Правила техобслуживания дизельных двигателей.
обслуживание судового дизельного двигателя при нормальной эксплуатации
Если достигнут аварийный предел и срабатывает сигнализация, то состояние двигателя уже серьезное. Необходимо предпринять все возможные меры для того, чтобы устранить аварийную ситуацию и вернуть двигатель в нормальное рабочее состояние. Поскольку неправильная работа двигателя может привести к повреждениям, следует приложить все усилия, чтобы восстановить нормальную работу, а не ждать автоматического отключения двигателя.
Через день либо через каждые 50 часов работы считать показания всех указателей температуры и давления, а также нагрузки двигателя, и сравнить полученные показания с соответствующими значениями нагрузки и оборотов в протоколе приемосдаточных испытаний и графиками:
- если разница между значениями температуры выхлопных газов на разных цилиндрах больше 70° C при нагрузке выше 25%, следует установить причину этого;
- температура нагнетаемого воздуха, в принципе, должна быть по возможности низкой при нагрузке выше 80%. Однако не настолько низкой, чтобы происходила конденсация. При нагрузке ниже 25% рекомендуется обеспечивать температуру нагнетаемого воздуха по возможности высокой;
- проверить индикатор перепада давления на топливных фильтрах, если он установлен. Если перепад давления на топливных фильтрах возрастает, давление в системе падает. Слишком низкое давление (ниже 0.5 бар) снижает мощность судового двигателя и может вызывать неравномерность распределения нагрузки между цилиндрами (опасность поломки!). Слишком высокий перепад давления может также привести к деформации фильтрующих элементов (опасность заклинивания инжекторных насосов);
|
|
- проверить перепад давления на масляных фильтрах. Слишком большой перепад указывает на засорение фильтрующих элементов. Уменьшение фильтрования масла вызывает повышенный износ. Прочистить фильтры и, если это не помогает, заменить фильтрующие элементы;
- проверить уровень масла в картере/масляном баке. Оценить внешний вид и консистенцию масла.
Простая проверка содержания воды: капнуть маслом на горячую поверхность (около 150° C), например, на горячую пластину. Если капля ведет себя «спокойно», в ней нет воды:
- если она «шипит» - в ней есть вода. Восполнить расход масла добавлением не более 10% свежего масла за один прием;
- убедиться в том, что удаляется воздух из системы циркуляции воды двигателя (расширительного бака). Убедиться в отсутствии чрезмерного подтекания из контрольного отверстия циркуляционных водяных насосов;
- проверить количество вытекающего топлива из дренажных труб;
|
|
- проверить, чтобы дренажные трубы воздухоохладителей были открыты;
- проверить, чтобы контрольные отверстия маслоохладителей и холодильников циркулирующей воды были открыты;
- слить из расходного бака воду и осадок, при наличии, и слить водоотстойник пускового воздуха;
- на остановленном судовом двигателе выполнить предварительную смазку и повернуть коленчатый вал в другое положение. Таким образом, снижается опасность повреждения коленчатого вала и подшипников под воздействием вибрации;
- содержать рейки инжекторного насоса в чистоте (очищать от липких отложений), проверить, чтобы детали системы управления подачей топлива перемещались свободно. Это должно выполняться на остановленном двигателе;
- очистить турбинную сторону турбонагнетателя посредством впрыскивания воды.
Один раз в месяц либо через каждые 500 часов работы проверить содержание присадок в циркулирующей охлаждающей жидкости и проверить давление на цилиндрах. Одновременно с этим обратить внимание на нагрузку двигателя (положением индикатора нагрузки на рейках инжекторных насосов точно указывается нагрузка двигателя). Проверить работу системы охлаждения.
контроль за работой судового двигателя
|
|
Не существует никакой аппаратуры автоматического наблюдения или контроля, которая смогла бы заменить наблюдения и контроль, выполняемые опытным инженером.
НАБЛЮДАЙТЕ и ПРОСЛУШИВАЙТЕ судовой двигатель!
Сильный прорыв газа через поршни - это наиболее опасное событие, которое может произойти на дизельном двигателе. Если предполагается прорыв газа (например, по внезапному росту расхода смазочного масла), проверить давление в картере. Если давление превышает 45 мм водяного столба, проверить систему вентиляции картера, если она в порядке, извлечь поршни.
