильное помутнение газов в районе выпускного патрубка, на настроенных ГДН (цельно стеклянный ГДН без регулировочных элементов кроме диаметра выпускного патрубка) разных двигателей.
При изменении режима двигателя (совместно с изменением диаметра выпускного патрубка) оптическое уплотнение и увеличивалось и уменьшалось, но всегда имело максимальный размер для конкретного диаметра выпуска при выдаче максимально возможной мощности с данным отверстием. Можно только предположить, что какая-либо поверхность в объеме оптического уплотнения отражает звуковую волну [5].
Общие наблюдения:
а) имеют значение длина, объем, размер выпускного отверстия ГДН;
б) внутренняя поверхность должна быть гладкой, без резких скачков размеров сечений и без шероховатостей;
в) диффузор должен обеспечивать эффективное разряжение в цилиндре двигателя, не должен завихрять истекающие газы, должен с минимальным сопротивлением и полностью возвращать остатки топливной смеси в цилиндр;
г) исходными параметрами для расчета трубы являются геометрические и динамические характеристики двигателя и система движетеля (пропеллер, колесо, гребной винт и так далие).
7.2 Инженерная часть
Конечным итогом доработки системы двигатель - ГДН является получение максимальной мощности. Во вращающихся системах известна взаимосвязь мощности с крутящим моментом и частотой вращения ВОМ (вала отбора мощности). Первый вопрос, который возникает: «Что лучше, повышение мощности за счет оборотов, повышение мощности за счет крутящего момента или и то и другое?» На первый взгляд напрашивается однозначный ответ: «Конечно, важнее всего выжать из мотора максимум!». Вопрос – на какой период времени? Есть ли гарантия стабильности запусков и так далие. Разумеется, для установления рекорда (одноразово) можно пожертвовать мотором. Весь смысл вопроса в том, чтобы правильно поставить задачу [7]. Варианты задач:
а) установление рекорда скорости авто мото транспорта– нужна мощность на предельных оборотах;
б) установление рекорда в воздухе или на воде – максимальная мощность должна «проявиться» на определенных оборотах, это связано с проблемами аэрогидродинамического характера (скачки уплотнения при околозвуковых скоростях на пропеллерах, кавитация гребных винтов, а в результате неэффективная эксплуатация ДВС);
г) продолжительные гонки на время (радиоуправляемые автомодели, судомодели класса FSR, шоссейно кольцевые гонки на мотоциклах);
д) гонки с особыми требованиями, например авиамодели класса F2-C, нужна и скорость и экономия топлива, причем рассчитанная на строго определенную дистанцию.
Формула Вишневского
L=P*a / 2f;
где P=(Фвых - h0)/360 ;h0=(Фвых- Фпер)/2; а=558800 мм/с;
f = n рез / 60 с -1;
D – приведенный внутренний диаметр входного отверстия трубы равный по площади 1,3 площади выхлопного окна двигателя; d-выпускное отверстие по площади меньше входного в 2,3-2,5 раза; a- скорость звука в среде выхлопных газов; Фвых - фаза выхлопа в градусах; Фпер - фаза перепуска в градусах; f - частота вращения вала в режиме резонанса в об/с.
Простые преобразования могут изменить вид формулы, но суть от этого не меняется. Суть формулы заключается в определении половины пути пройденной звуковой волной в среде выхлопных газов за время от начала процесса выпуска продуктов сгорания из окна цилиндра до момента перекрытия перепускных окон поршнем [10]. Почему так, единственное объяснение, эмперический подход, подгонка формулы длины результативной трубы под конкретный размер и скорость звуковой волны в продуктах сгорания. Почему именно 558,8 м/с? Вероятно это была достоверная величина из какого либо источника. Таким образом, состыковались длина трубы, скорость звука, обороты и комбинация из величин фаз перепуска и выхлопа.
Рассмотрим работу комплекса ДВС-ГДН, смотреть рисунки раздела 1.
Принцип работы резонансной трубы многим знаком.
Найдем время цикла фронта волны, для этого нужно время поворота вала двигателя на 10 умножить на эквивалент времени, то есть на Фвых.
