Основы химизма процесса. Термодинамика и термохимия основных реакций, их влияние на режим и аппаратное оформление процесса.
Сырье и продукты каталитического риформинга.
Сырье
В качестве сырья для каталитического риформинга обычно используют бензиновые фракции первичной перегонки нефтей. Пределы выкипания этих фракций колеблются в широком интервале— от 60 до 210°С. Для получения ароматических углеводородов в большей части используют фракции, выкипающие при 60— 105 или при 60—140°С, а для получения высокооктановых автомобильных бензинов — фракции 85—180 °С. Иногда широкую фракцию, выделяемую на установке первичной
перегонки нефти, дополнительно разгоняют на более узкие фракции на установках вторичной перегонки.
На рис. 61 показана зависимость октанового числа бензина от его выхода при каталитическом риформинге различных фракций (62—140, 85—140 и 105—140°С), полученных при первичной перегонке сернистых нефтей. С утяжелением сырья в пределах 85— 140 °С уменьшается содержание ароматических углеводородов и несколько снижается октановое число бензинов. Важно подчеркнуть, что между выходом бензина при риформинге и его октановым числом существует определенная
зависимость — с повышением октанового числа (независимо от метода определения) выход бензина уменьшается. Эта же зависимость подтверждается данными приведенными на рис. 62 и 63. Сопоставление результатов рифор-минга фракций 85—140 °С (при 20 ат) и 140—180 °С (при 40 ат) с результатами риформинга широкой фракции 85—180 °С при 20 ат показывает, что в случае риформинга фракции 85—180 °С выход бензина с октановым числом 95 (по исследовательскому методу) возрастает на 2—2,5%.
|
|
Однако раздельный риформинг бензиновых фракций имеет некоторые преимущества: большая продолжительность работы катализатора без регенерации, лучшая маневренность в работе и т. д. Поэтому выбор того или иного варианта получения высокооктанового бензина определяется с учетом конкретных условий работы нефтеперерабатывающего завода. Весьма важно учитывать возможность и целесообразность получения ароматических углеводородов.
Продукты каталитического риформинга.
В процессе каталитического риформинга образуются газы и жидкие продукты (риформат). Риформат можно использовать как высокооктановый компонент автомобильных и авиационных бензинов или направлять на выделение ароматических углеводородов, а газ, образующийся при риформинге, подвергают разделению.
Высвобождаемый при этом водород частично используют для пополнения потерь циркулирующего водородсодержащего газа и для гидроочистки исходного сырья (если она есть), но большую же часть водорода с установки выводят.
Такой водород значительно дешевле специально получаемого. Именно этим объясняется его широкое применение в процессах, потребляющих водород, особенно при гидроочистке нефтяных дистиллятов.
|
|
Кроме водородсодержащего газа из газов каталитического риформинга выделяют
сухой газ (C1—С2 или С1—С3) и сжиженные газы (Сз—С4); в результате получают стабильный
дебутанизированный бензин.
В ряде случаев на установке (в стабилизационной ее секции) получают стабильный бензин с заданным давлением насыщенных паров. Это имеет значение для производства высокооктановых компонентов автомобильного или авиационного бензина. Для получения товарных автомобильных бензинов бензин риформинга смешивают с другими компонентами (компаундируют). Смешение вызвано тем, что бензины каталитического риформинга содержат 60—70% ароматических
углеводородов и имеют утяжеленный состав, поэтому в чистом виде они непригодны для использования. В качестве компаундирующих компонентов могут применяться легкие бензиновые фракции (н. к. 62 °С) прямой перегонки нефти, изомеризаты и алкилаты. Поэтому для увеличения производства высокооктановых топлив на основе бензинов риформинга необходимо расширять производства высокооктановых изопарафиновых компонентов. В табл. 21 приведены данные о
|
|
составе высокооктановых автомобильных бензинов, полученных компаундированием соответствующих фракций каталитического риформинга и изопарафиновых компонентов.
Для получения автомобильного бензина с октановым числом 95 (по исследовательскому методу) риформинг-бензин должен иметь октановое число на 2—3 пункта больше. Это компенсирует уменьшение октанового числа бензина при разбавлении его изопарафиновыми компонентами.
