Расчет на прочность деталей КШМ
КШМ предназначен для передачи силы давления газов на поршень и через шатун на шейку коленвала. Основные элементы механизма: шатун, вкладыши подшипников, коленвал и шатунные болты.
Шатун. В процессе работы двигателя шатун испытывает действие переменных нагрузок давлений и сил инерции, причем на определенных режимах работы действие этих сил носит ударный характер.
Стержню шатуна придают в основном двутавровый или Н-образный профиль штамповкой, ковкой или литьем.
При проектировании поршневой головки шатуна необходимо добиться по возможности минимального удельного давления в соединении палец-шатун, а также наибольшей жесткости и прочности при наименьшей массе.
При конструировании кривошипной головки шатуна стремятся, чтобы она сопрягалась со стержнем большими радиусами и в средней части имела ребра жесткости по периметру головки для повышения жесткости и снижения концентрации напряжений в местах изменения сечений и переходов.
Головка должна быть минимальна по габаритам и массе, для уменьшения размеров картера и нагрузок на подшипники. При этом необходимо обеспечить работу шатунных болтов на чистое растяжение.
Поршневая головка шатуна подвергается растяжению и сжатию под действием сил инерции деталей поршневой группы и давления газов, постоянной силы от запрессовки подшипниковой втулки, а также от нагревания втулки и головки при работе. Наиболее опасное сечение - место перехода головки в стержень шатуна, поэтому этот переход делают максимально возможного радиуса.
|
|
Стержень шатуна испытывает растяжение под действием сил инерции масс, расположенных над сечением, а также суммарные напряжения сжатия и продольного изгиба.
Кривошипная головка шатуна работает на изгиб и растяжение под действием сил инерции возвратно-поступательно движущихся масс.
Коленчатый вал
Коленвал - наиболее важная деталь двигателя. Он работает в условиях периодических нагрузок от действия сил давления газов, сил и моментов инерции, которые в совокупности вызывают значительные знакопеременные скручивающие и изгибающие моменты, а также крутильные и продольные колебания вала, создающие при резонансе дополнительные напряжения.
В связи с форсированием двигателей наддувом и увеличением скорости вращения коленвала возрастают напряжения в опасных сечениях вала и удельные давления на подшипники, что снижает надежность работы вала и увеличивает износ подшипников. Поэтому коленвал должен быть прочным, жестким и износостойким; обеспечивать надежную работу в пределах срока эксплуатации; быть по возможности полностью динамически уравновешенным и технологичным в изготовлении.
|
|
Для автомобильных двигателей валы изготовляют цельными свободной ковкой, штамповкой, отливкой и т.д. Материал - высокопрочные легированные стали, высокопрочные чугуны.
При расчете коленвал рассматривают как разрезную балку, из которой выделяют одно наиболее нагруженное расчетное колено. За расчетные сечения принимают галтели шеек по щекам и края маслоподводящих отверстий в шейках.
При таком расчете напряжения получаются несколько завышенными, следовательно завышен действительный запас прочности, что дает возможность последующего форсирования режимов работы двигателя.
Шатунные болты - самостоятельно.
Вопросы для самоконтроля
1. 1. Какие характерные расчетные режимы принимают для расчета двигателя?
2. 2. Какие расчетные схемы используют для расчета на прочность поршня, поршневого пальца, поршневого кольца, коленвала? Какие нагрузки учитываются при этом?
Лекция 21.
План
1. Механизм газораспределения
2. Механизм привода
3. Кинематика клапанного механизма
4. Система смазки
5. Система питания
Механизм газораспределения
Процесс газообмена в четырехтактных двигателях обеспечивается работой клапанов, механизмов их приводов и распределительного вала с механизмом передач, передающим вращение от коленвала.
|
|
Конструкция механизма газораспределения зависит от :
1) расположения клапанов ( в блоке цилиндров (нижнее) или в головке блока (верхнее);
2) формы камеры сгорания;
3) размещения клапанов (последовательное одностороннее или поперечное двустороннее), числа одноименных клапанов;
4) расположения распредвала (нижний или средний в блоке цилиндров, верхний в головке блока);
5) типа толкателей ( плоские, роликовые, выпуклые или рычажные);
6) конструкции коромысел (одно- или двуплечевые рычаги, траверса на два одноименных клапана);
7) числа и типа пружин (цилиндрические, конические, тороидальные);
8) типа механизма передачи, передающего вращение от коленвала к распределительному ( зубчатая, цепная или ременная).
В существующих двигателях применяют исключительно клапанные механизмы, обеспечивающие достаточно совершенный процесс газообмена на высоких скоростных режимах и большом давлении наддува.
Эффективность газообмена оценивается коэффициентом наполнения и равномерностью наполнения отдельных цилиндров.
В карбюраторных двигателях применяют в основном верхнеклапаные распределительные механизмы.
|
|
Наиболее распространены цилиндрические, клиновидные и полусферические камеры сгорания. При цилиндрических и клиновидных камерах клапаны расположены обычно последовательно в один ряд вдоль оси двигателя. При полусферических - в поперечной плоскости.
Расположение клапанов в продольной плоскости предполагает удлинение выпускных каналов и усложнение приводного механизма.
В случае полусферических камер угол развала между осями клапанов при поперечном их расположении , при продольном - 55
. С увеличением угла наклона
форму канала удается сделать более плавной, т.е. уменьшить гидравлическое сопротивление. Обычно же
.
При расположении клапанов в продольной плоскости головки уменьшение угла вызывается трудностями размещения пружин. Величина угла между осями клапанов в этих двигателях практически не влияет на длину каналов и их форму.
