Технологияультразвуковой толщинометрии стенки резервуара
2.5.1УЗТ и сканирование ультразвуковуютолщинометрию с регистрацией рельефаконтролируемого сечения) производят для измерения толщины металла стенки резервуарас целью выявления коррозионных повреждений.
2.5.2На первом поясе резервуара УЗТ производится путем сканирования на высоте 200 ммот уторного узла. В случае обнаружения язвенных коррозионных повреждений листапроизводится дополнительное сканирование этого листа на высотах 100 мм и 300мм. Результаты контроля используются для проведения расчетов на прочность иустойчивость стенки резервуара.
2.5.3Подготовка поверхности к проведению УЗТ.
2.5.4 Непосредственно перед проведением измеренийповерхность стенки резервуара в месте замера толщины следует очистить от загрязнения,
снега, наледи и т.п. и протереть ее сухой чистой ветошью.
Впроцессе очистки поверхности недопустимы:
-повреждения антикоррозионного покрытия;
-повреждения поверхности основного металла.
Участокподготовленной для проведения измерений поверхности стенки резервуара должениметь размер не менее 50 мм в диаметре.
Присканировании ширина подготавливаемой зоны поверхности определяется конструкциейсканирующего устройства и должна быть указана в технологической карте.
2.5.5Проведение УЗТ.
2.5.6Произвести настройку толщиномера (дефектоскопа) в соответствии стребованиямиинструкции по его эксплуатации.
2.5.7Установить на поверхность контролируемого участка датчик толщи номераипроизвести измерения толщины стенки согласно инструкции по эксплуатацииприбора.
|
|
2.5.8При проведении сканирования скорость перемещения сканирующего устройства недолжна, превышать 20 мм/с.
Результаты контроля оформляются в виде Заключения в соответствии с приложениемД.
Технология ультразвукового контроля сварных соединений
2.6.1Ультразвуковойконтроль стыковых сварных соединений резервуаров и их участков после ремонтасваркой при номинальной толщине сваренных элементов от 5 до 28 мм включительно.
2.6.2 При ручном контроле следует применять контактные наклонные совмещенные илираздельно-совмещенные пьезопреобразователи, технические характеристики которыхв зависимости от толщины стенки контролируемого соединения приведены в таблице 5.
Таблица 5- Технические характеристики
Номинальная толщина стенки S, мм | Рабочая частота ПЭП f, ±10% МГц | Диаметр (ширина) пьез пластины ПЭП d, мм | Угол ввода a, ±2° | Стрела ПЭП k, мм, не более |
5,0<S£8,0 | 5,0 | 6,0 | 70/60* | 5-6 |
8,0<S£12,0 | 5,0 | 8,0 | 70/60* | 7-8 |
12,0<S£15,0 | 5,0 | 10,0 | 70/60* | 8-10 |
15,0<S£20,0 | 2,5 | 12,0 | 60 | 8-10 |
20,0<S£28,0 | 2,5 | 12,0 | 60 | 10-12 |
2.6.3 При использовании дефектоскопов с механизированными, полу автоматизированными и автоматизированными сканирующими устройствами характеристики ПЭП определяются конструкцией применяемого устройства при условии обеспечения просвечивания всего сечения контролируемого соединения.
|
|
2.6.4 Настройку параметров контроля следует выполнять на стандартном образце предприятия с угловыми отражателями (зарубками).
Перед проведением контроля следует выполнить подготовку сварного соединения к контролю, а именно:
- обеспечить доступ к сварному соединению для беспрепятственного сканирования около шовной зоны;
1, 2 - угловые отражатели; Д- длина образца (Д=140 мм при толщине образца до 20 мм, 160 мм при толщине образца 20<S£25 мм и 180 мм при толщине образца >25 мм)
Рисунок 3Стандартный образец предприятия с угловым отражателем (зарубкой) для настройки ультразвукового дефектоскопа:
2.6.5Подготовка сварного соединения к проведению контроля.