С увеличением количества изокомпонента чувствительность бензина (разница в его октановых числах по исследовательскому и моторному методам) снижается, так как октановые числа чистых изопарафиновых углеводородов по моторному и исследовательскому методам практически совпадают
Было установлено, что подвергать изомеризации н-гексан, выделенный из рафината каталитического риформинга, нецелесообразно. Лучше получать изокомпонент из пентановой фракции бензина прямой перегонки нефти и выделять
изогексановую фракцию из рафината каталитического риформинга
28. Катализаторы риформинга
Катализаторы риформинга обычно обладают двумя функциями: кислотной и дегидрирующей. В качестве катализаторов обычно используют платину на окиси алюминия. Кислотные свойства катализатора определяют его крекирующую и изомеризующую активность. Кислотность имеет особенно большое влияние при переработке сырья с большим содержанием парафиновых углеводородов: инициирование кислотными катализаторами реакций гидрокрекинга парафинов и изомеризации пятичленных нафтенов в шестичленные с последующей их дегидрогенизацией и дегидроциклизацией (в результате дегидрирующей способности катализатора) ведет к образованию ароматических углеводородов. Платиновый компонент катализатора обладает дегидрирующей функцией. Он ускоряет реакции гидрирования и дегидрирования и, следовательно, способствует образованию ароматических углеводородов и непрерывному гидрированию и удалению промежуточных продуктов, способствующих коксообразованию. Содержание платины обычно составляет 0,3—0,65 вес.%; при снижении этой величины уменьшается устойчивость катализатора против ядов. Но и чрезмерное содержание металла нежелательно: при повышении концентрации платины усиливаются реакции деметилирования и расщепления нафтеновых углеводородов. Другим фактором, ограничивающим содержание платины в катализаторе, является ее высокая стоимость. Таким образом, кислотная функция катализатора необходима для протекания реакций гидрокрекинга и изомеризации, а дегидрирующая— для процессов дегидрирования. Сочетание этих двух функций определяет качество бифункционального катализатора риформинга.
|
|
Промышленные катализаторы риформинга.
В промышленности применяются следующие катализаторы: платиновые (носители— окись алюминия, промотированная фтором или хлором, алюмосиликат, цеолит и др.); палладиевые (носители те же, что и для платины); сернистый вольфрамоникелевый; окисный алюмомолиб-деновый (~ 10% окиси молибдена на окиси алюминия); алюмо-хромовый (32% окиси хрома и 68% окиси алюминия); алюмо-кобальтмолибденовый (молибдат кобальта на носителе — окиси алюминия, стабилизированной кремнеземом). Наиболее широкое применение нашли алюмоплатиновые катализаторы. В последнее время в состав катализаторов с платиной и палладием стали вводить редкоземельные элементы. Некоторое распространение получили также цеолитсодержащие катализаторы. Цеолитсодержащие катализаторы ( цеолитные катализаторы), гетерогенные многофазные катализаторы на основе цеолитов. Цеолиты - минералы из группы водных алюмосиликатов щелочных и щелочноземельных элементов с тетраэдрическим структурным каркасом, включающим полости (пустоты), занятые катионами и молекулами воды.
Активность и стабильность цеолитсодержащих катализаторов определяется главным образом соотношением атомов Si/Al в кристаллическом каркасе цеолита, размерами и строением полостей и каналов цеолита и матрицы, а также наличием в цеолите или матрице катионов, отличных от щелочных и щел.-зем. Различают моно- и бифункциональные цеолитсодержащие катализаторы. Монофункциональные катализаторы содержат кислотные бренстедовские (протоны, связанные с каркасными атомами О) и льюисовские центры (катионы щелочных металлов или трех-координир. атомы А1, находящиеся в местах с дефицитом кислорода или местах расположения катионов):
Каталитическое действие таких цеолитсодержащих катализаторов связано с их способностью образовывать карбониевые ионы, поэтому они способны ускорять реакции крекинга, изомеризации и диспропорционирования алкилароматических углеводородов, переноса водорода и др.
