Выбор “базовой” части бурильной колонны.
В работе [5], посвященной выбору оптимальных сочетаний диаметров нефтепромысловых труб (и не только бурильных) и скважины, эта задача исследована достаточно детально на примере одноразмерных бурильных колонн без КНБК и долота.
Показано, что уровень оптимальности размеров труб следует оценивать исходя из следующих требований:
- обеспечение минимальных значений гидродинамических давлений при спуске (подъеме);
- минимизация общих (суммарных) гидравлических потерь давления при промывке (потерь в трубах рв и потерь в заколонном пространстве ркп);
- минимизация потерь давления в заколонном пространстве ркп при промывке скважины.
Перечисленные требования противоречивы, поэтому решение задачи сводится к поиску оптимального (компромиссного) варианта.
В работе [5] показано, что варианту сочетания диаметров бурильных труб dтр и скважины D, при котором достигается минимум суммарных потерь давления при промывке рп, почти точно соответствует самый неблагоприятный с точки зрения спуска колонн вариант с максимумом ргд. Оказалось, что зависимость ргд=f(dтр /D), если ргд в численном эксперименте определять с учетом поступления жидкости в трубы при спуске, имеет явно выраженный максимум, близко совпадающий с минимумум зависимости рп = f(dтр/D) при промывке. Было установлено, что при роторном бурении оптимальный компромисс для большинства типоразмеров бурильных труб достигается при величинах dтр/D=0,52...0,57.
|
|
Ниже излагаются результаты новых численных экспериментов, которые следует рассматривать как развитие изложенных в работе [5] исследований.
Расчеты выполнены только для скважины диаметром 215,9 мм, в которой могут разместиться практически все размеры стандартных бурильных труб, включая трубы диаметром 168,3 мм. В качестве “представителей” стандартного ассортимента труб выбраны трубы ТБВК-102,6*9; ТБПВ-114,3*9, ТБПК-127*9,2; ТБВК-139,7*10; СБТВ-168,3*10. На рис. 18.11 приведены результаты расчетов потерь давления при промывке скважины. Видно, что область минимума суммарных потерь давления приходится на интервал диаметров 135...140 мм, в котором располагается стандартный размер 139,7 мм. Из рис. 18.12, где те же данные показаны в относительных величинах, следует, что при использовании труб ТБВК-139,7*10 суммарные потери минимальны (они взяты за единицу), но потери давления в заколонном пространстве составляют около 30% от суммарных потерь давления и существенно превышают потери в случае использования труб меньшего диаметра.
Рис. 18.12. Влияние относительного диаметра бурильных труб на потери давления рп и ркп при промывке (условия расчета те же, что на рис. 18.11):
I - потери давления рп ; II - потери давления ркп . |
Рис. 18.13 иллюстрирует влияние диаметра бурильных труб на увеличение гидродинамического давления при спуске труб открытой и закрытой (“с обратным клапаном”) колонны. За 100% взяты давления при использовании труб диаметром 102,6 мм, когда закрытие труб практически не влияет на давление в скважине. Оказалось, что интенсивный рост давлений происходит начиная с диаметра 140 мм и более. Особенно интенсивно возрастает давление при спуске закрытых колонн.
На рис. 18.14 показано влияние изменения диаметров труб (в пределах перечисленного ассортимента) на эквивалентную плотность раствора при промывке. Приведенные данные полностью подтверждают сформулированные выше выводы. Обращает на себя внимание тот факт, что, начиная с диаметра 140 мм, особенно опасным является спуск с промывкой.
Обобщая изложенное можно утверждать, что оптимальное соотношение диаметра труб в “базовой” части бурильной колонны и диаметра скважины располагается в границах 0,52...0,58. При dбт/D < 0,52 существенно возрастают рп, а область dбт/D > 0,57 заведомо не технологична и должна быть отвергнута, поскольку совместно увеличиваются ркп и рп . Если иметь в виду скважину диаметром 215,9 мм, то бурильные трубы диаметром 139,7 мм и легкосплавные трубы диаметром 147 мм могут стать причиной осложнений и совершенно не допустимы к применению.
|
|
Рис. 18.13. Сравнение давлений при спуске открытой и закрытой колонн (условия расчета те же, что на рис. 18.11): I - открытая колонна; II - закрытая колонна. |
Обобщая изложенное можно утверждать, что оптимальное соотношение диаметра труб в “базовой” части бурильной колонны и диаметра скважины располагается в границах 0,52...0,58. При dтр/D < 0,52 существенно возрастают рп, а область dтр/D > 0,57 заведомо не технологична и должна быть отвергнута, поскольку совместно увеличиваются ркп и рп . Если иметь в виду скважину диаметром 215,9 мм, то бурильные трубы диаметром 139,7 мм и легкосплавные трубы диаметром 147 мм могут стать причиной осложнений и совершенно не допустимы к применению.
