Ремонт деталей методами пластического деформирования
Сущность этого метода основана на возможности восстановления изношенных рабочих поверхностей путем некоторого пластического перераспределения материала детали в холодном и горячем состоянии. В зависимости от износа, формы и размеров детали применяют осадку, вдавливание, раздачу, обжатие, вытяжку, правку. Эти методы различаются направлением внешней действующей силы и величиной требуемой деформации.
Обработка пластическим деформированием основана на способности металла изменять свои форму, размеры и механические свойства без разрушения под действием внешних сил за счет его пластических (остаточных) деформаций. При ремонте машин выполняют следующие основные операции: восстановление размеров изношенных участков путем перераспределения массы деталей (раздача, обжатие, осадка, вдавливание, вытяжка, растяжка, накатка); устранение дефектов формы деталей путем правки; повышение эксплуатационных свойств деталей в результате поверхностного пластического деформирования металла.
Ремонтные операции проводят без предварительного нагрева деталей и с предварительным их нагревом.
При обработке деталей в холодном состоянии пластическая деформация происходит вследствие сдвигов частиц, внутри кристаллов металлов (внутрикристаллическая деформация), что сопровождается изменением физико-механических свойств металла (увеличение предела текучести, снижением вязкости, повышением твердости).
|
|
Рис. 19.2. Восстановление деталей ДРД: 1 – деталь; 2 – ДРД; 3 – сварочный шов
![]() | ![]() | |
![]() ![]() | ![]() | ![]() |
При обработке давлением в горячем состоянии пластическая деформация происходит вследствие сдвигов целых зерен металла (межкристаллическая деформация). Нагрев деталей приводит к изменению физико-механических свойств и структуры металла, поэтому ответственные детали после обработки давлением подвергаются повторной термической обработке.
Раздача. Эту операцию применяют для увеличения по наружному диаметру изношенных полых деталей за счет изменения внутреннего диаметра (поршневые пальца, пустотелые валы, чашки дифференциала и др. При раздаче направление давления р от внешних сил совпадает с направлением деформацийd. Давление р (в МПа) при раздаче равно
р =1.15sтln(R/r),
где sт - предел текучести металла детали, МПа;
R и r - наружный и внутренний радиусы детали, мм.
Обжатие применяют для уменьшения по внутреннему диаметру изношенных полых деталей за счет изменения наружного диаметра. Способом обжатия восстанавливают, втулки шатунов и поршней, сепараторы роликовых подшипников, звенья гусениц при износе проушин и др.
|
|
Осадка. Осадкой увеличивают наружный диаметр сплошных деталей, а также уменьшают внутренний и увеличивают наружный диаметр полых деталей за счет уменьшения их длины. Давление р (в МПа) при осадке рассчитывают по формуле:
,
где D - наружный диаметр втулки после осадки, мм;
l - длина втулки, мм.
Вдавливание. Этот процесс применяют для увеличения размеров изношенных частей посредством перераспределения металла с ее нерабочих поверхностей, вдавливание объединяет операции раздачи и осадка, так как деформирующая сила направлена поднекоторым углом к направлению требуемой деформации. Вдавливание применяют при восстановлении изношенных боковых поверхностей шлицев, зубьев некоторых шестерен, шаровых пальцев и др. Так, технологический маршрут восстановления шлицевого вала следующий: отпуск, вдавливание, обтачивание вала, фрезерование боковых поверхностей шлицев, термическая обработка, шлифование.
Вытяжка и растяжка.При вытяжке увеличивают длину деталей рычагов, тяг, стержней) за счет местного сужения их поперечного сечения на небольшом участке. Вытяжку выполняют в горячем состояли с местным нагревом детали до 800-850°С. При вытяжке направление деформации перпендикулярно направлению деформирующей силы. Растяжкой также достигают увеличения длины детали, но в отличие от вытяжки направление деформации совпадает с направлением действующей силы.
|
|
Широкое распространение при ремонте а/м получим такой метод как правка:
Правка в холодном состоянии статическим нагружением (под прессом) (рис. 19.7); применение этого способа на первый взгляд эффективно, но связано с возникновением при этом больших внутренних напряжений в детали и значительным снижением усталостной прочности (на 15 - 40%).
![]() | ![]() |
С целью уменьшения внутренних, напряжений применяют после правки искусственное старение, т.е. выдержку правленой детали в течение I часа при = 400 - 500 °С.
