Восстановление автомобильных деталей гальваническими покрытиями .
Этот окислительно-восстановительный процесс носит название электролиза.
При электролизе катодом служит покрываемое изделие, а анодом – металлические пластины или стержни. Аноды могут быть растворимые и нерастворимые. Растворимые – выполняются из того же металла, который осаждается на детали.
Процесс электролитического осаждения любого металла подчиняется законам Фарадея:
QT = E I t
где QT – теоретическое количество вещества, выделившегося при электролизе; E – электрохимический эквивалент, г/А ч (это число граммов металла выделившегося на катоде при пропускании через электролит тока 1 А в течение 1 часа); I – сила тока, А; t – время электролиза, ч.
Одновременно с осаждением металла на катоде выделяется водород, а также протекают и другие побочные процессы, на что затрачивается часть электрического тока, поэтому действительная масса осажденного металла будет меньше теоретической, рассчитанной по закону Фарадея. Отношение практически полученного на катоде количества металла Мп к теоретически возможному называют катодным выходом металла по току, который выражают в процентах.
Отношение количества металла, практически растворенного на аноде, к теоретически возможному называют анодным выходом по току.
Условия электролизахарактеризуются составом и концентрацией электролита и режимом процесса. Режим характеризуется тремя основными показателями: кислотностью электролита (в г/л или в единицах водородного показателя рН); температурой электролита (в °С); катодной плотностью тока (в А/дм2).
|
|
Плотность тока – сила тока, приходящаяся на единицу площади поверхности электрода, А/дм2,
D = I/S,
где S – площадь поверхности электрода, дм2.
Технологический процесс получения гальванических покрытий складывается из подготовительных операций, процесса получения покрытий и заключительных операций.
К подготовительным операциям относят: механическую обработку (шлифование и др.) с целью придания правильной геометрической формы, удаления заусенцев, окалины и получения необходимой величины шероховатости; пескоструйную обработку и др.; обезжиривание – при помощи растворителей, синтетических моющих средств, химическим (в горячих щелочных растворах или растворах СМС: МС-6, МС-8, Лабомид-101, Лабомид-203) и электрохимическим способами (щелочными растворами в присутствии электрического тока, ультразвуковым способом.
К разновидности химического обезжиривания относят обезжиривание «венской известью» – смеси из окиси кальция (48%), окиси магния (49%) и кальцинированной соды (3%), разбавленной водой до кашеобразного состояния. «Венскую известь» можно заменить отходами карбида кальция от ацетиленового генератора или меловой кашицей, в состав которой входят мел (порошок) 1 кг, вода – 1 л, NaOH – 40 г.
|
|
Растворение и удаление оксидов обработкой химическим или электрохимическим способом называют травлением.
Химическое травление основано на растворении оксидов в кислотах или щелочах (в зависимости от вида металла). Черные металлы травят в водном растворе серной или соляной кислоты или их смесях.
Обычно применяют 15...25 % раствор серной или 10...20 % раствор соляной кислоты. При травлении в растворе серной кислоты его нагревают до 50...60 °С. Продолжительность процесса (30 мин и более) зависит от состояния поверхности детали, концентрации и температуры раствора.
Электрохимическое травление (декапирование) проводят в тех же ваннах, где происходит основной процесс получения покрытия; для этого к детали подключают плюс источника тока (деталь становится анодом), а анод на это время становится катодом.
После декапирования деталь выдерживают в ванне без тока в течение 0,5…1,0 мин, и поверхность детали подвергается травлению электролитом.
В процессе подготовки детали многократно промывают горячей и холодной водой.
|
|
Процесс получения покрытия происходит в электролите под действием электрического тока. По составу электролиты делят на три группы: хлористые, сернокислые и смешанные (сульфатно-хлористые). По температурному режиму электролиты делятся на горячие и холодные.
Методы осаждения покрытий
В зависимости от конструктивных особенностей восстанавливаемых деталей, применяют различные методы осаждения покрытий.
Вневанными методами наращивают поверхности крупногабаритных деталей сложной конфигурацией, поместить которые в ванну и изолировать неоткрываемые места затруднительно.
Вневанные методы обеспечивают значительное сокращение трудозатрат за счет исключения изоляционных и монтажных работ и применяются для наращивания отверстий под подшипники корпусных деталей, постелей под вкладыши блока двигателей, шеек коленчатых и др. валов.
Железнение, преимущества и недостатки, область применения.
Железнение занимает одно из ведущих мест среди прогрессивных способов восстановления деталей, которое отличается хорошими технико-экономическими показателями:
дешевизной применяемых исходных материалов;
высоким выходом металла по току (85-95%);
|
|
высокой скоростью осаждения металла (0,2-0,5мм/ч);
высокой износостойкостью и твердостью покрытия пластичностью;
возможностью нанесения осадков большой толщины, достигающей 0,8-1,2мм;
низкой себестоимостью восстановления, не превышающей 30-50% стоимости новой детали при одинаковой износостойкости.
Железнение целесообразно использовать при восстановлении изношенных деталей (наращивание до номинального или ремонтного размера) автомобилей, различного оборудования;
исправлении брака механической обработки;
упрочнении рабочих поверхностей деталей из малоуглеродистой и среднеуглеродистой сталей, не прошедших при изготовлении термической обработки;
покрытии пластинок твердого сплава для облегчения припайки их к резцам.
Таким образом, нами были рассмотрены технологический процесс наращивания железнением, который имеет хорошие технико-экономические преимущества и показатели, и распространен в практике ремонтных предприятий.
Хромирование, преимущества и недостатки, область применения.
Хромированная поверхность характеризуется:
высокой твердостью;
низким коэффициентом трения;
высокой жаростойкостью;
коррозийной устойчивостью;
высокой износоустойчивостью.
Хромирование в авторемонтном производстве может использоваться для следующих целей:
восстановления изношенных деталей автомобилей, различного оборудования, повышения износостойкости измерительного инструмента, калибров, режущего инструмента, пресс-форм, трущихся деталей машин, повышения отражательной способности зеркал, отражателей рефлекторов, защиты деталей от коррозии и т.д.
В настоящее время существуют различные варианты хромирования, например, хромо-алмазное покрытие, позволяющее существенно улучшить физико-механические свойства покрытия.
Производительность хромирования достигает 0,03мм/ч, а толщина покрытия 0,3-0,4мм. Вместе с тем, применяя хромирование, необходимо учитывать, что предел выносливости хромированных деталей снижается на 30-40%.
К недостаткам хромирования относятся:
-сравнительно низкая производительность процесса (0,03мм/ч) из-за малого значения Е – электрохимического эквивалента;
-невозможность восстановления деталей с большим износом (практически толщина осадка хрома не более 0,1мм на сторону);
-необходимость частой корректировки состава электролита нарушение соотношения хромового ангидрида и серной кислоты);
-сложность восстановления изношенных поверхностей крупногабаритных деталей;
-плохая смачиваемость, т.е. удержание смазки на поверхности детали.
Дата добавления: 2018-08-06; просмотров: 929; Мы поможем в написании вашей работы! |
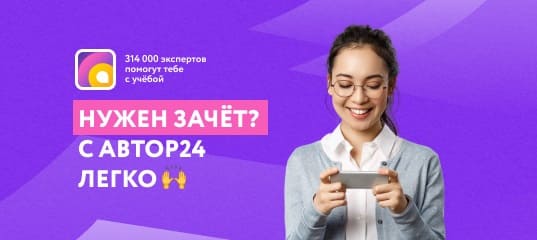
Мы поможем в написании ваших работ!