Определение знаменателя ряда частот вращения.
Анализ исходных данных: Основные исходные данные взяты из задания и приведены в таблице 1. Таблица1. Наименование Данные Тип станка Продольно – фрезерный (аналог А662) Тип привода электрический, с односкоростным электродвигателем фланцевого исполнения и сменными колесами. Количество ступеней регулирования z, шт. 18 Максимальный диаметр фрезы D, мм 240 Обрабатываемый материал 𝜎т , Н/мм2 750 Анализ аналога станка: Продольно – фрезерный станок модели А662. Назначение станка: Станок предназначен для фрезерования одновременно с двух сторон плоских поверхностей тяжелых деталей торцовыми, цилиндрическими и концевыми фрезами в условиях серийного и массового производства. На станке можно одновременно обрабатывать группу деталей средних размеров. Техническая характеристика станка А662: Наименование параметров Ед.изм. Величины Рабочая поверхность стола мм 450×1600 Наибольший продольный ход стола мм 1500 Расстояние от оси шпинделя до поверхности стола: - наибольшее мм 400 - наименьшее мм 115 Расстояние между головками шпинделя: - наибольшее мм 650 - наименьшее мм 300 Расстояние от оси шпинделя до хобота мм 195 Число скоростей вращения каждого шпинделя шт 12 Число оборотов шпинделя(пределы) об/мин 30 – 375 Количество скоростей подач стола шт 12 Скорость подач стола(пределы) мм/мин 36.5 – 475 Скорость быстрого перемещения стола мм/мин 3750 Мощность: - главного электродвигателя кВт 6 - привода быстрых перемещений стола кВт 2.3 - привода подач кВт 1.7 Рис.1 Общий вид продольно – фрезерного станка модели А662. Основные узлы станка: (рис.1). Станок А662 смонтирован из отдельных агрегатных узлов: А, Ж – стойки; Б, Е – шпиндельные бабки; В, Д – хоботы; Г – поперечная балка; З – стол; И – станина. Органы управления: На станке имеются квадраты 2 и 3 для ручного перемещения шпиндельных бабок по высоте и квадраты 1 и 4 для перемещения шпиндельных гильз вдоль своей оси, а также рукоятка для переключения величин подач стола. В представленной проекции общего вида эта рукоятка не видна. Движение в станке: Движение резания – вращение каждого из двух шпинделей с фрезами. Движение подачи – продольное поступательное перемещение стола с заготовкой. Вспомогательное движение – быстрое перемещение стола, ручные установочные вертикальные перемещения шпиндельных бабок и ручные поступательные перемещения гильз со шпинделями вдоль оси. Принцип работы: Обрабатываемые детали закрепляют на столе, которому сообщается поступательное движение только в продольном направлении. В двух горизонтальных шпинделях, смонтированных в выдвижных гильзах, расположенных в шпиндельных бабках, могут быть закреплены различные типы фрез. Настройка станка в соответствии с конфигурацией и размерами обрабатываемой детали производится перемещением шпиндельных бабок в вертикальных направлениях и шпиндельных гильз в горизонтальных направлениях вдоль оси. Станок позволяет работать по полуавтоматическом циклу: Быстрый подвод – рабочая подача – быстрый отвод в исходное положение и остановка; для этой цели предусмотрен командоаппарат и переставные кулачки, расположенные в боковом пазу стола.
|
|
|
|
Расчет режимов резания и расчетных усилий.
Цель расчета режимов резания:
установление оптимальных режимов обработки заготовки;
определение предельных частот вращения шпинделя станка и мощности ЭДВ.
Вначале выбираем виды фрезерования в зависимости от того, какие фрезы можно использовать на станке. При выборе пользуемся данными станка-аналога, а такжеисходные данные.
Расчет:
Максимальный размер заготовки согласно таблице1[1] вычисляется по формуле:
0.7L×0.7B =0.7×1600×0.7×450, где
|
|
L = 1600 мм – длина стола станка – аналога;
B = 450 мм – ширина стола станка – аналога.
Тогда наибольший размер обрабатываемой заготовки будет 1120×315 мм.
