Диаграмма состояния железоуглеродистых сплавов
Все железоуглеродистые сплавы делятся на два больших класса: стали (с содержанием углерода до 2,14%) и чугуны (с содержанием углерода более 2,14%). Стали и чугуны являются наиболее широко используемые в технике материалы. Поэтому изучение диаграммы Fe – C является необходимым условием правильного выбора марок сталей или чугунов, а также режимов их термической и технологической обработок.
Диаграмма состояния показывает строение сплава в зависимости от соотношения компонентов и от температуры. Она строится экспериментально по кривым охлаждения сплавов. В отличие от чистых металлов сплавы кристаллизуются не при постоянной температуре, а в интервале температур. Поэтому на кривых охлаждения имеется две критические точки. Критическими точками называются температуры начала и конца фазовых превращений. В верхней критической точке, называемой точкой ликвидус (tл) (от лат.liquidus – редкий, очевидный), начинается кристаллизация. В нижней критической точке, которая называется солидус (tс) (от лат. solidus – твёрдый), кристаллизация завершается.
Диаграмму состояния строят в координатах температура - концентрация углерода. Линии диаграммы разграничивают области одинаковых фазовых состояний. Вид диаграммы зависит от того, как взаимодействуют между собой компоненты. Для построения диаграммы состояния используют большое количество кривых охлаждения для сплавов различных концентраций. При построении диаграммы критические точки переносятся с кривых охлаждения на диаграмму и соединяются линией. В получившихся на диаграмме областях записывают фазы или структурные составляющие.
|
|
Линия диаграммы состояния, на которой при охлаждении начинается кристаллизация сплава, называется линией ликвидус, а линия, на которой кристаллизация завершается, - линией солидус.
Диаграмма состояния железоуглеродистых сплавов даёт представление о строении основных конструкционных сплавов – сталей и чугунов.
2.4.1. Компоненты, фазы и структурные составляющие сплавов железа с углеродом.
Железо – пластичный металл серебристо-белого цвета. Твёрдость и прочность железа невысока (НВ80, σв = 250 МПа) при значительной пластичности (δ=50%). Температура плавления - 1539ºС, плотность 7,83 г/см2.
Углерод встречается в природе в виде алмаза и графита. Графит имеют сложную кристаллическую решётку. Он является непрочным материалом, но с увеличением температуры прочность графита значительно возрастает. Температура плавления графита 3500ºС. С углеродом железо образует химические соединения и твёрдые растворы внедрения.
Цементит – это химическое соединение железа с углеродом (карбид железа) Fe3C. В нём содержится 6,67% углерода (по массе). Имеет сложную ромбическую кристаллическую решётку. Характеризуется очень высокой твёрдостью (НВ800), крайне низкой пластичностью и хрупкостью. Температура плавления зависит от его состава (хром, молибден и др.) находится в широком диапазоне 1250…1600ºС.
|
|
Феррит – твёрдый раствор углерода в α-железе. Содержание углерода в феррите очень невелико – максимальное – 0,02% при температуре 727ºС. При комнатной температуре в феррите содержится не более 0,006% углерода. Благодаря столь малому содержанию углерода свойства феррита совпадает со свойствами железа (низкая твёрдость и высокая пластичность). Твёрдый раствор углерода в δ-железе, существующий при температуре 1392…1539ºС, также называется ферритом или высокотемпературным ферритом (δ-ферритом). Он характеризуется максимальной растворимостью углерода 0,1% при температуре 1499ºС.
Аустенит – это твёрдый раствор углерода в γ-железе. Максимальное содержание углерода в аустените составляет 2,14% (при температуре 1147ºС). Аустенит характеризуется высокой пластичностью и низкими прочностью и твёрдостью (НВ220).
Перлит – это механическая смесь феррита с цементитом, содержит 0,8%углерода, образуется из аустенита при температуре 727º С, является эвтектоидом. Эвтектоид – это механическая смесь двух фаз, образующаяся из твёрдого раствора. Перлит имеет пластинчатое строение, т.е. состоит из чередующихся пластинок феррита и цементита. Возможно и зернистое строение перлита, когда он состоит из зёрен цементита, окружённых ферритом. Зернистый перлит значительно пластичнее пластичного, имеет меньшую твёрдость.
|
|
Ледебурит представляет собой эвтектическую смесь аустенита с цементитом. Содержит 4,3% углерода, образуется из жидкого сплава при температуре 1147ºС. При температуре 727ºС аустенит, входящий в состав ледебурита, превращается в перлит и ниже этой температуры ледебурит представляет собой механическую смесь перлита с цементитом. Ледебурит обладает высокой твёрдостью (НВ600…700) и хрупкостью.
