Технология ультразвукового контроля металла стенки и сварныхсоединений резервуаров
2.4.1Организации, выполняющие работы по ультразвуковому контролю стенки и сварных соединений РВС (П., ПК), должны отвечать требованиям к подрядным организациям, проводящим техническую диагностику.
2.4.2К работам по ультразвуковому контролю основного металла стенки и сварных соединений РВС (П., ПК) допускаются лица, прошедшие курс обучения и успешно выдержавшие квалификационные испытания. Они должны быть аттестованы на I, II или III уровень квалификации по ПБ03-440-02 и иметь действующие удостоверения установленной формы в соответствии с применяемым методом контроля.
2.4.3 Организации и персонал, выполняющие работы по контролю и диагностике резервуаров, должны отвечать требованиям промышленной безопасности.
Требования к средствам контроля:
2.4.4 При проведении ультразвуковой толщинометрии (УЗТ) металла стенки РВС должны применяться УЗ толщин меры или дефектоскопы, позволяющие измерять толщину металла до 30 мм с погрешностью не более 2% от номинальной толщины листа.
2.4.5 При наличии тонко пленочного антикоррозионного покрытия толщиномеры(дефектоскопы) должны обеспечивать возможность проведения измерений толщины металла без снятия покрытия при его толщине до 600 мкм.
2.4.6Для сканирования должны применяться толщиномеры или дефектоскопы, позволяющие регистрировать рельеф контролируемого сечения в заданном диапазоне толщин.
2.4.7 Для ультразвукового контроля сварных соединений, а также участков сварных соединений и металла стенки после ремонта, следует применять импульсные ультразвуковые дефектоскопы общего назначения, имеющие динамический диапазон экрана не менее 20 дБ.
|
|
2.4.8 Контроль может осуществляться как в ручном варианте, таки с применением механизированных, полу автоматизированных и автоматизированных сканирующих устройств.
2.4.9Для проверки и настройки аппаратуры (дефектоскопов, толщиномеров, пьез преобразователей), определения и настройки параметров контроля следует применять стандартные образцы (СО) по ГОСТ 14782
2.4.10Выбор типа СО и конструкции СО определяется технологическими параметрами настройки аппаратуры и выполнения контроля.
Настройку дефектоскопов с механизированными сканирующими устройствами, полу автоматизированных и автоматизированных установок (дефектоскопов) следует производить по специальным методикам, разработанным для этого оборудования.
2.4.11В качестве мерительного инструмента, используемого для разметки контролируемых элементов и измерения характеристик выявленных дефектов, следует применять масштабные линейки, штангенциркули, мерительные пояса и универсальные шаблоны сварщика, обеспечивающие измерение линейных размеров с точностью ±0,5 мм.
|
|
2.4.12Аппаратура и оборудование, применяемые для контроля, должны быть снабжены технической документацией, предусмотренной изготовителем и входящей в комплект поставки (технические паспорта, формуляры, инструкции по эксплуатации).
2.4.13Аппаратура и оборудование, применяемые для контроля, должны быть сертифицированы, проверены, аттестованы или откалиброваны в установленном порядке. В паспортах должны быть сделаны соответствующие записи о первичной и периодических поверках (аттестации, калибровке).
2.4.14 Для обеспечения акустического контакта следует применять специальные контактные смазки, в том числе, специализированные пасты, гели и т.п. отечественного и зарубежного производства.
2.4.15Требования к состоянию антикоррозионного покрытия.
2.4.16Покрытие должно иметь однородную поверхность без пропусков и видимых дефектов, в т.ч. наплывов, посторонних вкраплений и т.п., которые могли бы привести к нарушению акустического контакта и препятствовать перемещению.
2.4.17 Организация работ.
Для проведения контроля разрабатывают операционные технологические карты, которые должны содержать:
- наименование объекта контроля,
|
|
- перечень НТД, на основании которых осуществляется контроль конструктивных элементов этого объекта,
- сведения о конструкции контролируемого элемента и его параметрах
(толщина стенки, наличие антикоррозионного покрытия, тип разделки кромок сварного соединения и др.),
- требования к подготовке поверхности к контролю,
- схемы и параметры контроля, идентификационные признаки выявляемых дефектов и ложных индикаций,
- перечень и очередность выполнения операций по подготовке и проведению контроля, а также операций по обеспечению требований безопасности,
- порядок обработки результатов контроля и оценки качества проконтролированного элемента.
2.4.18Операционные технологические карты должны быть разработаны специалистами поУЗ контролю не ниже II-го уровня квалификации, подписаны разработчиком и утверждены техническим руководителем предприятия, выполняющей работы подиагностированию на данном объекте.
2.4.19В состав бригады (звена) по проведению контроля должно входить не менее двух человек. При этом, хотя бы один из них должен иметь II-й уровень квалификации (или выше) специалиста по ультразвуковому контролю.
2.4.20 Перед началом контроля специалист, осуществляющий контроль, должен:
|
|
- получить задание на контроль с указанием расположения подлежащего контролю участка стенки или сварного соединения;
- ознакомиться с паспортом резервуара для определения типа антикоррозионного покрытия, нанесенного на стенку резервуара, как с внутренней, так и с внешней стороны;
- ознакомиться с результатами предшествующего контроля;
- ознакомиться с операционными технологическими картами контроля проверяемого элемента;
- убедиться в отсутствии недопустимых наружных дефектов;
- при контроле сварных соединений, а также участков стенки резервуара и сварных швов, отремонтированных с применением сварки - ознакомиться с конструкцией и особенностями технологии выполнения сварных соединений и наплавок.
Дата добавления: 2018-06-27; просмотров: 485; Мы поможем в написании вашей работы! |
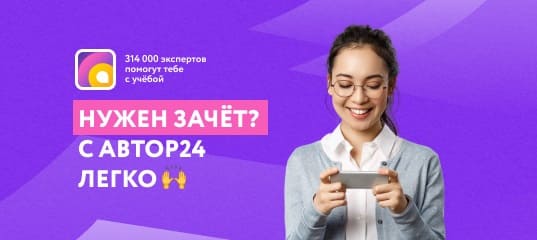
Мы поможем в написании ваших работ!