Коленвалы и распредвалы (т.е. детали подвергаемые закалке) подвергают после правки под прессом старению в течение 5 часов при температуре 180-200°С.
Правка деталей наклепом (рис. 19.8) является более эффективной, т.к. позволяет вести правку в желаемом направлении, обеспечивает высокую точность (до 0,02 мм) и не дает снижения усталостной прочности. Осуществляется правка наклепом специальными молотами с закругленным бойком или пневматическими устройствами с шариками.
|
|
Пластическое деформирование используют при восстановлении размеров деталей, их формы и физико-механических свойств. Изношенные детали восстанавливают осадкой, вдавливанием, раздачей, обжатием, вытяжкой и накаткой. Форму деталей, измененную вследствие деформаций от изгиба и кручения, восстанавливают правкой статическим нагружением или наклепом. Восстановление механических свойств материала деталей, повышение их усталостной прочности и износостойкости осуществляют способами поверхностного пластического деформирования, к которым относятся обкатка роликами и шариками, чеканка, алмазное выглаживание, дробеструйная обработка и др.
Восстановление размеров изношенных деталей пластическим деформированием достигается в процессе перераспределения металла с нерабочих элементов деталей на изношенные. Восстановление первоначальной формы деталей правкой основано на упругих свойствах материала детали. Восстановление усталостной прочности и износостойкости деталей производится повышением твердости поверхностного слоя металла и созданием в нем благоприятных остаточных напряжений.
Осадку применяют для уменьшения внутреннего или увеличения наружного диаметра полых деталей (втулок), а также увеличения наружного диаметра сплошных деталей за счет уменьшения их длины (рис. 4.14, а). Уменьшение высоты втулок, воспринимающих большие нагрузки, допускается не более чем на 8 %, а для менее нагруженных втулок — на 15 %.
Вдавливаниеприменяют для увеличения наружного размера детали за счет вытеснения металла из ограниченного участка ее нерабочей поверхности.
Раздачейвосстанавливают наружные размеры полых деталей, увеличивая их внутренние размеры (рис. 4.14, б). Методом раздачи восстанавливают, например, поршневые пальцы дизелей.
Обжатие применяют для уменьшения внутреннего диаметра полых деталей, уменьшая их наружный диаметр (рис. 4.14, в). При обжатии с нагреванием металл детали изменяет свою структуру, поэтому после деформации ее подвергают повторной термической обработке.
Вытяжкуиспользуют для увеличения длины деталей в результате местного обжатия (рис. 4.14, г).Деформацию производят чаше всего в холодном состоянии.
Рис. 4.14. Схема восстановления деталей давлением: а осадка; б — раздача; в — обжатие; г — вытяжка; д — накатка; Р — усилие; 5 — деформация
Накаткаприменяется для компенсации износа наружных цилиндрических поверхностей деталей, воспринимающих удельную нагрузку не более 7 МПа, за счет выдавливания металла из восстанавливаемой поверхности (рис. 4.14, д). Накаткой восстанавливают детали с твердостью не более 30 HRC. Если твердость выше, то деталь подвергают отпуску. Накатку производят зубчатым роликом с шагом зубьев 1,5—1,8 мм, обеспечивающим высоту подъема металла не более 0,2 мм на сторону и уменьшение опорной поверхности — не более 50 %.
Правка статическим нагружением под прессом производится в холодном состоянии. Чтобы получить после правки требуемую остаточную деформацию детали, ее перегибают в обратном направлении прогибом, в 10—15 раз большим первоначального. Для повышения стабильности правки и увеличения несущей способности деталей после правки их подвергают термической обработке. Правка под прессом снижает усталостную прочность деталей на 15-20 %.
Правку наклепом производят нанесением ударов по нерабочим поверхностям деталей. От ударов, наносимых пневматическим молотком, в поверхностном слое детали возникают местные напряжения сжатия, которые вызывают устойчивую остаточную деформацию детали. Режим правки зависит от материала детали, энергии удара и конструкции ударного бойка.
