Правила техобслуживания и ремонт теплообменных аппаратов.
Nbsp; 2 Экзаменационные вопросы: 1. Ручной инструмент и измерительные приборы, применяемые для ремонтных и пусконаладочных работ в судовых условиях. - Ручной инструмент обычно используюется для производства и ремонта на борту судов, щипцы, гибочные станки, резаки, ножовки, недостатки, съемный механизм, напильники, сверла, развертки, молотки, водопроводная и штампы, щетки, наковальни, обжимки блоков, перфораторы, скреперы, долота, ножницы и зажимы - объясняет и демонстрирует, как использовать ручные инструменты, обычно используемые для производства и ремонта - Измерительные приборы, которые обычно используются для производства и ремонта на борту судна, глубинометры, микрометры, циферблатные индикаторы, толщиномеры, приборы определения радиуса и шага винтовой резьбы - объясняет и демонстрирует, как использовать измерительные приборы включая их точность - объясняет и демонстрирует правильные выборы определенного измерения инструменты в соответствии с их целями использования - использует различные измерительные приборы для приобретения навыков их использования. 2. Организация судоремонта. Одним из важнейших отделов судоремонтного предприятия, осуществляющих организацию ремонта является отдел главного строителя. Этот отдел осуществляет подготовку судоремонта, подбирает ремонтную документацию, знакомится с ремонтной ведомостью, подготавливает заявки на материально-техническое снабжение, отвечает за качество ремонта. Согласно записям в судовой документации, а также на основании технической документации заводов-изготовителей и нормативных документов, актов освидетельствования Регистром РФ по корпусу, механизмам, электрооборудованию и другим частям и осмотров в доке, актов инспекторских осмотров судна, актов и предписаний органов надзора составляются ремонтные ведомости, являющиеся основным документом, который определяет номенклатуру работ по ремонту судна. Ремонтная ведомость — основа для определения стоимости, срока и технологии выполнения ремонта. Ее составляют отдельно по механической, корпусной и другим частям. Для судов серийной постройки используют типовые ремонтные ведомости (ТРВ). При определении фактического объема ремонтных работ позиции, не требующие ремонта, из них исключаются. Представленная на предприятие ремонтная ведомость калькулируется. Калькуляция— это технико-экономический расчет для выполнения работ по ремонтной ведомости (трудоемкость, зарплата, материалы и их стоимость). Ремонтная ведомость, по которой составлена калькуляция, называется сметой. Приемку отремонтированных механизмов в период ремонта судна ведут по мере готовности отдельных видов работ, а окончательно — после завершения ремонта в целом; главный двигатель и вспомогательные двигатели принимают по специальной программе швартовных и ходовых испытаний. Обнаруженные дефекты устраняют и при необходимости назначают повторные испытания. По окончании испытаний составляется акт с указанием результатов испытаний. После проведения всех испытаний (предварительных приемок, сдаточных испытаний) составляется приемосдаточный акт, время подписания которого считается окончанием ремонта судна. Гарантийный срок после выхода из ремонта устанавливается для среднего и капитального ремонтов не менее 6 мес. 3. Технология судоремонта. совокупность one раций по восстановлению исправного состояния кор-пуса, механизмов, устройств, судовых систем, электронного оборудо-вания и других элементов судна, осуществляемых на судо-ремонтных предприятиях. К ремонтным работам отно-сятся демонтаж, разборка, дефектация, ремонт, сбор-ка, монтаж, испытание элементов судна. Для проверки качества работ в их состав включают также операции технического контроля. Технологию ремонта какого-либо элемента судна выбирают исходя из его состояния, определяе-мого по результатам технической диагностики и дефектации. При этом остаточный ресурс детали, пригодной к даль-нейшему использованию без ее восстановления, дол-жен быть не меньше межремонтного периода соответствующего элемента судна; физико-химические процессы, происходящие в сопряжении новой и изношенной (или восстановлен-ной) деталей, не должны ускорять их износ; восстанов-ление деталей не должно увеличивать стоимость ре-монта элемента судна по сравнению с заменой их новы-ми. Технология судоремонта отличается большим разнообразием методов восстановления свойств изношенных деталей, их формы и размеров. К наиболее традиционным относятся механическая обра-ботка, сварка, наплавка, нанесение металлических и неметаллических покрытий (в том числе электролитическим способом), деформирование, применение полимерных композиций, термическая и химико-термическая обработка. Сварка и наплавка позволяют сравнительно быстро получать слои метал-ла значительной толщины и таким образом восстанавливать изношенные по-верхности. Применяют ручную, полуавтоматическую, авто-матическую, сварку и наплавку под слоем флюса и в защитных газах, а также плазменную, электроимпульсную, индукционную, наплавку ленточным электродом и др. Металлические покрытия наносят напылением или электро-литическим способом. Среди различных способов напыле-ния наиболее перспективна плазменная