Основные направления технологической стандартизации и
Унификации
Основными направлениями технологической унификации
являются: типизация технологических процессов, унификация технологической документации, групповые методы обработки, унификация оборудования и технологической оснастки.
Н соответствии с ГОСТ 14.301-83 на этапах технологической подготовки производства разрабатывается три вида технологических процессов: единичные, типовые и групповые. Единичный технологический процесс предназначен для изготовления изделия(детали) одного наименования, типоразмера и исполнения,
независимо от типа производства. Типовой технологический процесс предназначен для изготовления группы деталей с общими конструкционными и технологическими признаками. Он разрабатывается для типового представителя и включает все основные и вспомогательные операции, характерные для изделий, отнесенных к этой группе.
Групповой технологический процесс предназначен дляизготовления группы изделий с разными конструкционными, но общими технологическими признаками. Основой разработки групповых технологических процессов является комплексная деталь или изделие, которое включает все конструкционные элементы, характерные для деталей или изделий этой группы. Использование групповых методов производства позволяет применять в единичном, мелко- и среднесерийном производстве методы и средства, свойственные крупносерийному и массовому производству. Групповая технология выступает базой для автоматизации серийного
|
|
Н единичного производства. На ее основе создаются автоматизированные и механизированные приспособления для универсальных станков, автоматизированные агрегатные станки, наконец, гибкие автоматизированные линии. Для организации группового производства используют подетальную или узловую
формыспециализациипроизводственныхизделий.
86
Специализированными подразделениями группового производства могут быть групповые поточные или гибкие автоматизированные линии, участки, цехи.
Типовые или групповые методы изготовления изделий или деталей вносят существенные особенности в технологическую подготовку производства. Меняется классификация изделий, деталей
+ всех элементов технологического процесса, используются заранее разработанное решение по всему технологическому процессу или его части и заранее подготовленное к обработке деталей или сборке изделий оборудование и производственные подразделения (рабочие места, линии, участки).
Унификация технологической документации приводит к сокращению общего количества документов, облегчению труда технологов при подготовке производстве и внесении изменений в действующие процессы. К числу основных унифицированных документов, используемых при разработке типовых технологических процессов, относятся карты типовых представителей, операционные
|
|
+ сводные карты типовых и групповых процессов.
Конструкторская унификация узлов технологического оборудования и создание компоновок станков путем агрегирования также ускоряют подготовку новых изделий. В основе этого метода лежит принцип конструкционного формирования отдельных элементов по функциональному признаку. В качестве унифицированных элементов выделяются такие узлы, которые выполняют в оборудовании комплекс самостоятельных функций и отвечают следующим требованиям: быть конструкционно самостоятельными механизмами, удовлетворять требованиям станков, различных по технологическому назначению; обеспечивать их компоновку в различных сочетаниях и взаимных положениях; соответствовать типам и присоединительным размерам. Широкое применение принципа агрегатирования и стандартизации позволяет свести процесс проектирования к процессу подбора компоновок оборудования из отдельных унифицированных узлов.
|
|
87
Унификация и стандартизация технологической оснастки позволяет использовать ее при смене объектов производства, повысить коэффициент загрузки оснастки и ее эффективность, давая возможность вести обработку деталей большими партиями. Стандартизация оснастки существенно уменьшает затраты времени и средств на ее проектирование, сокращает цикл ее изготовления, является предпосылкой специализации производства, что приводит к сокращению затрат на оснащение.
3. технологических процессах используется несколько видов оснастки:
• универсальная безналадочная оснастка (УБО);
• унифицированная оснастка, в том числе универсально-наладочная (УНО), универсально-сборная, сборно-разборная (СРО), специализированная наладочная (СНО), неразработанная специальная (НСО).
