Восстановление автомобильных деталей полимерными материалами .
3.1. Классификация полимерных материалов, применяемых для ремонта
и изготовления деталей.
В авторемонтном производстве все более широкое применение при изготовлении и восстановлении деталей находят различные виды полимерных материалов.
Их используют при устранении механических повреждений на деталях (трещины, пробоины, отколы и т.п.), при компенсации износа рабочих поверхностей деталей, при соединении деталей склеиванием, а также при изготовлении деталей.
Главной составляющей частью пластмасс являются полимеры.
Полимеры – это высокомолекулярные соединения, которые содержат большое количество одинаковых группировок, соединенных химическими связями.
Пластмассовыми называют полимеры, в которых для придания требуемых свойств введены наполнители, пластификаторы, стабилизаторы, красители и др. добавки, сообщающие пластификаторы, стабилизаторы, красители и др. добавки, сообщающие пластмассам требуемые свойства.
В зависимости от структуры молекул по отношению к нагреву полимеры и пластмассы подразделяются на две большие группы:
термопласты (термопластичные),
реактопласты (термоактивные).
Термопласты при нормальной температуре находятся в твердом состоянии, а при нагреве размягчаются. В этом состоянии им можно придать любую форму. После охлаждения они снова затвердевают. При повторном нагреве термопласты сохраняют пластические свойства, то есть, пригодны для дальнейшего использования.
|
|
Из термопластов наибольшее применение нашли полиэтилены, полипропилены, полистиролы, винилпласты, полиамиды и фторопласты. К полиамидам относятся полиамидные смолы АК-7, капрон, нейлон и др.
Все эти материалы обладают хорошей адгезией с металлами, достаточно высокой механической прочностью и износостойкостью.
Реактопласты при нормальной температуре могут быть в жидком или твердом состоянии, но при нагреве до определенной температуры переходят в вязко-тягучее состояние, а при дальнейшем нагреве затвердевают и остаются в таком состоянии независимо от температуры.
Этот процесс необратимый, так как перевести реакпласты снова в пластическое состояние невозможно. Из реакпластов наиболее широкое применение при восстановлении и изготовлении деталей нашли фенопласты и эпокситопласты. В качестве связующих веществ применяются в термоактивные смолы, одной из разновидностей которых являются эпоксидные смолы ЭД-16 и ЭД-20.
Смола представляет собой вязкую жидкость светло-коричневого цвета и является основным связующим веществом в различных композициях. Для перехода смолы из жидкого состояния в неплавкое и нерастворимое состояние в смолу вводят отвердители. Существуют два вида отвердителей – холодные и горячие.
|
|
В качестве холодных отвердителей применяют полиэтиленполиамин (ПЭПА) и аминофенол (АФ-2).
При горячем отвердении смолы используют малиновый ангидрит и процесс происходит при температуре 120-160°С.
Для повышения пластических свойств эпоксидного состава в него вводят пластификаторы, в качестве которых наиболее часто используют дибутилфтолат (ДВФ).
Для придания эпоксидному составу требуемых физико-механических свойств в него вводят наполнители: стальной или чугунный порошок, алюминиевую пудру, порошки слюды, талька, асбеста и графита, стеклоткань и др.
Для сокращения времени приготовления композиции промышленностью выпускаются пластифицированные эпоксидные смолы-компаунды: К-115 (ТУ 6-05-1251-75); К-153 (ТУ:-63-1584-72), К-176 (ТУ 6-052-041-358-72).
Кроме синтетических материалов в последнее время все большее применение в авторемонтном производстве находят синтетические клеи: ВС-350, ВФ-2, ВС-10Т, МПФ-1 ВК-200, эпоксидные клеи и др.
3.2. Технология ремонта деталей полимерными материалами
Восстановление деталей производится как химическими, так и физическими методами, которые включают разнообразные способы.
|
|
Одним из наиболее часто применяемых в практике способов химического метода является применение эпоксидных композиций для устранения таких дефектов как трещины, пробоины, раковины и других механических повреждений, а также для восстановления в них посадочных поверхностей под подшипники.