Среднее время поворота вала на один градус: t0=[1:(nрез:60)]:360с. (3)
Где nрез:60 – частота вращения вала в 1 секунду;
1:( n рез:60) – время за которое совершается 1оборот. Таким образом, время прохождения звуковой волны от начала выхлопа до момента перекрытия выхлопного окна поршнем (обозначим как tв) будет:
tв = Фвых * [1:( n рез:60)]:360 c.
Достаточно умножить результат на скорость волны в среде выхлопных газов и поделить на 2 (весь путь до отражателя и назад) – получим искомую длину ГДН .
Теперь интересно сравнить характеристики эквивалентов времени в нашем случае и по формуле Вишневского.
Повторим формулу Вишневского и выделим в ней эквивалент времени:
L=P*a : 2f;
Где
P=(Фвых - h0):360; h0=(Фвых- Фпер):2;а=558800 мм/с;
f = nрез : 60 с -1;
Для этого необходимо исключить из формулы элементы самого времени и скорости звука.
Скорость звука: а=558800 мм/с;
Обороты в секунду: f = n рез : 60 с -1;
Время одного оборота: t = 60 :n рез с;
Время прохождения одного углового градуса: t0 = 1 : 6n рез с;
Подставим в формулу Вишневского значения его составляющих и преобразуем:
L= [(Фвых+ Фпер):4]* (1:6 nрез )*558800 (мм).
Разделим полученное выражение на компоненты времени, скорости и умножим на 2 (показатель отражения волны), находим выражение эквивалента времени по Вишневскому:
ТВиш= (Фвых+ Фпер):2; (4)
Рассмотрим вопросы, возникающие при решении подобной проблемы.
Нам нужно определить: длину ГДН, объем ГДН, геометрию ГДН.
Мы имеем:
¾ двигатель;
¾ цель эксплуатации двигателя;
¾ геометрические параметры двигателя;
¾ стендовые или паспортные характеристики двигателя;
¾ эксплуатационные требования к двигателю;
¾ состав топлива.
На основании тщательных замеров температуры внутри ГДН и окружающей среды, длины ГДН и частоты вращения в режиме резонанса с учетом индивидуальных геометрических характеристик ДВС методом от противного вывел величины скорости волны сжатия (термина «скорость звука» лучше избегать) для разных топлив. Для большей достоверности каждый двигатель вводился в резонанс с различными трубами и парами, обеспечивающими разброс оборотов до 40% при этом, естественно, менялась и температура и геометрия труб (длина и объем). Скорость волны «Св среде некоторых продуктов сгорания топливных смесей для 2-х тактных ДВС
Высота над морем 25м. Атмосферное давление 730-735 мм рт ст. Температура среды 200С. Влажность 70-80%.
Таблица 7.1 Статистические данные
Состав топлива | Минимальная температура выхлопных газов Т0К0/0С* | Скорость волны сжатия С, в м/с из экспериментов | Максимальная температура выхлопных газов Т0Кn/0С* | Скорость волны сжатия С, в м/с из экспериментов | Коэффициент р* |
МЕТАНОЛ 80%; КАСТОРКА 20% | 403 / 130 | 458,684 | 605 / 332 | 562,006 | 261,02809 |
МЕТАНОЛ 70%; КАСТОРКА 30% | 387 / 114,3 | 447,247 | 581 / 308 | 548,000 | 258,43717 |
МЕТАНОЛ65%;КАСТ20%;НИТРО15% | 453 / 180 | 480,761 | 680 / 412 | 601,003 | 255,11188 |
Б-95 95%; МК-22 5% | 552 / 279 | 470,909 | 883 / 610 | 600,000 | 200,86573 |
Б-95 90%; МК-22 5%; АЦЕТОН 5% | 546 / 273 | 462,059 | 873 / 600 | 593,000 | 195,51122 |
Низшая и высшая среднестатистические показатели температуры при экспериментах. Минимальную температуру Т0К0 можно считать базовой для дальнейших расчетов, т.к. она, практически, совпадает с температурой выхлопных газов указанных топлив для двигателей без ГДН.
Таким образом, чтобы определить скорость волны сжатия при любой температуре (в Т0К - градусах Кельвина) достаточно провести простое вычисление с «р» для конкретного топлива.