Преимущества способа восстановления деталей пластической деформацией — простота технологического процесса и применяемого оборудования, особенно при деформировании деталей в холодном состоянии; экономическая эффективность процесса из-за отсутствия дополнительных расходов на материалы. Преимущества правки наклепом — стабильность правки во времени, высокая точность (до 0,02 мм), высокая производительность, отсутствие снижения усталостной прочности деталей. К недостаткам данного способа следует отнести ограниченность номенклатуры восстанавливаемых деталей, невозможность их повторного восстановления и некоторое снижение механической прочности деталей при восстановлении изношенных поверхностей. Правка статическим нагружением под прессом в холодном состоянии не дает хорошего качества восстановления деталей из-за возникновения в процессе правки внутренних напряжений, которые снижают усталостную прочность детали на 15—40 %, а также с течением времени приводят к повторной деформации детали.
Восстановление втулок из цветных металлов осадкой производят в специальных приспособлениях в холодном состоянии. Если после осадки предусмотрена механическая обработка внутренней поверхности втулки, то размер пальца, ограничивающего деформацию втулки по внутреннему диаметру принимают на 0,3 мм меньше, чем диаметр окончательно обработанного отверстия. Осадкой восстанавливают также размеры стальных деталей — шейки валов, расположенные на концах деталей, толкатели клапанов и др. При этом деформацию деталей производят в штампах при нагревании до температуры ковки.
Восстановление зубьев шестерен и шлиц на валах осуществляют объемным вдавливанием в нагретом состоянии с использованием специальных приспособлений.
Восстановление поршневых пальцев и других наружных поверхностей деталей производят раздачей сферическими прошивками в холодном состоянии. Если деталь подвергалась закалке или цементации, то ее перед раздачей подвергают отжигу или высокому отпуску, а после раздачи восстанавливают первоначальную термическую обработку.
Восстановление отверстий во втулках из цветных металлов производят обжатием. Детали, восстановленные раздачей и обжатием, необходимо проверить на отсутствие трещин.
Правке подвергают детали рамы, коленчатые и распределительные валы, шатуны и другие детали. После правки коленчатых и распределительных валов, изготовленных из стали 45, статическим нагружением под прессом в холодном состоянии для стабилизации формы необходимо нагреть их до температуры не выше 180—200 °С и выдержать при этой температуре не менее 5 часов. Такая стабилизация восстанавливает несущую способность деталей только до 60—70 %.
5. Электрофизические и электрохимические методы обработки. Электроэрозионная обработка: электроискровая, электроимпульсная, анодномеханическая и электроконтактная.
Характеристика электрофизических и электрохимических методов обработки
Эти методы предназначены в основном для обработки заготовок из очень прочных, весьма вязких, хрупких и неметаллических материалов.
Эти методы имеют следующие преимущества:
– отсутствует силовое воздействие инструмента на заготовку (или очень мало и не влияет на суммарную погрешность обработки);
– позволяют менять форму поверхности заготовки и влияют на состояние поверхностного слоя: наклеп обработанной поверхности не образуется, дефектный слой незначителен; повышаются коррозионные, прочностные и другие эксплуатационные характеристики поверхности;
– можно обрабатывать очень сложные наружные и внутренние поверхности заготовок.
ЭФЭХ методы обработки являются универсальными и обеспечивают непрерывность процессов при одновременном формообразовании всей обрабатываемой поверхности. Эти методы внедряются в различных отраслях промышленности.
Электроэрозионные методы обработки
Эти методы основаны на явлении эрозии электродов из токопроводящих материалов при пропускании между ними импульсного электрического тока.
Разряд между электродами происходит в газовой среде или при заполнении межэлектродного пространства диэлектрической жидкостью – керосин, минеральное масло.
При наличии разности потенциалов на электродах происходит ионизация межэлектродного пространства. При определенном значении разности потенциалов – образуется канал проводимости, по которому устремляется электроэнергия в виде импульсного искрового или дугового разряда.
На поверхности заготовки температура возрастает до 10000…12000 0C. Происходит мгновенное оплавление и испарение элементарного объема металла и на обрабатываемой поверхности образуется лунка.
Удаленный металл застывает в диэлектрической жидкости в виде гранул диаметром 0,01…0,005 мм.
При непрерывном подведении к электродам импульсного тока процесс эрозии продолжается до тех пор, пока не будет удален весь металл, находящийся между электродами на расстоянии, при котором возможен электрический пробой (0,01…0,05 мм) при заданном напряжении.
Для продолжения процесса необходимо сблизить электроды до указанного расстояния. Электроды сближаются автоматически с помощью следящих систем.
