ПРОВЕРКА ПРОЧНОСТИ ШПОНОЧНЫХ И ШЛИЦЕВЫХ СОЕДИНЕНИЙ
7.1 ПРОВЕРКА ПРОЧНОСТИ ШПОНОЧНЫХ СОЕДИНЕНИЙ
ИСХОДНЫЕ ДАННЫЕ
Тип шпонки, материал шпонки
,
Рабочая длина шпонки
Основные параметры шпонки ,
,
(таблица 7.1)
1 Напряжение смятия и условие прочности
Допускаемые напряжения смятия при стальной ступице [ ]=100÷120МПа
Рисунок 7.1 – Соединение “вал-ступица” призматической шпонкой
Таблица 7.1 – Размеры призматических шпонок и сечений пазов, мм
Вал | Шпонка | Шпоночный паз | |||||
| | | | Ширина | Глубина | ||
Св. | до | ![]() | Вал
![]() | Втулка
![]() | |||
6 | 8 | 2 | 2 3 4 5 6 | 3...20 | 2 | 1,2 1,8 2,5 +0,1 3,0 0 3,5 | 1,0 1,4 1,8 +0,1 2,3 0 2,8 |
8 | 10 | 3 | 6...36 | 3 | |||
10 | 12 | 4 | 8...45 | 4 | |||
12 | 17 | 5 | 10...56 | 5 | |||
17 | 22 | 6 | 14...70 | 6 | |||
22 | 30 | 8 | 7 8 8 9 10 11 12 14 14 16 18 | 18...90 | 8 | 4,0 5,0 5,0 5,5 6,0 7,0 +0,2 7,5 0 9,0 9,0 10 11 | 3,3 3,3 3,3 3,8 4,3 4,4 +0,2 4,9 0 5,4 5,4 6,4 7,4 |
30 | 38 | 10 | 22...110 | 10 | |||
38 | 44 | 12 | 28...140 | 12 | |||
44 | 50 | 14 | 36...160 | 14 | |||
50 | 58 | 16 | 45...180 | 16 | |||
58 | 65 | 18 | 50...200 | 18 | |||
65 | 75 | 20 | 56...220 | 20 | |||
75 | 85 | 22 | 63...250 | 22 | |||
85 | 95 | 25 | 70...280 | 25 | |||
95 | 110 | 28 | 80...320 | 28 | |||
110 | 130 | 32 | 90...360 | 32 |
7.2 ПРОВЕРКА ПРОЧНОСТИ ШЛИЦЕВЫХ СОЕДИНЕНИЙ
ИСХОДНЫЕ ДАННЫЕ
Тип шпонки, материал шпонки
,
Рабочая длина шлиц
Основные параметры шпонки ,
(таблица 7.2)
1 Напряжение смятия и условие прочности
Допускаемые напряжения смятия при стальной ступице [ ]=100÷120МПа
а) вала; б) втулки
|
|
Рисунок 7.2 – Сечения шлицевого прямоточного соединения
Таблица 7.2 – Основные размеры, мм и число зубьев шлицевых прямобочных соединений
Легкая серия | ||||||||
![]() | Число зубьев ![]() | ![]() | ![]() | ![]() | ![]() | ![]() | ![]() | ![]() |
![]() | 6 | 23 | 26 | 6 | 22,1 | 3,54 | 0,3 | 0,2 |
![]() | 26 | 30 | 6 | 24,6 | 3,85 | 0,3 | 0,2 | |
![]() | 28 | 32 | 7 | 26,7 | 4,03 | 0,3 | 0,2 | |
![]() | 8 | 32 | 36 | 6 | 30,4 | 2,71 | 0,4 | 0,3 |
![]() | 36 | 40 | 7 | 34,5 | 3,46 | 0,4 | 0,3 | |
![]() | 42 | 46 | 8 | 40,4 | 5,03 | 0,4 | 0,3 | |
![]() | 46 | 50 | 9 | 44,6 | 5,75 | 0,4 | 0,3 |
Окончание таблицы 7.2
![]() | 8 | 52 | 58 | 10 | 49,7 | 4,89 | 0,5 | 0,5 | ||
![]() | 56 | 62 | 10 | 53,6 | 6,38 | 0,5 | 0,5 | |||
![]() | 62 | 68 | 12 | 59,8 | 7,31 | 0,5 | 0,5 | |||
![]() | 10 | 72 | 78 | 12 | 69,6 | 5,45 | 0,5 | 0,5 | ||
![]() | 82 | 88 | 12 | 79,3 | 8,62 | 0,5 | 0,5 | |||