В случае полусферических камер сгорания относительные диаметры горловин достигают наибольших значений: dВП/D= 0,46...0,52. В этом случае каналы клапанов, направленные в разные стороны могут иметь большие проходные сечения и спрямленные формы.
В случае клиновидных или плоскоовальных камер оси разноименных клапанов обычно параллельны. Для увеличения диаметра клапанов камеры сгорания иногда выводят за контур цилиндра. Относительные диаметры впускных клапанов в этом случае несколько меньше, чем при полусферической (dВП/D= 0,42...0,46).
В дизелях используют исключительно ГРМ с верхними клапанами. При вихрекамерном и предкамерном смесеобразовании относительные диаметры горловин впускных клапанов невелики, т.е. dВП/D= 0,35...0,4.
В дизелях с непосредственным впрыском это отношение достигает 0,38...0,42. Невозможность увеличения проходных сечений каналов объясняется размещением в головках цилиндров вихревых камер, предкамер и приливов под форсунки и свечи.
Механизм привода
При проектировании механизма привода стремятся по возможности приблизить распределительный вал к клапанам, что уменьшает поступательно движущиеся массы и увеличивает общую жесткость механизма привода.
Суммарные силы, действующие в механизме привода достигают в быстроходных дизелях больших значений. Для уменьшения сил инерции поступательно движущихся масс применяют среднее и верхнее расположение распредвала, что уменьшает массу и повышает жесткость механизма привода.
В V-образных дизелях распредвал целесообразно размещать в развале блока цилиндров.
Ведущие шестерни обычно располагают в передней части коленвала. Для уменьшения шума устанавливают шестерни из текстолита или других пластмасс. Широко распространены для привода верхних распредвалов цепные передачи.
Распределительный вал. При размещении распредвала в блок-картере его устанавливают в неразъемные подшипники с торца двигателя. При размещении вала в головке блока применяют и разъемные подшипники.
Распредвал фиксируют от осевых перемещений, чтобы положение ведомой шестерни оставалось неизменным. Фиксация осуществляется пластинами, подвижными упорами с пружиной или фланцами, выточенными на самом валу.
Диаметр распредвалов определяется как 0,28...0,35 D ( верхний предел - для более быстроходных двигателей).
Подшипники смазываются под давлением.
Толкатели - грибковые, цилиндрические выпуклые с износостойкой
вставкой, гидравлические. Продольную ось толкателя обычно смещают относительно оси симметрии кулачка. На поверхности контакта создается момент трения, под действием которого толкатель поворачивается вокруг своей оси, что обеспечивает равномерный износ контактирующих поверхностей.
Штанги - трубчатые, сплошные или составные. Длину по возможности минимизировать.
Клапаны. Наиболее нагруженная часть - головка клапана (удар, термические нагрузки). Наибольшая концентрация напряжений возникает на поверхности посадочного конуса и в зоне перехода головка-стержень.
Надежная работа клапанов обеспечивается в основном следующим:
1) выбор материалов для клапана, седла и направляющей втулки;
2) подбор конструктивных параметров и форм для уменьшения притока теплоты от отработавших газов и интенсивного теплоотвода;
3) повышение жаропрочности и износостойкости;
4) применение механизмов поворота клапанов;
5) эффективное охлаждение.
При форсировании двигателей температура клапанов повышается, поэтому клапаны дополнительно защищают от коррозии металлокерамическим покрытием.
Для улучшения теплоотвода от головки к стержню выпускные клапаны делают полыми; внутренние полости заполняют примерно на 40% натрием, имеющим высокую теплопроводность.
Теплота от клапана отводится через седло и стержень. Температура выпускного клапана может быть понижена с помощью следующих мероприятий:
1) укорочения направляющей втулки, чтобы она не выступала в патрубок и не омывалась отработавшими газами;
2) увеличение диаметра стержня клапана для усиления теплоотвода;
3) отливки направляющей втулки как одно целое с головкой цилиндров.
Для лучшего теплоотвода диаметр стержня выпускного клапана должен быть на 10-15% больше, чем впускного. У впускного втулку делают короче для увеличения проходного сечения в патрубке. Плотная посадка клапана на седло возможна только при наличии зазора в клапанном механизме.
Угол фаски у выпускных клапанов 45 , у впускных 45 или 30 . Уменьшение угла фаски позволяет увеличить пропускную способность в зоне малых подъемов клапана при высоких коэффициентах расхода воздуха.
Седла выпускных клапанов делают из легированных чугунов. Радиальная толщина стенки седла должна быть не меньше (0,1...0,13)dТ.
Направляющие втулки изготавливают из серого чугуна или бронзы (в форсированных двигателях для повышения теплоотвода). Втулки запрессовывают в головку цилиндров. Концы втулок со стороны пружины защищают манжетой от излишнего оседания на них масла. Подсос масла наблюдается в патрубке впускного клапана. Зазор между стержнем и втулкой для впускных клапанов 0,02...0,05 мм и 0,05...0,07 мм для выпускных.
Дата добавления: 2018-09-20; просмотров: 439; Мы поможем в написании вашей работы! |
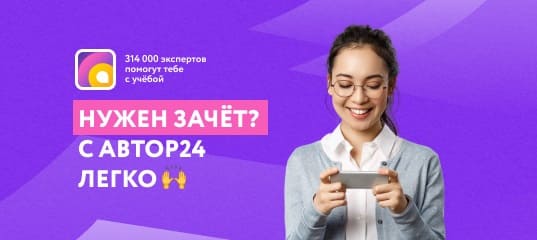
Мы поможем в написании ваших работ!