Чувствительность капиллярных методов контроля
Чувствительность капиллярного неразрушающего контроля – это качество контроля, характеризуемое порогом, классом и дифференциальной чувствительностью средств контроля в отдельности, либо целесообразным сочетанием.
Чувствительность метода капиллярной дефектоскопии условно определяется наименьшими значениями раскрытия, глубины и длины надежно выявляемого дефекта (типа трещины) по его индикаторному следу.
Порог чувствительности капиллярного метода – это раскрытие несплошности типа единичной трещины определенной длины, выявляемое с заданной вероятностью по заданным геометрическому или оптическому параметрам следа.
Чувствительность характеризуется нижним и верхним порогами.
Нижний порог чувствительности определяется максимальной величиной раскрытия протяженного дефекта.
Верхний порог чувствительности определяется минимальной величиной раскрытия протяженного дефекта.
Чувствительность капиллярного метода определяется в соответствии с ГОСТ 18422 – 80 в зависимости от минимального размера выявляемых дефектов с поперечными размерами 0,1 – 500 мкм (таблица 1).
С чувствительностью по I классу контролируют лопатки турбореактивных двигателей, уплотнительные поверхности клапанов и их гнезд, металлические уплотнительные прокладки фланцев и др. По II классу проверяют корпуса и антикоррозионные наплавки реакторов, основной металл и сварные соединения трубопроводов, детали подшипников (выявляемые трещины и поры в несколько мкм). По III классу проверяют крепеж ряда объектов, с возможностью выявления дефектов с раcкрытием до 100 мкм, по IV классу – толcтостенное
|
|
литье.
Таблица 1
Классы чувствительности в зависимости от размеров выявляемых
дефектов (ГОСТ18422 – 80)
Класс чувствительности | Минимальный размер, (ширина раскрытия) дефектов, мкм |
I | менее 1 |
II | от 1 до 10 |
III | от 10 до 100 |
IV | от 100до 500 |
технологический | не нормируется |
Нумерация уровней (классов) чувствительности по зарубежным стандартам MIL - 1-2513SE, AMS - 2644 и российскому ГОСТ 18442 – 80 не совпадает, по американскому стандарту уровень I – низкий, а по нашему ГОСТу класс чувствительности I самый высокий. Например, в немецком промышленном стандарте DIN 54 – 152 чувствительность пенетрантов разделяется на четыре класса в соответствии с табл. 2.
Чувствительность определяют на стандартных образцах (ГОСТ 23349 –84) предприятий по количеству и яркости индикаторных следов выявленных дефектов. Размеры дефектов в стандартных образцах определяют металлографическим или другими методами анализа.
Основные капиллярные методы по чувствительности, определяемой наименьшим размером уверенно выявляемого дефекта, можно расположить в порядке уменьшения чувствительности следующим образом:
|
|
– люминесцентный, последующего эмульгирования;
– люминесцентный, удаляемый растворителем;
– люминесцентный, смываемый водой;
– цветной, последующего эмульгирования;
– цветной, удаляемый растворителем;
– цветной, смываемый водой.
Таблица 2
Чувствительность капиллярного метода в зависимости
от минимального размера выявляемых дефектов (DIN 54 – 152)
Класс чувствительности | Ширина раскрытия дефектов, мкм | Толщина никелевого покрытия, мкм |
I – низкий | 4 | 100 |
II – средний | 2 | 60 |
III – средний | 1 | 60 |
IV – средний | 0,6 | 50 |
Установленный класс чувствительности дефектоскопических материалов достигается при:
– использовании аттестованного набора дефектоскопических материалов, обладающего требуемой чувствительностью;
– соблюдении заданной технологической последовательности операций;
– соответствии атмосферных условий (температуры, влажности, скорости воздуха) требуемым для правильного использования дефектоскопических материалов и аппаратуры;
– соответствии шероховатости поверхности объектов контроля требованиям набора дефектоскопических материалов;
|
|
– удалении загрязнений с поверхности объектов контроля и обеспечении доступа пенетранта в полости дефектов;
– выявлении дефектов конкретных типов;
– условии наличия соответствующей классификации у контролера (дефектоскописта).
На чувствительность КНМ оказывает влияние:
а) правильность выбора пенетранта;
б) смачивающая способность основного компонента;
в) свойства адсорбирующего вещества;
г) качества подготовки поверхности:
- загрязненность поверхности, посторонние вещества (нагар, шлаки, смазочные масла) препятствуют проникновению пенетранта в дефекты;
– уровень шероховатости поверхности;
– «заволакивание» поверхностных дефектов при механической обработке – дробеструйном наклепе при упрочнении закаленных деталей, пескоструйной обработке, очистке поверхностной щеткой, обработкой резанием;
д) вид очистителя;
е) температура (при снижении температуры чувствительность уменьшается).