- при наличии на стенке резервуара антикоррозионного покрытия необходимо без его удаления и повреждения очистить околошовную зону сварного соединения пообе стороны от шва и по всей его длине от пыли, грязи, снега и других загрязнений и неровностей.
|
|
При ручном контроле ширина подготавливаемой зоны с каждой стороны шва должна быть не менее (2S´tga)+40мм, где S - толщина стенки в миллиметрах, a - угол ввода ультразвуковых колебаний в градусах угловых;
- при отсутствии на поверхности стенки резервуара, с которой осуществляют сканирование, антикоррозионного покрытия, необходимо выполнить механическую очистку поверхности около шовной зоны. Чистота поверхности после обработкидолжна быть не хуже Ra 6,3 (Rz 40);
- произвести маркировку контролируемых швов стенки резервуара. Нумерация вертикальных сварных швов и листов стенки резервуара ведется от монтажного шва№ 1 в направлении против часовой стрелки. Нумерация горизонтальных швов ведётся с первого нижнего.
2.6.6Типовая настройка диапазона развертки осуществляется следующим образом:
-разместить ПЭП на поверхности стандартного образца V2 и получить дваэхо-сигнала на расстояниях 50 и 125 мм;
-используя параметры управления разверткой дефектоскопа «Задержка развертки» и «Длительность развертки», установить полученные эхо-сигналы так, чтобы вершина эхо-сигнала, соответствующего 50 мм, совпадала с четвертым делением экрана, а вершина второго эхо-сигнала, соответствующего 2.6.7 Настройку глубиномера следует выполнить таким образом, чтобы с помощью дефектоскопа можно было определять координаты дефекта непосредственно в линейных единицах измерения расстояний (в миллиметрах). Настройка выполняется в соответствии с Инструкцией по эксплуатации дефектоскопа.
|
|
2.6.8Настройку строб-импульса следует выполнять на стандартном образце предприятия с угловыми отражателями (зарубками). Конструкция СОП приведена на рисунке4.125 мм, была совмещена с 10-мделением экрана (рисунок 4).
1- зондирующий импульс;2- эхо- сигнал, соответствующий расстоянию 50мм;
3- эхо- сигнал, соответствующий расстоянию 125 мм.
Рисунок 4-Настройка диапазона развертки экрана дефектоскопа:
Приконтроле соединений с различной толщиной свариваемых элементов настройкуследует выполнять для каждого из них.
2.6.9Типовая настройка строб-импульса осуществляется следующим образом:
а) при контроле прямым лучом:
-получить эхо-сигнал от нижней зарубки в СОП прямым лучом;
-установить на экране дефектоскопа строб-импульс таким образом, чтобы начало его находилось на 2-3 мм правее зондирующего импульса, конец был совмещен с задним фронтом эхо-сигнала от нижней зарубки (смотри рисунок 5), а его уровень составлял 40% высоты экрана.
Рисунок 5- Настройка строб-импульса и чувствительности при контроле прямым лучом.
б) при контроле однократно-отраженным лучом (смотри рисунок 6):
Рисунок 6-Настройка строб-импульсаичувствительности однократно отраженным лучом
-получить эхо-сигнал от нижней зарубки в СОП прямым лучом;
-установить на экране дефектоскопа строб-импульс таким образом, чтобы начало его совпадало с передним фронтом эхо сигнала от нижней зарубки в СОП, а его уровень составлял 40% высоты экрана;
-получить эхо-сигнал от верхней зарубки в СОП однократно отраженным лучом;
-установить на экране дефектоскопа строб-импульс таким образом, чтобы конец был совмещён с задним фронтом эхо-сигнала от верхней зарубки.
в)при контроле прямым и однократно-отраженным лучом за один проход (смотри рисунок 7):
-получить эхо-сигнал от верхней зарубки в СОП однократно отраженным лучом;
-установить на экране дефектоскопа строб-импульс таким образом, чтобы начало его находилось на 2-3 мм правее зондирующего импульса, конец был совмещен с задним фронтом эхо-сигнала от верхней зарубки, а уровень его составлял 40% высоты экрана.