![]() | 92 | 98 | 14 | 89,4 | 10,08 | 0,5 | 0,5 | |||
![]() | 102 | 108 | 16 | 99,9 | 11,49 | 0,5 | 0,5 | |||
![]() | 112 | 120 | 18 | 108,8 | 10,72 | 0,5 | 0,5 | |||
Средняя серия | ||||||||||
![]() | 6 | 11 | 14 | 3,0 | 9,9 | - | 0,3 | 0,2 | ||
![]() | 13 | 16 | 3,5 | 12,0 | - | 0,3 | 0,2 | |||
![]() | 16 | 20 | 4,0 | 14,5 | - | 0,3 | 0,2 | |||
![]() | 18 | 22 | 5,0 | 16,7 | - | 0,3 | 0,2 | |||
![]() | 21 | 25 | 5,0 | 19,5 | 1,95 | 0,3 | 0,2 | |||
![]() | 23 | 28 | 6,0 | 21,3 | 1,34 | 0,3 | 0,2 | |||
![]() | 26 | 32 | 6,0 | 23,4 | 1,65 | 0,4 | 0,3 | |||
![]() | 28 | 34 | 7,0 | 25,9 | 1,70 | 0,4 | 0,3 | |||
![]() | 8 | 32 | 38 | 6,0 | 29,4 | - | 0,4 | 0,3 | ||
![]() | 36 | 42 | 7,0 | 33,5 | 1,02 | 0,4 | 0,3 | |||
![]() | 42 | 48 | 8,0 | 39,5 | 1,57 | 0,4 | 0,3 | |||
![]() | 46 | 54 | 9,0 | 42,7 | - | 0,5 | 0,5 | |||
![]() | 52 | 60 | 10 | 48,7 | 2,44 | 0,5 | 0,5 | |||
![]() | 56 | 65 | 10 | 52,2 | 2,50 | 0,5 | 0,5 | |||
![]() | 62 | 72 | 12 | 57,8 | 2,40 | 0,5 | 0,5 | |||
![]() | 10
| 72 | 82 | 12 | 67,4 | - | 0,5 | 0,5 | ||
![]() | 82 | 92 | 12 | 77,1 | 3,00 | 0,5 | 0,5 | |||
![]() | 92 | 102 | 14 | 87,3 | 4,50 | 0,5 | 0,5 | |||
![]() | 102 | 112 | 16 | 97,7 | 6,30 | 0,5 | 0,5 | |||
![]() | 112 | 125 | 18 | 106,3 | 4,40 | 0,5 | 0,5 | |||
Тяжелая серия | ||||||||||
![]() | 10 | 16 | 20 | 2,5 | 14,1 | - | 0,3 | 0,2 | ||
![]() | 18 | 23 | 3,0 | 15,6 | 0,32 | 0,3 | 0,2 | |||
![]() | 21 | 26 | 3,0 | 18,5 | 0,36 | 0,3 | 0,2 | |||
![]() | 23 | 29 | 4,0 | 20,3 | 0,45 | 0,3 | 0,2 | |||
![]() | 26 | 32 | 4,0 | 23,0 | 0,95 | 0,4 | 0,3 | |||
![]() | 28 | 35 | 4,0 | 24,4 | 1,34 | 0,4 | 0,3 | |||
![]() | 32 | 40 | 5,0 | 28,0 | 1,65 | 0,4 | 0,3 | |||
![]() | 36 | 45 | 5,0 | 31,3 | 1,70 | 0,4 | 0,3 | |||
![]() | 42 | 52 | 6,0 | 36,9 | 2,15 | 0,4 | 0,3 | |||
![]() | 46 | 56 | 7,0 | 40,9 | 3,02 | 0,5 | 0,5 | |||
![]() | 16 | 52 | 60 | 5,0 | 47,0 | 2,57 | 0,5 | 0,5 | ||
![]() | 56 | 65 | 5,0 | 50,6 | 2,86 | 0,5 | 0,5 | |||
![]() | 62 | 72 | 6,0 | 56,1 | 2,44 | 0,5 | 0,5 | |||
![]() | 72 | 82 | 7,0 | 65,9 | 2,50 | 0,5 | 0,5 | |||
![]() | 20 | 82 | 92 | 6,0 | 75,6 | 2,40 | 0,5 | 0,5 | ||
![]() | 92 | 102 | 7,0 | 85,5 | - | 0,5 | 0,5 | |||
![]() | 102 | 115 | 8,0 | 94,0 | 3,30 | 0,5 | 0,5 | |||
![]() | 112 | 125 | 9,0 | 104 | 4,40 | 0,5 | 0,5 |
ПОДБОР И ПРОВЕРОЧНЫЙ РАСЧЕТ МУФТ
Назначение муфт - это соединение валов или др. деталей машин и механизмов для передачи движения чаще всего вращательного.
