Обработка отверстий, в том числе глубоких, лезвийным инструментом
Виды обраб. отв. и применяемое оборудов. завис. в осн. от полученной загот. Достижение необходимой точности при обработке отверстий значительно труднее чем при обработке наружных поверхностей тел вращения. Поэтому допуски на точность отверстий больше допусков на наружные поверхности. Сверлением достигают 10-11квалитет (кв), Ra12,5-25мкм. Осуществляют на вертикальных и горизонтально-сверлильных станках. Отверстия диаметром более 30мм сверлят двумя последовательными свёрлами с меньшим и большим диаметрами с целью уменьшения осевой силы и увода сверла. При сверлении отверстий под резьбу диаметр сверла принимают больше внутреннего диаметра резьбы на (0,3-0,4) глубины резьбы. При сверлении глубоких отверстий диаметром от 80 до 200мм и длиной до 500 мм применяют кольцевые свёрла. Отлитые или отштампованные отв.обрабатываются сначала черновым, а затем чистовым зенкером, протяжкой и развёрткой. Зенкеры диаметром более 30 мм. чаще всего изготавливают с твердосплавными ножами. Цилиндрические отверстия под головки болтов и гаек выполняют на сверлильных станках цековкой. В крупносерийном и массовом производствах широко применяются комбинированные зенкеры, обрабатывающие одновременно отверстие, торец и фаску. Развёртывание – чистовая обработка отверстий по 7-8кв. и Ra2,5-0,63мкм. Развёртывание не изменяет положение геометрической оси отверстия. Прецизионное растачивание характеризуется применением высоких скоростей (100-1500м/мин), малых подач (0,01-0,15мм/об) и малых глубин резания (0,05-0,2мм) с использованием инструментов с алмазом, тв. сплавом или металлокерамическими пластинами. Наиболее эффективно прецизионное растачивание при обработке цветных металлов и сплавов (после прецизионной обработки применяют хонингование, суперфиниш, притирка). Протягивание отверстий применяют в КСП и М производствах для получения цилиндрических, шлицевых и др. форм отверстий. Протягивание обеспечивает 6-8кв, Ra1,25-0,32мкм. Протяжка – специальный инструмент, изготовленный из инструментальной (Р6М5) и конструкционной стали в виде хвостовиков (контактно-стыковая сварка трением) и подвергаются ТО.
|
|
Обработка глубоких отверстий
К глубоким отв. относят отв., у кот. L/D≥5. Обраб. произв. на универс.станках или на специальных станках для глубокого сверления спец. сверлами.
Сверление. Спиральные сверла не позвол. обесп. точность глубоких отв. Это объясняется тем, что у стандарт. сверл не идеальная заточка двух перьев. Поэтому силы, действующие на каждое перо не одинаковы. Поэтому создается биение и горизонтальными силами уводит ось сверла. Осевая сила искривляет сверло, способствуя доп-му уводу. На увод сверла еще влияют зазоры в подшипниках шпинделя.
|
|
Для предотвращения увода применяют следующие способы:
1)подача не более чем 0,02-0,05 мм/об
2)тщательн. затачивание сверла с соблюд. равномерн. наклона обоих реж. кромок
3)следить за износом сверла и налипании металла на реж. и вспом. кромки
4)применение СОЖ
5)предварительное центрование с помощью короткого сверла большого диаметра с углом 2φ=90°. Это особенно необходимо при работе без кондуктора.
6)Сверление при вращающейся заготовки.
Обработка отв. абразивн.инструм.(шлифование, хонингование) и методами ППД
Шлифование отверстий.На внутришлиф. станках отверстия шлифуются следующими способами: 1)при вращающейся детали, закрепленной в патроне; 2) при неподвижной детали —на станках с планетарным движением шпинделя; 3) при вращающейся незакрепленной детали — бесцентровое-шлифование.
