Пути повышения уровня унификации конструкций
Nbsp;
Тема: Организация подготовки производства
Практическое занятие№2:
I. Дайте определение производственного процесса.
II. Какова структура производственного процесса? Назовите основные принципы организации производственного процесса.
Приведите пример структуры основного производственного процесса. Приведите примеры ручных машинных, аппаратных
процессов.
III.Назовите особенности организации: а)непрерывныхпроцессов;
б) прерывистых процессов.
Назовите их достоинства и недостатки.
IV.Как обеспечивается ритмичность производства?
V.Назвать и охарактеризовать составляющие производственного цикла.
VI.На какие результаты работы предприятия влияет длительность цикла?
VII.Назвать направления сокращения продолжительности цикла.
VIII.Какие факторы ограничивают сокращение продолжительности
цикла?
IX.Характеристика поточного производства, признаки и предпосылки его организации?
X.Основные параметры поточной линии.
XI.Классификация поточных линий.
ТЕОРЕТИЧЕСКИЙ МАТЕРИАЛ ДЛЯ ВЫПОЛНЕНИЯ ПРАКТИЧЕСКОГО ЗАДАНИЯ
1.Организационная структура системы подготовки новой продукции.
и Организация технической подготовки производства. 2.1. Конструкторская подготовка производства
2.2. Содержание и основные этапы технологической подготовки производства. Выбор варианта технологического процесса.
|
|
Главная цель промышленного предприятия – удовлетворить потребности общества в определенных видах продукции. Для успешного функционирования оно должно выпускать конкурентоспособную продукцию высокого технического уровня. В условиях формирования рынка важнейшей задачей предприятия становится изучение потребности и спроса народного хозяйства и населения на ту продукцию, которая выпускается или может выпускаться данным предприятием..
Исследование рынка позволяет установить, на каком этапе жизненного цикла находятся изделия, выпускаемые данным предприятием. Цикл жизни изделия непосредственно в производстве охватывает период от начала промышленного выпуска, наращивания, стабилизации и, наконец, спада выпуска до полного прекращения его производства.
Продолжительность периода промышленного выпуска зависит от технического уровня изделий, от величины экономического эффекта. Подавляющее большинство промышленных предприятий нашей страны были монополистами на закрытом для конкуренции экономическом пространстве. Поэтому они могли в течение данного периода выпускать продукцию, не ощущая спада экономического эффекта. Появление на рынке конкурентоспособных изделий аналогичного назначения зарубежного производства изменило обстановку на рынках сбыта и привело к сокращению продолжительности периодов освоения, к повышению технических и экономических характеристик новых изделий.
|
|
Полный цикл жизни любого изделия включает не только промышленный выпуск, но и время от зарождения идеи, выполнения комплекса исследований и проектных работ, формирования исходных требований к изделию до окончания эксплуатации и потребления.
Поэтому период промышленного выпуска изделия – это только часть жизненного цикла изделия, который делится на следующие стадии: исследование и проектирование, промышленное производство, эксплуатация или потребление, утилизация изделия.
Первый этап жизненного цикла изделия составляет комплекс научно-исследовательских работ (НИР), которые могут носить фундаментальный, поисковый или прикладной характер.
Вторым этапом, выделяемым из непосредственно конструкторских работ, является разработка технического задания (ТЗ). Она осуществляется разработчиком на основе исходных требований к продукции, предъявляемых заказчиком на основе изучения потребительского спроса. В техническом задании определяются цели и назначение разработки, основные источники формирования технических и экономических характеристик проектируемого изделия, стадии разработки с указанием срока ее окончания, порядок контроля и приемки результатов разработки.
|
|
Третий – этап проектно-конструкторских работ (ПКР). Это – разработки технического предложения, эскизного и технического проектов, разработки опытных образцов и серий, проведения необходимых испытаний и создания в итоге рабочей документации для промышленного производства– воплощаются в чертежах и документах, используемых на следующем этапе. На этом этапе повышение экономичности может быть обеспечено в значительной мере за счет унификации и стандартизации изделий, повышения степени их конструктивной преемственности, технологичности и других путей технико-экономической оптимизации вариантов конструкторских решений.
Четвертый этап – технологическая подготовка и освоение производства (ТПП) – включает разработку маршрутной и пооперационной технологии, проектирование и изготовление специальной оснастки и нестандартного оборудования, их отладку и сдачу цехам, организационно-технические мероприятия по быстрому освоению промышленного производства новой продукции.
|
|
66
Пятый этап – непосредственно промышленное производство изделия – охватывает довольно длительный период выпуска данного изделия (и его модификаций), особенно в условиях крупносерийного или массового производства. На этой стадии, как правило, с помощью конструкторских и технологических служб проводится частичная модернизация изделия для улучшения его эксплуатационных характеристик, отдаления срока морального старения.