Рисунок 7 -Настройка строб-импульса и чувствительности при контроле прямым и однократно отраженным лучом.
2.6.10Технология ручного контроля стыковых сварных соединений.
2.6.11 Контроль стыковых сварных соединений резервуара, не имеющего антикоррозионного покрытия, проводят в 2 этапа в следующей последовательности:
Этап 1:ВИК сварного соединения.
Этап 2: УЗК сварного соединения.
На этапе 1 проводят визуальный и измерительный контроль сварного соединения.
На этапе 2 выполняют ультразвуковой контроль.
2.6.12Контроль стыковых сварных соединений через антикоррозионное покрытие проводят в4 этапа в следующей последовательности:
Этап1: ВИК сварного соединения и антикоррозионного покрытия в зоне перемещения ПЭП (в зоне сканирования).
Этап2:УЗК сварного соединения с предварительной корректировкой чувствительности.
Этап3: Измерение толщины покрытия в месте обнаружения дефекта.
Этап4: Окончательная корректировка чувствительности и определение характеристик дефекта.
На этапе 1 проводят визуальный и измерительный контроль сварного соединения, антикоррозионного покрытия в зоне перемещения ПЭП (в зоне сканирования).
На этапе 2 выполняют контроль сварного шва с предварительной корректировкой чувствительности.
На этапе 3 измеряют толщину антикоррозионного покрытия в месте расположения ПЭПпри обнаружении дефекта.
На этапе 4 в зависимости от толщины и вида покрытия производят окончательную корректировку чувствительности дефектоскопа
2.6.13Контроль сварных соединений осуществляют путем перемещения (сканирования) ПЭП (см. рисунок 6) по поверхности около шовнойзоны параллельно контролируемому шву с одновременным возвратно-поступательным движением в направлении, перпендикулярном ему. При сканировании следует поворачивать ПЭП в обе стороны от заданного направления движения на угол 10-15°.
2.6.14 Величина продольного (вдоль шва) шага сканирования недолжна превышать половины диаметра (ширины) (см. таблица 3)пьез пластины преобразователя. Сканирование следует осуществлять с обеих сторон усиления шва.
2.6.15 Контроль сварных соединений с толщиной свариваемых элементов до 15 мм выполняют пьез преобразователямис различными углами ввода (см. табл.3) за два прохода. При этом нижнюю часть шва контролируют прямым лучом, а верхнюю - однократно отраженным.
Контроль сварных соединений с толщиной свариваемых элементов более 15 мм выполняют одним ПЭП прямым и однократно отраженным лучом за один проход.
2.6.16Особенности контроля стыковых сварных соединений с использованием дефектоскопа с механизированным, полу автоматизированным или автоматизированным сканирующим устройством.
2.6.17Выполнить подготовку поверхности соединения к проведению контроля. Ширина подготавливаемой зоны определяется конструкцией сканирующего устройства и должна быть указана в операционной технологической карте.
2.6.18 Контроль стыковых сварных соединений резервуара, не имеющего антикоррозионного покрытия, следует выполнять в следующей последовательности:
Этап 1: ВИК сварного соединения.
Этап 2: УЗК с применением сканирующего устройства.
На этапе 1 проводят визуальный и измерительный контроль сварного соединения и около шовной зоны в пределах зоны сканирования.
На этапе 2выполняют ультразвуковой контроль с применением сканирующего устройства.
2.6.19 Контроль стыковых сварных соединений через антикоррозионное покрытие следует выполнять в следующей последовательности:
Этап 1: ВИК сварного соединения и антикоррозионного покрытия в зоне перемещения ПЭП (в зоне сканирования).
Этап 2: УЗК с применением сканирующего устройства и предварительной корректировкой чувствительности.
Этап 3: Измерение толщины покрытия в месте обнаружения дефекта.
Этап 4: УЗК с применением дефектоскопа общего назначения и ручного сканирования.
На этапе 1 проводят визуальный и измерительный контроль.
На этапе 2выполняют контроль сварного шва с корректировкой чувствительности +2 дБ на наличие покрытия и +2 дБ на наличие нефти и/или парафиновых отложений (если они есть).