Работа при нагрузке ниже 20% номинальной мощности при использовании тяжелого топлива должна ограничиваться максимум 100 часами путем повышения нагрузки свыше 70% номинального значения на один час перед тем, как продолжить работу при низкой нагрузке или остановить двигатель. Непрерывная работа на судовом дизельном топливе при нагрузке ниже 10% номинальной мощности должна ограничиваться максимум 100 часами путем повышения нагрузки свыше 70% номинального значения на один час перед тем, как продолжить работу при низкой нагрузке или остановить двигатель. Работа судового дизеля на холостом ходу (выключено сцепление главного двигателя, отключен генераторный агрегат) должна быть строго ограничена.
|
|
Ремонт дизельных двигателей.
В зависимости от производственных возможностей предприятия и конструктивных особенностей двигателя ремонт его может осуществляться на судне или в цехе. Как правило, при капитальном ремонте двигатель демонтируют (снимают с судового фундамента) и доставляют в цех для ремонта. Крупногабаритные дизели большой массы с фундамента не снимают, а демонтируют отдельными узлами.
Ремонт двигателя в цехе сокращает сроки ремонта, однако последующие работы на судне по монтажу и центровке двигателя могут быть весьма трудоемкими, поэтому необходимость демонтажа в каждом отдельном случае должна быть обоснована.
При капитальном ремонте двигателя в цехе основными этапами являются: разборка; дефектация (выявление износов и повреждений); восстановление деталей; изготовление новых деталей взамен забракованных; узловая сборка; общая сборка двигателя; испытание в цехе; монтаж на судовом фундаменте; испытание на судне.
Демонтажные работы начинают с отсоединения от двигателя всех трубопроводов, предварительно удалив из них и из двигателя воду, масло и топливо; затем снимают с двигателя контрольно-измерительные приборы, арматуру; все отверстия закрывают заглушками. Одновременно ведут работы по разборке площадок, приводов к арматуре и других частей, соединяющих двигатель с конструкциями корпуса судна. Затем разъединяют фланцы коленчатого и приводного валов, отсоединяют двигатель от судового фундамента, выгружают и транспортируют в цех, где устанавливают в горизонтальном положении на специальный фундамент или металлические балки.
Разборка двигателя — один из важнейших технологических процессов ремонта, во многом определяющий его продолжительность и стоимость. Небрежная разборка нередко приводит к повреждению, а иногда и к утере деталей.
Процесс разборки двигателя на судне и в цехе по существу одинаков, однако разборка в цехе удобнее и значительно производительнее, так как выполняется в более благоприятных условиях. Последовательность разборки двигателя зависит от его конструкции; в каждом отдельном случае разборка должна производиться в соответствии с инструкцией завода-изготовителя. Должное внимание при разборке дизелей необходимо уделять клеймению и маркировке деталей и мест их установки в соответствии с инструкцией, чтобы при последующей сборке установить детали правильно. На специализированных предприятиях, ремонтирующих быстроходные дизели одного типа, детали при разборке не маркируют.
Последовательность разборки двигателей, имеющих в качестве основной детали остова фундаментную раму, примерно такова: сначала снимают контрольно-измерительные приборы, затем электрооборудование, трубопроводы, тяги топливных насосов и регулятора частоты вращения, удаляют стойки с клапанными рычагами, толкатели и штанги клапанов, навесные агрегаты, кожух шестерен, распределительный вал, крышки цилиндров, производят разъем нижних головок шатунов и, поворачивая коленчатый вал, последовательно поднимают поршни с шатунами, извлекая их из цилиндров. Затем выпрессовывают втулки цилиндров, отделяют цилиндры (блок цилиндров), снимают маховик, вскрывают рамовые подшипники, поднимают коленчатый вал и укладывают его на козлы. До выпрессовки втулок цилиндров зарубашечное пространство очищают от накипи и подвергают гидравлическому испытанию, причем выпрессовку втулок удобнее производить после демонтажа блока цилиндров или отдельных цилиндров. Если разборке подвергают несколько одинаковых двигателей, то их детали, как правило, не обезличивают. Ремонт быстроходных двигателей, как уже указывалось, производят на специализированных предприятиях, где внедрен технологический опыт заводов массового или крупносерийного производства данных двигателей. Высокая точность механической обработки, стандартизация и взаимозаменяемость многих деталей позволяют вести ремонт по поточной схеме с обезличиванием значительного количества-деталей; избегают обезличивания лишь совместно обработанных деталей. На ряде предприятий разборке двигателей предшествует их наружная мойка в специальных моечных машинах.