1,2) Шлиф. на обычных внутришлиф. станках примен. наиб. часто. При этом дет. крепится в самоцентрир. патроне, например в кулачковом, цанговом, мембранном и др., и вращ. со скор. 40—60 м/мин (рис). Диам. шлиф. круга выбирается в завис. от диам. обрабат. отв. Так, для отверстий диаметром до 40 мм круг берется немного меньше (примерно 0,9 Dotв). С увеличением р-ра отв. (до 150 мм) диам. круга принимают равным от 0,6 до 0,8 диам. отв. и для больших диам. отв. не более 0,5.
|
|
Скорость вращения круга принимается для обычного шлифования до 35 м/сек и для скоростного — до 50 м/сек и более. Кроме вращения, круг совершает возвратно-посту-пательное движ.(продол. подачу) в направлении своей оси. Продол. подача обычно измеряется длиною пути, совершаемого кругом за один оборот детали и измеряемого в долях высоты круга. Так, при предварит. шлифов. продол. подача принимается от 0,4 до 0,8, а при чистовом — от 0,25 до 0,4 высоты круга. За каждый двойной ход круга осущ-ся поперечная подача (на глубину резания). Она принимается равной от 0,005 до 0,15 мм на двойной ход.
3)Метод предназн. для обраб. отв. и загот. диам. до 200 мм со сквозными и глухими отв., цилиндрич. и конич. Обраб. загот. 1 базируется по наружной цилиндр. пов-ти и торцу и опирается на ведущ. стальной ролик 2 и опорный стальн. ролик 3; нажимной ролик 4 имеет возможность поворачиваться относительно оси, прижимая шлифуемую загот. в период обработки. Загот. торцом прижимается к кольцевому упору осевой силой, возникающей вследствие поворота ведущего диска в вертикальной плоскости примерно на полградуса. Вращение передается загот. от ведущ. ролика, а нажимной и опорный ролики свободно вращаются на своих пальцах.При этой сх. шлиф. погрешн. формы наружн. пов-ти (овальность, волнистость и гранность) копируются на внутр. пов-ть. Поэтому до шлиф. отв. необх. обесп. макс. снижение погрешн. наружн. пов-ти и перпендикулярность ее торцу.(6-7-й квалитет)
|
|
Хонингование отверстий. Сущность заключ. в тонкой обраб. предварительно развернутого, шлифованного или расточенного отв специальной вращающейся головкой, называемой хоном. Эта головка имеет 6 (иногда и более) раздвижных абразивн. брусков прямоуг. сечения зернистостью от 12 до 3 и мельче. Кроме вращения, головка имеет возвратно-поступат. движ. Раздвижение абразивных брусков в радиальном направлении осущ. механическим, гидравлическим или пневматическим устройством. Скорость вращения хонинговальной головки 60- 75 м/мин при обработке заготовок из чугуна и 45- 60 м/мин из стали. Скорость возвратно-поступательного движения головки 12-15м/мин.
Поверхностное пластическое деформирование. Методы ППД основаны на использ. пластических св-тв металлов, отличаются высокой производит. и способностью создавать поверхность с необх. физико-механич. св-вами. В рез. повышаются твёрдость и прочность поверхностного слоя, формируются благоприятные остаточные напряжения, уменьшается параметр шероховатости Rа, увеличиваются радиусы закругления вершин и относительная опорная длина профиля. М. осущ. на различном технол. оборуд.(ток., сверл. и спец. станках), и вып-ется как отдельный вид обраб. или совмещенный с обработкой резанием. ППД наруж. тел вращ. может осущ. роликами, шариками, алмазным выглаживанием, дробеструйной обработкой и др.
Обраб. пов-тей роликами: 1-3 ролика прижимаются к обраб.пов-ти и под давлением сминают микронеровности и создают наклепанный слой, повышающий эксплуатационные св-ва обраб. пов-ости (рис. 40:а – одним, б – двумя, в – тремя).