На этапе 3 измеряют толщину антикоррозионного покрытия в месторасположения ПЭП при обнаружении дефекта.
На этапе 4 с помощью дефектоскопа общего назначения и ручного сканирования производят измерение характеристик обнаруженного дефекта с корректировкой чувствительности в зависимости от толщины и вида покрытия.
2.6.20Контроль на этапе 2 выполняют путем перемещения сканирующего устройства вдоль шва в соответствии с технологической картой для этого оборудования. После установки сканирующего устройства на начальную точку его перемещают до конечной точки сканирования со скоростью не более 1 м/мин.
Вовремя контроля допускаются остановки, плавное изменение скорости, а так же корректировка положения сканирующего устройства относительно оси сварного соединения.
2.6.21 После завершения сканирования проводят просмотр результатов контроля, оценку качества и предварительную обработку данных.
2.6.22По результатам обработки данных отмечают участки сварных швов с выявленными дефектами и участки, на которых были зафиксированы отсутствие контакта и превышение скорости перемещения. Такие участки подвергают повторному контролю.
2.6.23 На этапе 3 в местах, где по результатам контроля с применением сканирующего устройства было зафиксировано наличие дефектов, выполняют измерение толщины антикоррозионного покрытия.
2.6.24На этапе 4 на участках, где по результатам контроля с применением сканирующего устройства было зафиксировано наличие дефектов и измерена толщина покрытия, выполняют ручной контроль с помощью дефектоскопа общего назначения измерение характеристик этих дефектов.
2.6.25Если по результатам автоматизированного контроля выявленный дефект является недопустимым, этом имеет положительное значение более 2 дБ, то ручной контрольное проводят и разбраковку дефектов проводят по результатам АУЗК.
Техническое заключение
должно включать следующие данные:
- наименование организации, выполняющей обследование, фамилии, должности исполнителей;
- место расположения, инвентарный номер, тип и геометрические размеры по проекту резервуара, номер проекта;
- дата ввода в эксплуатацию, даты очередных обследований и ремонтов;
- виды дефектов, образовавшихся в процессе эксплуатации;
- краткую техническую характеристику с обязательным указанием полных данных примененного при строительстве материала, технологический и температурный режим работы, вид хранимого продукта;
- вид обследования (полное или частичное);
- проектные и фактические толщины листов кровли, стенки, понтона и днища;
- виды аварий, количество проведенных ремонтов и краткое описание;
- результаты внешнего осмотра и измерений;
- результаты неразрушающих методов контроля сварных соединений;
- результаты измерений геометрической формы стенки и нивелирования основания резервуара и отмостки;
- карты вертикальных разрезов днища (при значительной неравномерной просадке);
- результаты механических испытаний, металлографического и химического анализов основного металла и сварных соединений;
- расчет высоты налива продукта в случае, если фактическая толщина листов в одном из поясов стенки меньше минимально допустимой;
- расчет остаточного ресурса резервуара;
- заключение о состоянии резервуара и рекомендации по обеспечению его надежной эксплуатации, ремонтопригодности;
- предложения по выполнению ремонтных работ и режима дальнейшей эксплуатации.
2.7.1 Заключение и выводы должны быть четкими и конкретными, не допускающими двояких толкований.
2.7.2 Оформленное заключение подписывается исполнителями, проверяется и подписывается руководителем службы дефектоскопии.
2.7.3 В тех случаях, когда круг вопросов, подлежащих решению, выходит за пределы компетенции специалистов, выполнявших дефектоскопию, привлекаются специалисты соответствующего профиля с включением их мнения (расчетов) в заключение или с оформлением самостоятельного документа.