Фаза цементита имеет пять структурных фаз: цементит первичный, образующийся из жидкого сплава; цементит вторичный, образующийся из аустенита; цементит третичный, образующийся из феррита; цементит ледебурита; цементит перлита.
2.4.2. Диаграмма железо-цементит.
Практическое значение имеют сплавы железа с углеродом, содержащие углерода до 6,67% (стали и чугуны). Поэтому рассматривают диаграмму состояния сплавов железа с углеродом только до этой концентрации, т.е. фактически рассматривается диаграмма железо-цементит (Fe-Fe3C). На рис.2.2 приведена диаграмма состояния сплавов железа с цементитом. На горизонтальной оси концентраций отложено содержание углерода от 0 до 6,67%. Левая вертикальная ось соответствует 100% содержанию железа. На ней отложены температура плавления железа и температура его полиморфных превращений. Правая вертикальная ось (6,67% углерода) соответствует 100% содержанию цементита. Буквенное обозначение точек диаграммы принято согласно международному стандарту и изменению не подлежит.
|
|
Линия ABCD диаграммы является линией ликвидус. На ней начинается кристаллизация: на участке АВ – феррита, ВС – аустенита и CD – первичного цементита. Линия AHJECF является линией солидус диаграммы.
Главная роль в диаграмме состояния железоуглеродистых сплавов отводится её левой части – сталям, так как на превращениях, происходящих в стале, основана термическая обработка. Рассмотрим эти превращения. В результате кристаллизации образуется аустенит. При дальнейшем понижении температуры аустенит претерпевает превращения, связанные с изменением кристаллической решётки (γ-железа переходит в α-железо), при этом снижается в нём растворимость углерода
В точке S, соответствующей содержанию углерода 0,8%, при температуре 727ºС аустенит полностью распадается, образуется перлит. Сталь, содержащую 0,8% углерода, называют эвтектоидной. Её структура состоит из одного перлита. Сталь, содержащую менее 0,8% углерода, называют доэвтектоидной, а сталь с содержанием более 0,8% углерода – заэвтектоидной. Переход чистого железа из модификации γ-железа в α-железо происходит при температуре 911ºС. На диаграмме это соответствует точке G. В доэвтектоидных сталях при температурах, лежащих на линии GS, начинается выделение феррита из аустенита. Поэтому при дальнейшем понижении температуры содержание углерода в оставшемся аустените возрастает. Когда она составит 0,8% (при температуре 727ºС), оставшийся аустенит перейдёт в перлит. Таким образом, в доэвтектоидной стали при полном охлаждении получается структура, состоящая из равномерно распределённых зёрен перлита и феррита. В заэвтектоидной стали на линии SЕ, при понижении температуры из аустенита, пересыщенного углеродом, по границам зёрен начинает выделяться вторичный цементит. Когда в аустените останется 0,8% углерода, он при температуре 727ºС перейдёт в перлит. Следовательно, в заэвтектоидной стали при медленном охлаждении получается структура, состоящая из перлита и вторичного цементита. При этом вторичный цементит расположен в тонкой сетки по границам зёрен перлита.
Сплав, содержащий до 0,02% углерода не имеет после завершения всех превращений в структуре перлита. Такой сплав часто называют техническим железом. Структура технического железа представляет собой зёрна феррита или феррита с небольшим количеством третичного цементита.
Линия GSE диаграммы называется линией верхних критическихточек или линией начала превращения аустенита (при охлаждении). Линия PSK диаграммы (температура 727ºС) называется линией нижних критических точек или линией перлитного превращения.
2.4.3. Превращения в чугунах.
