Рамные стенды напольного исполнения
Эти стенды удобны для среднего и мелкого ремонта кузовов. Стенд (рисунок 5.3) представляет собой раму, сваренную из стальных балок специального профиля, установленную заподлицо на бетонном основании и закрепленную на нем фундаментными болтами. Рама комплектуется четырьмя кронштейнами для установки автомобиля, несколькими силовыми гидроцилиндрами с индивидуальными ножными гидроприводами, тяговыми цепями и набором зажимных приспособлений. Конструкция стенда позволяет использовать подкатной тяговый выпрямитель с усилием 10 тонн по любому направлению рамы. Стапель возможно комплектовать большим количеством разнообразной оснастки, что повышает степень его универсальности. В нерабочем разобранном состоянии стапель практически не занимает
производственную площадь.
Рисунок 5.3 - Рамный стенд напольного исполнения для восстановления геометрии кузовов легковых автомобилей фирмы CELETTE (Франция).
Анкерные стапели
Этот вид оборудования представляет собой набор фиксирующих и подкатных тяговых устройств, закрепляемых временно на бетонном основании с помощью системы анкеров. Фиксирующие устройства — это две направляющие, на которых легко монтируются регулируемые по высоте опоры с зажимными приспособлениями для крепления автомобиля (рисунок 5.4).
Подкатной тяговый выпрямитель с усилием 10 тонн может устанавливаться в нескольких фиксированных местах по периметру кузова и через цепь осуществлять его правку в нужном направлении. Один конец которой крепится к кольцу установленного в бетонное основание анкера, а другой — к элементу кузова.
|
|
Рисунок 5.4 - Анкерный стапель CHAINLESS для проведения краткосрочного кузовного ремонта фирмы WEDGECLAMPSYSTEM (Канада)
Шаблонные стенды
Для восстановления геометрических размеров кузова автомобиля, задаваемых производителем, предполагается жесткая установка кузова на стапеле. В настоящее время широко распространены две системы правки кузовов — классическая и шаблонная, в основу которых заложены разные принципы крепления кузова к стапелю и процесса правки.
Классическая система предусматривает крепление кузова за пороги автомобиля. Прикладывая определенные усилия к различным точкам, методом последовательного приближения, периодически проводя замеры, добиваются требуемого положения контрольных точек.
Достоинствами данного метода являются достаточно простое и быстрое крепление автомобиля на стапеле, а также сравнительно низкая цена такого стапеля. Недостатки проявляются в процессе работы. При приложении усилия к одной точке кузова возможно смещение других, ранее выставленных точек. По этой причине необходимо постоянно контролировать изменение размеров. В результате сложно добиться приведения размеров кузова к исходным, заданным в конструкторской документации на автомобиль.
|
|
Шаблонная система основывается на креплении кузова автомобиля за его технологические отверстия к конструкции стапеля. На каждый тип автомобиля имеются карты расположения технологических отверстий кузова. Для осуществления крепления используются специальные адаптеры-переходники(джиги), которые обеспечивают точную и надежную фиксацию кузова к стапелю.
При правке кузов закрепляют к раме стапеля за точки, которые сохранили свое правильное расположение. Далее прикладывается усилие к точке, положение которой смещено. При достижении точкой заданного положения ее крепят при помощи зажимов-джиг к раме стапеля, после чего приступают к вытяжке другой точки. При такой технологии «исправленная» точка находится неподвижно на закрепленном месте. Данная система фиксации имеет две разновидности.