Электроискровая обработка
Схема электроискровой обработки представлена на рис. 21.1.
Рис.21.1. Схема электроискрового станка:
1 – электрод-инструмент; 2 – ванна; 3 – заготовка-электрод; 4 – диэлектрическая жидкость; 5 – изолятор
При электроискровой обработке – используют импульсные искровые разряды между
электродами ( обрабатываемая заготовка (анод) – инструмент (катод)).
Конденсатор заряжается через резистор
от источника постоянного тока напряжением 100…200 В. Когда напряжение на электродах 1 и 3 достигает пробойного образуется канал, через который осуществляется искровой разряд энергии, накопленной конденсатором.
Продолжительность импульса 20…200 мкс.
Точность обработки до 0,002 мм, 0,63…0,16 мкм.
Для обеспечения непрерывности процесса ( зазор =const) станки снабжаются следящей системой и системой автоматической подачи инструмента.
Получают сквозные отверстия любой формы поперечного сечения, глухие отверстия и полости, отверстия с криволинейными осями, вырезают заготовки из листа, выполняют плоское, круглое и внутреннее шлифование.
Изготовляют штампы и пресс-формы, фильеры, режущий инструмент.
Схемы электроискровой обработки представлены на рис. 21.2.
Рис. 21.2. Схемы электроискровой обработки:
а – прошивание отверстия с криволинейной осью; б – шлифование внутренней поверхности фильеры
Электроискровую обработку применяют для упрочнения поверхностного слоя металла. На поверхность изделия наносят тонкий слой металла или композиционного материала. Подобные покрытия повышают твердость, износостойкость, жаростойкость, эрозионную стойкость и так далее.
Электроимпульсная обработка
При электроимпульсной обработке используют электрические импульсы большой длительности (5…10 мс), в результате чего происходит дуговой разряд.
Большие мощности импульсов от электронных генераторов обеспечивают высокую производительность обработки.
Электроимпульсную обработку целесообразно применять при предварительной обработке штампов, турбинных лопаток, фасонных отверстий в детали из коррозионно-стойких и жаропрочных сплавов.
Схема обработки показана на рис.21.3.
Рис. 21.3. Схема электроимпульсной обработки:
1 – электродвигатель; 2 – импульсный генератор постоянного тока; 3 – инструмент-электрод; 4 – заготовка-электрод; 5 – ванна.
Электроконтактная обработка.
Электроконтактная обработка основана на локальном нагреве заготовки в месте контакта с электродом-инструментом и удалении размягченного или расплавленного металла из зоны обработки механическим способом: относительным движением заготовки или инструмента.
Источником теплоты служат импульсные дуговые разряды.
Этот вид обработки рекомендуется для крупных деталей из углеродистых и легированных сталей, чугуна, цветных сплавов, тугоплавких и специальных сплавов (рис.21.4).
Рис. 21.4. Схема электроконтактной обработки плоской поверхности:
1 – обрабатываемая заготовка; 2 – инструмент-электрод; 3 – трансформатор
Этот метод применяют для зачистки отливок от заливов, отрезки литниковых систем, зачистки проката, шлифования коррозионных деталей из труднообрабатываемых сплавов.
Электрохимическая обработка
Электрохимическая обработка основана на законах анодного растворения металлов при электролизе.
При прохождении электрического тока через электролит на поверхности заготовки происходят химические реакции, и поверхностный слой металла превращается в химическое соединение.
Продукты электролиза переходят в раствор или удаляются механическим способом.
Производительность этого способа зависит от электрохимических свойств электролита, обрабатываемого материала и плотности тока.
Электрохимическое полирование.
Электрохимическое полирование осуществляется в ванне, заполненной электролитом (растворы кислот и щелочей).
Обрабатываемую заготовку подключают к катоду (рис. 21.5). Катодом служит металлическая пластинка из свинца, меди, стали (иногда электролит подогревают).
Рис. 21.5. Схема электрохимического полирования:
1 – ванна; 2 – обрабатываемая заготовка; 3 – пластина-электрод; 4 – электролит; 5 – микровыступ;
6 – продукты анодного растворения
При подаче напряжения начинается процесс растворения металла заготовки (в основном на выступах микронеровностей). В результате избирательного растворения, микронеровности сглаживаются, и обрабатываемая поверхность приобретает металлический блеск.