Сп = (2Т0К*р)0,5; (5)
Возникает вопрос, а при какой температуре нужно определять скорость? Помогут дополнительные данные, которые с достаточной точностью могут указать рабочую температуру для конкретного двигателя с конкретным топливом, при конкретных внешних условиях. Они должны заменить «Т0К» в формуле 5.
Сп = {2[Т0С-20+ Т0К0]*[Рат+0,001(Вот- Вот0)]*К*р)}0,5 ; м/с (6)
где Т0С-20+ Т0К0- Достоверная низшая температура продуктов сгорания в ГДН, складывается из температуры окружающей среды с вычетом температуры на момент определения Т0К0 и собственно, низшей температуры выхлопных газов в ГДН указанной в таблице.
Рат– атмосферное давление в «технических атмосферах.
1ат = 1кг/см2= 98066,5 Па = 735,561 мм ртутного столба;
0,001(Вот-Вот0)- 1/1000 часть разницы между относительной влажностью окружающей
среды с относительной влажностью на момент определения Т0К0. Может принять как положительное так и отрицательное значение.
К-теплонапряженность системы
р – индивидуальный для среды, безразмерный коэффициент (Таблица 7.1).
Установив скорость волны сжатия определим расстояние от зеркала поршня до вершины конфузора. У нас есть расчетные обороты двигателя и данные об условиях эксплуатации. Мы определили скорость поршня и коэффициент теплонапряженности. Из таблицы 3 и с помощью формулы 5 нашли «Сп».
Длина ГДНL=0,5[1:( n рез:60)]:360 *Cп*Фв (м); (7)
где 0,5 - показатель половины длины волны сжатия;
[1:( n рез:60)]:360 см. Формулу 3;
Сп-скорость волны сжатия в м/с находим по формуле 5;
Фв-фаза выхлопа ДВС в угловых градусах;
n рез-расчетная частота вращения вала мин-1.
Зная кубатуру ДВС и скорость поршня, по графику на рисунке 7 находим объем ГДН.
В формуле Вишневского фазы были, а здесь оказались не нужными. На самом деле все проще.
Особенность классического 2-х тактного ДВС в том что фазы выхлопа и перепуска симметричные относительно ВМТ и НМТ[8]. Волна сжатия смещается (при правильной настройке) тоже симметрично (от момента приоткрытия выхлопного окна до момента закрытия). Величина выхлопного окна влияет на быстроходность мотора, а перепуск на мощность. Оба окна нельзя до бесконечности увеличивать. Фаза выхлопа в первую очередь связана с эксплуатационными требованиями к ДВС, а фаза перепуска, при этом, должна быть максимальной. Но какой? Обратимся к фактам. За время выхлопа, одновременно происходят продувка цилиндра, вытеснение рабочей смеси из цилиндра и возвращение рабочей смеси из ГДН в цилиндр. Самое время вспомнить, что поршень движется не с постоянной скоростью, а от 0 м/с в НМТ до максимума по синусоиде. Мы до сих пор говорили только о средней скорости поршня, и все расчеты велись от средней скорости, что абсолютно корректно для волны сжатия и прочих процессов в ГДН. Чего нельзя сказать о процессах в двигателе. Попытка теоретического обоснования займет много места. Сошлюсь только на принцип из газовой динамики – потери давления в потоке пропорциональны квадрату скорости движения смеси, в данном случае, в перепускных окнах. Следовательно, максимальная площадь перепускных окон обеспечивает наименьшие потери, а вместе с ними и лучшее наполнение надпоршневого пространства свежей смесью. Из принципа неразрывности потока, следует, что весь объем надпоршневого пространства, с момента приоткрытия перепуска, заполнен двумя средами, замещающими одна другую. Скорость этого замещения зависит от соотношения площадей окон к объему пространства: чем больше выхлопное окно, тем быстрее по времени выходят продукты сгорания, и чем больше перепускные окна, тем быстрее и качественнее происходит замещение.
Какая минимальная (максимальная) разница должна быть между высотами выхлопа и перепуска?
Одинаковая высота исключается в виду вопиющей очевидности перерасхода топлива и максимального смешения горючей смеси с продуктами сгорания.