Стандартные муфты выбирается по расчетному моменту.
8.1 ВЫБОР И ПРОВЕРОЧНЫЙ РАСЧЕТ УПРУГОЙ ВТУЛОЧНО-ПАЛЬЦЕВОЙ МУФТЫ
|
|
По расчетному моменту выбираем по таблице 8.1 стандартную муфту.
Таблица 8.1 Параметры и размеры, мм, упругих втулочно-пальцевых муфт.
| | | | | | | | | | | ||
Исполнения | ||||||||||||
1 | 2 | 1 | 2 | |||||||||
0,063 | 20...24 | 100 | 104 | 76 | 38 | 24 | 28 | 16 | 16 | 40 | 14 | 63 |
0,125 | 25, 28 30 | 120 | 125 165 | 89 121 | 44 60 | 26 38 | 32 | 18 | 18 | 55 | 14 | 86 |
0,25 | 32...38 40...45 | 140 | 165 225 | 121 169 | 60 85 | 38 56 | 40 | 20 | 20 | 75 | 16 | 100 |
0,5 | 40...45 | 170 | 225 | 169 | 85 | 56 | 50 | 24 | 26 | 80 | 18 | 120 |
0,71 | 45...56 | 190 | 226 | 170 | 85 | 56 | 55 | 24 | 26 | 100 | 20 | 135 |
1,0 | 50...56 60...70 | 220 | 226 286 | 170 216 | 85 107 | 56 72 | 60 | 30 | 32 | 120 | 25 | 160 |
2,0 | 63...75 80...90 | 250 | 288 348 | 218 268 | 107 135 | 72 95 | 70 | 34 | 42 | 150 | 28 | 180 |
4,0 | 80...95 | 320 | 350 | 270 | 135 | 95 | 80 | 40 | 50 | 160 | 35 | 230 |
8,0 | 100...125 | 400 | 432 | 342 | 170 | 125 | 110 | 57 | 72 | 200 | 45 | 280 |
16,0 | 120, 125, 130...150 160 | 500 | 435 515 615 | 345 415 495 | 170 205 245 | 125 155 185 | 140 | 72 | 86 | 240 | 55 | 360 |
1,2 – полумуфты, 3 – палец (рисунок 8.2), 4 – втулка упругая, 5 – шайба для пальцев,
6 – шайба стопорная с носком, 7 – гайка, 8 – кольцо пружинное
Рисунок 8.1 – Муфта упругая втулочно-пальцевая
Рисунок 8.2 – Варианты выполнения пальца
Проверка осуществляется для пальца на прочность по изгибу в опасном сечении, затем проверяется прочность резиновой втулки на смятие пальцем.
|
|
Палец рассматривается как балка, защемленная одним концом (должно соблюдаться условие прочности пальца )
Допускаемое напряжение пальца на изгиб
Проверяем прочность резиновой втулки на смятие пальцем
Для резины .
8.2 ВЫБОР И ПРОВЕРОЧНЫЙ РАСЧЕТ ЗУБЧАТОЙ МУФТЫ
По расчетному моменту выбираем по таблице 8.2 стандартную муфту.
Таблица 8.2 – Параметры и основные размеры, мм, зубчатых муфт
| мин-1 max | | | | | | | | | Зацепление | |||
![]() | ![]() | ![]() | ![]() | ||||||||||
1,0 | 2500 | 40 | 145 | 105 | 60 | 174 | 82 | 12 | 50 | 2,5 | 30 | 12 | 60 |
1,6 | 2100 | 55 | 175 | 125 | 80 | 174 | 82 | 12 | 50 | 2,5 | 38 | 13 | 75 |
2,5 | 1900 | 60 | 185 | 135 | 85 | 220 | 105 | 12 | 50 | 3,0 | 36 | 15 | 75 |
4,0 | 1600 | 65 | 200 | 150 | 95 | 220 | 105 | 18 | 50 | 3,0 | 40 | 18 | 85 |
6,3 | 1300 | 80 | 230 | 175 | 115 | 270 | 130 | 18 | 60 | 3,0 | 48 | 20 | 125 |
10 | 1100 | 100 | 270 | 200 | 145 | 340 | 165 | 18 | 60 | 3,0 | 56 | 24 | 145 |
16 | 1000 | 120 | 300 | 230 | 175 | 345 | 165 | 25 | 70 | 4,0 | 48 | 30 | 180 |
25 | 800 | 140 | 330 | 260 | 200 | 415 | 200 | 30 | 70 | 4,0 | 56 | 32 | 180 |
40 | 700 | 160 | 410 | 330 | 230 | 415 | 200 | 30 | 90 | 6,0 | 46 | 35 | 210 |
63 | 600 | 200 | 470 | 390 | 290 | 500 | 240 | 35 | 90 | 6,0 | 56 | 40 | 250 |
1 – втулка, 2 – обойма
Рисунок 8.3 – Муфта зубчатая
Проверка осуществляется для рабочих поверхностей зубьев по напряжениям сжатия.