Улучшаются электрофизические характеристики деталей: уменьшается глубина микротрещин, поверхностный слой не деформируется, исключаются упрочнения и термические изменения структуры, повышается коррозионная стойкость.
Этим методом получают поверхности под гальванические покрытия, доводят рабочие поверхности режущего инструмента, изготовляют тонкие ленты и фольгу, очищают и декоративно отделывают детали.
Электрохимическая размерная обработка
Электрохимическая размерная обработка выполняется в струе электролита, прокачиваемого под давлением через межэлектродный промежуток.
Электролит растворяет образующиеся на поверхности заготовки – анода соли и удаляет их из зоны обработки. Высокая производительность процесса заключается в том, что одновременно обрабатывается вся поверхность заготовки.
Участки, не требующие обработки, изолируют. Инструменту придают форму, обратную форме обрабатываемой поверхности. Формообразование происходит по методу копирования ( рис. 21.6).
Рис. 21.6. Схема электрохимической размерной обработки:
1 – инструмент – катод; 2 – заготовка – анод
Точность обработки повышается при уменьшении рабочего зазора. Для его контроля используют высокочувствительные элементы, которые встраивают в следящую систему.
Этот способ рекомендуют для обработки заготовок из высокопрочных сталей, карбидных и труднообрабатываемых материалов. Также можно обрабатывать тонкостенные детали с высокой точностью и качеством обработанной поверхности (отсутствует давление инструмента на заготовку).
Комбинированные методы обработки
Электроабразивная и электроалмазная обработка.
При таких видах обработки инструментом служит шлифовальный круг из абразивного материала на электропроводящей связке (бакелитовая связка с графитовым наполнителем).
Между анодом – заготовкой и катодом – шлифовальным кругом имеется зазор, куда подается электролит. Продукты анодного растворения удаляются абразивными зернами; шлифовальный круг имеет вращательное движение, а заготовка – движение подачи, которые соответствуют процессу механического шлифования ( рис. 21.7).
Рис. 21.7. схема электроабразивного шлифования:
1 – заготовка; 2 – абразивные зерна; 3 – связка шлифовального круга.
Введение в зону резания ультразвуковых колебаний повышает производительность в 2…2,5 раза при улучшении качества поверхности. Эти методы применяются для отделочной обработки заготовок из труднообрабатываемых материалов, а также нежестких заготовок, так как силы резания незначительны.
Анодно-механическая обработка
Анодно-механическая обработка основана на сочетании электротермических и электромеханических процессов и занимает промежуточное место между электроэрозионным и электрохимическим методами.
Заготовку подключают к аноду, а инструмент – к катоду. В качестве инструмента используют металлические диски, цилиндры, ленты, проволоку.
Обработку ведут в среде электролита ( водный раствор жидкого натриевого стекла).
Рабочие движения, как при механической обработке резанием.
Электролит в зону обработки подают через сопло ( рис. 21.8).
Рис. 21.8. Схема анодно-механической обработки плоской поверхности.
При пропускании через раствор электролита постоянного электрического тока происходит процесс анодного растворения, как при электрохимической обработке.
При соприкосновении инструмента с микронеровностями заготовки происходит электроэрозия, присущая электроискровой обработке. Металл заготовки в месте контакта с инструментом разогревается и разжижается. Продукты электроэрозии и анодного растворения удаляются при относительных движениях инструмента и заготовки.
Этим способом обрабатывают заготовки из высокопрочных и труднообрабатываемых сплавов, вязких материалов.
Этим способом разрезают заготовки на части, прорезают пазы и щели, обрабатывают поверхности тел вращения, шлифуют плоские поверхности и поверхности, имеющие форму тел вращения, полируют поверхности, затачивают режущий инструмент.
6. Ультразвуковая обработка. Лучевая обработка. Магнитоимпульсная обработка. Электрохимическая обработка. Абразивноэлектрохимическая обработка.
Ультразвуковой метод обработки заключается в механическом воздействии на материал. Он назван ультразвуковым благодаря тому, что частота ударов соответствует диапазону неслышимых звуков, т.е. выше 16 кГц. Ультразвуковым методом можно обрабатывать твердые и хрупкие материалы, частицы которых могут, как бы выкалываться при ударе.
Широко используют ультразвуковую очистку деталей. Ультразвуковые колебания, накладываемые на жидкость для очистки деталей, особенно малогабаритных и имеющих сложную конфигурацию, резко повышают скорость и качество очистки.
