I ТЕХНОЛОГИЯ ИЗГОТОВЛЕНИЯ КОНСТРУКЦИЙ ИЗ МКМ И УУКМ
Рис. 3.6. Технологическая схема производства полуфабрикатов и изделий методом диффузионной сварки
240
16-243
241
3.2. Твердофазные методы изготовления деталей
ца—матрица, т.е. практически на поверхностях матрицы и уп-рочнителя. В связи с этим существенное влияние на качество процесса и качество полученного методом диффузионной сварки КМ оказывает состояние контактирующих поверхностей матрицы и упрочнителя.
Волокна, проволоки и нитевидные кристаллы, применяв-мые в качестве упрочнителей, перед процессом диффузионной сварки чаще всего подвергают поверхностной очистке химическими методами. Это связано с наличием на поверхности упрочнителей различного вида замасливателей, смазок, применяемых в процессе изготовления волокон и проволок, тонких слоев оксидов и др. Такую очистку осуществляют в щелочных или кислотных травителях. С целью повышения прочности связи на границе раздела упрочнителя с матрицей на поверхность волокон и нитевидных кристаллов в некоторых случаях наносят покрытие из металла или их соединений методами химического, электрохимического осаждения, осаждения из газовой фазы и др.
Как было отмечено выше, при изготовлении КМ методом диффузионной сварки под давлением матрицу чаще всего применяют в виде фольги. Поверхность фольги из металлов и сплавов может быть загрязнена различными смазками, применяемыми в процессе ее изготовления, может быть покрыта слоем оксида, затрудняющим протекание диффузионных процессов. Наличие плотной оксидной пленки особенно характерно для фольги из алюминия и его сплавов. К основным методам подготовки поверхности материала матрицы относятся промывка, обезжиривание, механическая очистка, химическая обработка.
|
|
Промывку применяют главным образом для очистки поверхности фольги от различного вида поверхностных загрязнений и осуществляют в спирте, горячей и холодной воде, в различных моющих средствах. Обезжиривание применяют в тех случаях, когда поверхность фольги загрязнена маслами, чаще всего входящими в состав смазок, применяемых при прокатке. Обезжиривание проводят в бензине, ацетоне, четыреххлорис-том углероде, дихлорэтане и специальных растворителях, в состав которых обычно входят перечисленные выше вещества.
3. ТЕХНОЛОГИЯ ИЗГОТОВЛЕНИЯ КОНСТРУКЦИЙ ИЗ МКМ И УУКМ
Механическая обработка является более радикальным средством очистки поверхности фольги, поскольку этот метод связан с удалением на небольшую глубину поверхностных слоев материала. Она позволяет не только очистить поверхность фольги, но и удалить оксидный слой, а также обнажить внутренние, неокисленные и поэтому более активные для прохождения диффузионных процессов слои матрицы. Механическую обработку можно осуществлять с помощью шлифовальной бумаги, металлических щеток, абразивного инструмента. Для удаления частиц металла и абразива, оставшихся на поверхности фольги после такой обработки, обычно применяют промывку.
|
|
Химическая обработка также сопровождается удалением на некоторую глубину поверхностных слоев материала матрицы. Обычно эта обработка включает в себя операции обезжиривания, щелочное или кислотное травление и иногда сочетание того и другого, пассивирование поверхности. После каждой из перечисленных операций обязательно применяют промывку. Реактивы для химической обработки специально подбирают для каждой матрицы. Технологические параметры процесса химической обработки, такие как концентрация травителей, температура и время обработки, определяют экспериментально из условий обеспечения необходимого качества поверхностных слоев, сохранения этого качества в течение некоторого времени (включающего промежуток между операциями химической обработки и диффузионной сварки) и съема поверхностных слоев матрицы заданной толщины. Последнее условие связано с тем, что матрицу обычно используют в виде фольги малой толщины (0,007...0,1 мм), поэтому удаление с поверхности слоя в несколько микрон в дальнейшем может значительно изменить соотношение матрицы и упрочнителя в КМ.
|
|
В соответствии с методом диффузионной сварки под давлением КМ получают прессованием в вакууме при определенной температуре и давлении в среде инертных газов или воздухе.
Прессование
Основной операцией процесса изготовления КМ методом диффузионной сварки под давлением является прессование. Именно при выполнении этой операции происходит соедине-
242
16*
243
3. ТЕХНОЛОГИЯ ИЗГОТОВЛЕНИЯ КОНСТРУКЦИЙ ИЗ МКМ. И УУКМ |
3.2. Твердофазные методы изготовления деталей
ние отдельных элементов предварительных заготовок в компактный материал (формирование изделий). В отличие от прессования как метода обработки давлением металлов и сплавов, заключающегося в выдавливании металла из замкнутой полос- ти через отверстие в матрице и связанного с большими степенями деформации обрабатываемого материала, данный процесс по существу больше соответствует процессу прессования порошковых материалов, применяемому в порошковой металлургии. Прессование заготовок композитов в большинстве случаев осуществляется в замкнутом объеме (в пресс-формах, состоящих из матрицы и двух пуансонов типа пресс-форм, применя-емых для получения изделий из металлических порошков) и с незначительной пластической деформацией материала матрицы, необходимой только для заполнения пространства между волокнами упрочнителя и максимального уплотнения самой матрицы. При этом, как и в случае горячего прессования порошков, наряду с пластической деформацией матрицы на границе раздела между слоями или частицами матрицы, т.е. на границе матрица—матрица, а также на границе матрица—волокно, протекают диффузионные процессы, обеспечивающие прочную связь на этих границах и, в конечном счете, необходимую прочность КМ.
