Особенности нормирования вспомогательного времени на
Станках, выполняющих однопереходные работы с
Постоянными режимами резания в одной операции
При обработке заготовок на станках: токарных многорезцовых и гидрокопировальных, резьбо-, зубо- и шлицеобрабатывающих, протяжных центровальных и других, выполняющих однопереходные работы с постоянными режимами в одной операции [28, карты 59-85] вспомогательное время дано в виде укрупненного комплекса приемов на операцию, включая время на установку и снятие детали.
, (35)
где tоп – норма основного времени на переход в данной операции, мин;
tв оп – вспомогательное время, связанное с операцией, мин;
Ктв – поправочный коэффициент в зависимости от характера серийности работ.
Вспомогательное время дано для каждого вида оборудования в зависимости от способа установки заготовки в том или ином приспособлении и способа закрепления заготовки (например, ключом или призматическим зажимом), в зависимости от веса детали, вручную или подъемником.
Для станков-полуавтоматов вспомогательное время на операцию включает время на установку и снятие заготовки и пуск станка. Время же на подводы и установку инструмента на размер обработки, на холостые ходы, включение и выключение подачу учитываются по паспортным данным станка и включается в норму штучного времени как отдельные слагаемые.
Если же вспомогательное время определяется на станок с ручным управлением, то дополнительных расчетов не требуется.
|
|
В нормативы времени на операцию не включено время на измерение обрабатываемой поверхности в процессе обработки, так как обеспечение точности размеров на данных станках достигается автоматически соответствующей конструкцией станка или режущего инструмента. Время на дополнительные приемы, связанные с измерением в процессе обработки, например, на шлицешлифовальных станках в зависимости от точности обработки указано в нормативах дополнительно.
Например, при установке на зубофрезерный станок 5Б32 с ручным управлением [28, карта 63] 5 заготовок весом 4,4 кг каждая устанавливаемых на оправке с креплением гайкой без выверки при подаче вдоль оси колеса за один рабочий ход (проход) на длину 120 мм вспомогательное время, связанное с операцией на одну заготовку составит 1,2 мин. При установке на оправку 5 заготовок на каждую последующую заготовку добавляется 0,26 мин, т.е. на 4 заготовки добавится 4 ´ 0,26 = 1,04 мин.
Кроме того, согласно примечанию при длине обработки 100 и более мм на станке модели 5В32 вспомогательное время на операцию уменьшается на 0,4 мин.
Тогда вспомогательное время на операцию
tв оп = 1,2 + 1,04 – 0,4 = 1,84 мин на 5 заготовок.
|
|
Вспомогательное время на контрольные измерения при обработке фрезой, установленной на размер на зубофрезерных станках не учитывается.
Если при одностаночном обслуживании основное время tо=22,9 мин на 5 деталей, то общее оперативное время при обработке 5 заготовок
tоп5 = tо + tв оп = 22,9 + 1,84 = 24,74 мин.
Оперативное время на обработку одной детали
мин.
При затратах времени на обслуживание рабочего места aоб= 4,5% от tоп9 на отдых aотд=49% от tоп, Тпз=33 мин и размере партии запуска nз=100 шт
мин.
Продолжительность обработки партии деталей
мин.
Продолжительность обработки за одну смену
мин.
Число смен, необходимых для обработки партии деталей
.
Тогда при обработке на средних станках поправочный коэффициент на вспомогательное время в зависимости от серийности работ [28, карта 1] равен Ктв=1,0. Таким образом, в данном случае уточнять норму штучно-калькуляционного времени не требуется.
Особенности выбора режимов резания при
многоинструментной обработке
Одним из основных путей снижения оперативного времени является использование многоинструментальных наладок.
На универсальных станках используется последовательная концентрация технологических переходов, когда каждый новый переход осуществляется другим инструментом последовательно за предыдущим. Например, установка четырех резцов, работающих последовательно, в четырехпозиционном резцедержателе токарного станка. В этом случае основное время операции равно сумме основных времен технологических переходов.
|
|
При параллельной концентрации технологических переходов, т.е. при их совмещении во времени, основное время операции равно основному времени самого длительного перехода. Например, при обработке на вертикальном многошпиндельном токарном полуавтомате последовательного действия основное время операции равно основному обработки на самой длительной позиции, а если на ней применяется один инструмент, то основному времени технологического перехода, выполняемого этим инструментом.
При параллельно-последовательной концентрации технологических переходов группы инструментов работают последовательно, а часть инструментов в группе параллельно, например, многосуппортные станки с последовательной работой суппортов.
В зависимости от типа станка определение режимов резания имеет свои особенности, но есть и общие закономерности.
В нормативах [21] предусмотрено два этапа расчетов режимов резания при многоинструментной обработке на различных станках:
|
|
1) расчет кинематических элементов режима резания (V, n, S) для отдельных групп инструментов, связанных общими кинематическими параметрами:
а) определение длины рабочего и холостого ходов стола, головок или суппортов в зависимости от типа станка;
б) определение нормативных подач (на оборот, минутной или на зуб);
в) определение периода стойкости лимитирующих инструментов, по которым идет расчет скорости резания с учетом коэффициента времени резания l, числа инструментов в наладке и условий работы;
г) расчет скоростей резания и частот вращения шпинделей станков с учетом принятой стойкости инструмента;
д) корректировка расчетных режимов резания по паспорту станка, чтобы паспортные данные не превышали расчетные на 10-15%;
е) расчет основного времени технологической операции на данном станке.