Технологический процесс восстановления деталей эпоксидными композициями состоит из следующих операций:
подготовка поверхностей деталей;
подготовка заплат;
подготовка композиций;
нанесение композиций;
отверждения композиций;
механической обработкой;
контроля.
Одной из основных операций определяющих качество ремонта деталей является подготовка поверхностей к нанесению эпоксидной композиции.
Подготовка поверхностей заключается в очистке поверхностей деталей до металлического блеска от загрязнений, ржавчины, краски, а также в придании в некоторых случаях поверхностям шероховатости для лучшего сцепления эпоксидной композиции с материалами деталей. Это достигается нанесением насечек зубилом, керном, обработкой крупнозернистыми абразивными кругами или нарезной рваной резьбой на цилиндрических поверхностях.
Подготовка к заделке трещин заключается в разделке трещины под углом 30-600С и зачистке поверхностей вдоль трещины шириной 20-25мм в обе стороны от трещины.
|
|
При подготовке пробоин необходимо притупить острые кромки и зачистить поверхность вокруг пробоины. Трещины и пробоины в нагруженных деталях (блоки цилиндров, картеры) предварительно завариваются, а затем для создания герметичности сварных швов заделываются эпоксидными композициями. На концах трещины на деталях, изготавливаемых из чугуна и алюминиевых сплавов, сверлятся отверстия диаметром 5-8мм. Для предотвращения вытекания композиции через отверстия, в них устанавливают асбестовые пробки, они должны быть утоплены на 2/3 глубины стенки детали.
Зачищенные поверхности тщательно обезжириваются ацетоном или другими легкоиспаряющимися растворами, а затем сушатся.
Подготовка заплат заключается в придании им требуемой формы, очистке и обезжиривании. В зависимости от нагруженности детали, характера повреждения заплаты могут изготавливаться из листового металла, стеклоткани или хлопчатобумажных тканей.
Металлическая заплата должна перекрывать пробоину на 10-20мм, зачистка и обслуживание ее производится аналогично подготовке металлических поверхностей деталей.
Заплаты из стеклоткани пропитывают в легколетучем органическом растворителе или прокаливают при 573-673К (300-400С). Стеклотканевая заплата накладывается на пробоину в несколько слоев.
Первый слой должен прикрывать кромки пробоины на 10-15мм, каждую предыдущую на 10-15мм. Общая толщина заплаты должна быть 5-6мм.
Каждый слой заплаты должен быть покрыт композицией. При необходимости при заделке трещин может накладываться заплата в один слой.
Например: Данный метод можно использовать при ремонте топливных баков при небольших повреждениях.
Приготовление композиций заключается в тщательном перемешивании компонентов. Смола марки ЭД-16 предварительно нагревается до 323-333К (50-600С), затем в нее вводят пластификатор ДБФ, который тщательно перемешивается со смолой в течение 10-12мин.
Затем в полученную смесь при перемешивании вводится наполнитель и продолжается перемешивание в течение 10-15мин.
Дозировка отвердителя должна точно соответствовать рецептуре состава. Жизнеспособность композиции после введения отвердителя зависит от типа отвердителя, массы композиции и температуры окружающей среды. Так при комнатной температуре жизнеспособность композиции массой 100г составляет:
для ПЭПА 30-40 мин (полиэтиленполиамин)
для АФ-2 10-15 мин (аминофенол).
Композиция наносится шпателем в два приема. Первый слой композиции следует тщательно втереть на подготовленную поверхность детали, а второй слой окончательно формирует валик высотой 2-3мм над поверхностью деталей с перекрытием трещины 8-10мм в обе стороны.
При наложении заплат из стеклоткани рекомендуется для уплотнения заплаты прикатать роликом каждый слой стеклоткани через полиэтиленовую пленку.
Отверждение композиции происходит как при комнатной температуре, так и при повышенных температурах.