|
|
К основным технологическим параметрам прессования КМ относятся давление прессования, температура, время выдержки и среда, в которой осуществляется процесс.
В зависимости от технологического оформления можно выделить четыре разновидности процесса прессования: прессование в замкнутых пресс-формах и между обогреваемыми плитами; ступенчатое прессование; изостатическое или авто-1 клавное прессование; динамическое горячее прессование.
Прессование в пресс-формах и между обогреваемыми плитами. В этом случае прессование КМ можно осуществлять на обычных гидравлических прессах различной мощности, применяемых для обработки металлов давлением, в порошковой металлургии, в производстве пластмасс. Для обеспечения пригодности пресса в процессе диффузионной сварки необходимым условием является возможность поддерживать заданное давление на нем в течение длительного времени. Прессование изделий из КМ на таких прессах проводят в специальных пресс-формах,
|
нагреваемых тем или иным способом до нужной температуры. Диффузионную сварку можно осуществлять на воздухе, в вакууме и защитной среде. В зависимости от этого пресс, на котором ее проводят, может быть оснащен камерой для создания вакуума или необходимого давления.
Рис.3.7. Схема установки для горячего прессования: 1 — корпус камеры; 2 — упор; 3 — индуктор; 4 — плоскость разъема камеры; 5 — огнеупорные плиты; 6 -пластины; 7 — прессуемый пакет; 8 — уплотнительная резина; 9 — термопара; 10 — стол; 11 — сильфон; 12 — шток пресса |
В качестве примера одной из таких установок, применяемой для получения методом диффузионной сварки КМ, рассмотрим установку, представляющую собой гидравлический пресс с вакуумной камерой (рис. 3.7). Нижняя часть разъемного корпуса камеры через сильфон связана со штоком пресса, на который устанавливают пакет из заготовок КМ. В верхнюю часть корпуса
вмонтирован индуктор. В рабочем состоянии, т.е. при сомкнутых верхней и нижней частях корпуса, пакет расположен внутри индуктора. Детали пресса и корпус камеры для предотвращения нагрева пакета изолируют от штока пресса и упора верхней части корпуса изоляционными огнеупорными плитами из хромомагнезита. Для обеспечения равномерного нагрева пакета между ним и огнеупорными плитами устанавливают более массивные по сравнению с пакетом молибденовые пластины, в результате чего основная часть магнитного потока, создаваемого индуктором, поглощается этими пластинами. С целью предотвращения схватывания КМ с молибденовыми пластинами на их поверхность предварительно наносят тонкий слой суспензии оксида алюминия в спирте. Прессование проводят в вакууме (Ю-3...10 мм рт.ст.). Схематически процесс прессования листов на прессе между обогреваемыми плитами показан на рис. 3.8.
244
245
3.2. Твердофазные методы изготовления деталей |
Рис.3.8. Схема изготовления листов из бороалюминия: 1 — лист; 2 — верхняя траверса; 3 — пакет; 4 — нижняя траверса; 5 — обогреваемые плиты |
Ступенчатое прессование. Разновидностью процесса прессования между обогреваемыми плитами пресса является ступенчатое прессование. J Особенность этого процесса заключа-4 ется в возможности получения полуфабрикатов в виде листов, полос, лент, профилей большой длины из КМ на прессах с небольшими размерами прессующих плит. Прессование пакета из заготовок КМ большой длины осуществляется периодически: вначале подпрессовывается участок, ближайший к одному из концов пакета, затем пакет передвигается между плитами пресса таким образом, что непосредственно между плитами оказывается часть ранее пропрессованного участка и еще не подвергавшаяся прессованию часть. Таким образом постепенно прорабатывается весь пакет.