Точка С (4,3%углерода) представляет собой эвтектическую точку (эвтектикой называют равномерную мелкозернистую смесь двух фаз, которые одновременно кристаллизуются из жидкого сплава). Она соответствует температуре 1147ºС, при которой кристаллизуется сплав указанного содержания углерода, при этом одновременно выделяются из жидкого сплава кристаллы аустенита и цементита, образуя эвтектическую смесь – ледебурит. Его структура представляет собой равномерную смесь кристаллов аустенита с цементитом. Чугун, содержащий 4,3% углерода, называется эвтектическим. Чугуны, содержащие менее 4,3%С, называют доэвтектическим. Их кристаллизация начинается при температурах, лежащих на линии ВС, с выделением аустенита, и заканчивается при температурах, лежащих на линии ЕС образованием ледебурита. При дальнейшем понижении температуры растворимость углерода уменьшается и из аустенита начинает выделяться вторичный цементит. Когда углерода в аустените останется 0,8%, при 727ºС аустенит переходит в перлит. Таким образом, в доэвтектическом чугуне образуется структура, состоящая из ледебурита, перлита и вторичного цементита.
Чугуны, содержащие более 4,3% углерода, называют заэвтектическими. Их кристаллизация начинается при температурах, лежащих на линии CD. При этом выделяется первичный цементит. Кристаллизация заканчивается при температуре 1147ºС по линии CF образованием ледебурита. Получившаяся структура остаётся неизменной. В составе ледебуритной эвтектики при температуре 727ºС аустенит переходит в перлит. Структура заэвтектических чугунов состоит из ледебурита и первичного цементита.
Диаграмма состояния железоуглеродистых сплавов позволяет установить температурные режимы кристаллизации сталей и белых чугунов, режимы горячей обработки давлением (ковки, прокатки, штамповки) режимы термической обработки. и т.д.
При очень медленном охлаждении кристаллизация может идти таким образом, что углерод будет выделяться в виде графита, а не цементита. Железоуглеродистые сплавы с содержанием углерода в виде графита называются серыми чугунами.
Дополнение к лекции №3
Диаграмма состояния железо-цементит отражает нестабильное равновесие фаз. Точка А соответствует температуре плавления чистого железа (1539ºС), а точка D – температуре плавления цементита (1250…1600ºС) Процесс кристаллизации сплавов железо-углерод (в зависимости от содержания углерода) начинается при температуре, отложенных на линии ABCD. Эта линия называется линией ликвидус.
Конец затвердевания сплавов происходит при температурах, отложенных на линии AHJECF. Эта линия называется линией солидус. Точка Е характеризует предельную растворимость углерода в γ-железе (2,14%C) при температуре 1147ºС.
С изменением концентрации углерода в сплаве при температурах, соответствующих участку АС линии ликвидус, из жидкого сплава кристаллизуется аустенит, а при температурах, соответствующих участку CD, кристаллизуется цементит, называемый первичным.
В точке С при температуре 1147ºС и концентрации углерода 4,3% из жидкого сплава одновременно кристаллизуется аустенит и первичный цементит с образованием эвтектики (смеси), называемой ледебуритом. На участке АЕ линии солидус сплавы с содержанием углерода до 2,14% кристаллизуются с образованием аустенита. На участке ЕС линии солидус при температурах 1147ºС сплавы с содержание м 2,14…4,3%C кристаллизуются с образованием ледебурита и аустенита. На участкеCF линии солидус при температурах 1147ºС сплавы с содержанием 4,3…6,67%C кристаллизуются с образованием ледебурита и цементита.
Все железоуглеродистые сплавы в результате первичной кристаллизации, имеющие ледебурит и более 2,14%C, называются чугунами. После кристаллизации (линияAHJECF)в железоуглеродистых сплавах с понижением температуры происходят структурные превращения.. Превращения в твёрдом состоянии характеризуют линии GS, SE,PSK и PQ. Точка G соответствует полиморфному превращению γ-железа в α-железо при температуре 911ºС.
Точка S при температуре 727ºС и концентрации углерода 0,8% показывает минимальную температуру равновесного скуществования аустенита. При понижении температуры ниже 727ºС происходит распад аустенита с одновременным выделением феррита и цементита – образуется эвтектоидная смесь, называемая перлитом.
Точка Р характеризует предельную растворимость углерода в α-железе при температуре 727 ºС, которая не превышает 0,02%.
Точка Q является граничной. Все сплавы, лежащие левее её, состоят только из феррита и называются техническим железом.
Все сплавы, имеющие концентрацию углерода дл 0,8% (проекция точки S), называются доэвтектоидными сталями. Они имеют в структуре феррит и перлит. Сплав железа с углеродом, в котором концентрация углерода равна 0,8%, называется эвтектоидной сталью. Структура её перлитная. Сплавы, в которых концентрация углерода меняется от 0,8 до 2,14% (проекция точки Е), называются заэвтектоидными сталями. Их структура состоит из перлита и цементита.