Выше, в разделе 18.3 (рис. 18.3), в качестве примера было проанализировано влияние на величину критерия промывки J различных по диаметру бурильных труб колонн, но “несущих” одни и те же КНБК.
Анализ показал, что для условий численного эксперимента бурильная колонна, составленная на основе труб ТБВК-139,7, явно уступает колоннам, составленным из труб меньшего диаметра. Неожиданно выяснилось, что применение труб ТБПВ-114,3 более эффективно по сравнению с трубами ТБПК-127 до глубины 2750 м, а при больших глубинах - наоборот. Разумеется, такой вывод справедлив только для данных конкретных условий бурения. Поэтому правомернее говорить не только о выборе оптимальных типоразмеров бурильных труб для данной скважины, но и о выборе компоновочного варианта колонны в целом.
|
|
Рис. 8.14. Влияние диаметра бурильных труб на эквивалентную плотность раствора при спуске: I - открытых труб; II - закрытых труб; III - с промывкой с расходом жидкости 0,02 м3/с. |
Дело в том, что на выбор решения, кроме диаметра труб, влияет ряд факторов:
- диаметр соединения (замка), от которого зависят потери давления в заколонном пространстве;
- конструкция замкового соединения, от чего зависит относительная величина гидравлических потерь, приходящаяся на соединение труб;
- конструкция скважины (длина обсаженной части ствола, внутренний диаметр обсадных труб);
- наличие сужений ствола и каверн;
- плотность и реологические параметры бурового раствора;
- технические возможности насосной группы в отношении создания и поддержания в течение всего долбления необходимого давления.
Анализ показывает, что нет правильной для всех случаев методики решения по выбору оптимальной конструкции бурильных колонн по косвенным признакам, кроме самых общих рекомендаций. Решение может быть найдено только путем перебора различных вариантов. Оптимальным будет считаться тот (или те), который обеспечивает при всех прочих равных условиях достижение самых высоких значений J по всем интервалам бурения.
В глубоком бурении используются три типа трубных колонн: бурильные, обсадные и колонны насосно-компрессорных труб (лифтовые колонны).
При турбинном бурении оправдано стремление передать на забой гидравлическую мощность с минимальными потерями в циркуляционной системе. А это делает обоснованным некоторое стремление к более высоким отношениям dтр/D (но не более 0,67). Для случая применения забойных двигателей рекомендуется в пределах от 0,56 до 0,62.
В итоге получается, что при роторном бурении долотами 215,9 мм следует пользоваться трубами не более 114…127 мм. При турбинном – трубами 127…139,7 мм. Применение труб диаметром 147 мм следует всячески ограничивать. Такой вывод справедлив только для долот диаметром 215,9 мм.
Аналогичные расчеты выполнены и для обсадных и для насосно-компрессорных труб, у которых диаметры соединительных муфт отличаются от диаметров самих труб в меньшей степени, чем у бурильных труб. По этой причине несколько смещаются величины dопт, при этом характер зависимостей не меняется.
При выборе диаметров обсадных труб практически не учитываются гидродинамические условия. Другое дело – насосно-компрессорные трубы, при использовании которых имеют конкретное значение все перечисленные ранее гидродинамические параметры (критерии). Например, следует учитывать величину dтр при выборе способа промывки. Если dтр/D > 0,6, то лучше промывку скважины осуществлять методом “обратной” промывки. Тогда в роли ркп “выступят” потери в трубах, и избыточное давление на пласт будет меньше, чем при “прямой” промывке.
19. Оптимизация режима промывки скважины с учётом фактора "утяжеления" восходящего потока в заколонном
пространстве выбуренной породой.
До сих пор принималось, что плотности буровой промывочной жидкости в трубах и в заколонном пространстве (как и другие параметры) совершенно одинаковы. Словом, считали, что рассматривается промывка без бурения, когда скважина промывается одной и той же жидкостью на всех участках циркуляционной системы скважины.