В первом случае джиги крепятся на раму стапеля через специальные колонны и балки. Для каждого типа кузова требуется свой комплект джиг, колонн и балок, поэтому для универсального участка кузовного ремонта стоимость всех необходимых комплектов очень высока, а при появлении новых автомобилей их потребуется еще больше.
|
|
Во втором случае (система предложена и запатентована итальянской фирмой ВВМ) джиги крепятся на универсальные колонны, высота которых задается и фиксируется по необходимым размерам. Положение колонн на раме стапеля тоже задается и фиксируется при помощи универсального комплекта балок. И колонны, и балки, и сама рама имеют удобные встроенные линейки. В результате можно создать шаблон для любого кузова, требующего ремонта. Стоимость такой системы значительно ниже и обладает еще одним преимуществом — устройство крепления джиг является одновременно и системой измерения. В любой момент наглядно видна вся геометрия нижней части кузова с точностью до 1 мм. После правки нижней части кузова производится ремонт верхней части. Недостаток такого метода — более длительная установка кузова на стапель, что компенсируется точностью геометрии восстановленного кузова и отсутствием необходимости постоянных измерений в процессе ремонта из-за «ухода» размеров.
Стапели на подъемниках
Эти стапели являются стендами рамного типа, конструктивно выполненными заодно с подъемниками (рисунок 5.5). В большинстве случаев для этой цели используются заглубленные подъемники ножничного типа, что дает достаточно легкую возможность установки кузова автомобиля на стенд, реже применяются четырехстоечные подъемники. По функциональным возможностям и комплектации средствами правки кузова и измерения его геометрии такие стенды не отличаются от других стендов рамного типа. Однако условия труда механиков на таких стапелях гораздо лучше за счет возможности менять высоту установки кузова относительно пола помещения, что дает дополнительные удобства для осмотра поврежденных элементов кузова, наблюдения за процессом правки и управления всеми операциями устранения деформации.
|
|
Рисунок 5.5 - Кузовные стапели рамного типа, выполненные на ножничном подъемнике: a — GRIFFON — стенд фирмы SELETTE (Франция) с рычажным тяговым устройством и возможностью использования механической измерительной системы MZ; б — PONYBENCH — стенд фирмы SPANESI (Испания) с тяговым устройством типа «силовая колонна»; в — PISTA — стенд фирмы SPANESI (Испания) с двумя тяговыми устройствами типа «силовая колонна» и одним — типа качающийся рычаг, с механической измеритель-ной системой верхней части кузова
Сварочное оборудование
На ПТС при ремонте автомобилей используются следующие виды сварочного оборудования: для дуговой сварки покрытыми электродами; для дуговой сварки в среде защитных газов; для сварки флюсовой проволокой без защитного газа; для контактной сварки.
Аппараты для дуговой сварки штучными электродами реализуют метод сварки ММА (ManualMetalArc, т. е. ручная сварка металлическим электродом). Они включают в себя источник сварочного тока; сварочные провода и электрододержатель. Источником сварочного тока может быть генератор(преобразователь), трансформатор или выпрямитель. Сварочный преобразователь представляет собой агрегат, состоящий из электродвигателя и генератора постоянного тока.
При дуговой сварке покрытыми флюсом электродами выделяется большое количество тепла, которое, вызывая местный нагрев свариваемых металлов, может вызвать появление внутренних напряжений и коробление. В этой связи оборудование этого вида находит ограниченное применение при ремонте автомобилей, особенно в кузовном ремонте.
Аппараты для дуговой сварки в среде защитных газов подразделяются на две основные группы:
— для сварки неплавящимся электродом — методом TIG;
— для сварки плавящимся электродом — методом MIG / MAG.
Аппараты для сварки неплавящимся электродом реализуют метод сварки TIG (Tungsten + InertGas, т. е. вольфрам + инертный газ), суть которого заключается в следующем. Электрическая дуга возникает между неплавящимся вольфрамовым электродом и свариваемым металлом. Из концентричного сопла электрода в зону сварки из баллона подается инертный газ, обычно аргон или гелий. В среде защитного газа сварочный шов охлаждается и твердеет. Сварка может осуществляться без присадочного материала, если свариваемые металлы тонкие, или с присадочным материалом в виде проволоки, которая плавится одновременно со свариваемыми металлами.