Бифункциональные цеолитсодержащие катализаторы помимо кислотных центров содержат катионы металлов VI и VIII групп, заряд которых компенсирует избыточный отрицательный заряд в каркасе цеолита. Наличие таких катионов определяет способность цеолитсодержащих катализаторов ускорять окислительно-восстановительные реакции. В связи с этим на бифункциональных цеолитсодержащих катализаторах протекают два типа реакций: на кислотных центрах происходят реакции, характерные для монофункциональных катализаторов; на катионах металлов - реакции гидрирования - дегидрирования (напр., гидрогенолиз, гидрокрекинг, синтез углеводородов из метанола). Направление и селективность реакций определяются соотношением кол-ва кислотных центров и кол-вом введенного в катализатор катиона металла
Полиметаллические катализаторы каталитического риформинга серии КР
Третий этап развития процесса каталитического риформинга связан с применением высокостабильных полиметаллических катализаторов серии КР.
Использование полиметаллических катализаторов требует глубокой очистки сырья от серы и других каталитических ядов, применения особых приемов вывода катализаторов на режим, связанных с их восстановлением и осернением, поддержания оптимального содержания хлора в катализаторах в цикле реакции. Большое значение приобретают способы быстрого хлорирования катализаторов в пусковой период. Регенерация полиметаллических катализаторов включает стадию оксихлорирования, необходимую для редиспергирования металлической фазы и доведения содержания хлора в катализаторе до требуемого уровня. В связи с высокой коррозионной активностью продуктов регенерации используют разные методы защиты конденсационно-холодильного оборудования блоков риформинга с применением ингибитора коррозии и щелочных растворов [262].
При переводе действующих установок риформинга на полиметаллические катализаторы серии КР технико-экономические показатели их работы повышаются, чему способствует ряд факторов. Стоимость полиметаллических катализаторов ниже стоимости монометаллических вследствие более низкого содержания платины. Высокая стабильность полиметаллических катализаторов обеспечивает более длительный межрегенерационный период их работы, в частности в жестких условиях процесса; она позволяет также осуществлять процесс при более низких давлениях, не опасаясь быстрого закоксовывания катализатора, что обеспечивает увеличение выходов целевых продуктов реакции (бензина риформинга, ароматических углеводородов, водорода) (см. 2, 5). Селективность полиметаллических катализаторов, вследствие высокой их стабильности, снижается значительно медленнее, чем селективность катализаторов монометаллических. Поэтому выход целевых продуктов риформинга за весь реакционный период выше при работе на полиметаллических катализаторах. Высокая стабильность полиметаллических катализаторов и хорошая регенерационная способность обеспечивают большие сроки их службы. Так, максимальная удельная производительность катализаторов на установках типа 35-6 и 35-8 составила (в т. сырья на кг катализатора) [255]:
АП-56
42
АП-64
58
КР-104
90
Эксплуатация в течение пяти лет полиметаллического катализатора КР-104, с периодической его регенерацией, показала, что активность его не снизилась, подтверждением чему служат среднегодовые октановые числа (м. м.) риформатов:
1 год
2 года
3 года
4 года
5 лет
ЛЧ-35-11/600 (Кириши)
83,1
84,1
84,9
84,3
85,3
ЛЧ-35-11/600 (Горький)
84,4
83,9
85,1
84,6
83,9
Л-35-11/1000 (Уфа)
80,1
81,3
81,9
82,1
82,7
Такой срок службы — не предел для полиметаллических катализаторов, он может быть значительно увеличен . Преимущества полиметаллических катализаторов не могут быть использованы в полной мере на действующих установках. Так, возможности снижения рабочего давления при неизменной производительности по сырью ограничены: давление на. установках типа 35-6 и 35-8 может быть снижено от 2,0 до 1,5 МПа, а на установках типа 35-11 — от 3,0—3,5 до 2,5—2,8 МПа [263 ]. Снижение давления лимитируется производительностью циркуляционных компрессоров. Однако и в этих условиях применение полиметаллических катализаторов дает значительный эффект. Так, согласно среднестатистическим данным за 1982 г. октановое число бензина риформинга на 4 выше, выход ароматических углеводородов (бензола и толуола) был на 14% больше при работе на катализаторах типа КР в сравнении с полученными при риформинге на монометаллических катализаторах АП-56 и АП-64
29.
Основным фактором, влияющим на качество получаемых на установках каталитического риформинга продуктов, является температура в реакторах блоков риформинга и гидроочистки.