где модуль зацепления;
длина зуба;
z- число зубьев;
диаметр окружности расположения пальцев;
Для стандартных зубчатых муфт допускаемое напряжение ,
8.3 РАСЧЕТ ПРЕДОХРАНИТЕЛЬНО МНОГОДИСКОВОЙ ФРИКЦИОННОЙ МУФТЫ
Рисунок 8.4 – Предохранительная фрикционная муфта
По результатам предварительных расчетов цилиндрической зубчатой пары определяем габариты, в которые должна вписаться муфта.
Назначаем высоту шлиц , мм, и зазор между шлицами и наружным диаметром внутренних дисков принять
, мм, рабочий наружный диаметр шлиц
.
Муфта должна передавать номинальный момент . Коэффициент перегрузки
, поэтому предельный момент определим по формуле
1) Выбираем в качестве материалов дисков закаленную сталь по текстолиту, которые будут работать со смазкой. Назначаем коэффициент трения .
2) Выше был установлен наружный диаметр , мм, внутренний диаметр
.
3) Приведенный радиус сил трения
4) Допускаемое осевое усилие
5) Число пар трения
округляем до ближайшего целого числа.
,
Необходимая сила нажатия при полученном
Необходимая сила нажатия при трущихся поверхностях
Назначаем толщину дисков.
РАСЧЕТ ПАКЕТА ЦИЛИНДРИЧЕСКИХ ПРУЖИН
По конструктивным соображениям принимаем наружный диаметр пружины.
Длина окружности опорной поверхности пружин по среднему диаметру сил трения
Набольший диаметр стакана по чертежу назначаем конструктивно .
Таким образом, можно на муфте по диаметру равнодействующих сил трения поместить не более
округляем до ближайшего целого числа. Тогда усилие
, которое должно развиваться одной пружиной,
По ГОСТ 13771-68 назначаем пружину, у которой диаметр проволоки , наружный диаметр пружины
, жесткость
одного витка
, наибольший прогиб одного витка
, сила
при максимальной деформации
, деформация рабочая
. Принимая пружины 1-го или 2-го классов, определяем максимальное значение силы сжатия пружины
где - относительный инерционный зазор пружин 1-го и 2-го классов.
Принимаем силу предварительного сжатия пружины
Тогда жесткость пружины
Число рабочих витков пружины
.
- целое число.
Уточненная жесткость
Назначаем 2 нерабочих витка, тогда полное число витков
Средний диаметр пружины
Рабочая деформация под действием силы
Полная деформация (при посадке на виток).
Высота пружины при посадке витка на виток
Высота пружины в ненагруженном состоянии
Высота пружины в рабочем положении
Шаг пружины
ВТОРАЯ ЭСКИЗНАЯ КОМПОНОВКА
Второй этап компоновки имеет целью конструктивно оформить зубчатые колеса, валы, подшипниковые узлы и подготовить данные для проверки прочности валов и некоторых других деталей.
Конструируем узлы ведущего, промежуточного и ведомого валов.
На ведущем и ведомом валах применяем шпонки призматические со скругленными торцами по ГОСТ 23360-78.
Непосредственным измерением уточняем расстояния между опорами и расстояния, определяющие положение зубчатых колес, шкивов, муфт, звездочек относительно опор. При значительном изменении этих расстояний уточняем реакции опор и вновь проверяем долговечность подшипников.
9.1 КОНСТРУИРОВАНИЕ ЦИЛИНДРИЧЕСКИХ КОЛЕС
ЗАДАННЫЕ ПАРАМЕТРЫ
- диаметр вершин зубьев;
- ширина венца;
- модуль;
материал зубчатого колеса;
- диаметр вала.
ОПРЕДЕЛЯЕТСЯ:
Толщина венца .
Диаметр ступицы .
Длина ступицы .
Фаски венца на диаметре вершин .
Диаметр расположения отверстий .
Диаметр отверстий .
ВАЛЫ ШЕСТЕРНИ
Рисунок 9.1 – Валы шестерни
КОЛЕСА КОВАННЫЕ
- таблица 9.1;
;
;
;
мм.
мм
мм
Рисунок 9.2 – Кованные зубчатые колеса
Таблица 9.1 – Значения
![]() | 1,5 | 2,0 | 2,5 | 3,0 | 4,0 | 5,0 | 6,0 |
![]() | ![]() | ![]() | ![]() | ![]() | ![]() | ![]() | ![]() |
КОЛЕСА ШТАМПОВАННЫЕ
;
;
.
