Что такое технологический маршрут?
Под технологическим маршрутом изготовления детали понимается последовательность выполнения технологических операций с определением содержания операций, выбором оборудования и технологической оснастки для их выполнения.
Для вновь проектируемых маршрутных ТП исходными данными являются: рабочий чертеж, определяющий материал, конструктивные формы и размеры детали; технические условия на изготовление детали, характеризующие точность и качество обработанных поверхностей, и особые требования (твердость и структура материала, термическая обработка, балансировка, виды контроля и др.); объѐм выпуска деталей во времени.
Задача проектирования ТП характерна многовариантностью возможных решений. Для уменьшения их числа важно использовать типовые решения, рекомендации нормативных и руководящих материалов. Методом последующего сопоставления эффективности и рентабельности (трудоемкости, себестоимости, КИМ) разработанных вариантов окончательно выбирают лучший вариант.
Процесс проектирования маршрута обработки заготовки содержит взаимосвязанные и выполняемые в определенной последовательности этапы:
¾ Анализ чертежа детали .
¾ Выбор исходной заготовки.
¾ Выбор технологических баз и схем установки заготовок.
¾ Определение методов и маршрутов обработки отдельных поверхностей и комплексов поверхностей детали с одинаковыми требованиями по точности и качеству, которые целесообразно обрабатывать с одного установа.
|
|
¾ Выбор оборудования, оснастки, режущего и мерительного инструмента.
¾ Разработка маршрута обработки заготовки в целом.
¾ Оформление технологической документации.
Для удобства дальнейшей разработки ТП рекомендуется на копии чертежа детали выполнить технологический чертеж, содержащий нумерацию поверхностей детали и оценку состояния каждой поверхности представить в виде таблицы.
Предварительный выбор методов обработки элементарных поверхностей и числа необходимых переходов (операций) производится на основе обобщенных таблиц примерных маршрутов (Приложение табл.1) исходя из требований, предъявляемых к конечной точности и качеству поверхностей, свойств материала и вида поверхности (плоская, цилиндрическая наружная, цилиндрическая внутренняя). По заданному квалитету точности и шероховатости поверхности выбирают один или несколько возможных методов окончательной обработки, т.е. последний технологический переход или операцию. Зная вид и точность заготовки, таким же образом выбирают первый начальный метод маршрута. Определив первый и окончательный переходы, устанавливают необходимость промежуточных переходов, число которых тем больше, чем ниже точность исходной заготовки и выше конечные требования к поверхности.
|
|
Для качественного проектирования маршрута могут быть рекомендованы общие принципы:
1. На первых операциях обрабатывают поверхности, которые будут использоваться в качестве технологических баз на всех или большинстве операциях ТП. Обработка черновых баз не должна повторяться в маршруте.
2. Используя чистовые базы, обрабатывают остальные поверхности в последовательности, обратной их степени точности: чем точнее поверхность, тем позже еѐ обрабатывают.
2. 3. Используя разработанные ранее маршруты обработки отдельных поверхностей, выявляют необходимость расчленения ТП на стадии обработки. Стадия – часть ТП, включающая однородную по характеру и точности обработку различных поверхностей и детали в целом. Такими стадиями являются черновая, чистовая, тонкая и отделочная.
3. Вспомогательные поверхности (мелкие отверстия, фаски, пазы, галтели и др.) обычно обрабатывают на чистовой стадии. В самостоятельные операции выделяют обработку шлицев, зубьев, групп отверстий или пазов.
4. Предварительное содержание операций устанавливают объединением тех переходов на данной стадии обработки, которые могут быть выполнены на одном станке. Компоновка переходов осуществляется на основе определения комплекса поверхностей с одинаковыми требованиями по точности и качеству, которые целесообразно обрабатывать с одного установа.
|
|
5. Операции механической обработки следует увязывать с операциями термической и химико-термической обработки. Отделочную стадию рекомендуется выполнять после термической обработки детали.
6. В маршрутный ТП включают слесарные, моечные и контрольные операции.
12. Как определяется нормируемое время (Тн)?
При расчёте изготовления детали определяют необходимую норму времени.
Нормированное время – это время полезной работы, связанной с выполнением производственного задания и определяется по формуле:
Тн =То +Тв +Тдоп +Тпз, мин,
где То – основное время, мин;
Тв– вспомогательное время, мин;
Тдоп– дополнительное время, мин;
Тпз– подготовительно – заключительное время, мин;
13. Как определяется штучное время (Тщт)?
Штучное время определяется по формуле:
,
где Тоб– время на обслуживание рабочего места, мин,
То– основное время, мин,
Тв– вспомогательное время, мин;
|
|
Тдоп– дополнительное время, мин;
14. На что затрачивается дополнительное время (Тд)? Как оно определяется?
Дополнительное времяопределяется по формуле:
мин.
Где
То– основное время, мин,
Тв– вспомогательное время, мин;
15. На что затрачивается вспомогательное время (Тв)? Как оно определяется?
Вспомогательное время определяется по формуле:
,
где ТВ1– время на установку и снятие детали.
ТВ2– время приемов управления станком и смены инструмента.
Дата добавления: 2018-08-06; просмотров: 1011; Мы поможем в написании вашей работы! |
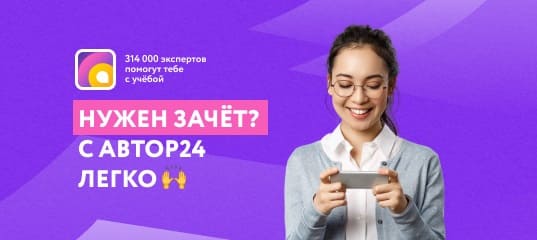
Мы поможем в написании ваших работ!