металлизация, для которой характерна более высокая механическая прочность сцепления покрытия с основным металлом. Электролитическое осталивание и хромирование применяют для восста-новления неподвижных соединений. С помощью неметаллических и композитных покрытий обычно восстанавли-вают элементы корпусных конструкций. Восстановле-ние деталей деформированием осуществляется растя-жением, осадкой, обжатием и правкой цилиндрических де-талей и корпусных конструкций. Наиболее распростране-на механическая, термическая и термомеханическая правка. Полимер-ные композиции используются в качестве клеев для со-единения различных материалов и деталей, как шпаклевоч-ных масс для устранения пороков литья, коррозных дефектов, трещин и т. д., для нанесения пленок при восстановлении натягов в неподвижных соединениях и защитных покрытий для предохранения судовых конструкций от воздействия различных агрессивных сред. Для увеличения долговечности элементов судна при-меняются различные методы повышения износостойкости деталей. Наиболее распространены поверхностное упроч-нение, термическая, химико-термическая обработка и обработка холодом. В технологии судоремонта широко используются неразрушающие методы контроля: мело-керосиновая, масляная, магнитная, ультразвуковая, рентгеновская дефектоскопия, цветные пробы, гамма-дефектоскопия, радиоизотопный ме-тод, гидравлические и воздушные испытания. Дальнейшее совершенствование технологии судоремонта неразрывно связано с его концентрацией и специализацией, ростом серийности, выполнением ремонта предприятиями — строителями судов и изготовителями комплектующих изделий, ме-ханизацией и автоматизацией производства. Технико-экономический уровень технологии судоремонта должен быть таким, чтобы народно-хозяйственные потребности удовлетворялись при минимальных затратах на техническую эксплуатацию флота. Такой уровень технологии судоремонта называют оптимальным. Для его оценки приме-няют совокупность показателей — производитель-ность, качество и себестоимость продукции, удельный расход материальных и энергетических ресурсов, уровень механизации и автоматизации, стабильность техно-логических операций. 4. Автоматический контроль и нормирование эксплуатационных показателей. Надежность оборудования определяется его конструкцией и качеством изготовления. Однако в ходе эксплуатации из-за процессов старения материалов и внешних воздействий надежность оборудования снижается. Создание электрооборудования, показатели надежности которого за весь период эксплуатации не станут ниже допустимых, - задача достаточно трудная и в значительном числе случаев экономически нецелесообразная. Поэтому в ходе эксплуатации оборудования необходимо проведение работ по поддержанию требуемого технического состояния. В условиях эксплуатации необходимо обеспечивать как минимум работоспособное состояние. Это возлагается на систему технического обслуживания (ТО) и ремонтов. Основное содержание ТО - контроль за состоянием оборудования и собственно обслуживание, т. е. поддержание исправности или работоспособности (чистка, смазка, регулировка и т. п.). Задача ремонта - восстановление исправности или работоспособности. Эксплуатационный контроль оборудования является системой определения его технического состояния. На основании полученных при контроле данных принимается решение о допустимости дальнейшей эксплуатации оборудования или о необходимости и объеме ремонта. Система эксплуатационного контроля должна обеспечить выявление и идентификацию дефектов (собственно диагностирование), а также прогнозирование их развития. Автоматизация измерений и анализов обеспечивает не только снижение объема работ персонала и возможность непрерывного контроля. Принципиальным отличием такой системы контроля является возможность передачи соответствующему устройству значительной части функций собственно диагностики, т. е. функций идентификации дефектов и оценки технического состояния объекта. Такими возможностями обладают диагностические системы на базе ЭВМ. Эти системы могут проводить измерения и математическую обработку полученных данных с целью снижения помех, анализ результатов измерений и сравнение их с нормами. При необходимости автоматическая система диагностики меняет тактику (алгоритм) контроля (периодичность измерений, способ оценки их результатов) и выдает оператору сообщение вместе с протоколом, содержащим данные для принятия решений по эксплуатации данного объекта. Возможны два способа организации контроля оборудования под напряжением: - ранняя диагностика, т. е. выявление признаков ухудшения технического состояния, вызывающих изменения значений контролируемых параметров; - сигнализация предельных состояний, т. е. выявление признаков ухудшения технического состояния, являющихся опасными с точки зрения надежности оборудования. 5. Правильность монтажа и центровки судовых насосов.
|
|
|
|
|
|
|
|
ПОДГОТОВКА К МОНТАЖУ
Так как насос не является статичным механизмом, а оснащён вращающимся на высоких скоростях ротором, необходимо прилагать все усилия, чтобы нагрузки, предусмотренные производителем, не были превышены. Для этого должны соблюдаться определённые условия, предлагаемые изготовителем, но согласованные с заказчиком.