Линия GS показывает начало превращения аустенита в феррит при охлаждении и, наоборот, при нагреве.
Линия SE показывает уменьшение растворимости углерода в аустените от 2,14% при 1147 ºС до 0,8% при 727 ºС. С понижением температуры от 1147 ºС до 727 ºС из аустенита выделяется избыточный углерод, образуя вторичный цементит.
Линия PSK характеризует превращения в результате распада аустенита (температура ниже 727 ºС) на смесь феррита и цементита, называемую перлитом.
Линия PQ показывает уменьшение растворимости углерода в феррите с понижением температуры от 0,02% при 727 ºС до 0,006% при 20 ºС. Выделяющийся из феррита избыточный углерод образует цементит, называемый третичным.
Лекция №3
3. Железоуглеродистые сплавы
К железоуглеродистым сплавам относят чугун и сталь. Чугун – самый дешёвый машиностроительный материал, обладающий хорошими литейными свойствами. Кроме того, он является исходным продуктом для получения стали.
3.1. Основные сведения о производстве чугуна.
3.1.1. Материалы для производства чугуна.
Сырьём для производства чугуна является железная руда. Это горная порода, содержащая железо в количестве, при котором её технически и экономически целесообразно перерабатывать. Важнейшими железными рудами являются: магнитный железняк, красный железняк, бурый железняк, шпатовый железняк и железистые кварциты. Наиболее богатые руды – это магнитный железняк, содержание железа в нём составляет до 70%, в красном железняке – до 65%.В остальных железняках железа, примерно, 30…50%.
В рудах кроме оксидов железа находится пустая порода - кремнезем, глина, сера, фосфор и др. примеси. Их частично удаляют ещё до плавки, подвергая руду предварительному обогащению с целью увеличения содержания в ней железа. Обогащения производят промывкой и магнитной сепарацией. Промывка позволяет отделить от руды менее плотную пустую породу. Магнитная сепарация заключается в разделе измельченной руды в магнитном поле на железосодержащие минералы, обладающие магнитными свойствами, и немагнитную пустую породу. После обогащения полученный железорудный концентрат перерабатывается в кусковые материалы необходимого размера путём агломерации или окатывания. Агломерация – это спекание смеси, состоящей из мелкой руды, рудной пыли с коксовой мелочью и флюса. В результате получается кусковый пористый материал – агломерат. При окатывании этой смеси придают форму шариков - окатышей диаметром около 20 мм. При использовании агломерата и окатышей нет необходимости в отдельной подаче флюса, так как он входит в их состав.
Продуктом, необходимым при плавке чугуна, являются флюсы, главным образом известнякCaCO3, они служат для окончательного удаления пустой породы из руды в процессе плавки в доменной печи. Флюсы образуют с пустой породой и золой легкоплавкое соединение, называемое шлаком. Шлак имеет меньшую плотность, чем металл, поэтому он располагается в печи над расплавленным металлом и может быть легко удалён.
Важным материалом для получения чугуна является топливо. Топливом является кокс. Его получают из специальных коксующихся каиенных углей путём нагрева до температуры 1000ºС без доступа воздуха. При этом удаляется смола и остаётся пористый материал, почти целиком состоящий из углерода. Кокс – дорогостоящее топливо, поэтому в целях уменьшения его расхода, который составляет 400 450 кг на 1 т чугуна, и для повышения производительности доменных печей используют природный газ. Существует способ вдувания в доменную печь угольной пыли. Это даёт большой экономический эффект. Кроме указанных материалов при плавке чугуна вводят немного марганцевой руды.
3.1.2.Устройцство доменной печи
Доменная печь – вертикальная печь шахтного типа. Внутри печь выложена огнеупорным кирпичом, сверху покрыта стальным кожухом. Высота современных домен достигает 80 м. Доменная печь состоит из пяти основных частей (рис.3.1): колошника, шахты, распара, заплечиков и горна. Колошник является верхней частью печи. Он содержит загрузочное устройство 4, представляющее собой систему конусов, которые создают условия для правильной загрузки материалов: руды, флюсов и топлива. В колошнике находятся газоотводные трубы 3, по ним уходит избыточный колошниковый газ, который в дальнейшем используется в качестве топлива.
В шахте, распаре, заплечиках имеется система холодильников для охлаждения кладки печи.