мм
Рисунок 9.2 – Штампованное зубчатое колесо
КОЛЕСА СВАРНЫЕ
;
;
;
мм;
.
Рисунок 9.3 – Сварное зубчатое колесо
КОЛЕСА ЛИТЫЕ
а) ; б)
; в)
;
;
;
;
;
;
;
;
;
;
.
мм
мм
мм
Рисунок 9.4 – Литые зубчатые колеса
9.2 КОНСТРУИРОВАНИЕ КОНИЧЕСКИХ КОЛЕС
ЗАДАННЫЕ ПАРАМЕТРЫ
- наружный делительный диаметр;
- наружный диаметр вершин зубьев;
- ширина венца;
- наружный (нормальный) модуль;
- угол делительного конуса;
- образующая конуса на наружном диаметре;
материал зубчатого колеса;
- диаметр вала.
- диаметр ступицы;
- длина ступицы.
ОПРЕДЕЛЯЕТСЯ:
Для кованных и штампованных колес:
.
;
Для литых колес
- при диаметре
.
;
- ст. литье;
- чугун;
- при диаметре
.
;
- ст. литье;
- чугун;
Рисунок 9.5 – Вал-шестерня
Рисунок 9.6 – Шестерня
Кованные Штампованные Литые
,
- выбираются конструктивно.
Рисунок 9.7 – Зубчатые колеса
9.3 КОНСТРУИРОВАНИЕ ЧЕРВЯКОВ И ЧЕРВЯЧНЫХ КОЛЕС
ЗАДАННЫЕ ПАРАМЕТРЫ
- межосевое расстояние;
- диаметр вершин зубьев червяка;
- диаметр вершин зубьев червячного колеса;
- длина нарезной части червяка;
- ширина червячного колеса;
- модуль;
- диаметр вала.
ОПРЕДЕЛЯЕТСЯ:
;
;
- ст. литье;
- чугун;
;
;
.
;
,
- округляются до целых чисел;
;
.
Таблица 9.2 – Зависимость , мм
![]() | 1,5 | 2,0 | 2,5 | 3,0 | 4,0 | 5,0 | ![]() |
![]() | ![]() | ![]() | ![]() | ![]() | ![]() | ![]() | ![]() |
Рисунок 9.8 – Конструкции червяков
Рисунок 9.9 – Конструкции червячных колес
УТОЧНЕННЫЙ РАСЧЕТ ВАЛОВ
ИСХОДНЫЕ ДАННЫЕ
1 Конструкция вала.
2 Материал и термообработка вала ( ,
,
).
3 Значения изгибающих и крутящих
моментов в сечении вала.
4 Реверсивность передачи.
Уточненный расчет валов заключается в проверке валов на усталостную прочность, т.е. в определении запасов прочности в опасных сечениях.
1 Анализируя линию сечения вала, где приведенные напряжения равны допускаемым, а также принятые размеры вала (рисунок 10.1), можно сделать вывод, что потенциально слабыми сечениями вала являются сечения, обозначенные цифрами 1, 2, 3.
Выбранные сечения имеют параметры:
сечение 1 ,
,
;
сечение 2 ,
,
;
сечение 3 ,
,
.
Рисунок 10.1 – Параметры вала для проверки на усталостную прочность
2. Для каждого выбранного сечения вала, следуя из его конструкции (рисунок 10.1), выбирается тип концентратора напряжений и по таблице 10.1 для этого типа концентратора выбираются значения коэффициентов концентрации напряжений по изгибу ( ) и по кручению (
):
сечение 1 - ,
; сечение 2 -
,
; сечение 3 -
,
.
3. Коэффициент запаса прочности вала по нормальным напряжениям
,
где - предел выносливости гладких стандартных цилиндрических образцов при симметричном цикле нагружения, МПа (таблица 5.1);
- амплитуда цикла изменения напряжений изгиба, МПа,
;
где - изгибающий момент в рассмотренном сечении вала, Н·м;
- момент сопротивления изгибу с учетом ослабления вала, мм3 (таблица 10.1);
- коэффициент снижения предела выносливости детали в рассматриваемом сечении при изгибе
,
где - коэффициент влияния абсолютных размеров поперечного сечения (рисунок 10.1),
;
- коэффициент влияния параметров шероховатости поверхности (рисунок 10.2);
- коэффициент влияния поверхности упрочнения (таблица 10.2).
4 Коэффициент запаса по касательным напряжениям:
для реверсивной передачи
для нереверсивной передачи
,
где предел выносливости гладких стандартных цилиндрических образцов при симметричном цикле кручения, МПа (таблица 5.1);
- амплитуда цикла напряжений кручения;
- постоянная составляющая напряжений кручения.
