Методика построения рациональной системы содержания электроподвижного состава промышленного транспорта
ФЕДЕРАЛЬНОЕ АГЕНТСТВО ЖЕЛЕЗНОДОРОЖНОГО ТРАНСПОРТА
федеральное государственное бюджетное образовательное учреждение
высшего образования
«Омский государственный университет путей сообщения»
(ОмГУПС (ОмИИТ))
Кафедра «Подвижной состав электрических железных дорог»
ОТЧЕТ
по учебной практике
(вид практики)
практике по получению первичных профессиональных умений и навыков, в том числе первичных умений и навыков научно-исследовательской деятельности
(тип практики)
ИНМВ. 700001.000
Место прохождения практики:
__________Южно-Уральская. ж.д., ТЧ-12 Петропавловск__________________
Студент гр.47-д
___________ В.О.Иванов
«___»___________2018г.
СОГЛАСОВАНО:
Руководитель практики Руководитель практики
от профильной организации от университета –
__________ _______________ доцент кафедры ЭПС
(подпись) (расшифровка подписи)
___________ E.А. Третьяков
|
|
«___»___________201_г.
Омск 2018
Содержание
Система технического обслуживания и текущего ремонта электроподвижного состава промышленного транспорта. 3
Методика построения рациональной системы содержания электроподвижного состава промышленного транспорта. 5
Структура ремонтного цикла и принцип определения периодичности ремонтов электроподвижного состава промышленного транспорта. 7
Дифференцирование норм межремонтных пробегов электроподвижного состава промышленного транспорта 9
Подготовка т. п. с. и ремонтной базы к внедрению новой системы содержания электроподвижного состава промышленного транспорта. 10
Назначение технических обслуживании, текущих и заводских ремонтов электроподвижного состава промышленного транспорта. 13
Технология и организация ремонта электроподвижного состава промышленного транспорта. 17
|
|
Организация выполнения текущих ремонтов электроподвижного состава промышленного транспорта 24
Эффективность сокращения простоя локомотивов в ремонте. 27
Организация ремонта по сетевому графику электроподвижного состава промышленного транспорта 28
Характеристики надежности оборудования электроподвижного состава промышленного транспорта 29
Литература. 34
Техническое обслуживание и текущий ремонт электроподвижного состава в ТЧ-12 Петропавловск
Система технического обслуживания и текущего ремонта электроподвижного состава промышленного транспорта
Общие сведения. Повышение надежности тягового подвижного состава (т. п. с), снижение стоимости его содержания может быть достигнуто только при оптимальной системе технического обслуживания и текущего ремонта. Эта система представляет собой комплекс взаимосвязанных мероприятий, положений и норм, определяющих организацию производства и порядок выполнения работ при технических обслуживаниях и текущих ремонтах тягового подвижного состава для заданных условий эксплуатации с целью улучшения его технического состояния, повышения эксплуатационной надежности и снижения продолжительности ремонта. Системой определяются условия изъятия тягового подвижного состава из эксплуатации для восстановления его работоспособности, виды обслуживания и ремонтов, структура ремонтного цикла, периодичность технического обслуживания и текущих ремонтов. Тяговый подвижной состав изымают из эксплуатации либо для проведения планово-предупредительного ремонта, либо для ремонта по фактическому состоянию. Для т. п. с. принята система планово-предупредительного ремонта, обладающая рядом преимуществ. При такой системе представляется возможность составлять перспективные планы ремонта т. п. с, определять потребность в ремонтной базе и технологическом оборудовании, материально-техническом обеспечении, рабочей силе, энергии и т. д. Назначение системы — проведение профилактических мероприятий (осмотров, испытаний, ревизий) с целью предупреждения случайных отказов в эксплуатации.
|
|
В ремонт по фактическому состоянию оборудование поступает в результате потери работоспособности, что регламентируется соответствующей технической документацией. Такой ремонт квалифицируется как неплановый. Ремонту по фактическому состоянию оборудование подвергается также на плановых видах технического обслуживания и текущих ремонтов независимо от номенклатуры регламентных работ. В этом случае ремонт квалифицируется как сверхобъемный. Основными причинами появления неплановых ремонтов являются низкий уровень надежности отдельных узлов, недостаточность средств диагностики, неприспособленность т. п. с. к диагностированию, нарушения, допускаемые в эксплуатации.
|
|
Наиболее эффективной, отвечающей поставленным требованиям, следует считать планово-предупредительную систему, предусматривающую проведение следующих работ:
· техническое обслуживание — наиболее полно обеспечивающее безопасность движения поездов;
· текущие ремонты, объем работы на которых определяется не заранее составленным перечнем, а фактическим состоянием оборудования на основе объективной оценки средствами технической диагностики. Эти средства должны быть настолько совершенными, чтобы устанавливать не только факт отказа, но и фиксировать предотказовое состояние оборудования.
Существующая система содержания построена на основании анализа опытно-статистических данных об отказах оборудования магистрального т. п. с. Данные о зафиксированных отказах обрабатываются методами математической статистики, и на основании полученных результатов делаются выводы о возможности изменения цикличности и периодичности технических обслуживании и текущих ремонтов. Обязательный объем профилактических работ регламентируется указаниями Правил ремонта. Ремонту по фактическому состоянию подвергаются только детали и узлы с отмеченными дефектами. Однако эта система имеет ряд существенных недостатков. Увеличение объема профилактических работ в начальный период эксплуатации приводит к повышению числа внезапных отказов. Система недостаточно полно учитывает разность износов деталей одного и того же локомотива, что приводит к значительным потерям из-за недоиспользования их ресурсов. Такой метод малоэффективен.
