Манометрические методы контроля герметичности.
Манометрический метод используется для контроля герметичности трубопроводов и задвижек. В трубопроводе создается давление воды или газа, и по уменьшению давления судят об исправности задвижек или утечке. Для осуществления контроля манометрическим методом изделие заполняют пробным газом под давлением выше атмосферного и выдерживают в течение определенного времени. Давление и время опрессовки устанавливаются техническими условиями на изделие или конструкторской (проектной) документацией. Изделие считают герметичным, если падение давления пробного газа во время выдержки под давлением не превысит норм, установленных техническими условиями или конструкторской (проектной) документацией. Давление газа измеряют манометрами класса точности 1,5 - 2,5 с пределом измерения на 1/3 больше давления опрессовки. На подводящей трубе должен быть установлен запорный кран для регулирования подачи газа. Количественная оценка общей негерметичности проводится по формуле QV =ΔP/t, где V - внутренний объем изделия и элементов испытательной системы, а ΔP - изменение давления пробного газа за время опрессовки, Па; t - время опрессовки, с.
Пузырьковые методы контроля. Разновидности.
Пузырьковый метод контроля герметичности предназначен для специалистов лабораторий, выполняющих неразрушающий контроль и испытания металлов, сплавов и сварных соединений.
|
|
Методы контроля герметичности соединений назначают в зависимости от условий эксплуатации изделий, типа конструкции и других факторов. Контроль, осуществляемый после внешнего осмотра, основан на способности газов и жидкостей проникать через несплошности. Для проведения испытаний используют керосин, аммиак, воздух, воду, гелий и др.
При испытании керосином поверхность, доступную для осмотра, покрывают водной суспензией мела или каолина и подсушивают. Противоположную сторону шва два-три раза смачивают керосином. Дефекты в шве обнаруживаются по появлению жирных желтых пятен на окрашенной поверхности. Таким методом испытывают сосуды, работающие без внутреннего давления с толщиной стенки до 16 мм и размером дефекта свыше 0,1 мм. Продолжительность испытания должна составлять не менее 12 ч при положительной температуре и не менее 26 ч — при отрицательной.
При пневматическом испытании (ГОСТ3242—79) сжатый газ (воздух, инертные газы и др.) подают в испытуемый сосуд под давлением, несколько превышающем рабочее. Плотность сварных соединений проверяют мыльным раствором или погружением сосуда в воду.
При гидравлическом испытании (ГОСТ 3845—75) все отверстия в изделии плотно закрывают заглушками и через штуцер заполняют изделие водой. С помощью гидравлического насоса создают давление, в 1,25...1,5 раза превышающее рабочее. О наличии дефектов судят по появлению на противоположной стороне шва течи, капель или следов жидкости. Данный вид испытаний применяют при проверке герметичности сварных соединений паровых и водяных котлов, трубопроводов и сосудов, работающих под давлением.
|
|
Химический метод контроля герметичности.
Химические методы контроля герметичности изделий основаны на использовании химических реакций для индикации течей. На контролируемые стыки наносят индикаторный слой массы, пасты или накладывают индикаторную ленту (бумажную, марлевую и т. п.). В изделии создается избыточное давление пробного газа. Пробный газ (аммиак, С02 и их смеси с воздухом или азотом) проникает через неплотности шва и, вступая в химическую реакцию с индикатором, образует пятна.
Способ контроля воздухом с добавлением аммиака (предложен С. Т. Назаровым) заключается в том, что швы испытуемого изделия покрывают бумажной лентой, смоченной 5%-ным раствором азотнокислой ртути или раствором фенолфталеина. Затем в сосуд подается воздух в смеси с 1—10% аммиака. Аммиак, проникая через неплотности, действует на бумагу и оставляет на ней черные или фиолетовые пятна, фиксируя дефекты. Бумагу выдерживают обычно 1—15 мин. Способ обладает значительно более высокой чувствительностью и большей производительностью, чем испытания с мыльной водой. В зависимости от времени выдержки чувствительность может достигать до 20 см3-ат/год, т. е. 5-Ю-4 л-мкм/с.
|
|
Желеобразные массы, применяемые для контроля герметичности с аммиаком, включают: индикатор креозоловый красный, водорастворимый и спирторастворимый (по 0,007%), агар и спирт (по 1%) глицерин (10%) и дистиллированную воду (остальное). Эта масса и воздушно-аммиачная смесь не оказывают коррозионного действия на алюминиевые и жаропрочные сплавы.
