Характеристики надежности оборудования электроподвижного состава промышленного транспорта
Общие сведения.Высокая оперативность работы транспортной цепи открытых горных разработок, внедрение новых инженерных решений при конструировании и высокая стоимость содержания тяговых агрегатов ставят одним из основных вопрос повышения характеристик надежности их основного оборудования. В связи с усовершенствованием конструкции подвижного состава, применением современных высокоэффективных материалов следовало бы ожидать снижения числа отказов, увеличения межремонтных пробегов, однако исследования показали, что сложность оборудования подвижного состава и интенсивность его использования в ряде случаев опережают рост надежности применяемых элементов.
Улучшение технических характеристик новых типов электроподвижного состава не всегда сопровождается повышением их надежности при значительном возрастании стоимости. Как показала практика эксплуатации, электроподвижной состав имеет ряд узлов с низкой надежностью, и основной задачей следует считать не только определение фактических значений характеристик надежности, но и их нормирование.
Таким образом, исследование характеристик надежности производится с целью выдачи обоснованных рекомендаций конструкторам для прогнозирования надежности новых систем на стадии проектирования, разработки эффективных технологических процессов восстановления деталей и узлов с нормированными значениями этих характеристик. Полученные численные значения характеристик надежности дают возможность при проектировании заложить, в изготовлении обеспечить и в эксплуатации поддержать экономически оптимальные показатели надежности.
|
|
Одним из основных понятий, определяющих состояние объекта, является отказ — событие, заключающееся в нарушении работоспособности локомотива, имеющее любое из следующих последствий:
· невыполнение показателей (веса поезда, времени хода, скорости движения); нарушение графика движения из-за восстановления работоспособности локомотива в пути следования; неплановый ремонт;
· досрочная замена или регулировка оборудования;
· повышенный объем работ по отношению к регламентированным на плановом ремонте.
Тяговый агрегат представляет собой сложную систему, состоящую из большого числа элементов. Отказ элемента — это событие, заключающееся в нарушении хотя бы одного из его параметров, границы которого определены указаниями технической документации.
По своему характеру отказы распределяются на две основные группы: внезапные и параметрические. Внезапный отказ характеризуется резким изменением одного или нескольких параметров элемента (пробой изоляции, появление трещин и разрушение деталей, перекрытие изоляционной поверхности электрической дугой и т. п.). Однако такие отказы не наступают вдруг, их появлению предшествуют медленно протекающие скрытые физические процессы (старение изоляции, накопление усталостных изменений структуры металла, изменение количественного и качественного характера загрязнений изоляционной поверхности и т. п.). Таким образом, внезапность отказа определяется технической возможностью контроля за ходом процесса, поэтому мероприятия планово-предупредительной системы ремонта далеко не всегда достигают цели.
|
|
Борьба с появлением внезапных отказов должна проводиться в двух направлениях: профилактикой и торможением скрытых процессов разрушения. Наряду с этим следует заниматься изучением закона распределения вероятностей безотказной работы и параметра потока отказов. В первом случае эффективными мерами могут быть: соблюдение эксплуатационных режимов (нагрузка, скорость, частота колебаний, температура), повышение устойчивости металла к усталостным явлениям, замена существующих материалов более эффективными и т. п.
Знание закона распределения вероятностей безотказной работы элемента, анализ параметра потока отказов позволяют прогнозировать границы наработки элемента, когда вероятность отказа наибольшая. Параметрический отказ определяется как момент наступления предельного состояния элемента вследствие изменения свойств, форм и размеров деталей (износ, старение), ухудшения производительности агрегата, изменения регулировочных характеристик аппаратов, ухудшения параметров полупроводниковых вентилей и т. п. Прогнозирование ухудшения параметров узлов (агрегатов) производится методами параметрической надежности машин.
|
|
В соответствии с принятыми понятиями отказ элемента влечет за собой и отказ системы, например тягового агрегата. Так как основной задачей, возложенной на тяговый агрегат, является вывозка определенного объема горной массы в смену, в качестве основного критерия отказа следует считать время простоя тягового агрегата для восстановления его работоспособности.
Однако время устранения отказа колеблется в широких пределах, большое значение имеет место и время вынужденной стоянки локомотиво-состава. Поэтому условно считают, что если остановка не вызвала сбоя в работе транспортной цепи, а отказ был устранен силами локомотивной бригады подручными средствами за время, не вызвавшее снижения производительности, — отказа не произошло. В табл. 2 представлены данные об отказах основного оборудования электровозов и тяговых агрегатов в процентах от общего их числа на локомотиве.
|
|
Из анализа данных табл. 2 видно, что наименее устойчиво работают электрические аппараты. Характерные повреждения: повышенный износ контактов, обрыв гибких проводов (шунтов), износ шарниров подвижной системы, нарушение тока уставки реле, аппаратов защиты и т. п. Отказы элементов механической части: разрывы бандажей колесных пар, изломы рессорных листов и подвесок, интенсивный износ деталей ударно-сцепных устройств и их разрушение, износ сопряжений межтележечных сочленений, неисправности редукторов тягового привода, разрушение резинометаллических блоков буксовых тяг.