Дефектоскопические материалы
Дефектоскопические материалы – специализированные вещества, предназначенные для пропитки, нейтрализации или удаления избытка проникающего вещества с поверхности и проявления его остатков с целью получения первичной информации о наличии несплошности в объекте контроля. Их выбирают в зависимости от требований, предъявляемых к контролируемому изделию, его состояния и условий работы. Их комплектуют в целевые наборы, в которые входят совместимые дефектоскопические материалы:
|
|
И – индикаторный пенетрант;
М – очиститель объекта контроля от пенетранта;
Г – гаситель пенетранта;
П – проявитель пенетранта.
Очистители поверхности
Очистители поверхности изделия от загрязнений – это органические растворители, которые применяют для очистки и обезжиривания изделия перед контролем. Они должны обладать высокой растворяющей способностью по отношению ко всем видам загрязнений, легко проникать в полости дефектов, после чего относительно быстро испаряться, очищая их полости. В качестве растворителей применяют технический ацетон, авиационный бензин, технический бензин, растворители 645, 646, метиленхлорид, четыреххлористый углерод и другое.
Ацетон применяют для удаления сложных растворителей, окончательной промывки слабозагрязненных деталей, а также для чистовой промывки перед повторным дефектоскопированием.
Детали, работавшие в минеральных маслах (коленчатые валы, поршни и другие тепловозные детали), вначале отмывают авиационным бензином, а затем ацетоном. Бензин лучше, чем ацетон, растворяет минеральные масла, смазки, жиры некоторые природные и искусственные смолы и красители. Его применяют для удаления керосина из внутренней полости трещины.
Растворитель 645 применяют в промышленности для разбавления нитроцеллюлозных лаков и эмалей. При дефектоскопии деталей его используют для очистки деталей от масел, жиров, мыл, мягкого сажистого нагара, некоторых искусственных и природных смол. Некоторые компоненты растворителя 645 сравнительно медленно испаряются и долго удерживаются в полостях дефектов. Поэтому после обработки растворителем 645 детали промывают ацетоном. Для очистки деталей также применяют растворители Р4 и 646.
Для удаления продуктов коррозии с поверхности деталей выполняют следующие операции: обезжиривание, травление, промывку водой, нейтрализацию применяемых реактивов, повторную промывку водой и сушку.
Обезжиривают детали обычно бензином Б70 или щелочными водными растворами с последующей просушкой в струе сжатого воздуха. Для удаления легкого налета окислов детали обрабатывают в слабых растворах кислот или щелочей (для стали – 3 –5 %-ный раствор серной или соляной кислоты). Толстый слой ржавчины удаляют 10 –15 %-ным раствором фосфорной кислоты при температуре 40 – 50 0С. При травлении растворы кислот применяют с добавкой ингибиторов коррозии.
Индикаторные пенетранты
Индикаторный пенетрант (И) – это проникающая индикаторная жидкость, имеющая в своем составе вещества, (люминесцентные, цветные, люминесцентно-цветные и т. п.), химически активные по отношению к проявителю пенетранта и предназначенная для заполнения полостей открытых поверхностных дефектов и последующего образования индикаторного следа с необходимыми яркостно-цветовыми или другими свойствами, достаточными для его индикации и регистрации.
Индикаторные пенетранты подразделяют в зависимости от физического состоянияи колористических признаков на растворы и суспензии, как указано в табл. 3.
В зависимости от физических свойств пенетранты делятся на нейтральные, магнитные, электропроводящие, ионизирующие, поглощающие ионизирующее излучение, комбинированные.
В зависимости от технологических свойств пенетрантыподразделяются на удаляемые органическими растворителями, водосмываемые после воздействия очистителя или поверхностно-активных веществ, нейтрализуемые гашением люминесценции или цвета.
Индикаторный пенетрант представляет собой раствор или суспензию жирорастворимого темно-красного (Ж или 5С) красителя, широко применяемых при цветном методе контроля, или смесь люминофора с различными органическими растворителями, маслами, керосином, поверхностно-активными и другими веществами. Например, красная краска № 1 – бензол – 95 %, трансформаторное масло – 5 %, краситель (судан IV) -10 г/л; Одним из простых и распространенных пенетрантов, способных люминесцировать, является 65 % керосина, 25 % трансформаторного масла, 10 % бензина и люминоформ с красителем. Люминесцирующим веществом в пенетрантах, применяемых при люминесцентном и люминесцентно-цветном методах контроля, могут быть нориол А или Б, родамин С, желто-зеленый люминоформ 490 РТ (люмоген II) и др.