У двигателей крейцкопфного типа сначала отсоединяют шток поршня от поперечины крейцкопфа и только после этого, подняв поршень вместе со штоком, вынимают из цилиндра. Затем временно закрепляют крейцкопф на параллели, разбирают головные соединения и мотылевый подшипник шатуна (кривошип коленчатого вала находится в ВМТ). Медленно вращая коленчатый вал, выводят шатун из станины и вынимают его, снимают крейцкопфы и параллели. Во время разборки любого двигателя рекомендуется соблюдать следующие общие правила:
— детали и трубы систем и приборы укладывать на заранее подготовленные места;
— разборку производить только специально предназначенными для этой цели инструментами и приспособлениями;
— при разборке не применять чрезмерных усилий, а если узел не поддается разборке, выяснить причины;
— все открытые полости закрывать специальными крышками (использование в качестве заглушек пакли и ветоши воспрещается) ;
— концы трубок глушить деревянными пробками или специальными заглушками;
— если деталь крепится несколькими гайками, то сначала последовательно ослабить их, а уже потом отвертывать; гайки после разборки навертывать обратно на болты или шпильки, а если этого сделать нельзя, то гайки с каждого узла собирать на отдельную проволоку с биркой.
Следующий этап — подетальная разборка, т. е. разборка узлов на отдельные детали.
Иногда при ремонте двигателя в цехе в целях уменьшения массы двигателя и предотвращения возможных повреждений его узлов и деталей при выгрузке с судна и транспортировке в цех производят демонтаж отдельных узлов на судне и отправляют их в цех. Облегченный двигатель отсоединяют от судового фундамента и также направляют в цех.
Рассмотрим технологию разборки некоторых наиболее ответственных узлов двигателя. Выпрессовку втулок цилиндров производят для их замены, а иногда для очистки водяного пространства. Втулки выпрессовывают с помощью приспособления, показанного на рис. 104. Снизу к торцу втулки подводится диск 8, имеющий по окружности четыре отверстия, в которые заводят стержни 7. Сверху на шпильки цилиндра устанавливают четыре подставки 6 и два гидравлических домкрата 5. На головки плунжеров домкратов помещают жесткие прокладки 4, которые упираются в скобу 3, насаженную на стержень 7 и закрепленную гайками. На две другие подставки 6 устанавливают скобу 2, соединенную с двумя другими стержнями 7; под эту скобу заводят клинья 1. Установив приспособление, в за-рубашечное пространство впускают пар низкого давления для подогрева цилиндра и облегчения выпрессовки втулки, слегка подбивают клинья и вводят в действие домкраты, с помощью которых и выпрессовывают втулку. Последовательность разборки поршней зависит от их конструкции. Разборка большинства поршней двигателей крейцкопфного типа сводится к отсоединению штока поршня от его головки и снятию поршневых колец с поршня. Отсоединение поршня тронкового двигателя производится путем выпрессовки поршневого пальца с помощью специального приспособления, позволяющего избежать ударов по пальцу. На рис. 105 показано простейшее приспособление для выпрессовки пальца 1 поршня 2. Через пустотелый палец поршня пропущен болт 4, под головку которого подложена шайба 5. Вторым концом болт проходит через отверстие П-образной скобы 3, опирающейся на поверхность поршня. Навертывая гайку на болт 4, выпрессовывают палец и отсоединяют шатун от поршня. Если палец плавающий, а поршень силуминовый, то снимают заглушки, фиксирующие палец, нагревают поршень в масле до 250° С (523 К) и вынимают палец из поршня. Поршневые кольца снимают при помощи несложных приспособлений, предохраняющих их от поломки. Разборка шатуна тронкового типа сводится к выпрессовке втулки головного подшипника с предварительным высверливанием стопоров, а также удалению вкладышей мотылевого подшипника.
Разбирая коленчатый вал, спрессовывают шестерню привода распределительного вала и маховик, снимают заглушки, обеспечивающие герметичность масляных полостей шеек вала; при необходимости снимают противовесы.
