Классификация вихретоковых преобразователей.
Электромагнитные методы подразделяют в основном по полезащитным системам. Полезадающие системы могут быть проходными, если катушка с током охватывает деталь или вставляется в нее, и накладными, когда катушку с током устанавливают на деталь торцом. В первом случае электромагнитная волна от полезадающей системы распространяется в направлении контролируемого объекта, во втором — вдоль его поверхности. Измерительные катушки (датчики) могут быть выполнены отдельно от полезадающих (генераторных) и обычно располагаются вблизи поверхности контролируемого изделия. Накладные преобразователи выполняют с ферромагнитным сердечником или без него. Ферромагнитный сердечник (обычно ферритовый) повышает абсолютную чувствительность преобразователя и уменьшает зону контроля за счет локализации магнитного потока.
Проходные вихретоковые преобразователи (ВТП) подразделяют на наружные и внутренние. Такая классификация проходных преобразователей основана на том, что они в процессе контроля проходят или снаружи объекта, охватывая его, или внутри объекта.
Накладные ВТП применяют в основном при контроле качества объектов с плоскими поверхностями и объектов сложной формы, а также в тех случаях, когда требуется обеспечить локальность и высокую чувствительность.
Наружные проходные ВТП используют при контроле линейно-протяжных объектов (проволоки, прутка, трубы и т. д.), а также при массовом контроле мелких изделий. Внутренними проходными ВТП контролируют внутренние поверхности трубы, а также стенки отверстий в различных деталях.
|
|
Дефектоскопы с проходными преобразователями. При автоматизированном, высокоскоростном и бесконтактном контроле качества эффективно применяют дефектоскопы с проходными преобразователями, позволяющими проверять в широком диапазоне типоразмеров протяженные объекты (трубы, прутки, проволоку с поперечными размерами 0,15—135 мм) и мелкие детали (шарики и ролики подшипников, метизы и т. д.). При этом производительность контроля может достигать 50 м/с (для проволоки) или несколько тысяч мелких деталей в час. Производительность контроля труб, прутков ограничивается инерционностью устройств транспортирования и разбраковки и редко превышает 3 м/с. Основной параметр дефектоскопа - порог чувствительности — определяется минимальными размерами дефекта заданной формы, при которых отношение сигнал/помеха равно двум. Порог чувствительности устанавливают по образцу с искусственными дефектами различной формы, например в виде отверстий разного диаметра и глубины в трубах и прутках, в виде продольных рисок на проволоке и т. д.
|
|
Реальный порог чувствительности зависит от уровня помех, связанных с вариацией параметров объекта, например шероховатости поверхности и др. Порог чувствительности дефектоскопа с проходными преобразователями обычно определяется глубиной узкого длинного продольного дефекта, выраженной в процентах от поперечного размера (диаметра детали).
Дефектоскопы отличаются главным образом конструкцией, наличием блоков сортировки, блоков представления и регистрации информации, блоков маркировки дефектных участков, блоков подмагничивания и т. д.
Дефектоскопы с накладными преобразователями:
Для контроля линейно-протяжённых объектов круглого сечения (прутки, трубы) применяют сканирующие дефектоскопы с вращающимися вокруг объекта накладными преобразователями. Для контроля плоских деталей разработаны дефектоскопы с преобразователями вращающимися в плоскости параллельной детали.
Радиационные методы контроля. Классификация и фазические основы.
Любой из известных методов радиационной дефектоскопии предполагает обязательное использование, как минимум, трех основных элементов: источника ионизирующего излучения; контролируемого объекта (сварного соединения); детектора, регистрирующего дефектоскопическую информацию.
|
|
При прохождении через вещество изделия ионизирующего излучения происходит его ослабление — поглощение и рассеяние. Степень ослабления зависит от толщины и плотности р контролируемого объекта, а также от интенсивности М и энергии Е самого излучения. Наличие в веществе внутренних дефектов размером
приводит к резкому изменению интенсивности и энергии выходящего пучка излучения. Иными словами, выходящий пучок несет дефектоскопическую информацию о внутренней структуре контролируемого объекта.