Самой сложной частью является горн. В горне расположены фурмы 2 – устройства для вдувания в печь нагретого воздуха, который поступает из воздухопровода 5. На современных доменных печах число фурм составляет 25…30. В нижней части горна имеется устройство для выпуска чугуна – чугунная летка 1 и выше её – шлаковая летка 6 для выпуска шлака. Большие доменные печи оборудованы тремя-четырьмя летками, этим достигается почти непрерывный процесс выпуска чугуна.
Для подогрева воздуха до температуры 1200º С служат воздухонагреватели, которые в свою очередь обогреваются отходящими колошниковыми газами.
3.1.3. Доменный процесс
. Условно процесс, протекающий в доменной печи, можно разделить на следующие этапы: восстановление железа из его оксидов; превращение железа в чугун и шлакообразование. Эти этапы процесса проходят в печи одновременно, переплетаясь друг с другом, но с разной интенсивностью, на разных уровнях печи.
Процесс получения чугуна заключается в следующем: шихтовые материалы (железная и марганцевая руды, топливо и флюсы) опускаются вниз, а навстречу им поднимаются газы. Они образуются при горении кокса. Горение начинается в области горна. Через фурменные отверстия раскалённый до температуры 1200º С воздух поступает в печь и на уровне фурм вступает в реакцию с углеродом кокса. При горении образуется углекислый газ и выделяется большое количество тепла:
|
|
В доменную печь вдувают также пар, который вступает в реакцию с коксом и окисляет его:
|
|
Важнейшим периодом доменного процесса является восстановление железа из его оксидов. Оно происходит постепенно по следующей схеме:
Одновременно идёт восстановление железа из оксидов за счёт твёрдого углерода по реакции
|
Таким образом восстанавливается до 50% шихты. Твёрдый углерод (в виде сажи) откладывается в порах руды и науглероживает железо.
Наряду с процессами восстановления железа происходят реакции восстановления и других элементов шихты: кремния, марганца, фосфора. Марганец восстанавливается из марганцевой руды, специально вводимой в шихту.
В результате восстановления указанных элементов в доменной печи получается сложный сплав железа с углеродом, марганцем, серой и фосфором.
Пустая порода, зола, часть серы, кокса и примеси руды соединяются с флюсами, образуя шлак. Роль шлака в доменном процессе очень велика: от него в значительной степени зависит качество чугуна. Шлак является ценным продуктом доменной плавки. Он используется в строительстве жилых и промышленных зданий, для изготовления цемента, бетона, кирпича, для грунтовки дорог и даже как удобрение.
Основным показателем работы доменной печи является коэффициент использования её полезного объёма (КИПО). Для вычисления КИПО нужно полезный объём печи (м3) разделить на суточную выплавку (т). Этот показатель в среднем составляет (0,5…0,6) м3/т. Прогрессивная технология доменной плавки предусматривает уменьшение КИПО печи , а значит увеличение её производительности.
3.2. Чугуны
Чугуном называют сплав железа с углеродом, содержащий от 2,14 до 6,67% углерода. Это теоретическое определение. На практике содержание углерода в чугуне находится в пределах 2,5…4,5%.
3.2.1. Классификация чугунов
В зависимости от того, в какой форме находится углерод в чугунах, различают следующие их виды.
Белый чугун. В этом чугуне весь углерод находится в связанном состоянии в виде цементита. Структура белого чугуна соответствует диаграмме железо-цементит.
Серый чугун. В этом чугуне большая часть углерода находится в виде графита, включения которого имеют пластинчатую форму.
Высокопрочный чугун в своём составе имеет графитные включения шаровидной формы.
Ковкий чугун имеет графитовые включения в форме хлопьев.
Содержание углерода в виде цементита в сером, высокопрочном и ковком чугунах составляет не более 0,8%.
Белый чугун обладает высокой твёрдостью, хрупкостью и очень плохо обрабатывается. Поэтому для изготовления изделий он не используется и применяется как передельный чугун, т.е. идёт на производство стали. Для деталей с высокой износостойкостью используется чугун с отбеленной поверхностью, в котором основная масса металла имеет структуру серого чугуна, а поверхностный слой – белого чугуна.