Таблица 3
Зависимость индикаторных пенетрантов от физического состояния
и колористических признаков на растворы и суспензии
Физическое состояние индикаторного пенетранта | Колористический признак индикаторного пенетранта | Колористическая характеристика индикаторного следа дефекта |
Проникающий раствор | Ахроматический | Черный, серый, бесцветный |
Цветной | Имеет характерный цветовой тон при наблюдении в видимом излучении | |
Люминесцентный | Испускает видимое излучение под воздействием длинноволнового ультрафиолетового излучения | |
Люминесцентно-цветной | Имеет характерный цветовой тон при наблюдении в видимом излучении и люминесцирует под воздействием длинноволнового ультрафиолетового излучения | |
Суспензии | Люминесцентный или цветной | Скопление люминесцентных или цветных частиц в устье дефекта |
Очиститель от пенетранта (М) – состав, предназначенный для удаления индикаторного пенетранта с контролируемой поверхности изделия самостоятельно или в сочетании с растворителем или водой.
В качестве очистителя пенетранта используют поверхностно-активные вещества типа ОП-10, моющие порошки, а также этиловый ректифицированный спирт и другие жидкости.
Гаситель пенетранта (Г) – состав, предназначенный для устранения фоновой окраски при цветном методе контроля или люминесценции при люминесцентном или люминесцентно-цветном методе контроля остатков индикаторного пенетранта на контролируемой поверхности.
В качестве гасителя для люминесцентных пенетрантов используется смесь резорцина с изопропиловым спиртом или ацетоном.
В зависимости от характера взаимодействия с индикаторным пенетрантом очистители и гасители подразделяют на растворяющие, самоэмульгирующие и эмульгирующие при внешнем воздействии.
Проявители пенетрантов
Проявитель пенетранта (П) – состав, предназначенный для извлечения индикаторного пенетранта из полости дефекта с целью образования индикаторного следа и создания фона, облегчающего обнаружение местоположения и визуальное восприятие изображения дефекта.
В зависимости от характера взаимодействия проявителя с индикаторным пенетрантом существуют химически пассивные, не меняющие колористические свойства индикаторного пенетранта; химически активные, (реактивные) меняющие цвет, способность люминесцировать или дающие продукты реакции, индицирующие дефекты.
Таблица 4
Характеристики физических состояний проявителей
Физическое состояние | Принцип действия | Характеристика |
Порошок |
Сорбционный | Сухой, преимущественно белый сорбент, поглощающий индикаторный пенетрант |
Суспензия | Преимущественно белый сорбент, поглощающий индикаторный пенетрант, диспергированный в летучих растворителях, воде или быстросохнущих смесях | |
Краска (лак) |
Диффузионный | Связывающий пигментированный или бесцветный быстросохнущий раствор, поглощающий индикаторный пенетрант |
Пленка | Бесцветная или белая накладная лента с проявляющим, например липким слоем, поглощающим индикаторный пенетрант, отделяемый с индикаторным следом от контролируемой поверхности |
Для проявления дефектов на контролируемой поверхности изделия используют растворенные в воде, спирте, ацетоне или других жидкостях, каолин, белую нитроэмаль, медицинский коллодий, оксид магния MgO, углекислый кальций CaCO3, углекислый магний MgCO3. В зависимости от физического состояния проявители существуют в виде порошка, суспензии, краски, пленки (табл. 4).
Проявители, создающие пленочное покрытие, состоят из 79 % коллодия на эфирно-спиртовой смеси, 20 % бензола, 10 % ацетона, густотертых цинковых белил – 50 г на 1 л смеси.
Дата добавления: 2018-06-01; просмотров: 1341; Мы поможем в написании вашей работы! |
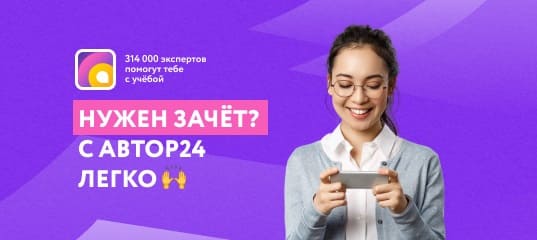
Мы поможем в написании ваших работ!