· Одним из таких условий является предмонтажная центровка соединения насоса и привода. Её следует не просто выполнить, но и контролировать в течение всего периода эксплуатации. Далее мы расскажем более подробно, как это делается.
· Вторым важным условием комфортной работы насоса является регулярная проверка соединений трубопровода. Это наиболее важно, когда выполняется частичный или полный демонтаж элементов системы.
Вертикальные насосы наиболее чувствительны к несоосности, чем горизонтальные. Поэтому для них стандарт устанавливает меньшие допустимые значения крутящих моментов на фланцах. Чрезмерные нагрузки на них приводят к усилению вибрации.
Центровка
Центровка выполняется при установке крупных центробежных, а также поршневых агрегатов. Бытовые насосы в этом не нуждаются, так как у них двигатель и насос заключены в одном корпусе и отцентрованы производителем.
· Самая ответственная часть предмонтажной подготовки агрегата – это центровка по полумуфтам: насоса и редуктора, или редуктора и электродвигателя. Суть данного действия такова.
Центровка вала двигателя и центробежного насоса
· Один из валов принимают за базовый, чаще всего это вал насоса. Его закрепляют на раме и с помощью штангенциркуля и щупа выверяют зазоры. Затем то же самое проделывают на полумуфте двигателя. При наличии отклонений его вал смещают так, чтобы он принял нужное положение.
· Делают это путём установки подкладок или смещения самого двигателя. Затем снова проверяют ширину торцевых зазоров. Оси насоса и двигателя совпадут только в том случае, если зазоры на полумуфтах будут одинаковыми.
· Кстати, центровать элементы агрегата необходимо не только перед первичным запуском, но и после проведения ремонта и технического обслуживания двигателя. Для этого его отсоединяют от насоса и разбирают.
· При небольшом износе рабочих деталей их не меняют, а просто очищают и промывают керосином. Шейки валов шлифуют, набивают сальник и собирают вновь. После центровки оси вала двигателя и насоса никакой вибрации и шума, а также нагрева сальника и подшипников не должно быть.
- При установке центробежных насосов, механики придерживаются таких правил: если насос идёт с завода в сборе, то его ротор центруют по валу двигателя, если же насос собирают на опорной раме, то вал ротора двигателя выверяют по нему.
В тех случаях, когда насос соединяется с двигателем через редуктор и промежуточный вал, сначала центруют редуктор и фиксируют его штифтами. Положение валов всех остальных частей агрегата ориентируют уже на него.
6. Трубопроводы. Выбор диаметра и толщины трубы, для замены на судовых трубопроводах
Трубопровод — это сооружение, предназначенное для транспортировки жидких, газообразных и твердых (сыпучих) продуктов. Трубопроводы состоят из плотно соединённых между собой прямых участков труб, деталей, запорно-регулирующей арматуры, контрольно-измерительных приборов, средств автоматики, опор и подвесок, крепежа, прокладок и уплотнений, а также материалов, применяемых для тепловой и антикоррозионной изоляции.
Выбор диаметра труб является техническим и экономическим решением. Следует иметь в виду, что во избежании излишних затрат энергии, потери давления, не должны быть чрезмерно высокими. Размер отверстий всасывающего и нагнетающего патрубков насосов указывают только на минимальный размер труб.
Выбор адекватных сечений должен осуществляться таким образом, чтобы максимальная скорость прохождения была следующей:
На линии всасывания: 1,8 м/сек
На линии нагнетания: 2,5 м/сек
Важно учитывать скорость потока, так как от этого зависит экономичность и продолжительность срока службы системы нагнетания.
- Скорости меньше 0,5 м/сек обычно приводят к осадконакоплениям.
- Скорости свыше 5 м/сек могут вызвать абразивный износ.
7. Правила техобслуживания центробежного насоса.