Для ряда изделий особо выделяется шестой этап – реализация – включающий хранение, транспортировку, монтаж и отладку изделия.
Седьмой этап – эксплуатация – период использования изделия по назначению, когда оно дает экономический или иной положительный эффект от вложенных в его разработку и постановку на производство средств.
И, наконец, восьмой этап – утилизация изделия – стал весьма актуальным в связи с большим вниманием, которое уделяется в настоящее время решению экологических проблем, ликвидации загрязнения окружающей среды. Необходима четкая система утилизации и переработки прошедшей свой цикл продукции.
Первые четыре этапа (научно-исследовательские работы, разработка технического задания, проектно-конструкторские работы, технологическая подготовка и освоение производства) формируют систему технической подготовки создания и освоения новой техники.. Техническая подготовка может осуществляться не только службами предприятия-изготовителя, но и многими предприятиями и организациями вне его. По месту выполнения работы по технической подготовке можно подразделить на внезаводские и внутризаводские.
Внезаводскую подготовку производства могут осуществлять отраслевые конструкторские бюро (ОКБ), специализированные конструкторско-технологические бюро (СКТБ), проектные и научно-исследовательские институты, высшие учебные заведения. Эти организации устанавливают потребность в изделиях с учетом потребности внутреннего и внешнего рынков, определяют технико-
67
экономические параметры конкурентоспособности изделий, выполняют комплекс научно-исследовательских работ, а также совместно с заказчиком и заводом-изготовителем осуществляют проектирование новых конструкций. Внутризаводская подготовка производства проводится непосредственно заводом, выпускающим продукцию. В зависимости от принятой на заводе системы организации технической подготовки она предусматривает либо работы по совершенствованию серийного производства выпускаемых изделий и освоению производства новых и модернизированных изделий, либо весь комплекс работ, включающий проектирование новых конструкций и подготовку их серийного производства.
Отдельные этапы технической подготовки регламентировались стандартами. Например, ГОСТ 15.001-73 "Разработка и постановка продукции на производство. Основные положения" содержал типовые этапы опытно-конструкторских работ.
Организация конструкторской подготовки производства
Продукции
Информация, полученная в результате проведения научно-
исследовательских работ, патентных исследований, экспериментальных исследований новых рабочих процессов, кинематических схем, материалов, конструктивных элементов, позволяет начать техническую подготовку производства новой продукции. Первым ее этапом является конструкторскаяподготовка,от уровня организации которой во многом зависиткачество объектов новой техники, ее экономическая эффективность и сроки освоения.
Конструкторская подготовка должна обеспечить создание новых машин, оборудования и механизмов, не только соответствующих современному уровню техники, но и значительно превосходящих этот достигнутый уровень. Проектирование нового изделия в соответствии с требованием ГОСТ 2.103-68 ЕСКД (единая система конструкторской документации) включает разработку:
68
• технического задания на проектирование (ТЗ);
• технического предложения;
• эскизного проекта;
• технического проекта;
• рабочей документации.
Согласно ГОСТ 15.001-78 в техническое задание, подготавливаемое организацией-разработчиком на основе исходных требований заказчика, входят:
1. наименование объекта разработки и область его применения;
2. основание для разработки, т. е. перечень документов, регламентирующих разработку;
3. цель, эксплуатационное и функциональное назначение, перспективность разработки, т. е. перечень НИР, патентов, публикаций и т. д.;
4. технические (или тактико-технические) требования: состав продукции, показатели назначения, надежности, технологичности, степень унификации и стандартизации, безопасность, эстетика и эргономика, перечень стран, в отношении которых должна быть обеспечена патентная чистота, условия эксплуатации, транспортировки, хранения и др.;
5. экономические показатели: ориентировочная экономическая эффективность, лимитная (договорная) цена, годовая потребность, сопоставление с лучшими отечественными и зарубежными образцами;
6. перечень стадий и этапов разработки;
7. порядок контроля и приема работ.
Техническое задание определяет назначение новой конструкции, основные эксплуатационные (производительность, мощность, надежность, скорость и т. д.) и конструкторские (масса, габариты и т. д.) показатели, потребность в изделии на перспективу и ориентировочный годовой объем его выпуска.