Машиностроительными чугунами, идущими на изготовление деталей, являются серый, высокопрочный и ковкий чугуны. Детали из них изготовляются литьём, так как чугуны имеют очень хорошие литейные свойства. Благодаря графитным включениям эти чугуны хорошо обрабатываются, имею высокую износостойкость, гасят колебания и вибрации. Но графитные включения уменьшают прочность.
Таким образом, структура машиностроительных чугунов состоит из металлической основы и графитных включений.
По металлической основе они классифицируются на ферритный чугун (весь углерод содержится в виде графита), феррито-перлитный и перлитный (содержит 0,8% углерода в виде цементита). Характер металлической основы влияет на механические свойства чугунов: прочность и твёрдость выше у перлитных, а пластичность – у ферритных.
Серый чугун имеет пластинчатые графитные включения. Структура серого чугуна схематически показана на рис.3.2,а. Получают серый чугун путём первичной кристаллизации из жидкого сплава. На графитизацию (процесс выделения графита) влияет скорость охлаждения и химический состав чугуна. При быстром охлаждении графитизация не происходит и получается белый чугун. По мере уменьшения скорости охлаждения получаются соответственно перлитный, феррито-перлитный и ферритный чугуны. Способствуют графитизации углерод и кремний. Содержание кремния в чугуне 0,5…5%. Марганец и сера препятствуют графитизации, сера ухудшает механические и литейные свойства, Фосфор не влияет на графитизацию, но улучшает литейные свойства.
Механические свойства серого чугуна зависят от количества и размера графитных включений. Графитовые включения можно считать нарушениями сплошности, ослабляющими металлическую основу.. Так как пластинчатые включения наиболее сильно ослабляют металлическую основу, серый чугун имеет наиболее низкие характеристики как прочности, так и пластичности среди всех машиностроительных чугунов. Уменьшение размера графитовых включений улучшает механические свойства. Измельчанию графитовых включений способствует кремний.
Маркируется серый чугун буквами СЧ и числом, показывающим предел прочности в десятках мегапаскалей. Так, чугун СЧ35 имеет σв=350 МПа. Имеются следующие марки серых чугунов СЧ10, СЧ15, сч20,…,СЧ45.
Высокопрочный чугун имеет шаровидные графитные включения. Структура этого чугуна изображена на рис.3.2,б. Получают высокопрочный чугун добавкой в жидкий чугун небольшого количества щелочных или щелочноземельных металлов, которые округляют графитные включения в чугуне, что объясняется увеличением поверхностного натяжения графита. Чаще всего для этой цели применяют магний в количестве 0,03…0,07%. По содержанию других элементов высокопрочный чугун не отличается от серого. Шаровидные графитные включения в наименьшей степени ослабляют металлическую основу. Именно поэтому высокопрочный чугун имеет более высокую прочность и более пластичен, чем серый. При этом он сохраняет хорошие литейные свойства, обрабатываемость резанием, способность гасить вибрации и т.д.
Маркируются высокопрочный чугун буквами ВЧ и цифрами, показывающими предел прочности в десятках мегапаскалей. Например, чугун ВЧ60 имеет σв = 600 МПа. Существуют следующие марки высокопрочных чугунов: ВЧ35, Вч40, Вч45, ВЧ50, ВЧ60, ВЧ70, ВЧ80, ВЧ100.
Применяются высокопрочные чугуны для изготовления ответственных деталей – зубчатых колёс, валов и др.
Ковкий чугун имеет хлопьевидные графитные включения (рис.3.2,в). Благодаря такой форме графитных включений он также характеризуется более высокой прочностью и пластичностью, чем серый чугун. Его получают из белого чугуна путём графитизирующего отжига, который заключается в длительной (до 2 суток) выдержке при температуре 950 970ºС. Если после этого чугун охладить, то получается ковкий перлитный чугун, металлическая основа которого состоит из перлита и небольшого количества (до 20%) феррита. Такой чугун называется также светлосердечным. Если в области эвтектоидного превращения (720…760ºС) проводить очень медленное охлаждение или даже выдержку, то получиться ковкий ферритный чугун, металлическая основа которого состоит из феррита и очень небольшого количества перлита (до 10%). Этот чугун называют черносердечным, так как он содержит сравнительно много графита.
Маркируется ковкий чугун буквами КЧ и двумя числами, показывающими предел прочности в десятках мегапаскалей и относительное удлинение в %. Так, чугун КЧ45-7 имеет σв = 450 МПа и δ = 7%. Ферритные ковкие чугуны (КЧ33-8, КЧ37-12) имеют более пластичность, а перлитные (КЧ50-4, КЧ60-3) более высокую прочность.