Техническое обслуживание включает комплекс работ по уходу за насосным оборудованием, проведение осмотров, систематическое наблюдение за их исправным состоянием, соблюдением правил эксплуатации и инструкций заводов-изготовителей, устранение мелких неисправностей, контроль и осуществление необходимых мер по эко-номному расходованию всех видов энергоресурсов. Техническое обслуживание производится силами оперативного или оперативно-ремонтного персонала в процессе эксплуатации насосного оборудования. Осмотры являются важнейшей функцией технического обслуживания и фактором, обеспечивающим безаварийную работу насосного оборудования. Как самостоятельная операция осмотры планируются перед текущим и капитальным ремонтами. Во время осмотра проверяют состояние оборудования, производят чистку, промывку, продувку, ремонт изоляции, доливку или замену масел, выявляют дефекты эксплуатации и нарушения правил безопасности, уточняют состав и объем работ, подлежащих выполнению при очередном текущем или капитальном ремонте.
8. Ремонт центробежного насоса.
Разбирать подключенный насос запрещается правилами техники безопасности. Свой прибор необходимо обесточить ровно, как и всю принадлежащую ему автоматику и защиту, и, только убедившись в этом, начинать работу. Коротко процесс ремонта описывается следующим образом: разборка производится после вытаскивания насоса из воды на чистой гладкой поверхности, чтобы не произошла утеря соединительных элементов и частей конструкции. Для надежности следует подписать/пронумеровать все демонтируемые части приспособления. Весь процесс можно сопровождать фотофиксацией или видеосъёмкой; визуальным осмотром обнаружить изношенные элементы и произвести их замену предварительно купив у производителя или дилера оборудования. Только полностью соответствующий аналог предоставит дальнейшую безопасную работу; очистить другие конструктивные элементы и при необходимости внести смазочный материал; в обратном порядке произвести сборку оборудования и проверить его работоспособность. Если пользователь забыл, как подключить насос обратно в систему водяного снабжения или к электросети, необходимо эти действия согласовать с идущими в комплекте схемами и рекомендациями инструкции.
9. Правила техобслуживания винтового и шестеренчатого насосов.
Винтовой насос особого технического обслуживания не требует, но следует регулярно проверять трубопроводы на герметичность.
Подшипники качения насоса через каждые 5000 часов работы следует заполнять консистентной смазкой. Регулярно, во время работы насоса, необходимо проверять сальниковое уплотнение, которое не должно быть сильно затянуто. Из сальника должна капать рабочая жидкость.
Опыт эксплуатации винтовых насосов показал, что насосы надёжны и обладают высоким ресурсом. Они устойчиво работают в условиях крена и дифферента и не требуют непрерывного ухода и наблюдения. Азотированные поверхности профилированной части винтов и хромированные поверхности шеек практически не подвергаются изнашиванию, даже при наличии механических частиц в перекачиваемой жидкости.
Для заполнения смазкой подшипников качения необходимо:
- снять крышку подшипника;
- пространство между кольцами подшипника промыть и заполнить смазкой;
- установить крышку подшипника на место.
Шестеренчатый насос Пуск шестеренного насоса производят при открытых всасывающем и нагнетательном клапанах. Если насос готовится к работе впервые, его необходимо залить. Работа насоса без жидкости запрещается. Для шестеренного насоса особого ТО не требуется.
ТО включает внешний осмотр насоса и проверку:
- соединения нагнетательных и всасывающих трубопроводов;
- сальникового уплотнения (при необходимости подтягивать);
- крепления фундаментных болтов;
- центровку шестеренного насоса с электродвигателем.
Подшипники качения насоса через каждые 5000 часов работы следует заполнять консистентной смазкой. Снять крышку подшипника, полость подшипника промыть. Подшипники качения и уплотнительные кольца валов осмотреть. Поврежденные детали заменить. Крышку подшипника поставить на место.
10. Ремонт винтового и шестеренчатого насосов.
Шестеренчатый насос:
У шестеренного насоса характерными дефектами являются: увеличение диаметрального зазора между корпусом и вершинами зубьев шестерён из-за их изнашивания, осевого зазора между торцами шестерён и крышками корпуса, подшипников и уплотнения, диаметрального зазора в опорных подшипниках скольжения.