Различают следующие методы: радиографический, радиоскопический и радиометрический.
Радиография — метод получения на детекторах статического видимого изображения внутренней структуры изделия, просвечиваемого ионизирующим излучением. На практике этот метод получил наибольшее распространение в связи с его простотой и документальным подтверждением получаемых результатов. В зависимости от используемых детекторов различают пленочную радиографию и ксерорадиографию (электрорадиографию). В первом случае детектором скрытого изображения и регистратором статического видимого изображения служит фоточувствительная пленка. При ксерорадиографии детектором служат полупроводниковые пластины, а в качестве регистратора используют обычную бумагу.
|
|
В зависимости от используемого излучения различают несколько разновидностей радиографии: рентгенографию, гаммаграфию, бета-тронную и нейтронную. Каждый из перечисленных методов имеет свою сферу использования, дополняя и обогащая друг друга. В частности, рентгенографию применяют преимущественно в цеховых и реже в полевых условиях в случаях, когда к контролю качества сварных соединений предъявляются наивысшие требования по чувствительности. Гаммаграфия доминирует при контроле качества сварных соединений, расположенных в труднодоступных местах, в полевых и монтажных условиях. Бетатронную радиографию используют при дефектоскопии сварных соединений большой толщины преимущественно в цеховых условиях. Нейтронная радиография — единственный метод, обеспечивающий контроль качества
сварных соединений тяжелых металлов, водородосодержащих материалов и радиоактивных изделий.
Применяя перечисленные методы, возможно просвечивать стальные сварные соединения толщиной 1—500 мм, обеспечивая при этом чувствительность к выявлению дефектов 1—2%.
Радиоскопия (радиационная интроскопия) — метод получения на экране видимого динамического изображения внутренней структуры изделия, просвечиваемого ионизирующим излучением. Чувствительность этого метода несколько уступает радиографии. К числу его преимуществ относится повышенная достоверность получаемых результатов за счет возможности стереоскопического видения дефектов и рассмотрения сварного соединения под разными углами, «экспрессность» и непрерывность контроля. Применение метода радиационной интроскопии в промышленности непрерывно растет.
Источниками излучения обычно служат рентгеновские аппараты. Значительно реже используют радиоизотопные источники у-излучения, источники нейтронов и ускорители. Детекторами излучения служат флуороскопические экраны, сцинтилляционные кристаллы, электронно-оптические преобразователи, рентген-видиконы и др. Они обеспечивают преобразование скрытого радиационного изображения изделия в светотеневое или электронное изображение и передачу этих изображений на расстояние посредством оптики или телевидения.
Радиометрическая дефектоскопия— метод получения информации о внутреннем состоянии контролируемого изделия, просвечиваемого ионизирующим излучением, в виде электрических сигналов (различной величины, длительности или количества). Этот метод обеспечивает наибольшие возможности автоматизации процесса контроля и осуществления автоматической обратной связи от контроля к технологическому процессу сварки или изготовления изделия. К числу несомненных преимуществ метода относится возможность проведения непрерывного высокопроизводительного контроля качества изделия, обусловленная высоким быстродействием применяемой аппаратуры.
Дата добавления: 2018-06-01; просмотров: 899; Мы поможем в написании вашей работы! |
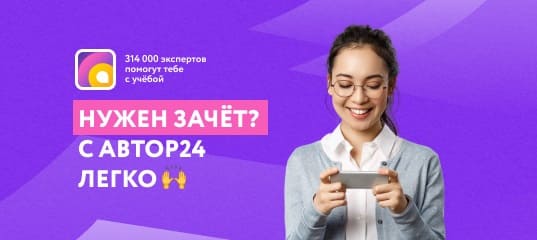
Мы поможем в написании ваших работ!