При реверсивной передаче
, МПа;
.
При нереверсивной передаче
, МПа,
где - крутящий момент на валу, Н·м;
- момент сопротивления кручению с учетом ослабления вала, мм3 (таблица 10.1)
- коэффициент снижения предела выносливости детали в рассматриваемом сечении при кручении
,
где - коэффициент влияния абсолютных размеров поперечного сечения (рисунок 10.2),
;
- коэффициент влияния параметров шероховатости поверхности (рисунок 10.3);
- коэффициент влияния поверхности упрочнения (таблица 10.2).
- коэффициент, характеризующий чувствительность вала к асимметрии цикла изменения напряжений (таблица 10.3).
5 Общий запас сопротивления усталости
;
При невыполнении условия следует:
изменить конструкцию вала так, чтобы увеличился меньший из коэффициентов или
;
выбрать материал вала с более высокими механическими характеристиками;
увеличить диаметр вала.
1 – углеродистая сталь без концентрации напряжений; 2 – легированная сталь без концентрации напряжений и углеродистая сталь при концентрации напряжений ; 3 - легированная сталь с концентрацией напряжений
Рисунок 10.2 – График для определения
1 – шлифование тонкое ( - 0,32; 0,16); 2 – обточка чистовая (
- 2,5; 1,25; 0,63);
3 – обдирка ( - 20; 40; 80); 4 – необработанные поверхности с окалиной
Рисунок 10.3 – График для определения
Таблица 10.1 – Значения ,
,
,
| | | Эскиз | Момент сопротивления, мм3 | |||
| | | |||||
![]() | ![]() | ![]() | ![]() | ||||
Галтель ![]() ![]() | 2,50 1,85 1,60 | 3,50 2,00 1,64 | 1,80 1,40 1,25 | 2,10 1,53 1,35 | ![]() | ![]() | ![]() |
Поперечное отверстие
при ![]() | 1,90 | 2,00 | 1,75 | 2,00 | ![]() | ![]() | ![]() |
Выточка ![]() ![]() | 1,90 1,80 1,70 | 2,35 2,00 1,85 | 1,40 1,35 1,25 | 1,70 1,65 1,50 | ![]() | ![]() | ![]() |
Шпоночный паз | 1,75 | 2,00 | 1,50 | 1,90 | ![]() | ![]() | ![]() |
Шлицы прямобочные | 1,60 | 1,75 | 2,45 | 2,80 | | ![]() | ![]() |
Для шлице легкой серии средней | |||||||
Витки червяка | 2,30 | 2,50 | 1,70 | 1,90 |
| ![]() | ![]() |
| |||||||
Резьба | 1,80 | 2,40 | 1,20 | 1,50 |
| ![]() | ![]() |
|
Таблица 10.2 – Значение
Вид упрочнения поверхности вала |
сердцевины | При концентрации напряжений | |
![]() | ![]() | ||
Закалка ТВЧ | 600...800 | 1,6...1,7 | 2,4...2,6 |
Накатка роликом | 1,3...1,5 | 1,6...2,0 | |
Дробеструйный наклеп | 600...150 | 1,5...1,6 | 1,7...2,1 |
Таблица 10.3 – Значения
Углеродистые стали: - с малым содержанием углерода - со средним содержанием углерода |
![]() ![]() |
Легированные стали | ![]() |
ДОПУСКИ И ПОСАДКИ
ВАЛ
1 Поля допусков и посадки
1.1 Подшипников качения (таблица 11.1).
1.2 Зубчатых колес
1.2.1 Для обычных соединений: (
),
,
(
).
1.2.2 Для соединений при ударных нагрузках: (
),
(
).
1.2.3 Для соединений при ударных нагрузках: ,
,
.
1.3 Муфт
1.3.1 Для обычных соединений: ,
,
.
1.3.2 Для соединений при ударных нагрузках: ,
.
1.4 Распорных втулок ,
.
1.5 Отклонений вала в месте установки уплотнений -
1.6 Рекомендуемые посадки установки валов (рисунок 11.1).
Рисунок 11.1 – Посадки, связанные с установкой валов
Таблица 11.1 – Рекомендуемые посадки подшипников 0 и 6 классов точности
Посадки для основных отклонений | |||||||||||||||||
вала | отверстия корпуса | ||||||||||||||||
![]() | ![]() | ![]() ![]() | ![]() | ![]() | ![]() | ![]() | ![]() | ![]() | ![]() ![]() | ![]() ![]() | ![]() ![]() | ![]() | ![]() | ![]() | ![]() | ![]() | ![]() |
![]() ![]() | ![]() | ![]() ![]() | ![]() | ![]() | ![]() | ![]() | ![]() | ![]() | ![]() ![]() | ![]() ![]() | ![]() ![]() | ![]() | ![]() | ![]() | ![]() | ![]() | ![]() |
2 Допуски формы и расположения поверхностей (рисунок 11.2).