Для пайки алюминия и его сплавов применяют способ удаления окисленной пленки, основанный на ее механическом разрушении интенсивными ультразвуковыми колебаниями. При этом осуществляется процесс ультразвукового лужения. Сущность явлений, происходящих при ультразвуковом лужении, заключается в следующем. Излучаемые рабочей частью паяльника знакопеременные упругие колебания частотой 16…22 кГц вызывают периодические растяжения и сжатия частиц жидкого припоя. В результате чего образуются кавитационные процессы в расплавленном припое. При этом возникают большие ударные импульсы, воздействующие на жидкий припой и поверхность облуживаемых деталей и вызывающие разрушение окисной пленки. Раздробленные частицы окисной пленки, обладают меньшей плотностью, всплывают на поверхность припоя, и он беспрепятственно облуживает очищенную поверхность металла.
Процесс ультразвукового лужения позволяет облудить всю обрабатываемую поверхность, с которой сняты окисные пленки, в то время как при механическом удалении окисной пленки облуживаются только отдельные зачищенные места поверхности.
На частоте 18…23 кГц окисная пленка наиболее эффективно удаляется при интенсивности ультразвуковых колебаний 25…100 Вт/см2. зона такой интенсивности из-за относительно высокой вязкости распространяется от излучающей поверхности преобразователя не далее 3 мм. В этой зоне можно получить эффективное лужение в течение 0,1с, при условии, что поверхность детали была предварительно нагрета до температуры расславленного припоя.
При уменьшении интенсивности ультразвуковых колебаний продолжительность удаления пленки увеличивается до 1с. Более длительное воздействие кавитации разрушает поверхность обрабатываемого изделия, а в некоторых случаях приводит к растворению изделия в припое.
Ультразвуковая обработка представляет собой ударо-абразивный метод обработки твердых и хрупких материалов. Она осуществляется (рис. 1.29) инструментом 1, колеблющемся с ультразвуковой частотой 18…20кГц. Под торец инструмента подается водная суспензия абразивного порошка. Зерна абразива 2, «вбиваемые» инструментом в заготовку 3, скалывают материал мелкими частицами, которые вместе с размельченным абразивом уносятся жидкостью. Если же инструмент ударяет по свободно висящему в жидкости зерну абразива, то выкалывание частиц материала изделия не происходит.
Кавитационные явления сообщают зернам абразива скорости, в десятки раз меньшие, чем инструмент в момент удара по зернам, но кавитация усиливает циркуляцию суспензии, что способствует попаданию свежего абразива в зону обработки, а так же удалению сколотых частиц и разрушенных зерен абразива.
Этим методом хорошо обрабатываются твердые и хрупкие материалы: керамика, кварц, рубин, алмаз, кремний, твердые сплавы и др. Для обработки твердых сплавов инструмент целесообразно изготовить из стали 45 с последующей закалкой до твердости HRC 48…56. При точной обработке применяют инструмент из незакаленной стали, так как при закалке может произойти его деформация. Шаржирование поверхности инструмента абразивными зернами не влияет на обработку.
Максимальная скорость съема материала по обработке стекла составляет 9000мм3/мин, а по твердому сплаву – 200м3/мин.
Вязкие материалы (например, сталь незакаленная) плохо обрабатываются ультразвуковым способом, так как под ударами зерен абразива не происходит сколов материалов изделия, а зерна просто внедряются в обрабатываемый материал.
Производительность ультразвуковой обработки зависит от физико-механических свойств обрабатываемого материала, зернистости абразива, состава абразивной суспензии, амплитуды колебания инструмента и др.
Оптимальная величина зерен абразива составляет 110мкм, причем максимальная производительность достигается при концентрации абразива 30…40% от общей массы суспензии.
Скорость обработки растет пропорционально квадрату амплитуды. В настоящее время максимальные амплитуды колебаний в 45…50мкм. Дальнейшее увеличение амплитуды приводит к быстрому усталостному разрушению инструменту.
Точность и частота обрабатываемой поверхности при ультразвуковой обработке в основном зависит от величин зерен абразива в суспензии.