При ступенчатом прессовании только ширина изделия определяется шириной прессующих плит, длина же его практически не ограничена. Схема процесса ступенчатого прессования показана на рис. 3.9. Перспективность получения этим
|
методом листов из бороалюмини-
Рис.3.9. Схема ступенчатого полуфабрикатов (полос, профилей и т.п.) из бороалюминиевых композиций: / - полоса; 2 — обогреваемые плиты; 3 — верхняя траверса; 4 — пакет; 5 — нижняя траверса |
ц. евых материалов шириной 1,2 м и / длиной до 9 м очевидна. Недостат-—3~ком ступенчатого прессования является невысокая производительность процесса, обусловленная необходимостью выдержки каждого из прессуемых участков пакета при заданном давлении и температуре в течение промежутка времени, требующегося для пластической деформации и процессов диффузии. Изостатическое, или автоклавное прессование. Процесс изо-статического горячего прессования известен сравнительно недавно. Он сочетает в себе воздействие на тело температуры и
3. ТЕХНОЛОГИЯ ИЗГОТОВЛЕНИЯ КОНСТРУКЦИЙ ИЗ МКМ И УУКМ
давления газа. Обычно тело, на которое оказывается воздействие, помещают в вакуумированный герметичный контейнер, способный деформироваться при температуре процесса. Установка для изостатического горячего прессования, как правило, состоит из трех основных агрегатов: сосуда высокого давления или автоклава, системы для создания давления и системы обеспечения температуры. Сосуд высокого давления может быть выполнен либо в виде оболочки небольшой толщины, подкрепленной намотанной на нее проволокой, либо толстостенным, монолитным. Применяемые в настоящее время в США в опытном производстве установки горячего изостатического прессования имеют диаметр рабочего пространства до 910 мм и рассчитаны на давление от 21 до 210 МПа. Наиболее часто применяют установки с давлением 70...105 МПа. Экспериментальные установки горячего изостатического прессования могут работать под давлением до 1050 МПа. Давление в установках в зависимости от требуемой скорости нагружения обеспечивается компрессорами диафрагменного или поршневого типа. Высокие скорости создания давления достигаются в результате использования аккумуляторов высокого давления. В качестве рабочего газа обычно применяют гелий или аргон, однако существуют системы, в которых используют азот или воздух.
Установки изостатического горячего прессования обычно построены по принципу "холодных стенок", означающему, что охлаждающая среда приложена либо снаружи, либо изнутри к стенкам сосуда высокого давления, уплотнениям и соединениям.
Наиболее сложная и ответственная часть установки — система обеспечения температуры прессования. Основой этой системы является печь, устанавливаемая внутри сосуда высокого давления таким образом, чтобы не было утечки теплоты за счет излучения и конвекции газов, находящихся под высоким давлением, к стенкам сосуда.
Конструкции установок изостатического прессования в течение последних 5—8 лет разрабатывали в двух основных направлениях. Первое направление связано с усовершенствованием сосудов высокого давления. Были созданы автоматические быстрозакрывающиеся механизмы, позволяющие заклады-
246
247
3.2. Твердофазные методы изготовления деталей
вать и извлекать обрабатываемые детали. В конструкциях этих механизмов применяют затворы игольчатого типа и безрезьбовые затворы (закрепляемые обоймой), как в дополнение к обычным резьбовым гидравлическим затворам.
Схема выполнения профилей из металлокомпозитов показана на рис. 3.10, а— е, возможные виды полуфабрикатов и схемы приспособлений для их изготовления — на рис. 3.11.
Рис. 3.10.Схема изготовления профиля из КМ в изостате:
|
а — заготовка; б — сборка заготовки с формирующими элементами; в - заключение сборки в пластичный металлический контейнер и вакуумирование контейнера; г — заваривание контейнера; д — нагрев и подача давления; е — готовый профиль
Рис. 3.11.Возможные виды полуфабрикатов: / — готовый полуфабрикат; 2 — заготовка; 3 формирующий элемент; 4 — контейнер
3. ТЕХНОЛОГИЯ ИЗГОТОВЛЕНИЯ КОНСТРУКЦИЙ ИЗ МКМ И УУКМ
Динамическое горячее прессование. Этот процесс, относящий-I к категории импульсных методов формирования и называемый за рубежом процессом формования с применением высо-<их скоростей и энергий, применялся первоначально для прецизионной ковки металлических слитков в изделия сложной |>ормы. Изготовление композиционных материалов этим ме-юдом заключается в диффузионной сварке пакета предвари-гельной заготовки, нагретого до необходимой температуры, в результате кратковременного приложения очень больших дав-иений. Динамическое горячее прессование предварительных шготовок можно осуществлять на ковочных молотах и подобных им установках в специальных пресс-формах или вакууми-рованных пакетах. В отечественной практике этот метод применяется редко.
Режимы изготовления и свойства бороалюминиевых композиций, полученных методом диффузионной сварки в изостате, представлены в табл. 3.1.
Таблица 3.1
Дата добавления: 2018-05-02; просмотров: 807; Мы поможем в написании вашей работы! |
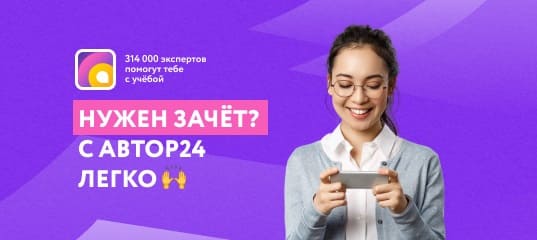
Мы поможем в написании ваших работ!