При дефектоскопии шестерённого насоса измеряют диаметральный зазор между корпусом и шестернёй и осевой зазор — между торцом шестерни и корпусом насоса. Полученные зазоры сравнивают с монтажными и предельно допустимыми в шестеренных насосах при эксплуатации. Ремонт способом обжатия корпуса насоса, изготовленного из цветных сплавов. Способ заключается в том, что корпус насоса, нагретый до необходимой температуры (в зависимости от материала), продавливают через фильеру, или обжимают в специальной призматической оправке до получения необходимых размеров внутренних цилиндрических поверхностей с припуском на обработку, после этого корпус вторично нагревают до той же температуры и медленно охлаждают до температуры окружающей среды для снятия внутренних напряжений. Затем внутренние цилиндрические поверхности растачивают на номинальный диаметр. Резьбовые отверстия в корпусе калибруют. Крепёжные отверстия в крышках рассверливают до необходимых размеров. Крышки после установки и центровки фиксируют штифтами.
Однако, отремонтированные таким образом насосы при напоре выше 6 МПа, как показала практика, часто выходят из строя в результате длительного воздействия на корпус высокого давления, вызывающего деформацию корпуса, в ряде случаев с появлением трещин.
По этой причине данный способ ремонта корпусов шестерённых насосов, работающих при напоре выше 6 МПа, не получил широкого распространения.
Винтовой насос: Для винтовых насосов характерно изнашивание профильных частей винтов, упорных поверхностей и шеек под подшипники, а также подшипников и уплотнений.
Профильную часть поверхности винтов восстанавливают электролитическим хромированием с последующей обкаткой на специальных стендах с пастами ГОИ. Контакт по профилю зубьев должен быть не менее 90% по длине и не менее 50% по высоте зуба. Упорные поверхности винтов шлифуют.
Винты изготавливают из азотируемых сталей типа 38ХМА. Глубина азотированного слоя составляет не менее 0,5 мм. Шейки винтов под подшипники, если они не имеют сменных хромированных втулок, хромируют.
Номинальный зазор в зацеплении винтов в нормальном сечении составляет 0,05-0,1 мм. Износ профильных частей винтов допускается не более чем 0,15 мм.
Во всех насосах подшипники скольжения восстанавливают или заменяют.
Плоскости разъёма корпусов насосов пришабривают на краску. Радиальный установочный зазор между корпусом и винтами обеспечивается посадкой Н9Я9. Минимальное значение зазора составляет 0,04 мм.
При центровке насоса с электродвигателем должны быть выдержаны нормы на смещение и излом, в зависимости от типа соединительной муфты.
11. Правила техобслуживания поршневого насоса.
Аксиально- и радиально-плунжерные насосы надёжно работают при соблюдении следующих требований:
- при применении марки масла, указанного в паспорте;
- не смешивать (при доливке) масла разной вязкости, а также минеральные и синтетические;
- использовать в системе только штатные масляные фильтры и регулярно их менять;
- содержать в чисготе всю гидравлическую систему, так как загрязнённое масло — основная причина отказов насоса;
- замену масла производить ежегодно.
Перед пуском аксиально- и радиально-плунжерных насосов необходимо:
- проверить уровень масла в расширительном баке и редукторе;
- открыть клапаны на нагнетательном и всасывающем трубопроводах;
- проверить наличие и подключение штатных контрольно-измерительных приборов;
- проверить в действии предохранительный (перепускной) клапан;
- проверить состояние соединительной муфты;
- пустить в ход электродвигатель и убедиться в нормальном функционировании агрегата.
Запрещается пуск насоса при закрытых клапанах на нагнетательном трубопроводе, так как это станет причиной гидравлического удара и разрушения клапанной коробки или других деталей.
Во время работы необходимо:
- следить за уровнем масла;
- проверять сальник на плотность и в случае необходимости его подтянуть.
Аксиально- и радиально-плунжерные насосы, как правило, не требуют обслуживания.
12. Ремонт поршневого насоса.
К основным дефектам относят: изнашивание цилиндровых втулок, плунжеров, клапанов и подшипников. Как правило, цилиндровые втулки ремонтируют, а плунжеры заменяют на новые, или ремонтируют, увеличивая диаметр путём нанесения слоя хрома электролитическим способом.
Цилиндровая втулка, имеющая трещины, подлежит замене; риски, задиры — зашлифовывают. Если износ на диаметр превысил допустимую величину — втулку заменяют или растачивают на очередной ремонтный размер, соответственно этому размеру подбирают новый плунжер.
Плунжер — при механическом изнашивании отверстия под поршневой палец, канавок под поршневые кольца, наличии рисок, задиров шлифуют по фактическому размеру цилиндровой втулки, обеспечивая допуск от + 0,01 до + 0,015 мм на доводку по внутреннему диаметру цилиндра, то есть наружный диаметр плунжера. Критерием качества ремонта является то, что плунжер не должен выпадать из втулки при его вертикальном положении.