2.1 Допуск радиального биения :
- поверхностей установки подшипников качения (когда допуск относится к оси вала) – 0,5 допуска круглости;
- поверхностей установки ступиц различного типа колес, муфт и д.т. (таблица11.2);
- поверхностей установки уплотнений – 0,05 мм.
2.2 Допуск осевого биения уступов (заплечиков) вала для установки:
- колес зубчатых передач (таблица 11.3);
- колес незубчатых передач, муфт и т.д. (таблица 11.4);
- подшипников качения (таблица 11.5)
2.3 Допуск круглости и профиля продольного сечения
(или цилиндричности
):
- подшипников качения (таблица 11.6);
а) базой является ось центровых отверстий; б) базой является ось вала
Рисунок 11.2 – Обозначение допусков формы и расположения вала.
Таблица 11.2 – Допуски радиального биения поверхностей вала
Окружная скорость ![]() | ![]() | ![]() | ![]() | ![]() |
Допуск радиального биения поверхности
установки по отношению к ![]() | ![]() | ![]() | ![]() | ![]() |
Таблица 11.3 – Допуски осевого биения уступов (заплечиков) вала для установки колес зубчатых передач
| Степень точности зубчатых колес |
| ||
![]() | ![]() | ![]() | ||
Допуск осевого биения уступов (заплечиков) вала, мкм | 6, 7 | 20 | 30 | 40 |
8, 9 | 30 | 40 | 50 |
Таблица 11.4 – Допуски осевого биения уступов (заплечиков) вала для установки колес незубчатых передач, муфт
Окружная скорость ![]() | ![]() | ![]() | ![]() | ![]() | ![]() |
Допуск осевого биения уступов (заплечиков) вала, мкм | 60 | 50 | 40 | 30 | 20 |
Таблица 11.5 – Допуски осевого биения
Интервалы диаметров | Допуски осевого биения заплечиков, мкм | |||
валов (осей) | отверстий корпусов | |||
для классов точности подшипников | ||||
0 | 6 | 0 | 6 | |
Св. 18 до 30 | 21 | 13 | 33 | 21 |
Св. 30 до 50 | 25 | 16 | 39 | 25 |
Св. 50 до 80 | 30 | 19 | 46 | 30 |
Св. 80 до 120 | 35 | 22 | 54 | 35 |
Св. 120 до 180 | 40 | 25 | 63 | 40 |
Св. 180 до 250 | 46 | 29 | 72 | 46 |
Таблица 11.6 – Допуски формы посадочных поверхностей для подшипников 0 и 6 класса точности
Интервалы диаметров | Допуски формы посадочных поверхностей, мкм | |||
валов (осей) | отверстий корпусов | |||
Допуск круглости | Допуск профиля продольного сечения | Допуск круглости | Допуск профиля продольного сечения | |
Св. 18 до 30 | 3,5 | 3,5 | 5,0 | 5,0 |
Св. 30 до 50 | 4,0 | 4,0 | 6,0 | 6,0 |
Св. 50 до 80 | 5,0 | 5,0 | 7,5 | 7,5 |
Св. 80 до 120 | 6,0 | 6,0 | 9,0 | 9,0 |
Св. 120 до 180 | 6,0 | 6,0 | 10,0 | 10,0 |
Св. 180 до 250 | 7,0 | 7,0 | 11,5 | 11,5 |
ЦИЛИНДРИЧЕСКИЕ КОЛЕСА
1 Допуски формы и расположения
1.1 Допуск радиального биения , мкм поверхностей заготовки под диаметр вершин зубьев относительно поверхности А (таблица 11.7).
1.2 Допуск осевого биения , мкм, ступицы колеса и базовых поверхностей венца относительно поверхности А (таблица 11.8).
