Тепловой расчет червячной передачи. Охлаждение и смазка червячной передачи
Расчет при установившемся тепловом состоянии проводят по уравнению теплового баланса:
W = W1,
где W – количество теплоты, Дж, выделяющейся при непрерывной работе передачи в единицу времени, Дж/с;
W1 – количество теплоты, отводимой с поверхности корпуса передачи и через основание в единицу времени.
W = 103(1-η)P1,
где η – КПД передачи без учета потерь на привод вентилятора;
Р1 – мощность на червяке, кВт.
W1 = KT(tM – t0)A(1+ψ),
где KT – коэффициент теплопередачи с поверхности корпуса, равный 12…18 Вт/(м2 0С);
tM и t0 – соответственно температура масла и окружающей среды °С;
А – поверхность теплопередачи корпуса (без учета основания), м2;
ψ – коэффициент, учитывающий теплоотвода через основание, при установке корпуса на металлическом основании он достигает 0,3, при бетонном основании он равен примерно 0.
Если температура масла в передачи превышает допустимую для данного смазочного материала, необходимо:
1) либо увеличить поверхность охлаждения, применяя охлаждающие ребра (в расчете учитывается только 50% поверхности ребер;
2) либо применить искусственное охлаждение, которое можно осуществить:
− обдувом корпуса воздухом с помощью вентилятора, насаженного на вал червяка, коэффициент теплоотдачи обдуваемых стенок достигает 30 Вт/(м2 °С);
− охлаждением масла водой, проходящей через змеевик, коэффициент теплоотдачи с поверхности труб до 200 Вт/ (м2 °С);
− применением циркуляционной системы смазки со специальным, отдельно стоящим холодильником.
|
|
Силы в зацеплении червячной передачи. Материалы для червячной передачи
Изготовление червячной пары из твердых материалов не обеспечивает достаточной износостойкости и сопротивления заеданию. Поэтому одну из деталей (обычно червячное колесо) выполняют из антифрикционного материала, хорошо сопротивляющегося заеданию и износу.
Наиболее часто в качестве материала для изготовления червяка применяют сталь 18ХГТ, твердость которой после цементации и
закалки 56…63 НRС. Используют также стали 40Х. 40ХН, 35ХГСА с поверхностной закалкой до твердости 45…55 НRС.
Червячные колеса обычно выполняют составными: т.е. венец – из антифрикционных, относительно дорогих и малопрочных материалов (табл. 9.3); центральная часть – из стали, а при небольших нагрузках – из чугуна. При скоростях скольжения больше 3 м/с венцы выполняют из оловянно – фосфористых бронз БрО10НФ, БрО10Ф.
Валы и оси. Классификация и материалы. Приближенный, проектный расчет валов
Валом называется деталь, предназначенная для поддерживания вращающихся частей машины, непосредственно участвующих в передаче вращательного движения; и передающая крутящий момент.
|
|
В отличие от вала, ось – деталь, предназначенная для поддержания вращающихся частей, но в передаче энергии непосредственно не участвует.
По назначению валы можно разделить на коренные, т.е.валы несущие основные рабочие органы машины (ротор турбины, коленчатый вал двигателя внутреннего сгорания), и передаточные
По форме геометрической оси разделяют на и коленчатые
По профилю поперечного сечения: со шпоночными или шлицевыми канавками, а также фасонно-профильные, граненные
По наличию осевого отверстия: полые и сплошные
По изменению сечения вдоль геометрической оси валы и оси могут быть постоянного сечения ступенчатые с цилиндрическими и коническими отверстиями
По числу опор валы и оси могут быть консольными, двух- и многоопорными.
Основными материалами для валов и осей служат углеродистые и легированные стали. Для валов и осей, диаметры которых определяются , в основном, жесткостью, применяют углеродистые конструкционные стали Ст4, Ст5 без термообработки. В ответственных и тяжелонагруженных конструкциях ( когда критерием работоспособности является прочность) используют термически обрабатываемые среднеуглеродистые и легированные стали 40, 45, 40Х, 40ХН, 40ХН2МА, 30ХГС, 30ХГСА и др. Валы из этих сталей в зависимости от решаемых задач подвергают улучшению (закалке с высоким отпуском) или поверхностной закалке например, нагрев ТВЧ) с низким отпуском.
|
|
Применение легированных сталей дает возможность при необходимости ограничить массу и габаритные размеры, повысить стойкость шлицевых соединений. Их применение можно оправдать конструктивными соображениями (прочностью зубьев, нарезаемых непосредственно на валу и т.д.)
Быстроходные валы, вращающиеся в подшипниках скольжения, требуют весьма высокую твердость поверхности цапф; для этого их изготовляют из цементируемых сталей типа 20Х, 12ХН3А, 18ХГТ или из азотируемых сталей типа 38Х2МЮА.
Для изготовления коленчатых валов и валов с большими фланцами, наряду со сталью применяют высокопрочные (с шаровиднымграфитом) и модифицированные чугун.
Дата добавления: 2018-09-20; просмотров: 743; Мы поможем в написании вашей работы! |
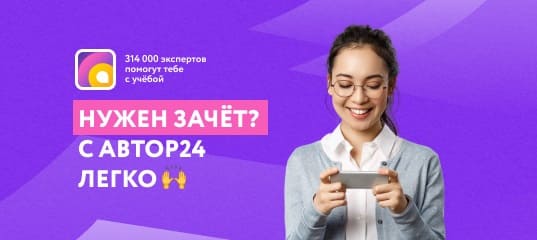
Мы поможем в написании ваших работ!