2) корректировка режимов резания по позициям с учетом выравнивания времени работы отдельных групп инструментов, кинематически не связанных между собой, например, путем более равномерного распределения инструментов по позициям на многопозиционных станках.
Например. На токарном многорезцовом полуавтомате 1А730 (N0=14 кВт, h=0,81) нужно обработать ступенчатый валик (рисунок 2) [18] из стали 40 с sв=650 МПа (65 кг/мм2), обеспечив точность размеров h11 и шероховатость цилиндрических ступеней Ra=5 мкм (Ñ5) заготовка, предварительно обработанная, имеет форму детали с промежуточными припусками на сторону на каждой ступени 1,5 мм.
Резцы 1, 4, 7 – токарные проходные с сечением державки 16´25 мм, j=45°, r=1 мм. Резцы 2 и 3 – проходные упорные 16´25 мм, j=90°, g=10°, r=1 мм. Режущие пластины резцов 1, 2, 3, 4, 7 изготовлены из твердого сплава Т15К6. Резцы канавочные 5 и 6 имеют сечение державки 16´25 мм, b=5 мм и изготовлены из твердого сплава Т5К10. Работа без охлаждения.
Рисунок 2 – Схема многорезцового точения
Последовательность расчета основного времени.
1. Определение расчетных размеров обработки:
- за расчетный диаметр принимаем наибольший диаметр обрабатываемой заготовки Dр=88 мм;
- длина рабочего хода продольного суппорта
, (36)
где lрез пр – наибольшая длина резания продольного суппорта, в данном случае длина резания резцом 2, lрез пр=60 мм;
ll – суммарная длина врезания и перебега этого резца при точении в упор с прямым врезанием t до 2 мм, j=90°, ll=1 мм [21, прил. 4, лист 1];
lдоп – дополнительный путь, вызванный в ряде случаев особенностями наладки и конфигурации заготовки, с учетом отклонений по длине заготовке на предыдущей операции lдоп=2 мм.
Тогда Lрх пр = 60 + 1 + 2 = 63 мм;
- длина рабочего хода поперечного суппорта
, (37)
где lрез п – наибольшая длина резания поперечного суппорта,
lрез п = (85 – 80) / 2 = 2,5 мм;
ll – длина врезания канавочных резцов,
ll=1 мм, т.к. из примечания к [21, прил. 4, лист 1] при радиальном врезании ll = lподв = 1÷2 мм;
lдоп=0.
Тогда Lрх п = 2,5 + 1 = 3,5 мм.
2. Выбор значения подачи.
Для резцов продольного точения подачу выбираем в зависимости от значения параметра Ra шероховатости поверхности при обработке углеродистой стали с V=250 м/мин, r=1 мм, для всех ступеней Ra=5 мкм (Ñ5), Sпр = 0,3÷0,35 мм/об. Если бы на какой-либо ступени шероховатость была бы меньше, чем на других ступенях, то подачу нужно было бы выбрать по этой шероховатости [21, карта 5].
Для резцов поперечного суппорта при ширине резца b=3 мм для наибольшего диаметра d=30 мм при этой ширине реза при обработке стали Sп=0,10…0,12 мм/об. Так как паспортные значения подачи в справочнике [13] отсутствуют, то за паспортное принимают значение подачи из [21, карта 6, лист 2] Sпр=0,34 мм/об, Sп=0,1 мм/об.
3. Определение периода стойкости лимитирующих инструментов.
Период стойкости каждого лимитирующего инструмента определяется по формуле:
, (38)
где Тм – период стойкости инструмента в минутах машинной работы станка;
l – коэффициент времени резания.
, (39)
где nрез – число оборотов шпинделя за время резания;
nрх – число оборотов шпинделя за время рабочего хода суппорта.
Для любого лимитирующего инструмента при числе инструментов в наладке до 8 и наличии фасочных и канавочных резцов более 20% от общего количества инструментов в наладке принимаем вторую группу наладки и тогда Тм=150 мин [21, с. 30].
Лимитирующим среди резцов продольного суппорта является резец 4, обрабатывающий наибольший диаметр заготовки, а среди резцов поперечного суппорта – канавочные резцы 5 и 6, работающие в наиболее неблагоприятных условиях по сравнению с резцом 7.
Для определения коэффициента резания l резца 4 нужно:
а) определить nрез по формуле:
(40)
оборотов (lрез=50 мм из рисунка 1)
б) определить nрх
, (41)
где Lрх – длина рабочего хода суппорта, мм;
S – подача суппорта, мм/об.
Для суппортов, работающих последовательно, число оборотов шпинделя принимают за время от начала рабочего хода одного суппорта до конца работы второго [18].
Тогда nрх = Lрх пр / Sпр + Lрх п / Sп = 63/0,34 + 3,5/0,1 = 220 оборотов;
в) рассчитать l4
г) определить Т
мин.