Следующей стадией конструкторской подготовки выступает разработка технического предложения разработчика (ЕСКД, ГОСТ
69
2.118-73), которое должно содержать технико-экономическое обоснование разработки данной конструкторской документации на основе анализа технического задания, вариантов возможных решений, патентных материалов.
На таком этапе проектирования, как выполнение эскизногопроекта,всоответствии с требованием ГОСТ2.119-73разрабатываются основные принципиальные схемы изделия, чертежи общих видов, составляются спецификации сборочных единиц, в том числе унифицированных и покупных. Основное назначение эскизного проекта – выбор наилучшего варианта конструкции изделия. В эскизном проекте содержатся конструктивные решения, дающие общее представление об устройстве и принципе работы изделия, а также основные параметры и габаритные размеры разрабатываемого изделия и его составных частей.
• техническом проекте (по ГОСТ2.120-73)наиболеетрудоемкими являются работы, связанные с разработкой отдельных узлов и агрегатов изделия. На этой стадии требуется осуществить конструкторское оформление всех компонентов изделия, провести большое количество расчетов, связанных с обеспечением прочности, жесткости, надежности всех сборочных единиц изделия, обеспечить минимальные издержки производства при соблюдении всех эксплуатационных требований к изделию, т. е. добиться высокой технологичности конструкции для заданных объемов и условий производства. На этой стадии проектирования особую важность приобретает тесная взаимосвязь конструкторов и технологов, способствующая тому, чтобы обеспечить изготовление элементов конструкции наиболее производительными технологическими способами.
Стадия технического проекта заканчивается составлением пояснительной записки. В нее входят конструкторские расчеты и технико-экономическое обоснование проекта. Пояснительная записка
с приложенными к ней чертежами, схемами и другими техническими документами представляет собой проект, содержащий окончательные
70
технические решения и дающий полное представление об устройстве разрабатываемого изделия:
Проектно-конструкторские работы представляют собой комплекс длительных, сложных и дорогих процессов. Однако стремление сократить сроки и затраты может привести к созданию конструкций низкого качества, которые или будут сняты с производства, или будут требовать многочисленных доработок в процессе технологической подготовки. Недостаточный объем испытаний в процессе создания опытного образца или установочной серии приводит к. к невыявленным дефектам конструкции, которые затем проявляются в эксплуатации.
1) другой стороны, большая длительность проектно-конструкторских работ может привести к тому, что к моменту запуска в производство конструкция будет морально устаревшей и опять-таки ее надо будет снимать с производства или вообще отказаться от ее изготовления. Поэтому так важны основные организационно-экономические пути сокращения сроков конструкторской подготовки при сохранении высокого качества проектных разработок, таких как: широкое применение стандартизации и унификации, обеспечение технологичности конструкций, наличие и использование информационно-поисковых систем, организация системы автоматизированного проектирования (САПР) и др.
Пути повышения уровня унификации конструкций
Одной из эффективных мер, позволяющих повысить качество изделий, уменьшить трудоемкость и сократить цикл подготовки производства, является применение типовых конструкторских решений, базирующихся на принципах унификации и стандартизации.
Конструктивная унификация – это комплекс мероприятий,устраняющих необоснованное многообразие типов и конструкций изделий, форм и размеров деталей и заготовок, профилей и марок материалов. Унификация создает условия для использования
71
преимуществ специализированного производства повторяющихся изделий и их элементов.
Унификация является базой агрегатирования, т. е. создания изделий путем их компоновки из ограниченного числа унифицированных элементов, и конструктивной преемственности, т. е. применения в конструкции нового изделия уже освоенных в производстве сборочных единиц и деталей.
Конструктивная унификация выступает составной частью комплексной унификации всего производственного процесса, включая техническую подготовку производства. Производственная унификация предполагает единообразие требований не только к разработке конструкций, но и другим факторам производства – применяемым технологическим процессам, в том числе технологической оснастке, видам оборудования и др. Основными методами производственной унификации являются стандартизация, типизация технологических процессов, внедрение групповых методов обработки, универсализация и нормализация технологической оснастки и таких элементов конструкции, как диаметры посадки, резьбы, радиусы гантелей и др.
Стандарты суть нормы, образцы, типовые виды изделий, удовлетворяющие определенным условиям. Международная организация по стандартизации (ИСО), членом которой является и наша страна, приняла такое определение термина "стандартизация": "Стандартизация – это процесс установления и применения правил с целью упорядочения деятельности в данной области на пользу и при участии всех заинтересованных сторон, в частности, для достижения всеобщей максимальной экономии, с соблюдением функциональных условий и требований безопасности".