Отказы тяговых двигателей возникают главным образом из-за разрушений выводов обмоток возбуждения, соединений межкатушечного монтажа, пробоя витковой и корпусной изоляции обмоток якоря и возбуждения, сползания шестерен. Основным видом отказа пневматического и тормозного оборудования являются пропуск воздуха клапанами, манжетами, соединениями, повреждения клапанных коробок компрессоров, резкое повышение температуры их цилиндров, износ колец. Выпрямительные установки отказывают из-за пробоя полупроводникового слоя, ухудшения характеристик.
Причинами отказов оборудования тяговых агрегатов являются: неудовлетворительная конструкция (К), некачественное изготовление (И), нарушение режима эксплуатации (Э),
Таблица 2
Наименование оборудования | Отказы т. п. с, % | |||||||
EL1 | 26Е | Д100 | ПЭ2М | ОПЭ1 | ОПЭ1А | ОПЭ2 | ELI0 | |
Механическое | 21 | 22 | 23 | 31 | 15 | 25 | 30 | 14 |
Тяговые двигатели | 27 | 21 | 7 | 6 | 2 | 2 | 1,5 | 24 |
Вспомогательные машины | 10 | 11 | 19 | 3 | 4 | 2 | 1,1 | 13 |
Электрические аппараты силовой цепи | 21 | 24 | 19 | 24 | 10 | 22 | 26 | 20 |
Электрические аппараты вспомогательных цепей и защиты | 17 | 12 | 18 | 23 | 6 | 15 | 19 | 17 |
Пневматическое и тормозное оборудование | 4 | 10 | 7 | 13 | 9 | 15 | 16 | |
Выпрямительная установка | 5 | 5 | 7 | 1 | ||||
Дизель-генераторная установка | 22 | 20 | 4 | |||||
Тяговый трансформатор | - | 2 | 1 |
некачественный ремонт (Р). Статистические данные причин и числа отказов применительно к тяговому агрегату ОПЭ2 за 3 года эксплуатации представлены в табл. 3.
Таблица 3
Наименование оборудования | Число отказов по причинам | |||
К | И | Э | Р | |
Механическое | 4 | - | 7 | 31 |
Электрические машины | 1 | 4 | 3 | 27 |
Электрические аппараты силовой цепи | 26 | 16 | 10 | 12 |
Электрические аппараты вспомогательных цепей и защиты | 4 | 1 | — | 4 |
Пневматическое | — | — | 2 | 13 |
Таким образом, причиной большего числа отказов является неудовлетворительное качество ремонта и нарушение режима эксплуатации подвижного состава. Так, неудовлетворительное содержание автосцепных устройств, нарушения режима восстановления корпуса автосцепки и деталей шарнирного узла вызывают их интенсивный износ и разрушения. Попытки восстановить гребни бандажей колесных пар наплавкой без выкатки из-под локомотива приводят к образованию трещин и последующему их разрыву. На основании анализа отказов оборудования т. п.с. можно выявить узлы и детали, неудовлетворительно работающие в эксплуатации, установить причины. Это позволяет определить основные направления при конструировании нового подвижного состава и назначить такие технологические процессы восстановления, которые обеспечили бы повышение эксплуатационной надежности.
Литература
1. Н. С. Конарев «Железнодорожный транспорт. Энциклопедия», 1995
2. А. С. Бакулин «Сооружения, устройства и подвижной состав метрополитена», 1979
3. Петропавлов Ю.П. Технология ремонта электроподвижного состава: Учебник для техникумов и колледжей железнодорожного транспорта – М.: Маршрут, 2006.
4. Распоряжение ОАО «РЖД» № 3р «О системе технического обслуживания и ремонта локомотивов» от 17 января 2005
Дата добавления: 2018-08-06; просмотров: 398; Мы поможем в написании вашей работы! |
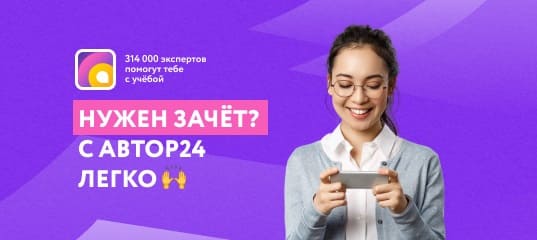
Мы поможем в написании ваших работ!