Произведем расчеты режимов резания для чернового и чистового фрезерования торцовой, концевой и цилиндрической фрезами.
В качестве примера проведем расчет чернового фрезерования торцовой фрезой максимального диаметра и чистовой обработки концевой.
Максимальный диаметр торцевой фрезы по заданию и по ГОСТ 24359-80
D = 250 мм;
диаметр концевой фрезы определяем согласно таблице1[1]:
dк = 0.15× D = 0.15×250 =37.5мм. Примем ближайшую по диаметру стандартную концевую фрезу по ГОСТ 17026 – 71*. Тогда dк = 36 мм;
Диаметр цилиндрической фрезы по ГОСТ 29092 – 91 равен 160мм.
Черновое фрезерование торцевой фрезой:
B = D/1.25 = 250/1.25 =200 мм – ширина фрезерования (назначается для достижения производительных режимов резания диаметр фрезы D должен быть больше ширины фрезерования B, т.е. D=(1.25 – 1.5) ×B).
t = 5 мм – глубина фрезерования (назначается при черновом фрезеровании [2])
Sz = 0,15мм/зуб – подача на один зуб фрезы(стр. 283[2]);
z = 24 – число зубьев фрезы;
T = 240 мин – стойкость фрезы(стр. 290[2]);
𝜑 = 450 – угол в плане фрезы;
Торцевая фреза с ножами, оснащенными пластинами из быстрорежущей стали Р6М5(по рекомендации [1]);
|
|
Схема установки фрезы – смещенная.
Скорость резания:
м/мин
Но по примечанию стр.290[2] необходимо полученную скорость умножить, на коэффициент равный 1.1 и тогда получаем скорость резания:
Vр = V×1.1 = 39.6≈40 м/мин.
где
По табл.39[2]:
СV = 41 – коэффициент;
Показатели степени:
x=0,1; y=0,4; m=0,2; u=0.15;q=0.25; р=0.
KV– поправочный коэффициент на скорость резания, учитывающий влияние:
КмV=Kr×(750/𝛿в)-n =1×(750/750)0.9=1 – коэффициент учитывающий материал заготовки, где
𝛿в - Предел кратковременной прочности, [МПа];
Kr= 1,0 – коэффициент для материала инструмента(стр262[2]);
nv =0,9 – показатель степени при обработке(стр262[2]).
КnV=0,8 - коэффициент учитывающий состояние поверхности (стр.263[2])
КuV=1,0 - коэффициент учитывающий материал инструмента (стр.263[2])
KV = КмV × КnV × КuV=1×0.8×1.0=0.8
Частота вращения фрезы, соответствующая найденной скорости резания:
,об/мин
Главнаясоставляющаясилрезанияприфрезеровании–окружная сила:
Pz=((10×Ср×tX×SzY×Bu×z)/(Dq×nw))×KP=((10×82.5×50.95×0.150.8×2001.1×24)/(2501.1×510)×1=15667Н.
Но по примечанию стр.291[2] необходимо полученную окружную силу умножить, на коэффициент равный 1.2:
Pz=Pz×1.2 =15667×1.2 =18800 Н
Где (из стр.291[2])
Ср=82.5 коэффицент;
x =0.95; y =0,8; u=1.1;q= 1.1;w=0 – показатели степени.
КРм– поправочный коэффициент учитывающий влияние качества обрабатываемого материала на силовые зависимости.
КmP =( 𝛿в /750)n = (750/750)0,3= 1
n=0.3 – показатель степени (стр.264[2]).
Крутящий момент на шпинделе:
Мкр=(Pz×D)/(1000×2)=(18800×250)/2000=2350 Н×м
Мощность резания:
N = (Pz×V)/(1020×60)=18800×40/61200=12.3 кВт.
Чистовое фрезерование концевой фрезой:
D = 0,15×Dторцев.фрезы =0,15×250 = 37.5 – диаметр инструмента, табл.1[1] и согласуя с ГОСТ 17026 – 71 выбираем окончательно диаметр концевой фрезы:
D = 36 мм.