Универсальная безналадочная оснастка применяется для многократной и долговременной установки различных по форме и размерам заготовок, обрабатываемых на универсальных металлорежущих станках. Примерами такой оснастки могут служить универсальные патроны, машинные тиски, делительные головки, поворотные столы и др. Ее преимущества заключаются в небольших сроках и затратах на проектирование и изготовление, разнообразии деталей, для которых они могут применяться, возможности использовать их до полного износа. Основным недостатком УБО является невысокая производительность из-за необходимости постоянно выверять точность установки заготовок.
|
|
Универсально-наладочная оснастка имеет базовую деталь и сменную наладку. Базовая деталь используется многократно. Примером универсально-наладочного приспособления являются универсально-наладочные тиски, патроны со сменными кулачками и др. К недостаткам УНО можно отнести замену сменных наладок раньше их полного износа в связи с необходимостью переходить на выпуск новых изделий.
88
Универсально-сборная оснастка состоит из стандартных деталей
4 узлов многократного использования, изготовленных с высокой степенью точности. Ее недостатком являются высокая стоимость набора и пониженная жесткость конструкции приспособления.
Сборно-разборная оснастка (СРО) состоит из стандартных и специальных деталей; при перекомпоновке на новое изделие возможна доработка стандартных элементов. СРО представляет собой обратимую специальную оснастку долгосрочного применения. Она, как и неразборная специальная оснастка, используется для одной или нескольких деталеопераций.
Специализированная наладочная оснастка применяется для деталей, близких по конструктивно-технологическим признакам, имеющих общие базовые поверхности и одинаковый характер обработки. Эта оснастка состоит из базового агрегата и наладки (или регулируемого элемента). Она допускает регулирование элементов или замену специальной наладки. Детали в этом случае обрабатываются по единому групповому или типовому процессам. Установка осуществляется без выверки, а размеры обеспечиваются автоматически.
Выбор системы оснастки проводится с учетом конструкционно-технологической характеристики обрабатываемых деталей (точность обработки, габаритные размеры, конфигурация заготовок, материал детали), экономических требований к оснащаемой операции (годовой объем выпуска, продолжительность выпуска, темпы оснащения, трудоемкость операций), организационных и технических условий выполнения операций (вид оборудования, вид операции, формы организации производственного процесса).
Технико-экономическое обоснование выбора систем технологического оснащения в соответствии включает в себя расчеты коэффициента загрузки и затрат на оснащение операции.
Коэффициент загрузки каждой единицы технологической операции определяется как формула 2.50.
89
|
Sсмт |
|
tшт1, tшт2 |
(2.50)
где tшт – штучно-калькуляционное время выполнения технологической операции, мин;
Nвып – месячный объем выпуска, шт.;
Фэф – эффективный месячный фонд времени оснастки, ч.
Годовой экономический эффект от применения различных систем оснастки рассчитывается путем сопоставления экономии от сокращения затрат времени на операцию и дополнительных затрат, связанных с применением оснастки.
Экономия, получаемая за счет использования оснастки, снижающей трудоемкость операции (р/год), исчисляется как
(2.51) где Nгод – годовой объем выпуска деталей, шт.;
m– количество наименований деталей, обрабатываемых по типовому или групповому процессу;
– трудоемкость выполнения операций по сравниваемым
вариантам оснащения технологических процессов;
– сметная ставка по данному виду оборудования, р/мин, в которую включаются затраты, связанные с работой оборудования (амортизационные отчисления, затраты на инструмент, вспомогательные материалы, электроэнергия двигательная и др.); Зт – тарифная ставка основного рабочего, р/мин.
Дата добавления: 2018-06-01; просмотров: 346; Мы поможем в написании вашей работы! |
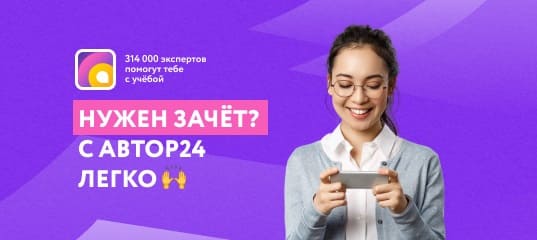
Мы поможем в написании ваших работ!