Важнейшей задачей стандартизации является отбор всего лучшего из того, что имеется, узаконение его и внедрение в промышленность с целью повышения технического уровня и качества продукции при одновременном снижении затрат на производство и эксплуатацию изделия. Стандартизация базируется на
72
результатах научных исследований и обобщении практического опыта.
Одним из направлений конструктивной унификации выступает сокращение номенклатуры изделий, имеющих одинаковое или сходное эксплуатационное назначение. Оно реализуется, в первую очередь, путем создания параметрических рядов (гамм) изделий. Каждый ряд представляет собой совокупность изделий, аналогичных по своей кинематике, рабочему процессу, но различных по габаритным, мощностным и другим эксплуатационным параметрам
(грузоподъемность автомобилей, кранов, мощность электродвигателей, производительность компрессоров и др.)..
2) зависимости от характера и назначения унификация может проводиться на базе существующих конструкций путем отбора лучших образцов изделий и их элементов или же путем создания новых изделий на основе использования унифицированных агрегатов, узлов и деталей. Следовательно, конструктивная унификация может осуществляться методами стандартизации, типизации, агрегирования
с конструктивной преемственности. В каждом конструктивном ряду устанавливается базовая модель, которая служит исходной для создания различных ее модификаций. Логическим завершением работ по унификации является агрегатирование.
Агрегатирование –это метод создания машин путем ихкомпоновки из ограниченного числа унифицированных элементов, и в первую очередь законченных агрегатов. Эффективны принципы агрегатирования при создании технологического оборудования и средств механизации и автоматизации машиностроительного производства. Основными преимуществами метода агрегатирования являются сокращение в 2-3 раза сроков создания агрегатных станков
с автоматических линий, значительное их удешевление и возможность быстрого переналаживания линии при смене объектов производства.
Другим направлением конструктивной унификации можно считать сокращение в аналогичных (иногда и в разнородных)
73
изделиях номенклатуры сборочных единиц и деталей за счет стандартизации и конструктивной преемственности.Вбольшинстве отраслей машиностроения органами стандартизации периодически издаются альбомы рабочих чертежей унифицированных узлов и деталей, которые конструкторы обязаны использовать наряду со стандартами.
Количественная оценка работ по унификации производится согласно "Методическим указаниям определения уровня унификации
в стандартизации" В них предусмотрены три показателя уровня унификации: коэффициент преемственности Кпр, коэффициент повторяемости Кпи коэффициент) унификации Км.у. Первые два показателя применяются для оценки уровня унификации и
стандартизации конкретного изделия, а третий – для группы изделий. Коэффициент преемственности Кпр определяется как отношение количества заимствованных типоразмеров составных частей в изделии (без оригинальных) к общему количеству типоразмеров
составных частей в изделии П (в процентах) по формуле 2.38:
(2.38)
где По – количество оригинальных типоразмеров составных частей в изделии, разработанных впервые для данного изделия.
Количественная оценка не всегда в полной мере характеризует эффективность унификации. При высоком уровне унификации неунифицированные, оригинальные детали, составляя меньшую долю по количеству, могут быть весьма трудоемки в проектировании и изготовлении. Поэтому желательно оценить уровень унификации не только количественно, но и с качественной стороны – по массе, трудоемкости и стоимости.
Коэффициент унификации по массе можно рассчитать по формуле 2.39:
(2.39)
гдеQу– масса унифицированных деталей;
74
Qоб – масса всех деталей (всего изделия).
Коэффициент унификации по себестоимости исчисляется по следующим формуле 2.40.:
(2.40)
где Су и Соб – себестоимость единицы массы унифицированных деталей и всего изделия, соответственно;
Sу и Sоб – средняя стоимость одного нормо-часа унифицированных деталей и всего изделия, соответственно.
Приведенные выше показатели унификации по массе, трудоемкости и стоимости можно представить в виде комплексного показателя формула 2.41.
(2.41)
Этот показатель характеризует отношение части производственных затрат на изготовление унифицированных деталей к производственным затратам на изготовление всего изделия в целом.
Коэффициент повторяемости Кп – отношение повторяющихся составных частей изделия (насыщенность изделия повторяющимися составными частями) в процентах, т. е. уровень внутрипроектной унификации изделия и взаимозаменяемость составных частей внутри изделия (формула 2.42):
(2.42)
где N – общее количество составных частей в изделии.
Коэффициент) унификации определяется по формуле 2.43.