Регулирование заданной температуры на входе в реакторы осуществляется автоматически путем изменения подачи отопительного газа или мазута к форсункам соответствующих секций реакторной печи риформинга и к форсункам печи гидроочистки.
Температурный режим в реакторах по высоте и по сечению (по слоям катализатора) контролируется многозонными термопарами. Температура корпуса реакторов контролируется поверхностными термопарами.
Сопротивление по реакторам определяется дифманометром по перепаду давления.
Для обеспечения нормального режима нагрева продуктов в печах и нормального горения топлива предусмотрены соответствующие контрольно-измерительные приборы и автоматическое регулирование.
Температура газосырьевой смеси замеряется на входе в конвекционные камеры после теплообменников, на перекидках из конвекционных камер в радиантные камеры гидроочистки и первой ступени риформннга, в параллельных коллекторах на выходе каждой камеры риформинга, на входе и выходе из реакторов.
При повышении температуры перед реактором гидроочистки выше 420 °С, а перед реакторами риформинга выше 530 °С предусмотрена сигнализация.
Регулирование этих температур осуществляется автоматически путем изменения подачи топливного газа к горелкам печей с помощью клапанов, установленных перед камерами каждой ступени нагрева.
Температура продуктов сгорания (дымовых газов) контролируется с помощью термопар, установленных на выходе из радиантных камер, на перевалах, на выходе из конвекционных камер.
В этих же местах контролируется и разрежение дымовых газов. По падению разрежения перед дымососом включаются автоматические блокировки.
Постоянное давление топлива (топливного газа и мазута) поддерживается автоматически регулятором давления.
Температура нагрева топлива в подогревателях мазута и топливного газа регулируется клапанами, установленными на линии подачи пара к подогревателям.
Процесс горения топлива в печах регулируется подачей воздуха на горение в каждую горелку по величине и цвету факела. Процесс горения топлива контролируется автоматическими газоанализаторами по содержанию окиси углерода и кислорода в дымовых газах.
Для налаживания работы горелок на трубопроводах подачи мазута, газа и пара к горелкам перед входом устанавливаются манометры.
Регулирование давления в блоке риформннга осуществляется с помощью клапана, установленного на линии подачи избыточного водородсодержащего газа в блок гидроочистки. Давление в блоке гидроочистки регулируется с помощью клапана, установленного на отдуве водородсодержащего газа из сепаратора гидроочистки.
Для поддержания режима в отпарной колонне следует подавать в колонну определенное количество орошения, контролировать и регулировать температуру на входе сырья в колонну, уровень жидкости, температуру и давление в нижней части колонны.
Давление в колонне поддерживается регулирующим клапаном, установленным на отдуве углеводородного газа из емкости орошения.
Температура низа колонны автоматически регулируется клапаном, установленным на греющем агенте, подаваемом в кипятильник колонны.
Если для нагрева горячей струи используется печь, то температура продукта на выходе из печи регулируется с помощью клапана, установленного на подаче газообразного или жидкого топлива в печь.
Уровень в колонне поддерживается клапаном, установленным на нагнетательном трубопроводе насоса, который откачивает нижний продукт из колонны.
Для поддержания режима в стабилизационной колонне необходимо контролировать и регулировать температуру, давление и уровень жидкости в нижней части колонны, подавать определенное количество орошения, причем основным регулируемым параметром является расход орошения, а заданным — расход питания.
Давление в стабилизационной колонне поддерживается регулирующим клапаном, установленным на шлемовой линии.
Давление в емкости орошения поддерживается регулирующим клапаном, установленным на выходе паров из емкости орошения. Раздельное регулирование давления в колонне и в рефлюксной емкости обеспечивает работу конденсатора-холодильника в постоянных условиях и равномерное поступление конденсата в емкость орошения.
Температура питания регулируется подачей теплоносителя в подогреватель питания колонны.
Температура, давление и уровень жидкости, температура и давление в нижней части колонны регулируется и контролируется.
Автоматическое регулирование процесса ректификации затрудняется из-за большого количества взаимосвязанных переменных, влияющих на процесс разделения, а также из-за значительной емкости и инерционности объекта регулирования.
Ректификационная колонна имеет большое число тарелок.
Всякое изменение рабочих условий распространяется от тарелки
" тарелке, новое равновесное состояние достигается постепенно.