Зная параметры объема и длины ГДН можно нарисовать множество геометрий отличающихся пропорциями и степенью апроксимации, то есть приближения к плавным обводам. За основу геометрического построения ГДН была выбрана простая фигура, названная «единичный ГДН». Единичный ГДН представляет собой некую геометрическую фигуру с известными (определяемыми) параметрами длины и объема. Для изображения реального ГДН с вычисленными параметрами длины и объема, достаточно «растянуть и раздуть» единичный ГДН. Что показано на следующем изображении.
![]() |
Рисунок 7.2 - единичный газодинамический насос
|
Рисунок 7.3 - единичный ГДН после преобразований. Окончательная геометрия
Единичный ГДН представляет собой совокупность двух объемов: диффузора и камеры, в различных соотношениях диаметров камеры к диаметру впускного отверстия. Диаметр камеры равен единице (например, 1 см), остальные размеры в долях диаметра. Объемы конфигураций с различными соотношениями диаметров камеры к диаметру впускного отверстия даны в тех же единицах. В данном случае в см3.
Выполняя последовательно простые арифметические действия можно с достаточной точностью определить основные геометрические параметры требуемого ГДН.
Иногда для этого потребуется два и более повтора некоторых шагов. Связано это с непропорциональностью расчетного диаметра камеры ГДН с конструктивными размерами выхлопного окна конкретного двигателя.
Таблица 7.2 Соотношение основных размеров единичного ГДН
№№ | dвх – диаметр входа (см) | rвх – радиус входа (см) | VГДН – объем единичной ГДН (см3) | R – радиус образующей диффузора (см) | L – длина единичного ГДН (см) |
11 | 0,080 | 0,040 | 0,5428110 | 0,8169565 | 1,5 |
22 | 0,110 | 0,055 | 0,5495420 | 0,8460955 | 1,5 |
33 | 0,140 | 0,070 | 0,5564771 | 0,8777906 | 1,5 |
44 | 0,170 | 0,085 | 0,5636448 | 0,9123192 | 1,5 |
55 | 0,200 | 0,100 | 0,5714550 | 0,9500000 | 1,5 |
66 | 0,230 | 0,115 | 0,5788251 | 0,9912012 | 1,5 |
77 | 0,260 | 0,130 | 0,5867141 | 1,0365130 | 1,5 |
88 | 0,290 | 0,145 | 0,5954985 | 1,0859507 | 1,5 |
99 | 0,320 | 0,160 | 0,6047544 | 1,1405882 | 1,5 |
110 | 0,350 | 0,175 | 0,6144549 | 1,2009615 | 1,5 |
111 | 0,380 | 0,190 | 0,6256917 | 1,2679032 | 1,5 |
112 | 0,410 | 0,205 | 0,6366658 | 1,3424152 | 1,5 |
313 | 0,440 | 0,220 | 0,6496533 | 1,4257142 | 1,5 |
114 | 0,470 | 0,235 | 0,6621079 | 1,5192924 | 1,5 |
115 | 0,500 | 0,250 | 0,6763178 | 1,6250000 | 1,5 |
116 | 0,530 | 0,265 | 0,6919999 | 1,7451595 | 1,5 |
117 | 0,560 | 0,280 | 0,7090538 | 1,8827272 | 1,5 |
*Выделена средняя строка, удобная для начального варианта расчетов.
7.3 Расчетная часть
1) Принцип черчения ГДН. Примем длину ГДН равную 284 мм;
2) Зная скорость поршня, определяем объем ГДН, 89 см3:
3) Делим расчетную длину ГДН на длину единичного ГДН:
28,4/1,5= 18,9333333;
4) Умножаем полученную величину на усредненный объем единичного ГДН (строка 9):
18,9333333 * 0,6047544 = 11,450016;
5) Делим расчетный объем ГДН на полученную величину:
89 / 11,450016 = 7,7729149
6) Полученная величина есть квадрат кратности диаметров искомого ГДН к единичному.
Извлекаем корень квадратный:
7,77291490,5 = 2,7879947;
7) Внутренний диаметр входного отверстия ГДН по мотору, допустим 11,3 мм., Если мы увеличим диаметр выбранного единичного ГДН в 2,7879947 раза, получим всего 8,92 ;
8) Следующий шаг, второе приближение: 11,3 / 2,788 = 4,053...
9) Выбираем из таблицы 7.2, ряд с ближайшим диаметром – 0,41 это будет 12-ая строка.
10) Повторяем шаг 4, теперь умножая 18,9333333 * 0,6366658 = 12,054205.