B =26 мм – ширина фрезерования (назначается для достижения производительных режимов резания диаметр фрезы D должен быть больше ширины фрезерования B, т.е. D =(1.25 – 1.5)×B)⇒B =D/1,375.
t =0.5 мм – глубина фрезерования (назначается при черновом фрезеровании [2])
Sz =S/z =0.25/6 = 0,042мм/зуб – подача на один зуб фрезы(стр. 283[2]и с помощью линейной интерполяции);
z = 6 – число зубьев фрезы;
Концевая фреза с напаянными пластинами из твердого сплава марки ВК8(по рекомендации [1]);
T = 112 мин – стойкость фрезы(стр. 290[2]и с помощью линейной интерполяции).
Скорость резания:
м/мин
где
По табл.39[2]:
СV = 234 – коэффициент;
Показатели степени:
x=0,24; y=0,26; m=0,37; u=0.1;q=0.44; р=0.13
KV– поправочный коэффициент на скорость резания, учитывающий влияние:
КмV=Kr×(750/𝛿в)-n =1×(750/750)-1=1 – коэффициент учитывающий материал заготовки, где
𝛿в - Предел кратковременной прочности, [МПа];
Kr= 1,0 – коэффициент для материала инструмента(стр262[2]);
nv =1,0 – показатель степени при обработке(стр262[2]).
КnV=0,8 - коэффициент учитывающий состояние поверхности (стр.263[2])
КuV=0.4 - коэффициент учитывающий материал инструмента (стр.263[2])
KV = КмV × КnV × КuV=1 ×0.8×0.4=0.32
Частота вращения фрезы, соответствующая найденной скорости резания:
,об/мин
Главнаясоставляющаясилрезанияприфрезеровании–окружная сила:
Pz=((10×Ср×tX×SzY×Bu×z)/(Dq×nw))×KP=
= (10×12.5×0.50.85×0.0420.75×361×6)/(360.73×8580.13)×1=211 Н.
Но по примечанию стр.291[2] необходимо полученную окружную силу умножить, на коэффициент равный 1.2:
Pz=Pz×1.2 =176×1.2 =211 Н
Где (из стр.291[2])
Ср=12.5 коэффицент;
x =0.85; y =0,75; u=1.0;q= 0.73;w= – 0.13 – показатели степени.
КРм– поправочный коэффициент учитывающий влияние качества обрабатываемого материала на силовые зависимости.
КmP =( 𝛿в /750)n = (750/750)0,3= 1
n=0.3 – показатель степени (стр.264[2]).
Крутящиймоментнашпинделе:
Мкр=(Pz×D)/(1000×2)=(211×36)/2000=7.758≈8 Н×м
Мощностьрезания:
N = (Pz×V)/(1020×60)=211×97/61200=0.33 кВт.
Для оставшихся переходов занесем данные в таблицу 3.
Таблица 3
Режимы резания
№ пп |
Вид обработки | Размеры обработки(L× B) | Материал заготовки |
Режущий инструмент |
Элементы режима резания | |||||||||
Ширина фрезерования | Глубина | Подача | Стойкость | Скорость резания | Частота вращения | Сила резания | Мощность резания | Крутящий момент | ||||||
B | t | Sz | T | V | n | Pz | N | Mкр | ||||||
мм | мм | мм/зуб | мин | м/мин | об/мин | Н | кВт | Н×м | ||||||
1 |
Торцевое фрезерование Плоскости
| Черновое | 1120×315 мм | Конструкционная сталь 𝛿т=750 Н/мм2 | Торцевая фреза Р6М5 ГОСТ 9473-80 ∅250мм | 200 | 5 | 0.15 | 240 | 40 | 51 | 18800 | 12.3 | 2350 |
Чистовое | Торцевая фреза ВК8 ГОСТ 9473-80 ∅250мм | 200 | 0.5 | 0.015 | 240 | 235 | 300 | 422 | 1.62 | 52.75 | ||||
2 2 |
Концевое фрезерование плоскости
| Черновое | Концевая фреза Р6М5 ГОСТ17026–71 ∅36мм | 26 | 5 | 0.1 | 112 | 34 | 301 | 4454 | 2.47 | 80 | ||
Чистовое | Концевая фреза ВК8 ГОСТ17026–71∅36мм | 26 | 0.5 | 0.042 | 112 | 97 | 858 | 211 | 0.33 | 3.80 | ||||
3 |
Цилиндрическое фрезерование плоскости | Черновое | Цилиндрическая фреза Р6М5 ГОСТ 29092-91 ∅160мм | 250 | 5 | 0.15 | 192 | 27 | 54 | 63602 | 28 | 5088 | ||
Чистовое | Цилиндрическая фреза ВК8 ГОСТ 29092-91 ∅160мм | 250 | 0.5 | 0.06 | 192 | 125 | 249 | 4826 | 9.86 | 386 |
Вывод:
На проектируемом станке применение чернового фрезерования максимальной по диаметру цилиндрической фрезой и с приведенными данными режимами резания (табл.3) нецелесообразно. Это связанно с возникновением больших сил резания, потреблением высокой мощности и т.д. Таким образом, исключая данный тип фрезерования из расчета, приходим к следующим предельным значениям, которые берем за основу проектирования.