Поправочный коэффициент на скорость резания при Т=101 Кт v=0,89 (получен путем интерполяции) [21, с. 36].
Для канавочных резцов 5 и 6:
а) оборотов;
б) , принимаем l5,6=0,12;
в) мин.
По нормативам [21, с. 31] принимаем наименьшее значение периода стойкости Т=30 мин, Кт v=1,15.
4. Расчет скорости резания.
Скорость резания резцом 4 при наружном продольном точении углеродистой стали с sв = 600 МПа (sв=56÷62 кг/мм2) при глубине резания 1,5 мм (до 3 мм) и подаче S=0,34 мм/об (до 0,38 мм/об) и угле j=45° равна Vн=188 мм/мин [21, карта 6, лист 2]. С учетом дополнительного коэффициента к=0,85, гарантирующего получение расчетных значений стойкости [18, с. 68] и коэффициента Кт v=0,89.
м/мин
Скорость резания для резцов 5 и 6 при прорезке канавок в стали с sв=600 МПа (sв=56÷62 кг/мм2) при подаче S=0,1 мм/об равна Vн=153 м/мин [21, карта 19].
Необходимо учесть поправочные коэффициенты на скорость резания для измененных условий работы в зависимости от:
1) отношения диаметров d:D = 80:85 = 0,94, Кd v=0,84;
2) наличия охлаждения – без охлаждения, Коv=1,0;
3) марки твердого сплава Т15К6, Кu v=1,54, а также коэффицинты Кт v=1,15 и к=0,85 [21, карта 19].
Тогда скорость резания
V5 = Vн ´ Кт v ´ Кd v ´ Ко v ´ Кu v ´ к =
= 153 ´ 1,15 ´ 0,84 ´ 0,1 ´ 1,0 ´0,85 = 126 м/мин.
5. Расчет частот вращения шпинделей станков и корректировки по паспорту станка:
а) для резца 4, об/мин;
б) для резца 5, об/мин.
Принимаем ближайшее меньшее значение по паспорту стан-ка nn = 450 об/мин (при отсутствии паспорта в учебных целях допустимо рассчитать среднее число оборотов nс = (472 + 514)/2 = = 493 об/мин и округлить до 0 или 5 в меньшую сторону nn=490 об/мин ).
6. Расчет значений фактической скорости резания:
- для резца 4, м/мин;
- для резца 5, м/мин;
- для резца 1, м/мин;
- для резца 2, м/мин;
- для резца 3, м/мин;
- для резца 6, м/мин.
7. Определение мощности, необходимой для резания.
Для резца 4 при точении стали с sв=600 МПа (sв=59÷97 кг/мм2), глубине резания t=1,5 мм (до 2 мм), подаче S=0,34 мм/об (до 0,37 мм/об) и скорости резания Vн=124 м/мин (до 131 м/мин) равна Np4=2,4 кВт.
Для резцов 3 (V3=126 м/мин) и 2 (V2=117 м/мин)
Np3 = Np2 = Np4 = 2,4 кВт.
Для резцов 1 (V1 = 106 м/мин) Np1 = 2,0 кВт.
Тогда суммарная мощность для продольного суппорта
Np пр = Np1 + Np2 + Np3 + Np4 = 2,0 + 2,4 + 2,4 + 2,4 = 9,2 кВт.
Для того, чтобы мощности привода хватило на резание резцами продольного суппорта нужно, чтобы выполнялось неравенство Nр пр<ND´h. Это условие выполняется 9,2<14´0,8 или 9,2<11,2 кВт.
Мощность на резание резцами поперечного суппорта не рассматривается и ее значения для канавочных и фрезерных резцов отсутствуют в нормативах [21] из-за их незначительной величины.
8. Расчет основного времени.
Для суппортов, работающих последовательно применяется формула:
(42)
В нашем случае:
мин.
Для двух операций в двух вариантах каждая, заполняются 4 бланка операционных карт, пример заполнения которых приведен в пособии [8, прил.16] и 4 бланка операционных эскизов, пример заполнения которых приведен в пособии [8, прил. 6].
При небольших размерах операционных эскизов можно принимать бланки операционных карт с полем по эскиз, пример заполнения которых приведен в пособии [8, прил. 5].
Если операционные эскизы на две сравнительные операции одинаковые, то можно применить один бланк эскиза на две операции, а если эскиз изображен на специальном поле операционной карты, то можно сослаться на этом поле на операционный эскиз альтернативной операции (см. операционный эскиз к операции).
Дата добавления: 2018-05-12; просмотров: 380; Мы поможем в написании вашей работы! |
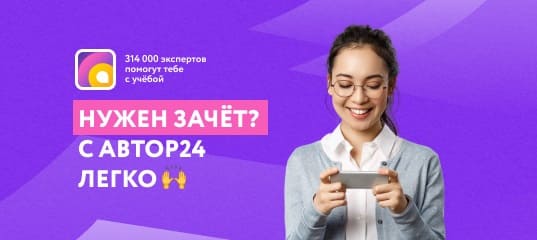
Мы поможем в написании ваших работ!