11) Делим расчетный объем ГДН на полученную величину:
89 / 12,054205 = 7,3833156;
12) Извлекаем корень квадратный:7,38331560,5 = 2,7172257.
13) Диаметры входа единичного ГДН (строка 12) умножим на результат п.12: 4,1 * 2,7172257 = 11,140625.
Полученный результат на 0,15 мм меньше требуемого. Принимаем решение:
А) увеличить диаметр входного отверстия до 11,3 мм, плавно сопрягая с остальной геометрией;
Б) провести самостоятельное построение геометрии .
14) Вычерчиваем геометрию ГДН любым известным способом.
15) Рассчитываем и строим оконечность ГДН:
Диаметр отверстия выпускного патрубка находящегося в неподвижной среде без эжекции
dвых = [(Фв * V1/3ДВС *n ) / (K1/3ГДН * 55673)]0,5; мм (8)
где: Фв- фаза выхлопа, V1/3ДВС – корень кубический из объема мотора, n - обороты двигателя;
K1/3ГДН – корень кубический из показателя кратности объема ГДН 55673 – безразмерный коэффициент.
Площадь выпускного отверстия
S0 = (dвых /2)2*p; мм2
Площадь отверстия находящегося в потоке с установившейся скоростью V км/час:
SV = S0 – [(S0 * V) / 657 ] мм2 (9)
16) Выполняем сопряжение выпускного патрубка с конфузором. В акустике одна из аксиом гласит, что энергия волны не искажается, если канал, по которому проходит волна, имеет искривления или изменения сечений с радиусами не менее 1/10 длины волны.
Этот же принцип позволяет как угодно изгибать ГДН, при этом соблюдая правила:
А) длина средней линии изогнутого ГДН должна равняться расчетной прямой длине;
Б) поверхность оболочки искривленного ГДН является касательной к множеству сфер построенных на средней линии и равных по размеру и координатам от начала отсчета по оси, аналогичным на прямой оси (правило площадей).
C / n (10)
где С – скорость волны сжатия;
n - частота вращения ДВС в секунду.
Минимальный радиус rmin> 1
Если настроить резонансную трубу на режим экономии топлива калильные, искровые то в установившемся режиме резонанса трубу можно отсоединить от двигателя разгерметизировать двигатель продолжает экономить топливо, меняется только звук. Расстояние при котором разгерметизация не влияет на качество, четко лимитировано. Кроме зазора на работу влияет геометрия кромки ГДН. При отработанной компоновке системы ДВС-ГДН ввод двигателя в режим резонанса значительно ускоряется в отличие от герметичных ГДН. Алгоритм зазора и геометрия ГДН установлены.
Пример расчета ГДН:
Имеется двигатель для Р/У автомодели с данными:
- Объем двигателя, см3 - 3,5;
- Диаметр поршня, см - 1,66;
- Ход поршня, см - 1,6;
- Высота выхлопного окна, мм - 7,0;
- Длина шатуна, мм - 29;
Максимальная мощность при частоте вращения вала, мин-1 - 34500;Диаметр впускного отверстия ГДН, мм - 12,5;
Условия эксплуатации, при температуре воздуха 270С, относительной влажности 40% и атмосферном давлении 720 мм. Ртутного столба, то есть 0,98 кг/см2.
Находим:
А) Фаза выхлопа получается 181036’, принимаем 181,50;
Б) Скорость поршня - 18,4 м/с;
В) Теплонапряженность. Sс - площадь стенок цилиндра в рабочей зоне, включая окна;
Sоб - суммарная площадь поверхностей стенок, днища поршня и головки;
Ктн1 – показатель теплонапряженности первого рода, относительное количество тепла от сгорания топлива на единицу поверхности, рассеивающей это тепло;
Ктн2 - показатель теплонапряженности второго рода, влияние размеров трущихся поверхностей на единицу;
Ктн3 - показатель теплонапряженности третьего рода, влияние скорости трущихся поверхностей на единицу;
Ктн – совокупный показатель теплонапряженности.
Совокупный показатель теплонапряженности как прирощение к тепловым процессам двигателя прибавляем к единице и получаем искомый показатель теплонапряженности, необходимый для дальнейших расчетов:
К=(1 + Ктн )
Определяем исходные параметры
– площадь поршня Sп 3,14159*0,832= 2,1642413 см2.