При разборке распределительного вала спрессовывают передаточную шестерню, а в случае необходимости и кулачковые шайбы. Если вал состоит из нескольких частей, их разъединяют.
Перед дефектацией разобранные детали двигателя чистят и моют для удаления нагара, коррозии, жирового слоя и накипи. Очистку производят химическим, механическим и ультразвуковым способами.
Дефектация деталей — ответственный этап технологического процесса ремонта ДВС. Задачей дефектации является проверка цельности деталей (обнаружение наружных и внутренних трещин, обломков и т. п.) и определение степени износа, деформации, нарушений взаимного расположения поверхностей и их чистоты.
От того, как организована дефектация, зависят качество и стоимость ремонта. При недостаточно внимательном контроле может снизиться его качество, а чрезмерно жесткий контроль может вызвать перерасход запасных деталей. Дефектация позволяет разделить все детали на три группы. К 1-й группе относят детали, имеющие допустимый износ, а также прошедшие необходимые виды проверки; ко 2-й группе — детали, которые имеют предельный износ и изменение геометрической формы поверхности, но восстановление которых возможно; к 3-й группе относят детали, имеющие признаки окончательного брака и непригодные к восстановлению.
При дефектации деталей производят внешний осмотр, проверку на специальных приборах для выявления невидимых глазом дефектов, проверку герметичности, измерение размеров и проверку для выявления отклонений от первоначальной геометрической формы.
Внешний осмотр предшествует всем остальным проверкам и производится с помощью лупы. Он позволяет обнаружить трещины, раковины и другие дефекты, а также изменения поверхностного слоя металла (например, перегрев — по наличию цветов побежалости). До применения лупы производят визуальную проверку, а места, недоступные осмотру, проверяют обстукиванием для выявления трещин. Для обнаружения в деталях пороков, невидимых простым глазом, на предприятиях применяют магнитную дефектоскопию, просвечивание рентгеновскими лучами, гамма-дефектоскопию, ультразвуковой и люминесцентный контроль.
При дефектации деталей ДВС (исключая детали топливной аппаратуры) необходимы следующие контрольно-измерительные инструменты, приборы и приспособления: микрометрические скобы с пределами измерений 0—75 мм, 25—50 мм и более в зависимости от размеров поршневых пальцев, шеек коленчатого вала и поршней; индикаторный нутрометр со вставками различной длины; микрометрический нутрометр; индикатор линейный со штативом; щупы; штангенциркули; уровень слесарный с ценой делений 0,05—0,20 мм на 1 м длины; резьбомеры; проверочная линейка стальная; приспособление для измерения расхождения щек кривошипа; грузы и тонкая стальная проволока для отвесов; металлические рулетки и метр.
На специализированных предприятиях наряду с обычным инструментом широко применяют браковочные калибры и специальные измерительные приборы. Контроль с помощью калибров высокопроизводителен. Калибры бывают необходимы при проверке размеров труднодоступных поверхностей. Для определения размеров деталей прецизионных пар топливной аппаратуры внедряется пневматический метод измерений. Пневматические приборы отличаются высокой производительностью и большей точностью, чем индикаторные.
Измеряя детали, пользуются определенной методикой, учитывающей конструктивные особенности и условия работы каждой детали. Диаметр цилиндрических поверхностей трения проверяют в нескольких поясах, определяя отклонения от цилиндрической формы по длине (конусность, бочкообразность, корсетность). Диаметр проверяют в нескольких взаимно-перпендикулярных плоскостях, определяя отклонения от цилиндрической формы по поперечному сечению (овальность). Записав данные измерений в карту замеров и обработав их, делают заключение о том, к какой группе по степени дефектности следует отнести данную деталь двигателя.
Дата добавления: 2018-08-06; просмотров: 420; Мы поможем в написании вашей работы! |
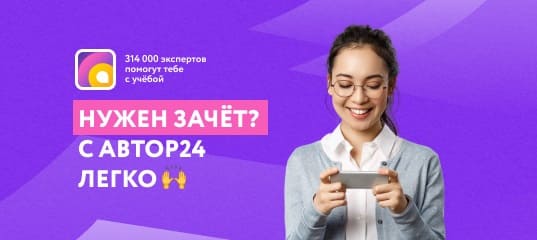
Мы поможем в написании ваших работ!