Обкатывание роликами может осуществляться с продольной или поперечной подачей. Обычно этими способами обрабатывают достаточно жёсткие детали из стали, чугуна и цветных сплавов. Ролики изготавливаются из закаленной стали, стали ШХ или твердого сплава.
Обработка пов. шариками реализовывается в виде динамического наклепа, используя центробежную силу шариков (роликов), свободно сидящих в радиальных отверстиях быстровращающегося диска. Шарики 2 при вращ. диска 3 смещаются в радиал. направлении на величину h = R1 – R нанося многочисленные удары по заготовке 1 и пластически деформируя пов. Обработка ведется с применением керосина или веретенного масла на шлифовальных или токарных станка с применение на последних специальных устройств – приспособлений.
Вибронакатывание -для повышения износост. дет. машин, работ. в усл. трения. Помимо обычных движений (скорость заготовки, Sпр и усилие прижима) упрочняемый инструмент имеет дополнительное колебательное движение, сообщаемое ему при помощи специального устройства, причем амплитуда колебаний очень маленькая. Этим методом на поверхности деталей машин выдавливаются слабо заметные, прилегающие друг к другу канавки. В качестве упрочняющего инструмента используют шар или алмаз, установленный в резцедержателе токарного станка.
Алмазное выглаживание -для получения пов. с минимальным параметром шерох. и упрочнённым слоем небольшой глубины. При выглаживании алмаз (твердый сплав), находящийся в специальной державке, прижимается с определенным усилием к обрабатываемой поверхности. Особенность данного метода - алмазным выглаживанием м. обрабатывать пов., предварительно закаленные до HRC 60. При обработке данным методом размер заготовки увеличивается на 1..15 мкм, а микротвердость увеличивается на 5..50%. Глубина наклепанного слоя достигает до 400 мкм. Достоинства данного метода:- снижается шероховатость поверхности;- отсутствует перенос на обрабатываемую поверхность посторонних частиц (абразивных зерен);- позволяет обрабатывать тонкостенные детали и детали сложной конфигурации из различных материалов;- простота конструкции выглаживателя (подпружиненная державка).
Дробеструйное наклепывание -для повышения прочности деталей (при ударных нагрузках), для предупреждения растрескивания при работе в коррозионных средах, повышения маслоудерживающих св-тв пов-тей. Сущность: обработка поверхности многочисленными ударами дробинок или шариков из стали, чугуна, алюминия или стекла. Твердость поверхностного слоя увеличивается на 20..40% , причем глубина наклепа составляет не более 1 мм и эта глубина падает с увеличением твердости исходного материала. Применяется и для повышения долговечности рессорных листов, пружин, лопаток турбин, штоков, штампов и др. деталей.
Накатывание рифлений-для образования на пов. цилиндрич. дет. (рукоятки, гайки, головки микрометрических винтов и др.) рифлений для удобства пользования. Рифления накатывают плоскими плашками на резьбонакатных станках или вращающимися цилиндрическими роликами на токарных и револьверных станках. Накатывание рифлений на поверхностях тел вращения может быть: прямым, угловым, сетчатым. В зависимости от этого накатывание осуществляется одним роликом (прямое и угловое) или двумя роликами со встречным наклоном (угловое). В процессе накатывания рифлений увеличивается диаметр обрабатываемой поверхности, необходимая глубина накатки достигается за несколько проходов в зависимости от свойств обрабатываемого материала, заданного шага и глубины рифлений.
Дата добавления: 2018-06-01; просмотров: 615; Мы поможем в написании вашей работы! |
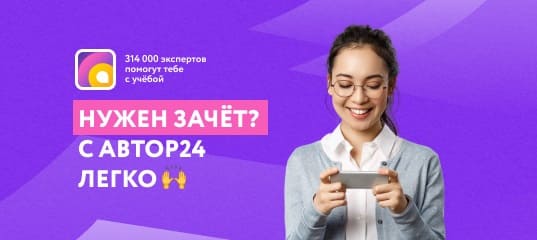
Мы поможем в написании ваших работ!