поверхность рабочей части цилиндра Sс 3,14159*1,66*1,6=8,344063 см2.
поверхность объема Sоб 8,344063+2*2,1642413=12,672545 см2.
- Ктн1= 3,5/12,672545=0,2761876
-Ктн2=8,344063*1,6/12,672545=1,0534979}
- Ктн3 = 18,4/12,672545=1,4519577
- Ктн=Ктн1*Ктн2*Ктн3=0.422466
- К=1+Ктн=1,422466;
Г) Объем ГДН в соответствии со скоростью поршня.
Находим:
VГДН= 3.5*36,4=127,4 см3.
Д) Скорость волны сжатия:
для топлива метанол 80% + масло 20%
Сп={2*[27-20+403]*[0,98+0,001*(40-75)]*1,422466*261,02809}0,5= 536,3983м/с;
для топлива с 15% нитрометана
Сп={2*[27-20+453]*[0,98+0,001*(40-75)]*1,422466*255,11188}0,5= 561,68923 м/с;
Е) Длина ГДН
для топлива метанол 80% + масло 20%
L=0,5[1:( 34500:60)]:360 *536,3983*181,5 = 279,9 мм
для топлива с 15% нитрометана
L=0,5[1:( 34500:60)]:360 *561,68923*181,5 = 293,1 мм;
Ж) Масштаб увеличения длины единичного ГДН:
для топлива метанол 80% + масло 20% 279,9/1,5=18,66;
для топлива с 15% нитрометана293,1/1,5=19,54;
З) Масштаб увеличения диаметра единичного ГДН, в первом приближении для топлива метанол 80% + масло 20%
18,66*0,6047544=11,284717; 127,4/11,284717=11,289605; 11,2896050,5=3,36;
для топлива с 15% нитрометана
19,54*0,6047544=11,8169;
127,4/11,8169=10,781169;10,7811690,5=3,283;
И) Определяем соответствие входного отверстия ГДН:
для топлива метанол 80% + масло 20% 3,36*0,32=1,075см;
Не достаточно.
для топлива с 15% нитрометана 3,283*0,32=1,0507см;
Не достаточно.
Повторяем действия для топлива метанол 80% + масло 20%
18,66*0,6256917=11,675407;
127,4/11,675407=10,911825;10,9118250,5=3,3033051;
для топлива с 15% нитрометана
19,54*0,6256917=12,226015; 127,4/12,226015=10,420402;10,4204020,5= 3,2280647;
Определяем соответствие входного отверстия ГДН:
для топлива метанол 80% + масло 20% 3,3033051*0,38=1,255см; Удовлетворяет.
для топлива с 15% нитрометана 3,2280647*0,38= 1,227см;
Удовлетворяет.
М) Диаметр выпускного патрубка
dвых = [(181.5* 1,51829*34500 ) / (3,31411* 55673)]0,5= 7,18 мм,………... разумнее сделать больше, затем дросселировать по необходимости.
Длину патрубка предварительно рисуем 45-50 мм
Радиус сопряжения патрубка с конфузором по формулам 10 и 11:
топливо метанол 80%+масло 20% 536398, 3 / 34500 = 932,487 мм; принимаем r94 мм;
топливос 15% нитрометана561689,23/34500=976,85мм;
принимаем r98 мм;
Технологически целесообразно на обеих ГДН сопряжения выполнить одинаковыми, большего радиуса. Патрубок можно отрезать на расстоянии 7,5 мм от точки касания дуги r98 мм с диметром патрубка.
8. Технико-экономическое обоснование работы
Дата добавления: 2018-09-22; просмотров: 308; Мы поможем в написании вашей работы! |
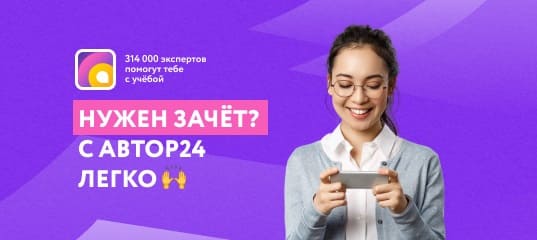
Мы поможем в написании ваших работ!