Основы расчета на прочность деталей ЦПГ и КШМ
Двигателей
План
1. Расчетные режимы нагрузок ДВС.
2. Расчет поршня.
3. Поршневой палец.
4. Поршневые кольца.
5. Расчет на прочность деталей КШМ.
6. Коленчатый вал.
Расчетные режимы нагрузок ДВС
Основные виды нагрузок - это силы давления газов, силы и моменты инерции поступательно движущихся и вращающихся масс, усилия от упругих колебаний и теплового воздействия. Нагрузки зависят от абсолютных значений сил и моментов, от характера их приложения. Они бывают кратковременные или длительные, ударные или постепенные.
За характерные расчетные режимы принимают:
1) Режим максимального крутящего момента MK.max при соответствующей частоте вращения nMK.max=(0.4…0.6)nH.. При этом давление газов в конце процесса сгорания (ВМТ) достигает наибольшего значения pZmax, а силы инерции сравнительно малы и ими можно принебречь. Давление газов pzmax определяют по тепловому расчету, выполненному для режима максимального крутящего момента, силами инерции пренебрегают.
2) Режим номинальной мощности Nен и номинальной частоты вращения коленвала n 4н 0. В этом режиме на детали двигателя действуют силы инерции и давления газов. Этот режим в качестве расчетного принимают очень часто. Условно принимают, что максимальная сила давления газов действует совместно с максимальной инерционной силой в ВМТ. Максимальную силу давления определяют тепловым расчетом для режима номинальной мощности с учетом скругления индикаторной диаграммы.
|
|
3) Режим максимальной частоты вращения nx.max вала при работе двигателя на холостом ходу. При этом силы инерции имеют наибольшее значение, а давление газов незначительно и им пренебрегают.
Для карбюраторных двигателей nx.max=(1.05…1.2)nH ; для дизелей nx.max = (1,04...1,07)nH.
Однако выбор расчетных режимов не характеризует точного распределения нагрузок в деталях. Он не учитывает температурное состояние деталей и возможное нарушение физико-механических свойств, а также изменение геометрии деталей и узлов. Поэтому наиболее ответственные детали двигателей рассчитывают на статическую прочность по действию максимальной силы и на усталостную по действию переменных нагрузок.
При расчетах делается ряд допущений в схемах действия нагрузок и по форме деталей: коленвал рассчитывают как разрезную балку; донышко поршня как равномерно нагруженную пластину, свободно опирающуюся на кольцевую опору и т.д.
Существующие расчеты на прочность позволяют с достаточной точностью определять напряжения и деформации, которые затем сравнивают с расчетными значениями напряжений в деталях, успешно работающих.
Детали ДВС рассчитывают на :
|
|
1) Статическую прочность по действию максимальной нагрузки и усталостную прочность по действию переменных ударных, контактных и тепловых нагрузок (коленвал, шатун, клапаны и др.);
2) Жесткость, которая для некоторых деталей более важна, чем прочность, т.к. быстрый износ, изменение формы (овализация поршневого кольца, гильзы цилиндра и др.) - это следствие недостаточной жесткости деталей. Этому расчету подвергают распредвал, шатун, гильзу цилиндра, поршневой палец;
3) Крутильные колебания, для чего определяют напряжения в валах при резонансе и условия его появления, устанавливают способы предотвращения или ослабления резонансных колебаний ( в основном для коленвалов);
4) Работоспособность теплонапряженных деталей. Расчет заключается в определении температурного состояния в характерных точках или зонах, температурных полей и напряжений, тепловых зазоров и т.д.
Наряду с перечисленными возможны и специальные расчеты.
Определение запасов прочности деталей с учетом факторов формы, масштабного, технологического и других факторов выполняют по известным зависимостям из курса “Сопротивление материалов”.