Клапаны с небольшими раковинами на уплотнительных поясках подлежат притирке, с крупными раковинами — проточке с последующей притиркой. Притирка осуществляется притирочными пастами, начиная с крупнозернистой и заканчивая мелкозернистой, затем пастой ГОИ.
Подшипники скольжения, имеющие изнашивание антифрикционного слоя выше нормы, риски, задиры, оплавление, заменяют на новые (увеличенный размер приводит к проворачиванию подшипника, уменьшенный — к нагреву).
Цапфа, вал — при ремонте рабочей шейки цапфы, на которой вращается звёздочка, её шлифуют до восстановления цилиндрической формы, а втулку звёздочки заменяют. При наличии трещин, скручивания и изгиба вала его заменяют. Наработки и задиры на шлицах устраняют опиливанием и шабрением.
Корпус с трещинами, раковинами и коррозионными разрушениями заменяют. Раковины заваривают, коррозионные разрушения посадочных мест под подшипники устраняют растачиванием, хромированием наружного кольца подшипника с последующим шлифованием.
13. Проверка работы клапанов запорной арматуры.
Время от времени запорная арматура должна проходить проверку на герметичность. Это обязательное условия для работы без сбоев и остановок. Протечка возможна по производственной причине, из-за заводского дефекта или погрешностей при сборке и обработке прилегающих деталей. После того как бы выполнен монтаж запорной арматуры на трубопровод, проводится проверка. Недостаточная герметичность может сказываться на эксплуатационных качествах конструкции или прочность аппаратуры. Чтобы ликвидировать ее, необходимо провести гидравлическое испытание или серию таковых.
Испытание проводится в два этапа:
1. Проверка на прочность, непроницаемость, статичность разъемных соединений.
2. Проверка исправности запорной арматуры.
На первом этапе мастер находит детали с дефектами. Это может быть пористость металла, газовые или песчаные раковины, различные трещины, смещение стенок, остаточное внутреннее напряжение, щели на месте сварных швов. Чтобы окончательно убедиться в том, что через отверстия проходит воздух или вода, только внешнего осмотра недостаточно. Нужно прогнать через арматуру воду под давлением в полтора-два раза выше условного рабочего. Это производится с помощью насоса. В среднем это длится около двух минут. Температура жидкости – не более 100 градусов Цельсия. Если вода находит выход наружу через металл – дефект налицо.
Важно: испытания проводятся на всех полостях, при открытом положении запорного клапана, но закрытыми проходными отверстиями. Литые детали нужно простучать молотком из меди или свинца массой не тяжелее килограмма. Это позволит более точно поставить «диагноз».
На втором этапе проводится проверка запорной арматуры. Специалист должен убедиться в том, что уплотнительные поверхности притерты друг к другу качественно. А также осмотреть места соединений мембранного и сальникового узлов.
ПРОВЕРКА ЗАПОРНОЙ АРМАТУРЫ НА ПРОЧНОСТЬ И ГЕРМЕТИЧНОСТЬ
Иногда нет нужды применять к проверяемой арматуре чересчур высокие требования по непроницаемости. В некоторых случаях допускается незначительный пропуск воды или воздуха. Это не вредит производственному процессу и не снижает срока эксплуатации устройства. ГОСТ 9544-75 определяет нормы герметичности для разных классов арматуры.
· класс первый: взрывоопасные и токсичные среды;
· класс второй: пожароопасные среды;
· класс третий: прочие среды.
Кроме способа проверить пропуск водой, можно использовать мыльный раствор. Для этого следует нанести кисточкой на место контроля смесь воды и мыла и посмотреть, появляются ли пузыри. Размер «бедствия» оценивается по числу пузырей в минуту.
14. Правила техобслуживания воздушного компрессора.
Для смазки компрессора рекомендуется применять только специальные компрессорные масла. При продолжительной стоянке компрессора его необходимо запускать не реже одного раза в неделю на 2-3 минуты на холостом ходу.
При отсутствии указаний завода-изготовителя о сроках проведения технического обслуживания (ТО), его следует выполнять ежеквартально, через полгода и ежегодно.
Через три месяца эксплуатации необходимо проверить состояние:
- смазочных устройств и системы охлаждения;
- предохранительных клапанов;
- контрольно-измерительных приборов;
- крепления компрессора к фундаментной раме;
- состояние приводного электродвигателя и его пускового устройства.
Через 6 месяцев эксплуатации выполнить следующие работы:
- вскрытие и осмотр цилиндров;
- проверку зазоров между поршнем и цилиндровой втулкой;
- проверку зазоров в рамовых и шатунных подшипниках скольжения.