В то же время придётся признать, что промывка во время бурения (углубления скважины) сопровождается «утяжелением» жидкости в заколонном пространстве выбуренной породой, и средняя плотность восходящей промывочной жидкости будет больше плотности закачиваемой в трубу жидкости.
Предположим, что механическая скорость бурения долотом диаметром 295,3 мм при расходе жидкости 0,035 м3/с составила 50 м/час. Если средняя плотность породы равна 2500 кг/м3, а исходная плотность жидкости – 1200 кг/м3, то средняя плотность жидкости ρсм в заколонном пространстве во время бурения составит около 1240 кг/м3. Разница, как видим, существенная. Увеличение подачи насосов Q уменьшит эту разницу вследствие того, что концентрация шлама в растворе уменьшится. Это, в частности, означает, что изменение Q непосредственно влияет на гидростатическое давление на забой (через плотность смеси ρсм). С другой стороны, увеличение или уменьшение Q изменяет потери давления в заколонном пространстве. Как видим, вопрос представляется не таким уж простым и требует специального рассмотрения.
19.1. Подъём выбуренной породы потоком жидкости
в заколонном пространстве.
Если скважина промывается вязко-пластичной жидкостью, то можно считать, что твёрдые частицы, характерный (эквивалентный) размер которых dэ:
, (19.1)
где q - статическое напряжение сдвига бурового раствора,
Кф - коэффициент формы,
ρп - плотность породы,
ρ- плотность бурового раствора,
будут двигаться со скоростью, равной скорости восходящего потока в данной точке сечения заколонного пространства. Твёрдые частицы большего диаметра начнут “оседать” в восходящем потоке (по отношению к жидкости), и скорость подъёма их будет меньше скорости жидкости, окружающей частицу. Но в разных точках сечения скорости, как известно, разные. Они равны нулю на стенке скважины и на наружной поверхности трубы. В центральной части кольцевого пространства (если трубы расположены строго концентрично относительно скважины) скорость максимальна. В отличие от трубы при структурном режиме потока в затрубном пространстве образуются два градиентных кольцевых слоя: один между трубой и кольцеобразным стуктурным ядром, а другой - между ядром и стенкой скважины. Следовательно, твердые частицы, оказавщиеся в ядре, будут подниматься быстрее, а те частицы, которые случайно оказались либо у поверхности трубы, либо у стенки скважины, отстанут от первых и в какой-то момент даже могут оседать, пока не окажутся так же случайно втянутыми в ядро или в зоны, прилегающие с внутренней стороны или с наружной стороны к структурному ядру. Это говорит о том, что процесс транспортировки шлама имеет весьма своеобразный характер даже при структурном движении. При турбулентном режиме движения скорости потока по сечению не так сильно отличаются между собой, как это имеет место при структурном режиме. Поэтому и твердые частицы одинакового размера dэ будут двигаться (по отношению к скважине) с близкими скоростями.
Фракционный состав выбуренной породы, "поставляемой" забоем восходящему потоку, охватывает очень широкий спектр размеров и форм: от сотых долей до десятков миллиметров; от частиц, которые условно можно отнести к круглым, до пластинчатых, длина которых кратно больше поперечных размеров частицы. Ясно, что частицы, эквивалентный размер которых, найденный по формуле:
, (19.2)
где V- объем частицы, диаметр которой меньше dэ, найденого по формуле (5.1), будут двигаться вместе с потоком, не отставая от него. Другие же частицы будут двигаться со скоростью, которая заведомо меньше скорости в том месте сечения потока, где они случайно оказались. Все это означает, что частицы больших размеров отстанут от частиц меньших размеров. Концентрация частиц большего размера в нижней части скважины окажется, естественно, больше, чем в среднем по стволу.
Существует немало методик определения относительной скорости движения твердой частицы в восходящем потоке жидкости. Приведем одну из них.
В структурном потоке (ламинарном) ВПЖ среднюю скорость оседания частиц можно найти по формуле:
, (19.3)
где
, (19.4)
. (19.5)
Критерий (параметр) Ar- критерий Архимеда.
При турбулентном режиме движения жидкости средняя скорость оседания частиц определяется по формуле
, (19.6)
а максимальные размеры частиц можно найти по приближенной формуле:
dэ = 0,002+0,037Dд. (19.7)
В этой формуле игнорируется влияние, например, осевой нагрузки или скорости вращения на dэ.