Расчет поршня
К основным элементам поршня относятся головка и направляющая часть (юбка).
|
|
Днище поршня может быть разнообразной формы в зависимости от организации рабочего процесса в двигателе. В карбюраторных двигателях в основном применяют плоское днище поршня, за исключением двухтактных, где днище имеет выпуклую форму.
В дизелях форма днища определяет способ смесеобразования и эффективность рабочего процесса.
Юбка поршня передает гильзе цилиндра нормальную силу N от шатуна. В процессе работы поверхность юбки деформируется под действием сил давления газов и нагрева.
В карбюраторных двигателях юбки поршней в основном разрезные, с П- или Т-образной прорезью, что позволяет уменьшить зазоры по длине юбки, снизить рабочие температуры, избежать задиров, снизить массу поршня.
Юбку дизелей выполняют цельной.
В результате действия температурных деформаций и нормальной силы на боковую поверхность поршня его сечение принимает овальную форму, причем с увеличением размера вдоль оси пальца. Эта деформация учитывается при изготовлении поршня, снятием части металла в зоне бобышек поршневого пальца или приданием корпусу поршня овальной формы, с большой осью элипса, перпендикулярной оси поршневого пальца.
Для обеспечения надежной работы поршневой группы теплота отводится от головки поршня через поршневые кольца, стенки поршня, смазку, поршневой палец и др. Через поршневые кольца в охлаждаемую гильзу цилиндра отводится 60...75% всей теплоты.
|
|
Необходимо стремиться к равномерному распределению температурного поля в головке поршня.
Допустимые температуры головки поршня:
1) из алюминиевых сплавов - 570...620 К;
2) из чугуна - 670...720 К;
3) из жаропрочных сплавов - 870...920 К.
Во избежании пригорания первого кольца температура стенки под канавкой не должна превышать 470...490 К.
Днище поршня рассчитывают по механическим напряжениям изгиба под действием максимального давления сгорания pz.max и по температурным напряжениям, возникающим от осевого и радиального перепада температур. Действительному режиму работы поршня наиболее соответствует предположение о заделке днища по контуру и его нагружении наибольшим, равномерно распределенным давлением газов.
При этом не учитывается действительная форма днища и фактическое распределение температур по днищу, влияние юбки, ребер жесткости и т.д. Поэтому расчет является приближенным, результаты проверяются экспериментально.
За расчетный режим принимают:
1) для карбюраторных двигателей - режим максимального крутящего момента MK.max
2) для дизелей - режим максимальной мощности Ne.max.
Поршневой палец
Поршневой палец передает усилия давления газов на шатун. В процессе работы он подвергается деформации изгиба, сдвига и овализации. Материал пальца работает на усталость. Овализация выше допустимого значения приводит к образованию трещин в бобышках поршня и продольных трещин в поршневом пальце.
В основном применяют пальцы плавающего типа, у которых износ распределяется равномерно по рабочей поверхности и устранена опасность заедания. Усталостную прочность пальца повышают полировкой его поверхности.
Поршневой палец рассчитывают на наибольшее напряжение изгиба в среднем сечении по длине и касательное напряжение среза в сечении между бобышкой поршня и головкой шатуна от действия силы максимального давления сгорания pz.max. Определяют также наибольшее напряжение от овализации, возникающее на внутренней поверхности пальца; максимальное удельное давление на опорную поверхность пальца и втулки поршневой го-ловки шатуна и монтажные зазоры между пальцами и бобышками поршня.
Дата добавления: 2018-09-20; просмотров: 909; Мы поможем в написании вашей работы! |
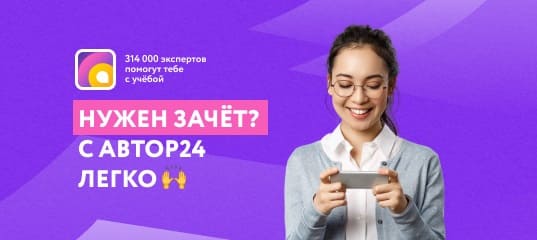
Мы поможем в написании ваших работ!