При использовании суспензии с зернами карбида бора №10 (100мкм) можно получить шероховатость поверхности Ra 1,25 мкм, а точность – 0,06мм. Применение абразива №3 дает возможность повысить точность до 0,02мм при шероховатости поверхности Ra 0,32мкм. Однако производительность при этом уменьшается примерно в 10 раз. Наиболее целесообразно ультразвуковую обработку применять для обработки изделий твердых сплавов (глухие отверстия штампов, пресс-форм и др.), резки германия и кремния, обработки алмазных и твердосплавных фильер, ферритовых плат и др.
Лучевые методы обработки
Электроннолучевая обработка – основана на превращении кинетической энергии направленного пучка электронов в тепловую энергию. Высокая плотность энергии сфокусированного электронного луча позволяет обрабатывать заготовку за счет нагрева, расплавления и испарения материала с локального участка.
Схема электроннолучевой обработки представлена на рис. 21.9.
Электронный луч образуется за счет эмиссии электронов с нагретого в вакууме катода. Он с помощью электростатических и электромагнитных линз фокусируется на заготовке.
При размерной обработке установка работает в импульсном режиме, что обеспечивает локальный нагрев заготовки.
Электроннолучевой метод эффективен при обработке отверстий диаметром 1…0,010 мм, при прорезании пазов, резке заготовок, изготовлении тонких пленок и сеток из фольги, изготовлении заготовок из труднообрабатываемых металлов и сплавов, керамики, кварца, полупроводникового материала.
Рис. 21.9. Схема установки для электроннолучевой сварки: 1 – катод электронной пушки; 2 – электрод; 3 – анод; 4 и 5 – отклоняющая магнитная система; 6 – заготовка
Магнитно-импульсная обработка (МИО) металлов представляет собой способ пластической деформации металлов, который возможен при прямом преобразовании электроэнергии в механическую в обрабатываемом изделии.
Основой магнитно-импульсной обработки являются электродинамические силы, возникающие в проводящем теле изделия, находящемся в переменном электромагнитном поле.
Установка магнитно-импульсной обработки (рис. 1.2) имеет зарядное устройство, батарею конденсаторов - накопитель энергии, коммутирующее устройство и индуктор. Батарея 3 заряжается через выпрямитель 2 от источника питания 1. По завершении зарядки батарея с помощью коммутирующего устройства 4 замыкается на индуктор 6.
Рис. 1.2. Принципиальная схема электрической цепи установки для магнитноимпульсной обработки металлов: 1 - источник питания; 2 - выпрямитель; 3 — батарея конденсаторов; 4 - коммутирующее устройство; 5 - изделие; 6 - индуктор
Протекающий по индуктору ток создает магнитный поток, который пересекает металлическое изделие 5 и создает в нем вихревые токи.
При разрядке конденсатора емкостью С на индуктивную катушку L импульс тока имеет длительность и форму, определяемые параметрами разрядного контура R, L и С.
Энергия, выделяющаяся в цепи, идет на нагрев заготовки, механическую работу деформации заготовки, нагрев проводников цепи и частично рассеивается в пространстве. Давление на обрабатываемую заготовку (кг/см2) зависит от плотности энергии электромагнитного.
При плавной скорости нарастания магнитного поля и значительной длительности импульса давление может проникнуть за заготовку и вызвать обратную реакцию, что существенно ослабит результирующее давление на обрабатываемую заготовку. Для предотвращения противодавления необходимо, чтобы длительность импульса не превышала времени деформации заготовки.
1.2. Технологическое оборудование магнитно-импульсной обработки
Установки для магнитно-импульсной обработки включают два основных узла: подготовительный (накопление энергии и формирование импульсного напряжения и тока) и технологический. К подготовительному узлу относятся генераторы импульсных токов, к технологическому - индукторы.
Генераторы импульсных токов преобразуют переменный ток промышленной частоты в импульсы токов большой амплитуды. Главными элементами генератора являются зарядное устройство, батарея конденсаторов, коммутирующее и поджигающее устройства.
В узел зарядного устройства входят повышающий трансформатор, выпрямитель и пускорегулирующая аппаратура. Батарея конденсаторов предназначена для накопления электрической энергии с дальнейшей разрядкой на технологический узел. В установках магнитно-импульсной обработки для этих целей применяются импульсные конденсаторы. Они должны иметь очень маленькую индуктивность, их конструкция должна обеспечивать длительную работу в режиме близком к режиму короткого замыкания. Объединение конденсаторов в батарею вызвано требуемой рабочей характеристикой генератора импульсного тока. С целью уменьшения времени разрядки батареи конденсаторов и обеспечения кратковременности выделения энергии в индукторе необходимо уменьшать общую индуктивность установки путем снижения индуктивности батареи конденсаторов, ошиновки и разрядника, что приведет к повышению эффективности магнитно-импульсной обработки.