Дальнейшая корректировка системы может быть произведена только после накопления необходимого объема статистических данных, что неизбежно связано со значительной потерей времени и средств. Подобные разработки необходимо осуществлять на научной основе, используя математический аппарат теории вероятностей, массового обслуживания, линейного программирования.
Предварительно необходимо сформулировать основные требования, предъявляемые к системе. Система должна:
· носить планово-предупредительный профилактический характер, обоснованный технико-экономической целесообразностью;
· предусматривать своевременное устранение износа оборудования и снижение доступными средствами контроля вероятности появления внезапных отказов;
· обеспечивать поддержание на заданном уровне характеристик надежности основного оборудования и локомотива в целом, а также неуклонное снижение расходов на содержание т. п. с. и плановое повышение производительности труда на основе научной организации труда;
· предусматривать такой объем регламентных работ на плановых видах ремонтов, который наиболее полно обеспечивал бы использование технического ресурса деталей; обладать свойствами адаптации к изменяющейся производственной и эксплуатационной обстановке.
Методика построения рациональной системы содержания электроподвижного состава промышленного транспорта
Для получения исходных данных предварительно устанавливают нормы предельного состояния деталей и узлов, ограничивающих межремонтные пробеги, и определяют их технический ресурс; составляют карту средних значений ресурсов деталей по видам оборудования; регистрируют внезапные отказы, производят анализ причин их возникновения, определяют закон распределения отказов, наработку на отказ и стоимость устранения отказов.
Аналитическое решение задачи дает возможность предложить метод восстановления, обеспечивающий наименьшие затраты при заданном уровне безотказности за установленную наработку. Локомотив рассматривается как сложная восстанавливаемая система, условно разбитая на элементы таким образом, что отказ любого из них приводит к отказу всей системы. При этом предполагаются следующие допущения:
· элементы системы являются полностью работоспособными до наступления отказа, затем они становятся неработоспособными и требуется их восстановление
· (замена);
· степень восстановления элемента на идентичных видах ремонта постоянна;
· время между смежными отказами — случайная величина и ее закон распределения известен;
· виды замены отказавших элементов: неплановый — после наступления отказа,
· плановый — в заранее определенный момент времени;
· элемент, отказ которого наступает по нескольким независимым причинам, можно рассматривать как несколько различных элементов, и для каждой причины отказа следует определить закон распределения вероятности безотказной работы.
Ниже приводится методика расчета периодичности ремонта карьерных локомотивов, разработанная Днепропетровским институтом инженеров железнодорожного транспорта им. М. И. Калинина. Методика принята для использования на горно-обогатительных комбинатах (ГОК) МЧМ СССР. Так как число отказов Ni — случайная величина, определяется его математическое ожидание: Hi(x) = M [Ni(x)].
Здесь функция восстановления
(1)
где Fi(х) — функция распределения вероятности безотказной работы i-го элемента, которая определяется на основании полученных статистических данных об отказах: 0 ≤ Fi(x) ≤ 1; dFi (у) — дифференциал функции Fi(у), а у — переменная дифференцирования.
Примем, что сi и qi — стоимости устранения отказа соответственно на планово-предупредительном и неплановом ремонтах. Предположим, что сi < qi . В противном случае введение системы планово-предупредительных ремонтов для i-гo элемента не имеет смысла. Пусть x0i — оптимальная периодичность ремонта i-гo элемента. Тогда затраты на ремонт i-гo элемента за период x0i
(2)
Наименьшие приведенные затраты на единицу наработки
Решение задачи сводится к определению х0i для каждого i-гo элемента. Таким образом, оптимальная периодичность восстановления должна удовлетворять уравнению
(3)
Значение yi(x) должно быть наименьшим. Тогда производная
или
(4)
откуда (5)
Для решения уравнения (5) необходимо определить функции Hi(x) и H’i(x). Однако для большинства функций распределения вероятностей безотказной работы уравнение (1) не решается в элементарных функциях и Hi(х) нельзя определить аналитически. Поэтому Hi(х) определяют в точках x1,x2, ..., хn экспериментально на основании статистических данных.
Если известна функция распределения вероятностей отказов Fi(x), процесс моделирования работы элемента заключается в следующем. Выбирают последовательно случайные числа xk, распределенные равномерно на интервале от нуля до единицы. Каждому числу соответствует наработка на отказ хк в соответствии с законом распределения xk = Fi (xk). Таким образом получают достаточное число значений хк для определения Н(хк). Для каждого элемента задают наибольшее допустимое число отказов H0i между плановыми ремонтами исходя из условий эксплуатации и характера работы элементов. Последовательно определяют значения Hi(xk)n (здйсь n = 1, 2, ...); выбирают значение наименьших приведенных затрат yi (х) при условии Hi (хк) ≤ H0i. Наработка х0i, соответствующая наименьшим приведенным затратам, и является оптимальной периодичностью восстановления i-гo элемента.
По приведенной методике составляют программу расчетов для реализации на ЭВМ и производят расчет оптимальной периодичности восстановления для элементов, лимитирующих межремонтный пробег, с учетом данных таблицы (карты) ресурсов деталей.
Дата добавления: 2018-08-06; просмотров: 372; Мы поможем в написании вашей работы! |
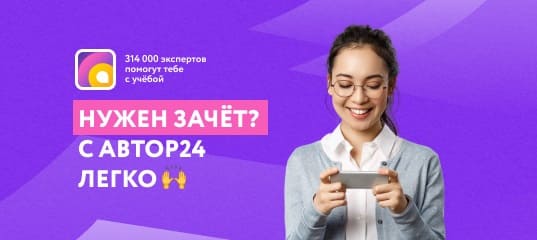
Мы поможем в написании ваших работ!