В зависимости от аппаратурного решения технологической схемы и от конкретных условий проведения процесса разделения принимаются различные схемы регулирования давления в ректификационных колоннах.
Давление регулируется воздействием на регулирующий клапан, установленный на шлемовой линии, если температура верха невысокая и для получения удовлетворительного качества продуктов разделения требуется минимальное запаздывание в этом, контуре регулирования.
Наиболее распространенным способом регулирования давления в колонне является байпасирование горячего газа мимо конденсатора-холодильника. При этом горячий газ поступает непосредственно в рефлюксную емкость либо в емкость после конденсатора-холодильника.
Система автоматического контроля и регулирования в ректификационных колоннах с полной конденсацией дистиллята заключается в поддержании постоянного перепада давления между колонной и рефлюксной емкостью воздействием на регулирующий клапан, установленный на перепуске паров мимо конденсаторов-холодильников.
Основным условием, обеспечивающим получение продуктов аданного качества, является поддержание определенного теплового баланса колонны.
Тепловой баланс колонны складывается из теплоты, подводимой в колонну с сырьем, с парами, поступающими из рибойлера, и теплоты, снимаемой в верху колонны холодным орошением, а также теплоты, отводимой из колонны с дистиллятом и остатком.
Параметром, характеризующим качество поддержания заданного теплового баланса, является температура.
Применяются различные варианты регулирования температуры сырья, поступающего в колонну. От стабильности этого теплового потока во многом зависит устойчивая работа колонны в целом. Используются различные варианты регулирования температуры сырья, поступающего в колонну.
Наиболее часто применяется прямая схема регулирования подачи греющего пара в подогреватель сырья по температуре сырья на выходе из подогревателя, а также каскадная схема, когда регулятор температуры сырья на выходе из подогревателя корректирует регулятор расхода греющего пара.
Используется также схема регулирования температуры сырья изменением поверхности нагрева. Установленный на выходе конденсата пэра клапан прикрывается, трубки теплообмепного аппарата заполняются жидкостью, что уменьшает поверхность нагрева.
Основной составляющей теплового баланса колонны является теплота, подводимая с парами из рибойлера, Температура этих паров, как и температура в зоне подачи питания или на контрольной тарелке колонны, определяющая качество поддержания теплового баланса колонны, регулируется воздействием на подачу водяного пара в рибойлер.
Если для нагрева сырья используется печь, то регулятор температуры па выходе горячей струи из печи воздействует на подачу газообразного или жидкого топлива.
В зависимости от конструкции колонны, условий проведения процесса разделения, качества получаемых продуктов выбирается схема воздействия на подачу пэра в рибойлер.
Наиболее распространены схемы воздействия регулятора температуры в зоне питания или на контрольной тарелке.
Подвод орошения в колонну осуществляется либо по расходу, либо по температуре паров наверху или на контрольной тарелке.
Однако не рекомендуется применять схемы с одновременным регулированием температуры верха (воздействием на расход орошения) и температуры низа колонны (воздействием на расход тепло'юеителя в рибойлер), так как это может нарушить процесс разделения.
На установках применяются пневматические приборы типа «Старт», а также используется электрическая унифицированная система приборов.
Температура регулируется многоточечными потенциометрами типа КСП-2И с искробезопасными входными цепями.
Для измерения и регулирования температуры применяются термопары с нормирующими преобразователями с искробезопасными выходными цепями типа НП-ТЛ-11 и электропреобразователями ЭПП-63.
В качестве измерителей уровня используются приборы буйкового типа наружного монтажа.
Все аппараты оснащены магнитными указателями уровня, что увеличивает надежность визуального наблюдения за уровнем в аппаратах.
Дата добавления: 2018-08-06; просмотров: 738; Мы поможем в написании вашей работы! |
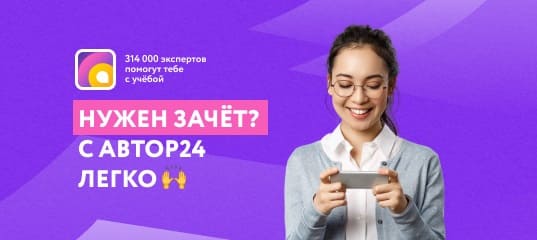
Мы поможем в написании ваших работ!