При использовании С02 простейшая индикаторная масса имеет состав (в массовых частях): дистиллят-40, агар-1, фенолфталеин — 0,15, безводная сода — 0,01. Места негерметичности фиксируются бесцветными пятнами на малиновом фоне массы. Чувствительность 4 10~2 л-мкм/с. При других составах индикаторных масс чувствительность может быть повышена до 10~3 л-мкм/с.
Течеискатели.
Существуют два типа течеискателей: масс-спектрометрический (гелиевый) и галоидно-электрический (галоидный).
|
|
Принцип работы гелиевых течеискателей основан на выделении из комплекса газов, поступающих в камеру масс-спектрометра течеискателя, гелия. Этот газ применяют в качестве индикатора.
Попадание гелия в камеру масс-спектрометра обеспечивается присоединением течеискателя или к вакуумированному изделию, или к камере, наполненной гелием, до некоторого избыточного давления, в которую помещают изделие. Увеличение парциального давления гелия в камере масс-спектрометра, вызванное прониканием гелия через дефектное место, фиксируется одновременно выносным стрелочным прибором и звуковым сигналом.
Эффективность контроля герметичности изделий в большой степени зависит от состояния внутренней и наружной поверхности контролируемого изделия. Механические загрязнения (шлак, окалина, абразивная пыль), влага, масла и другие вещества на стенках изделия резко снижают надежность контроля.
Гелий, пройдя через неплотности, попадает в камеру масс-спектрометра, где давление составляет 5*10~в мм рт. ст., Камера масс-спектрометра находится в магнитном поле напряженностью порядка 1,3—1,4 МА/м. Камера имеет латунный корпус, в котором помещены катод, ионизатор, диафрагмы и коллектор ионов. Катод эмиттирует поток электронов, которые ионизируют встречающиеся молекулы газа, превращая их в положительные ионы с зарядом е.
Ионы ускоряются напряжением 300—400 В в продольном электрическом поле. Затем ионный пучок попадает в камеру масс-спектрометра и под действием магнитного поля ионы попадают на круговую тракторию. Ионы с разным отношением массы т к заряду е летят по разным радиусам. Диафрагмы выделяют только ионы с определенным т/е, которые попадают на коллектор. Ионный ток усиливается и передается на индикаторы: миллиамперметр и сирену.
По схеме галоидноготечеискателя в испытуемый сосуд подают воздух в смеси с галоидным газом (фреон, SF6,CCl4, хлороформ и др.) под давлением 0,2-0,6 атм. Смесь проходит через неплотности и прогоняется через межэлектродный промежуток щупа. Анод щупа нагрет до температуры 800-900 0С. Ионы галоидного газа имеют высокий отрицательный потенциал. Попадая в щуп, они вызывают резкое увеличение потока положительных ионов с анода, что приводит к значительному изменению ионного тока. Индикаторами служат миллиамперметр и телефон. Применяют установки ГТИ-2, ГТИ-3, ВАГТИ-4.
Перед испытанием галоидным течеискателем изделия проверяют менее чувствительными методами — гидравлическими и пневматическими с опрессовкой азотом или воздухом. После устранения грубых течей аппарат вакуумируют до давления 30—40 мм рт. ст. Затем подают под давлением фреон или смесь фреона с воздухом или азотом, взятых в отношении 1 : 10. При испытании предусматривают отсос воздуха со скоростью 0,2—0,3 м/с, а также возможность откачки фреона за пределы цеха.
Дата добавления: 2018-06-01; просмотров: 2309; Мы поможем в написании вашей работы! |
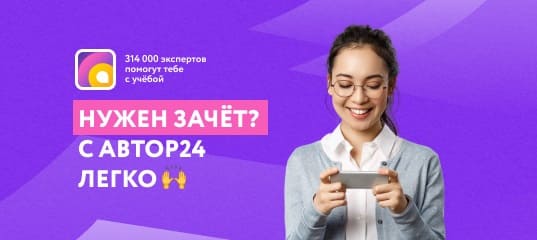
Мы поможем в написании ваших работ!