Коммутирующее устройство (коммутатор) предназначено для того, чтобы в заданный момент подавать импульс напряжения на рабочую катушку, пропускать возникающий импульсный ток за определенное время и регулировать напряжение на конденсаторах. Коммутатор должен обеспечивать возможность регулирования рабочего напряжения, пропускать значительные токи, иметь малую индуктивность и большой срок службы. В установках применяют механические, ионные и дуговые коммутирующие устройства.
Разрядники, применяемые в коммутирующих устройствах, бывают трех типов: открытые, вакуумные и газонаполненные. Более востребованными являются вакуумные и газонаполненные разрядники. Они характеризуются широким диапазоном регулирования рабочего напряжения, возможностью изменения давления в разряднике и способностью коммутировать значительную энергию. Электрическая схема двухэлектродного газонаполненного разрядника показана на рис. 1.3.
Применение МИО металлов разнообразно и определяется импульсным характером и большой удельной мощностью возникающих давлений. Данный метод преимущественно применяется для обработки давлением тонкостенных металлических заготовок любых форм.
Рис. 1.3. Схема двухэлектродного разрядника: a, b — контрольные точки схемы; (Lп - Lк - 0,5Lo) — разрядная цепь; Lп - индуктивность поджигающей цепи; Lк - индуктивность колебательного контура; L0 - основная индуктивность; (Сп - Lп - Lк - 0,5Lo) — колебательный контур схемы поджига; С0 — основная емкость; Сп — поджигающая емкость; КУ — коммутирующее устройство; Рп - вспомогательный разрядник поджига
Рис. 1.4. Схема магнитно-импульсной обработки: а - соединение концов труб; б - соединение труб муфтой; 1 - заготовки; 2 - соленоид; 3 - муфта
Главными преимуществами установок магнитно-импульсной обработки (рис. 1.4) являются: отсутствие движущихся и трущихся частей; простота управления и регулирования мощности; компактность, простота обслуживания; высокая производительность; возможность механизации и автоматизации операций обработки.
К недостаткам магнитно-импульсной обработки следует отнести: невысокий КПД процесса; сложность обработки деталей с отверстиями или пазами, мешающими прохождению тока; недостаточную долговечность индукторов при работе в электрических полях высокой напряженности; сложность обработки деталей большой толщины.
Электрохимическая обработка (ЭХО, ЭХРО, ECM ) — это современный, высокотехнологичный прецизионный способ обработки электропроводных металлов и сплавов, который основан на растворении материала обрабатываемой детали с высокой скоростью, при одновременном воздействии импульсного тока в потоке электролита, поступающего через межэлектродный зазор (МЭЗ) между материалом обрабатываемой детали (анодом) и электродом-инструментом (катодом).
· В процессе электрохимическая обработка происходит прямое или обратное копирование на обрабатываемой заготовке формы и размеров электрода-инструмента сразу по всей поверхности заготовки.
· В результате только одного поступательного движения электрода инструмента в координате Z, за небольшой промежуток времени с применением электрохимического станка SFE, работающем в импульсно-циклическом режиме, можно получить готовые детали, штампы, матрицы самой сложной формы c хорошими показателями точности, шероховатости.
· Введением в техпроцесс изготовления детали только одной операции электрохимической обработки, можно сократить в несколько раз машинное время на изготовление готового изделия, исключая большое количество механических и ручных операций по доводке, высвободить рабочий персонал и энергоемкое оборудование.
Дата добавления: 2018-06-01; просмотров: 1494; Мы поможем в написании вашей работы! |
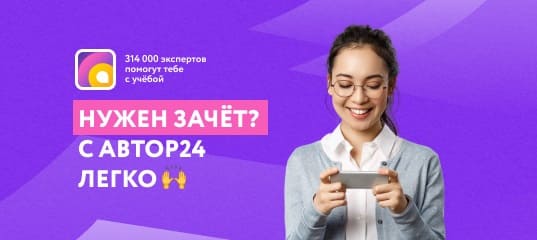
Мы поможем в написании ваших работ!