Исходя из таблицы 3, находим:
Предельные значения:
1. n min = 51 об/мин и n max = 858 об/мин;
2. Максимальная мощность резания составляет N =12.3 кВт;
3. Максимальный крутящий момент Mкр = 2350 Н×м.
2. Кинематический расчет привода главного движения:
Целью кинематического расчета является разработка кинематической схемы (КС) привода. Расчет выполняется на основе графоаналитического метода.
Исходными данными для кинематического расчета являются:
1. Количество ступеней регулирования частот вращения .
2. Предельные значения частот вращения на выходе ПГД:
n min = 51 об/мин и n max = 858 об/мин;
Определение знаменателя ряда частот вращения.
Найдем диапазон регулирования скоростей:
При ступенчатом регулировании ряда частот вращения привода строится по геометрическому закону, поэтому диапазон регулирования R, число степеней регулирования z и знаменатель 𝜑 связанны между собой:
По рекомендации [1] в соответствие с рядом стандартных значений, выбирается ближайшее значение знаменателя ряда:
, и выписывается для него ряд частот вращения:
57; 64; 72; 81; 91; 102; 114; 128; 143; 160; 179; 200; 224; 251; 281; 315; 353; 395 об/мин.
, тогда ряд частот вращения имеет вид:
64; 81; 102; 129; 163; 205; 259; 326; 411; 518; 653; 823; 1037; 1307; 1647; 2075; 2615; об/мин.
Стандартный ряд не обеспечивает необходимое число ступеней регулирования, поэтому знаменатель ряда выбираем расчетный и для него находим ряд частот вращения:
n1=nmin= 51 [об/мин] | n10 = n9×𝜑 =193×1.181=228 |
n2 = n1×𝜑 =51×1.181=60 | n11 = n10×𝜑 =228×1.181=269 |
n3 = n2×𝜑 =60×1.181=71 | n12 = n11×𝜑 =269×1.181=318 |
n4 = n3×𝜑 =71×1.181=84 | n13 = n12×𝜑 =318×1.181=376 |
n5 = n4×𝜑 =84×1.181=99 | n14 = n13×𝜑 =376×1.181=444 |
n6 = n5×𝜑 =99×1.181=117 | n15 = n14×𝜑 =444×1.181=524 |
n7 = n6×𝜑 =117×1.181=138 | n16 = n15×𝜑 =524×1.181=619 |
n8 = n7×𝜑 =138×1.181=163 | n17 = n16×𝜑 =619×1.181=730 |
n9 = n8×𝜑 =163×1.181=193 | n18 = n17×𝜑 =731×1.181=861 |
Дата добавления: 2018-06-27; просмотров: 612; Мы поможем в написании вашей работы! |
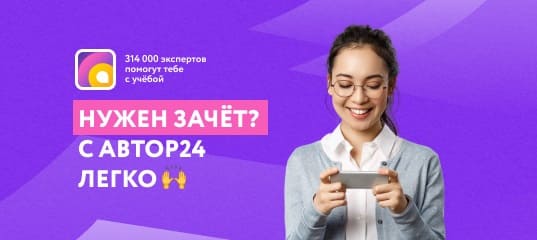
Мы поможем в написании ваших работ!