Через год эксплуатации:
- провести полную разборку компрессора;
- детали тщательно очистить, промыть и произвести дефектоскопию деталей компрессора;
- выбраковать детали, имеющие предельные износы;
- проверить состояние приводного электродвигателя и его пускового устройства;
- составить ведомость на ремонт;
- записать необходимые сведения в журнал технического состояния.
Если компрессор выводится из эксплуатации на ремонт в зимний период, необходимо спустить воду из блока, насоса и трубопроводов системы охлаждения и продуть их сжатым воздухом во избежание размораживания.
15. Ремонт воздушного компрессора.
Техническое состояние компрессора без его разборки можно проконтролировать по уровню вибрации, ударных импульсов, по величине снижения производительности и по наличию воды в масле. Состояние клапанов можно определить по уровню температуры и давления воздуха за ступенями.
Состояние цилиндро-поршневой группы (зазоры в рамовых, шатунных подшипниках и в верхней головке шатуна (головной подшипник), между поршнем и втулкой, состояние поршневых колец) контролируется по уровню вибрации и снижению производительности компрессора.
Измерение уровня вибрации производится виброметром ВШВ-003, VTM-33, или аналогичными приборами.
Вибрация измеряется в вертикальной плоскости на крышках цилиндров и в горизонтальной плоскости на верхних кромках цилиндрового блока (середина цилиндра).
Уровень виброскорости (мм/с, среднеквадратичное значение), измеренный в горизонтальной плоскости на основной частоте вращения коленчатого вала компрессора Fо = n/60 Гц ( где n — частота вращения, мин-1), характеризует состояние зазоров в рамовых подшипниках; на частотах 2Fо и 4Fo — зазоры между поршнем и цилиндровой втулкой и состояние поршневых колец.
Уровень виброскорости, измеренный в вертикальной плоскости на частотах 2Fo и 4Fo, характеризует зазоры в шатунных подшипниках и верхней головки шатуна.Техническое состояниеохладителей определяют по величине снижения производительности и разности между температурой поверхности выходного воздушного патрубка цилиндра 1-й ступени и температурой поверхности водяного патрубка на входе в воздухоохладитель.
Состояние смазочного насоса контролируется по величине давления в смазочной системе.
Состояние уплотнительной прокладки головки блока компрессора определяется по наличию воды в масле. Контроль воды в масле производится с помощью прибора ИВМ-индикатор, разработанным ЦНИИМФом, или зарубежных средств типа «Toetik» или «Perotec». Предельное значение содержание воды в масле не должно превышать 0,2%.
В связи с тем, что ремонт поршней, поршневых колец, шатунов, коленчатых валов, подшипников, цилиндров и клапанов поршневых компрессоров ничем не отличаются от ремонта этих же деталей ДВС, то мы ознакомимся только с работами, характерными для компрессоров. К таким работам по ремонту компрессоров относят:
- регулировку высоты камеры сжатия;
- очистку змеевиков охладителей воздуха;
- регулировку предохранительных клапанов;
- гидравлические испытания воздушных баллонов.
Регулировка высоты камеры сжатия заключается в том, чтобы объём камеры сжатия приближался к наименьшей возможной величине, при которой не было бы ударов поршня о крышку цилиндра. Величина высоты камеры сжатия у поршневых компрессоров, в зависимости от их размеров, не превышает 0,2-0,4 мм в ступенях высокого давления и 0,5-1 мм — в ступенях низкого давления.
Регулировку высоты камеры сжатия в поршневых компрессорах производят путём изменения толщины прокладок в пределах 0,05-0,5 мм:
- между крышкой и цилиндровой втулкой;
- между шатуном и шатунным подшипником;
- между картером и цилиндровой втулкой.
Проверку высоты камеры сжатия в цилиндрах компрессоров производят и перед ремонтом.
Очистка змеевиков охладителей воздуха необходима, так как в процессе эксплуатации поршневого компрессора змеевики снаружи покрываются слоем накипи, а внутри змеевиков скапливается много нагара и масла. Поэтому, при капитальном ремонте компрессора каждый змеевик должен быть разобран, отожжён и испытан гидравлическим давлением, равным не менее полуторного и не более двойного рабочего давления в данной ступени компрессора.
Отжиг змеевиков включает следующие операции:
- к одному из концов змеевика подсоединяют воздушный шланг низкого давления (0,3-0,7 МПа) и продувают сжатым воздухом;
- затем змеевик нагревают до температуры 600-700 С в нагревательной печи, на горне или паяльными лампами. Нагретый змеевик быстро опускают в воду;
- после отжига змеевик вновь продувают сжатым воздухом и подвергают гидравлическому испытанию.