Логично увязывать размер частиц, образующихся при бурении не с диаметром долота, а с проходкой долота за один оборот. Для определения dэ, можно предложить формулу:
dэ=30vм/n, (19.8)
где vм - скорость механического бурения, м/час;
n – скорость вращения долота, об/мин.
При этом dэ получается в мм.
К этой формуле следует относиться как к весьма ориентировочной, приближенной. Она может исказить результат (в сторону занижения) при усталостном режиме разрушения. С другой стороны, она может завысить dэ при высоких скоростях бурения долотами с большим скольжением зубьев. Очевидно и то, что dэ не может превысить высоту зубьев шарошки.
Расчеты показывают, что формулы (19.3) и (19.6) дают завышенные результаты. Опыт свидетельствует, что при скоростях восходящего потока 0,10…0,15 м/с наблюдается устойчивый подъем частиц шлама в восходящем потоке ВПЖ.
Нужно учесть и тот неоспоримый факт, что трубы всегда прижаты к стенке скважины и канал для транспорта шлама всегда имеет серповидную форму, а поток периодически обтекает замки (муфты), где подвергается интенсивному перемешиванию.
Если обобщить сказанное выше, то можно заключить, что невозможно количественно определить тот так называемый расход витания Qвит при котором все частицы "повиснут" в заколонном пространстве. Такой расход существует только для частиц одного размера. Можно только говорить о некоторой условной скорости потока в заколонном пространстве vо.кп, меньше которой большинство частиц останутся в зоне долота. Для каждого размера, режимы движения этой скорости будут разными. Для ВПЖ меньше, чем для технической воды. Ориентировочно можно принять для ВПЖ с τо ≥ 3Па vо.кп= 0,10…0,12 м/с. Для воды - vо.кп= 0,15…0,20 м/с. Этим скоростям будут соответствовать и условные расходы Qо, при которых частицы не могут подниматься по стволу скважины.
Это значит, что эффективный танспорт шлама возможен только при Q >Qо.
19.2. Влияние выбуренной породы, поступающей в скважину
в процессе бурения, на давления при промывке.
Представим себе, что за время наблюдения t долотом пройден интервал от глубины Lо, при этом проходка составила h м (рис. 19.1). За время от начала бурения жидкость успеет подняться на высоту
, (19.9)
где ƒкп – площадь сечения кольцевого пространства.
Выбуренная порода "отстанет" от жидкости и поднимется за это же время только на высоту
, (19.10)
где Qо- усредненный (эквивалентный) расход витания.
Концентрация шлама (объёмная) в столбе раствора высотой H составит:
, (19.11)
где vм- скорость механического бурения.
Плотность смеси раствора и шлама будет равна:
ρсм=φρп+(1-φ)ρ, (19.12)
где ρп- плотность выбуренной породы.
Пока "грязный" раствор не достигнет устья, давление на забой будет равно:
рзаб=ρсмgH+ρg(L-H)+ркп , (19.13)
где ркп – потери давления в заколонном пространстве.
Давление на насосе выразится уравнением:
рн=рпот+ρсмgH-ρgH, (19.14)
где рпот – сумма всех потерь давления, в циркуляционной системе, включая долото, обвязку и турбобур. Преобразуем формулу (19.12) к виду:
ρсм=ρ+φ(ρп-ρ). (19.12)'
Уравнение (19.13) с учетом (19.12)' целесообразно представить в виде:
pзаб= ρgL- ρgH+ ρgH+ φ(ρп-ρ) gH+pкп, (19.13)'
Преобразуем аналогично и уравнение (19.14):
pн=[ρ+φ(ρп-ρ)gH-ρgH+ pпот=
ρgH+φ(ρп-ρ)gH-ρgH+pкп=
φ(ρп-ρ)gH+pпот (19.14)'
Подставим в (19.13)' и (19.14)' выражения для φ и H из (19.10) и (19.11):
, (19.15)
, (19.16)
Формулы (19.15) и (19.16) описывают изменение рзаб и рн соответственно в начале долбления, пока "шламовый" поток не дошел до устья (H<L).
При H=L, когда "грязный" раствор достигнет устья скважины, формулы (19.15) и (19.16) примут вид:
, (19.17)
. (19.18)
Как видим, рзаб и рн являются функцией Q, vм и потерь давления pкп и pпот.