Рисунок 11.3 – Допуски формы и расположения цилиндрического колеса
Таблица 11.7 – Допуски радиального биения заготовок зубчатого колеса
Степень точности | Радиальное биение, мкм при диаметре заготовки, мм | ||||||
![]() | ![]() | ![]() | ![]() | ![]() | ![]() | ![]() | |
6 | 12 | 16 | 20 | 22 | 26 | 32 | 40 |
7 | 20 | 25 | 32 | 36 | 42 | 50 | 60 |
8 | 32 | 40 | 50 | 55 | 65 | 80 | 100 |
9 | 50 | 60 | 80 | 90 | 105 | 120 | 160 |
Таблица 11.8 – Допуски осевого биения базовых поверхностей венца и ступицы
Степень точности | Осевое биение, мкм | ||||
венца колеса шириною | Ступицы при | ||||
<55 | 55...110 | ![]() | ![]() | ![]() | |
6 | 17 | 9 | 20 | 30 | 40 |
7 | 21 | 11 | 20 | 30 | 40 |
8 | 26 | 14 | 30 | 40 | 50 |
9 | 34 | 18 | 30 | 40 | 50 |
Примечание. При |
КОНИЧЕСКИЕ КОЛЕСА
Рисунок 11.4 – Допуски формы и расположения поверхностей вала-шестерни
Рисунок 11.5 – Допуски формы и расположения поверхностей шестерни
Рисунок 11.6 – Допуски формы и расположения поверхностей зубчатого колеса
Таблица 11.9 – Допуски формы и расположения поверхностей заготовок конической шестерни (рисунок 11.5)
Диаметр отверстия ![]() | 25...100 | 100...150 | 150...200 | >200 |
Радиальное биение наружного диаметра вершин зубьев ![]() | 25 | 38 | 50 | 75 |
Базовая поверхность ![]() | 25...100 | 100...150 | 150...200 | >200 |
Торцевое биение поверхности ![]() | 15 | 25 | 35 | 45 |
Таблица 11.10 – Допуски формы и расположения поверхностей заготовок конической вал-шестерни (рисунок 11.4)
Базовая поверхность ![]() | 25...100 | 100...150 | 150...200 | >200 |
Торцевое биение поверхности ![]() | 5 | 8 | 12 | 15 |
Таблица 11.11 – Допуски формы и расположения поверхностей заготовок конического колеса (рисунок 11.6)
Наружный диаметр (базовой) поверхности ![]() | 25...100 | 100...150 | 150...250 | >250 |
Торцевое биение поверхности ![]() | 10...15 | 15...25 | 25...35 | 30...45 |
Биение поверхности вершин зубьев, мкм | 30 | 40 | 50 | 60 |
Торцевое биение поверхности ![]() | 15 | 25 | 35 | 45 |
Радиальное биение наружного диаметра вершин зубьев ![]() | 25 | 38 | 50 | 60 |
ЧЕРВЯКИ И ЧЕРВЯЧНЫЕ КОЛЕСА
1 Допуски формы и расположения червячного колеса:
1.1 Допуск радиального биения , мкм поверхностей заготовки под диаметр вершин зубьев относительно поверхности А (таблица 11.12).
1.2 Допуск осевого биения , мкм, ступицы колеса и базовых поверхностей венца относительно поверхности А (таблица 11.8).
Рисунок 11.7 - Допуски формы и расположения поверхностей червячного колеса
2 Допуски формы и расположения червяка:
2.1 Допуск радиального биения , мкм поверхностей заготовки под диаметр вершин витков относительно поверхностей А-Б (таблица 11.13).
Рисунок 11.8 - Допуски формы и расположения поверхностей червяка
Таблица 11.12 – Допуски радиального биения заготовок червячного колеса
Степень точности | Радиальное биение, мкм при диаметре | ||||||
![]() | ![]() | ![]() | ![]() | ![]() | ![]() | ![]() | |
6 | 12 | 16 | 20 | 22 | 26 | 32 | 40 |
7 | 20 | 25 | 32 | 36 | 42 | 50 | 60 |
8 | 32 | 40 | 50 | 55 | 65 | 80 | 100 |
9 | 50 | 60 | 80 | 90 | 105 | 120 | 160 |
Таблица 11.13 – Допуски биения заготовок червяка
Степень точности | Радиальное биение, мкм заготовок червяка при делительном диаметре | |||||
![]() | ![]() | ![]() | ![]() | ![]() | ![]() | |
6 | 12 | 13 | 14 | 16 | 18 | 22 |
7 | 17 | 18 | 20 | 22 | 25 | 30 |
8 | 21 | 22 | 25 | 28 | 32 | 38 |
9 | 26 | 28 | 32 | 36 | 40 | 48 |
Дата добавления: 2018-06-27; просмотров: 759; Мы поможем в написании вашей работы! |
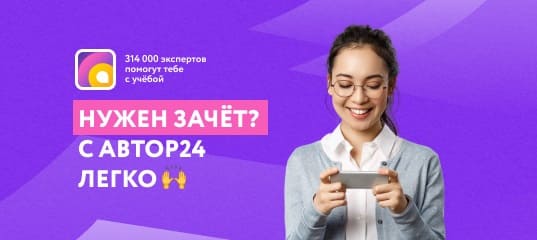
Мы поможем в написании ваших работ!