Правила техобслуживания и ремонт теплообменных аппаратов.
Важнейшим условием нормальной и достаточно эффективной работы теплообменных аппаратов (конденсаторов, испарителей, воздухоохладителей и батарей в холодильных камерах) является поддержание поверхностей теплопередачи и участвующих в процессе сред в состоянии благоприятном для теплообмена.
В отношении конденсаторов для выполнения этого условия необходимо: стремиться не допускать в трубчатую систему масло, а проникшее туда масло, а также воздух регулярно удалять, систематически очищать трубы конденсатора от накипи. Важно, чтобы вода на конденсатор подавалась непрерывно и в достаточном количестве; на оросительных конденсаторах необходимо следить за равномерностью орошения трубчатой системы водой и за тем, чтобы в жалюзных шатрах не образовывался туман. Равномерность орошения достигается правильным положением отбойных щитков на конденсаторе, а образование тумана предотвращается усиленной циркуляцией воздуха в жалюзном помещении (например, снять часть жалюзных досок).
В отношении испарителей важными моментами технического обслуживания являются: удаление масла, тщательная очистка поверхностей, поддержание соответствующего уровня жидкого агента и рассола, концентрация которого должна систематически контролироваться, безотказно должны работать мешалки и рассольные насосы.
Растворы солей оказывают коррозирующее воздействие на металлы, что резко отрицательно сказывается на сроке службы рассольных систем. Наиболее сильно подвергаются коррозии те металлические детали, которые попеременно подвергаются воздействию рассола и кислорода воздуха. Для уменьшения коррозии в рассол добавляют антикоррозийные вещества или так называемые пассиваторы (силикат натрия, хромовая соль, фосфорная кислота), а также принимают меры, препятствующие насыщению рассола кислородом воздуха и предохраняющие металлические части от прямого соприкосновения с рассолом и воздухом (не допускать взбалтывания рассола в местах его соприкосновения с воздухом, плотно закрывать рассольные баки, периодически окрашивать трубы и т. д.). Тепловая изоляция испарителя должна поддерживаться в хорошем состоянии. В сухих воздухоохладителях необходимо проверять трубчатую систему на плотность, не допуская утечек холодильного агента, следить за надежностью закрытия дверок кожуха и правильным положением шиберов. При нормальной работе воздухоохладителя его трубчатая система равномерно покрывается инеем, который должен систематически удаляться. Нельзя допускать нарастание на трубах инея толщиной более 5 мм.
В мокрых воздухоохладителях должна быть отрегулирована система орошения рассолом, безотказно работать форсунки, вентиляторы и насосы, поддерживаться определенная концентрация рассола.
Трубчатые батареи холодильных камер следует систематически очищать от инея (снеговой шубы) и освобождать от попавшего в них масла.
Батареи непосредственного испарения очищают от масла и механических примесей, продувая их горячими парами холодильного агента или воздухом в тот период, когда камера освобождена от продуктов.
Иней, образующийся на трубах воздухоохладителей и батареях, когда температура поверхностей их ниже точки росы и 0°С, ухудшает теплопередачу и циркуляцию воздуха. На холодильниках снеговую шубу с батарей удаляют механическим способом или оттайкой горячими парами холодильного агента. Последний способ является наиболее совершенным и распространенным.
Снеговую шубу с батарей удаляют следующим способом: на батареях перекрывают вентили, через которые они питаются жидким аммиаком. Ресивер, свободный от аммиака, присоединяют к линии отсоса паров и батарей к отделителю жидкости, что понижает в нем давление до давления всасывания. Затем вентиль отсоса паров аммиака из батарей, предназначенных для оттаивания, закрывают, а вентиль на сливной линии открывают. После этого жидкий аммиак из батарей самотеком поступает в расположенный ниже ресивер
Дата добавления: 2018-08-06; просмотров: 464; Мы поможем в написании вашей работы! |
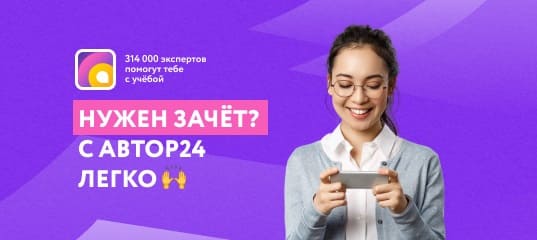
Мы поможем в написании ваших работ!