19.3. Оптимизация промывки скважины с учетом фактора
"утяжеления" раствора выбуренной породой.
Предположим, что в заколонном пространстве движется ВПЖ и режим движения при любом значении Q структурный. Тогда формула (19.18) примет вид:
. (19.19)
При турбулентном режиме:
. (19.20)
Получается, что рзаб является сложной функцией Q.
Легко доказать, что функции (19.19) и (19.20) имеют минимум.
В самом деле, при малой величине разности Q-Qо будет очень высока концентрация шлама в растворе, плотность ρсм приблизиться к плотности породы ρп, и величина рзаб будет определяться, в основном, составляющей ρсмgL (второй член уравнения). При очень больших расходах Q концентрация φ будет мала, плотность смеси ρсм будет практически равна ρ, но при этом резко возрастут потери ркп. В результате и в первом и во втором случаях рзаб будет велико. Следовательно, имеется оптимальный расход Qопт, при котором рзаб примет минимальное значение, при котором станет минимальным и дифференциальное давление на забое (и не только на забое). Разумеется, такой вариант промывки будет самым предпочтительным.
Сказанное в равной степени справедливо и для рн. Расчеты убедительно доказывают, что и рзаб и рн имеют минимумы, не совпадающие в общем случае по величинам Qопт.
С технологической точки зрения оптимизация по критерию рзаб имеет важнейшее значение, чего нельзя сказать о рн. Ввиду сложной зависимости между Q и ркп поиск Qопт целесообразно поручить ЭВМ.
Расчеты показывают, что существенное влияние выбуренной породы на рзаб начинается при vм > 10…15 м/час.
Список использованных источников
1. Осипов П.Ф., Скрябин Г.Ф. Оптимизация режимов бурения гидромониторными шарошечными долотами. – Ярославль: Медиум-пресс, 2001. – 239 с.
2. Маковей Н. Гидравлика бурения. – М.: Недра, 1986. – 536 с.
3. Гетлин К. Бурение и заканчивание скважин. – М.: Гостоптехиздат, 1963.
4. Осипов П.Ф., Самусенко И.М. Применение ЭВМ для выполнения гидравлических расчетов процессов промывки и спуска труб в скважину // Тр. Гипровостокнефти. – Вып. 32. - Куйбышев: Гипровостокнефть. – С. 31-36.
5. Осипов П.Ф. Методика расчета критических скоростей спуска колонны труб в скважину при самозаполнении их буровым раствором // Тр. Гипровостокнефти. - Куйбышев: Гипровостокнефть, 1980.
ПРИЛОЖЕНИЕ.
Алгоритмы расчета потерь и перпадов давления
в циркуляционной системе скважины.
Лист 1. Потери давления в трубах при движении вязкопластичной жидкости.
Лист 2. Потери давления в заколонном пространстве при движении
вязкопластичной жидкости (ВПЖ)
Лист 3. Потери давления в заколонном пространстве за замками (муфтами)
при движении вязкопластичной жидкости (ВПЖ)
Лист 4.Потери давления в трубах при движении псевдопластичной
(степенной) жидкости (ППЖ).
Лист 5. Потери давления в заколонном пространстве при движении
псевдопластичной (степенной) жидкости.
Лист 6.Потери давления в заколонном пространстве за замками (муфтами)
при движении псевдопластичной (степенной) жидкости.
Лист 7.Потери давления в трубах при движении вязкой жидкости (ВЖ).
Лист 8. Потери давления в заколонном пространстве при движении
вязкой жидкости (ВЖ)
Лист 9. Потери давления в заколонном пространстве за замками (муфтами)
при движении вязкой жидкости (ВЖ)
Лист 10. Давление на насосах.
Дата добавления: 2018-06-27; просмотров: 668; Мы поможем в написании вашей работы! |
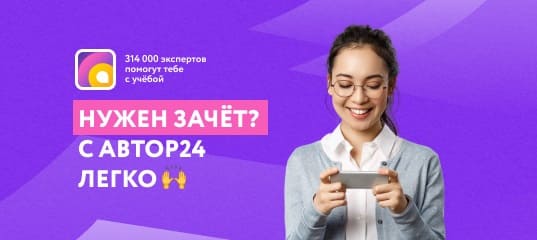
Мы поможем в написании ваших работ!