Процесс отверждения состоит из четырех этапов:
а) начало отверждения;
б) схватывания композиции;
в) достижения наибольшей прочности соединения;
г) практически полного отверждения.
Время отверждения композиции с разными отвердителями по этапам приведено в инструкции.
Так для эпоксидной смолой ЭД-20 с полиэтиленполиамином время начала отверждения составляет 4 часа, время схватывания 6,5 час., время достижения наибольшей прочности соединения – 24 часа, а время полного отверждения 6-7 суток.
Это время отверждения композиции в тонком слое при комнатной температуре. Процесс отверждения можно ускорить подогревом. Подогрев должен быть равномерным при невысокой температуре. Целесообразно подогревать не композицию, а прилежащие слои металла.
Механическая обработка восстанавливаемого участка производится после отверждения композиции и заключается в зачистке от наплывов, снятия фасок. Зачистка производится напильниками, шлифовальными кругами и другими инструментами
При помощи клеев можно соединять в различном сочетании металлы, фрикционные материалы, пластмассы, стекло и др.; при этом обеспечивается герметичность соединения, устойчивость к воздействию смазочных масел, бензина, отсутствие внутренних напряжений.
К недостаткам клеевого соединения следует отнести низкую теплостойкость, недостаточную адгезию, поэтому при выборе клея необходимо учитывать материал склеиваемых деталей, температурные условия работы деталей сопряжения, характер и примерные значения нагрузки.
Например: при склеивании тормозных накладок к тормозным колодкам, так как эти детали работают в жестких условиях, когда на них воздействуют высокая температура и различные нагрузки, необходимо применять клей вс-10т.
3.3 Изготовление деталей из полимерных материалов
Основными способами изготовления деталей из полимеров и пластмасс являются:
1. Для реактопластов – прессование на гидравлических и механических прессах;
2. Для термопластов – литье под давлением, экструзия, вакуумное и пневматическое формование.
Технологический процесс прессования реактопластов осуществляется следующим образом.
В процессе прессования при нагревании пресс-материал приобретает пластичность, благодаря чему он заполняет все углубления полости пресс-формы. Затем на материал в пресс-форме воздействуют высоким давлением.
Спрессованное изделие выдерживают в пресс-форме под давлением до завершения процесса перехода смолы в отвержденное состояние. После этого давление снимается, и готовая деталь извлекается из формы после этого производится обработка заусенцев.
Например: Литьем под давлением как изготавливаются, так и восстанавливаются следующие детали:
вкладыши подшипников скольжения;
втулки рессор, коромысел;
шестерни, крыльчатки водяных насосов, шкивы;
оси блоков шестерен;
детали гидросистемы.
Технологический процесс литья под давлением состоит из следующих операций:
дозирование;
нагрева и расплавления полимера;
впрыска под давлением порции расплавленного полимера через сопло в сомкнутую форму;
размыкания и снятия детали из формы.
При изготовлении деталей способом прессования применяют экструзию, т.е. способ непрерывного выдавливания расплавленного термопластического материала через формообразующее отверстие в виде профиля того или иного сечения.
Вакуумное и пневматическое формование применяется для крупногабаритных деталей.
Сущность способа состоит в том, что листовые термопласты предварительно нагреваются до высокопластического состояния и укладываются в форму (или укладываются в форму до нагрева) и под воздействием вакуума или давления, лист плотно прилегает к стенкам формы. Затем производится охлаждение, извлечение детали из формы.
Дата добавления: 2018-08-06; просмотров: 1023; Мы поможем в написании вашей работы! |
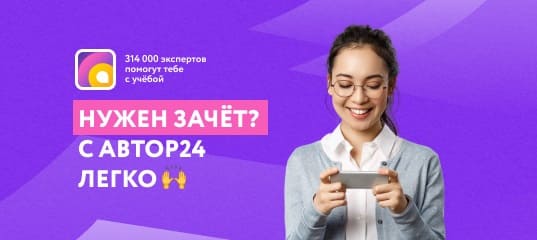
Мы поможем в написании ваших работ!