Проектирование технологического процесса
Механической обработки заготовки
Отнесение детали по внешнему виду к классу типовых деталей
Для отнесения детали к одному из типов: втулки, валы, корпуса, зубчатые колеса, рычаги и др., нужно знать только ее конфигурацию и габариты.
К валам относятся детали, имеющие форму тел вращения с отношением длины к среднему диаметру L/D>2 (валы, оси и т.д.).
К втулкам относят детали, образованные концентричными наружными и внутренними поверхностями вращения с отношением 0,5<L/D<2 (втулки, гильзы, фланцы).
К рычагам относятся детали, состоящие из нежесткого стержня и головок с отверстиями, оси которых расположены параллельно или под углом (рычаги, вилки, шатуны и т.д.).
К корпусам относятся детали призматического типа с плоскими поверхностями больших размеров и основными отверстиями, оси которых расположены параллельно друг другу или под углом.
К зубчатым колесам относятся детали – тела вращения с элементами зубчатого зацепления (цилиндрические, конические и червячные).
Для облегчения отнесения детали к нужному типу в методическом пособии [7] описаны основные виды типовых деталей, их служебное название и даны их изображения.
Установление маршрута технологических операций механической обработки
Установление маршрута технологических операций механической обработки детали производится на основе типовых технологических процессов обработки типовых деталей для определенного ранее типа производства.
|
|
Для каждого типа деталей рассмотрены основные технологические задачи, основные схемы базирования, применяемый материал, виды и методы получения заготовок.
Отнеся деталь к одному из указанных типов, нужно на основании соответствующих таблиц пособия [7] выбрать типовой маршрут для данного типа производства и скорректировать его применительно к конкретным особенностям каждой детали. В таблицах приведены типовые маршруты механической обработки с указанием основных этапов, оборудования и приспособлений. Для облегчения этой задачи типовые ТП получения заготовок и обработки конкретных деталей (валов и т.д.) приведены с указанием переходов для каждой операции, оборудования, приспособлений, инструментов, операционных эскизов и схем обработки на основных операциях для валов, втулок и зубчатых колес.
Если деталь нельзя отнести ни к одному из указанных типов, то нужно разрабатывать индивидуальный ТП в соответствии с рекомендациями [3].
Подробно установление маршрута технологических операций механической обработки заготовки с примером для цилиндрического зубчатого колеса приведено в методических указаниях [3, п. 4.2.2].
|
|
Выбор оборудования и оснастки для выполнения
Операций технологического процесса
Выбор металлорежущих станков
При выборе металлорежущего станка для выполнения определенной технологической операции должны выполняться два принципа.
1. Технический – изготовленная деталь должна отвечать требованиям по точности выполняемых размеров и шероховатости обработанных поверхностей, указанным в операционном эскизе;
2. Экономический – затраты на изготовление детали на данной операции должны быть минимальны.
Предварительный выбор модели металлорежущего станка производится в следующей последовательности:
а) группа станка (первая цифра индекса модели) определяется по методам обработки поверхностей на операции, выбранным ранее из маршрута обработки поверхностей на основании формы, точности и шероховатости поверхности. Например, предварительное и чистовое точение и растачивание, зенкерование и развертывание поверхностей деталей – тел вращения производится на станках первой (1) токарной группы;
б) тип станка (вторая цифра индекса модели) определяется с учетом типа производства, соотношений размеров детали, вида и расположения обрабатываемых поверхностей, и далее уточняется на основе экономического расчета;
|
|
в) типоразмер станка (третья или третья и четвертая цифры индекса модели) выбирают на основании габаритных размеров заготовки (длины, диаметра, ширины, высоты) и размеров обрабатываемой поверхности (модуля зубчатого колеса, диаметра и длины шлифуемого отверстия и т.д.) минимально необходимых по габаритам рабочего пространства станка для установки детали, из справочника [13], из каталога станков или по таблицам основных характеристик станков;
г) модель станка должна быть выбрана с учетом необходимой точности обработки для выполнения технического принципа. Точность станка (кроме нормальной – Н) оговаривается буквой в конце цифровой части индекса модели: П – повышенная, В – высокая, А – особо высокая и С – особо точная. Для черновой, получистовой и однократной обработки можно применять станки нормальной точности, для чистовой обработки при достижении точности до IT7 – повышенной П и высокой В – точности.
Выбор усовершенствованной модели станка по сравнению с базовой, имеющей систему числового управления станком (Ф1, Ф2, Ф3, Ф4) или автоматической смены инструмента (Р, М) производится на основе экономического расчета. После выбора режимов резания модель станка уточняется по диапазонам частот вращения шпинделя и подач.
|
|
Для операций, варианты которых не сравниваются на основе экономического расчета, модель станка выбирается по справочнику [13].
Для операций, варианты которых сравниваются на основе экономического расчета, модель станка уточняется по справочнику [14] с учетом экономических показателей, причем станки должны быть приблизительно одного типоразмера, например, токарные станки с наибольшим диаметром обрабатываемой заготовки 400 мм.
Дата добавления: 2018-05-12; просмотров: 317; Мы поможем в написании вашей работы! |
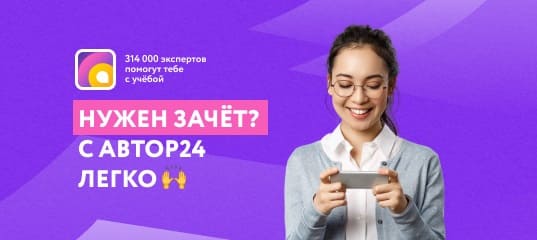
Мы поможем в написании ваших работ!