Сварочные аппараты типа TIG могут иметь источник для получения переменного или постоянного сварочного тока. Оборудование первой группы, в свою очередь, делится на две подгруппы — аппараты для сварки током промышленной частоты (50 Гц) и аппараты с инвертором, преобразующим частоту тока с 50 до 5000 Гц, что обеспечивает лучшее качество сварного шва, делает аппарат легче и уменьшает потребляемую мощность в 5—6 раз.
Сварочные аппараты типа TIG выпускаются как оборудование полуавтоматического или ручного действия. Они компонуются на передвижной тележке, на которой установлены баллон с инертным газом и источник сварочного тока, выполненный в отдельном корпусе (собственно сварочный аппарат). Аппарат и баллон с газом соединены со сварочным пистолетом, соответственно, кабелем и шлангом.
Аппараты для сварки плавящимся электродом относятся к оборудованию как неавтоматизированному, так и полуавтоматического действия. Процесс сварки плавящимся электродом в среде защитного газа происходит за счет электрической дуги, возникающей между проволокой-электродом и свариваемыми металлами. Проволока одновременно является и электродом, и присадочным материалом.
В зависимости от вида защитного газа реализуются три метода сварки:
— MIG (Metal + InertGas), он требует применения аргона или гелия;
— MAG (Metal +AktivGas), здесь используется углекислый газ;
— MIG / MAG с использованием смеси газов — аргона и двуокиси углерода, например, для сварки стальных листов требуется 80% аргона и 20% углекислого газа.
Сварочные полуавтоматы типа MIG, MAG и MIG / MAG выпускаются в отдельном корпусе, внутри которого размещены: привод подачи проволоки, источник сварочного тока и блок управления. Проволока с бобины сматывается принудительно вращающимися роликами. Вращение роликов осуществляет мотор-редуктор с автоматически регулируемой скоростью в зависимости от вида свариваемых металлов, толщины проволоки и вида защитного газа.
Аппараты для дуговой сварки флюсовой проволокой без защитного газа относятся к аппаратам полуавтоматического действия и реализует метод сварки плавящимся непрерывным электродом. В качестве плавящегося электрода выступает специальная проволока в виде тонкой трубочки, набитой сварочным флюсом. В зоне сварки флюс выполняет защитную функцию для сварного шва. По конструкции эти аппараты аналогичны сварочным полуавтоматам типа MIG / MAG, за исключением того, что они не подсоединяются к баллону с защитным газом.
Комбинированные аппараты для дуговой сварки. Ряд производителей сварочного оборудования для автосервиса выпускают сварочные аппараты, которые могут реализовывать различные методы дуговой сварки в разных комбинациях, благодаря чему расширяется область их применения и повышается степень универсальности, что немаловажно для их использования на малых предприятиях автосервиса.
Аппараты для двусторонней точечной сварки состоят из двусторонних сварочных клещей, которые включают сварочный трансформатор, клещевого механизма с приводом от рукоятки и пружинным, пневматическим или гидравлическим исполнительным механизмом и электродов, закрепленных в клещевом механизме.
Аппараты для односторонней точечной сварки состоят из блока питания, включающего источник сварочного тока и аппаратуру управления, сварочного пистолета и провода с зажимом. Эти аппараты успешно применяют для приварки гвоздиков, необходимых при правке тонких панелей. Величина сварочного тока и время импульса сварки таковы, что не приводят к дополнительной деформации панели и не вызывают повреждение лакокрасочного покрытия или пластмассовых накладок с другой стороны листа панели.
Дата добавления: 2018-06-27; просмотров: 4679; Мы поможем в написании вашей работы! |
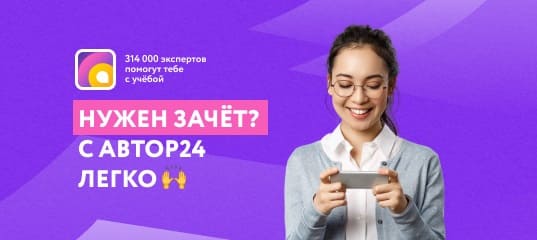
Мы поможем в написании ваших работ!