(2.43)
где m – общее количество рассматриваемых проектов (изделий);
ni – количество типоразмеров составных частей в i-м проекте;
nmax – максимальное количество типоразмеров составных частей одного проекта (изделия);
75
В – общее количество типоразмеров в группе из n проектов. Эффективность унификации в самом общем виде может быть
выражена через коэффициент эффективности унификации, равный отношению полученного эффекта (экономии) от унификации (Эу) к затратам, его вызвавшим (Sy) формула 2.44:
(2.44)
r организации работ по унификации и стандартизации есть ряд недостатков. Слабо развито специализированное производство унифицированных и стандартных сборочных единиц и деталей, объемы выпуска которых в данной связи занижены, что препятствует автоматизации их производства. В итоге многие виды техники имеют явно завышенную себестоимость и оптовую цену. Медленно происходит обновление стандартов и технических условий.
Технологичность конструкций и пути ее обеспеченияСоздание новых конструкций изделий, обладающих высокими
технико-экономическими характеристиками, является сложной комплексной задачей, для решения которой прежде всего необходимо обеспечить максимальную возможную для данных условий производственную и эксплуатационную технологичность конструкций.
Производственной технологичностью называется степеньсоответствия конструкции изделия оптимальным производственно-технологическим условиям его изготовления при заданном объеме выпуска; технологичной можно считать только ту, удовлетворяющую эксплуатационным требованиям конструкцию, освоение и выпуск которой при заданном объеме производства будут протекать с минимальными производственными издержками (в первую очередь, с наименьшей трудоемкостью и материалоемкостью) и с кратчайшим производственным циклом.
76
Эксплуатационная технологичность конструкции изделияпроявляется в сокращении затрат времени и средств на техническое обслуживание и ремонт изделий, зависящих от так называемой ремонтопригодности конструкции – ее приспособленности к предупреждению, обнаружению и устранению отказов и неисправностей.
Для обеспечения производственной технологичности необходимо придать изделию такую форму и выбрать для него такие материалы, которые обусловят наиболее простое и экономичное его изготовление. Изделие, технологичное в условиях мелкосерийного производства, может оказаться совершенно нетехнологичным при его массовом выпуске (и наоборот). К нетехнологичным следует относить конструкции, изготовление которых известными в данный момент средствами либо невозможно, либо вызывает существенное и неоправданное усложнение технологических операций и увеличение их трудоемкости, а также ведет к росту материалоемкости изделий.
Производственная технологичность конструкций оценивается рядом показателей: материалоемкостью, трудоемкостью изготовления, себестоимостью, производственным циклом, а для некоторых изделий – еще и трудоемкостью и циклом монтажа у потребителя.
Уровень производственной технологичности характеризуется как абсолютными, так и относительными показателями. Абсолютные показатели включают: массу изделия и его элементов, нормы расхода материалов, квалитет, класс шероховатости поверхности, общую трудоемкость производства изделия и как итоговый показатель затраты на изготовление. Относительные показатели – это в основном различные коэффициенты, связанные с унификацией и стандартизацией.
Технологичность проектируемого изделия должна оцениваться не только с точки зрения производства, но и со стороны ее эксплуатации. К показателям эксплуатационной технологичности необходимо отнести: удельную трудоемкость профилактического
77
обслуживания, трудоемкость ремонта, удельные затраты на обслуживание и ремонты.
На стадиях проектирования технологичность конструкции обеспечивается в основном конструктором. Однако не следует забывать, что это достаточно комплексная и конкретная задача. Комплексная потому, что к ее решению должны привлекаться кроме конструкторского отдела и другие службы завода (технологический отдел, отделы материально-технического обеспечения, технического контроля и др.). Конкретная потому, что она должна решаться исходя из конкретных производственных возможностей (наличие необходимых материалов, оборудования необходимых параметров по габаритам и точности, возможности их приобретения, возможности привлечения работников необходимой квалификации и т. п.), с учетом перспектив развития производства.
Дата добавления: 2018-06-01; просмотров: 489; Мы поможем в написании вашей работы! |
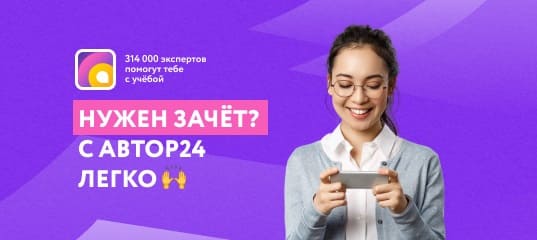
Мы поможем в написании ваших работ!