2.7.4 Оценку технического состояния резервуаров проводят только при наличии следующих данных:
- поверочного расчета на прочность с учетом хрупкого разрушения, выполненного по результатам измерения толщины листов стенки;
- фактической толщины листов стенки, которые должны быть в пределах нормативных величин. Если толщина листов каких-либо поясов стенки ниже предельно допустимой, то следует провести расчет на снижение предельного эксплуатационного уровня нефтепродукта;
- результатов проведенной дефектоскопии основного металла и сварных соединений;
- результатов проверки качества основного металла и сварных соединений. Механические свойства и химический состав основного металла и сварных соединений должен соответствовать требованиям проекта, стандартов и технических условий;
- результатов контроля состояния оснований резервуаров;
- расчета остаточного ресурса с учетом коррозионного износа и изменения механических свойств металла.
2.7.5 Предельно допустимую минимальную толщину отдельных листов стенки резервуаров, находящихся в эксплуатации, показана в таблице 6.
Таблица 6-Предельная минимальная толщина листов стенки резервуара, изготовленного из стали ВСТ3
Вместимость резервуара, м3 | Марка стали | Номер пояса | |||||||
1 | 2 | 3 | 4 | 5 | 6 | 7 | 8 | ||
100 | ВСТ3 | 2,0 | 2,0 | 1,5 | 1,5 | ||||
200 | ВСТ3 | 2,0 | 2,0 | 1,5 | 1,5 | ||||
400 | ВСТ3 | 2,5 | 2,0 | 1,5 | 1,5 | ||||
700 | ВСТ3 | 3,0 | 2,5 | 2,0 | 2,0 | 1,5 | 1,5 | ||
1000 | ВСТ3 | 3,5 | 3,0 | 2,5 | 2,5 | 2,0 | 2,0 | 1,5 | 1,5 |
09Г2С | 3,2 | 2,4 | 2,4 | 2,0 | 2,0 | 2,0 | 1,5 | 1,5 | |
2000 | ВСТ3 | 5,5 | 5,0 | 4,0 | 3,5 | 3,0 | 3,0 | 2,0 | 2,0 |
09Г2С | 4,3 | 4,2 | 3,8 | 3,2 | 2,8 | 2,0 | 2,0 | 2,0 | |
3000 | ВСТ3 | 7,0 | 6,0 | 5,0 | 4,0 | 3,5 | 2,5 | 2,0 | 2,0 |
09Г2С | 5,2 | 4,8 | 4,5 | 3,5 | 3,0 | 2,0 | 2,0 | 2,0 | |
5000 | ВСТ3 | 7,8 | 6,8 | 5,9 | 4,8 | 3,8 | 2,7 | 2,0 | 2,0 |
09Г2С | 6,0 | 5,3 | 4,5 | 3,9 | 3,5 | 2,5 | 2,0 | 2,0 | |
10000 | ВСТ3 | 10,5 | 10,0 | 8,5 | 7,0 | 5,5 | 4,0 | 3,0 | 3,0 |
09Г2С | 9,0 | 8,0 | 7,0 | 6,0 | 4,8 | 3,0 | 3,0 | 3,0 | |
20000 | 09Г2С | 12,0 | 11,0 | 10,0 | 9,0 | 8,0 | 6,0 | 6,0 | 6,0 |
Примечания:
1 Вычисления производились из расчета плотности нефтепродукта 0,008 кН/м3.
2 Толщина верхних поясов принята из условия обеспечения их устойчивости.
2.7.6 Предельно допустимый износ листов кровли и днища по измерениям наиболее изношенных частей не должен превышать 50 % проектной величины.
2.7.7 Предельно допустимый износ несущих конструкций кровли (ферм, прогонов, балок, связей), а также окрайков днища не должен превышать 30 % проектной величины.
Дата добавления: 2018-06-27; просмотров: 1160; Мы поможем в написании вашей работы! |
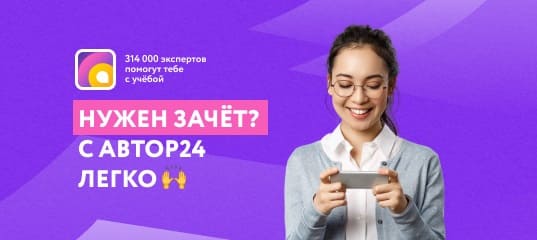
Мы поможем в написании ваших работ!