Применяют ковкий чугун для изготовления деталей небольшого сечения, работающих при ударных и вибрационных нагрузках.
Дополнение к лекции №3
Диаграмма состояния железо-цементит отражает нестабильное равновесие фаз. Точка А соответствует температуре плавления чистого железа (1539ºС), а точка D – температуре плавления цементита (1250…1600ºС) Процесс кристаллизации сплавов железо-углерод (в зависимости от содержания углерода) начинается при температуре, отложенных на линии ABCD. Эта линия называется линией ликвидус.
Конец затвердевания сплавов происходит при температурах, отложенных на линии AHJECF. Эта линия называется линией солидус. Точка Е характеризует предельную растворимость углерода в γ-железе (2,14%C) при температуре 1147ºС.
С изменением концентрации углерода в сплаве при температурах, соответствующих участку АС линии ликвидус, из жидкого сплава кристаллизуется аустенит, а при температурах, соответствующих участку CD, кристаллизуется цементит, называемый первичным.
В точке С при температуре 1147ºС и концентрации углерода 4,3% из жидкого сплава одновременно кристаллизуется аустенит и первичный цементит с образованием эвтектики (смеси), называемой ледебуритом. На участке АЕ линии солидус сплавы с содержанием углерода до 2,14% кристаллизуются с образованием аустенита. На участке ЕС линии солидус при температурах 1147ºС сплавы с содержание м 2,14…4,3%C кристаллизуются с образованием ледебурита и аустенита. На участкеCF линии солидус при температурах 1147ºС сплавы с содержанием 4,3…6,67%C кристаллизуются с образованием ледебурита и цементита.
Все железоуглеродистые сплавы в результате первичной кристаллизации, имеющие ледебурит и более 2,14%C, называются чугунами. После кристаллизации (линияAHJECF)в железоуглеродистых сплавах с понижением температуры происходят структурные превращения.. Превращения в твёрдом состоянии характеризуют линии GS, SE,PSK и PQ. Точка G соответствует полиморфному превращению γ-железа в α-железо при температуре 911ºС.
Точка S при температуре 727ºС и концентрации углерода 0,8% показывает минимальную температуру равновесного скуществования аустенита. При понижении температуры ниже 727ºС происходит распад аустенита с одновременным выделением феррита и цементита – образуется эвтектоидная смесь, называемая перлитом.
Точка Р характеризует предельную растворимость углерода в α-железе при температуре 727 ºС, которая не превышает 0,02%.
Точка Q является граничной. Все сплавы, лежащие левее её, состоят только из феррита и называются техническим железом.
Все сплавы, имеющие концентрацию углерода дл 0,8% (проекция точки S), называются доэвтектоидными сталями. Они имеют в структуре феррит и перлит. Сплав железа с углеродом, в котором концентрация углерода равна 0,8%, называется эвтектоидной сталью. Структура её перлитная. Сплавы, в которых концентрация углерода меняется от 0,8 до 2,14% (проекция точки Е), называются заэвтектоидными сталями. Их структура состоит из перлита и цементита.
Линия GS показывает начало превращения аустенита в феррит при охлаждении и, наоборот, при нагреве.
Линия SE показывает уменьшение растворимости углерода в аустените от 2,14% при 1147 ºС до 0,8% при 727 ºС. С понижением температуры от 1147 ºС до 727 ºС из аустенита выделяется избыточный углерод, образуя вторичный цементит.
Линия PSK характеризует превращения в результате распада аустенита (температура ниже 727 ºС) на смесь феррита и цементита, называемую перлитом.
Линия PQ показывает уменьшение растворимости углерода в феррите с понижением температуры от 0,02% при 727 ºС до 0,006% при 20 ºС. Выделяющийся из феррита избыточный углерод образует цементит, называемый третичным.
Лекция №4
Производство стали
Сталь – важнейший материал, используемый в машиностроении, В отличие от чугуна она содержит меньше углерода и вредных примесей. Поэтому процесс получения стали состоит в удалении этих элементов. Основные способы получения стали: кислородно-конверторный, мартеновский и в электропечах.
Конвертерный способ
В настоящее время применяют кислородную плавку, основанную на продувке жидкого чугуна кислородом, подводимым сверху в конвертер (от лат.converto – изменяю, превращаю). Конвертер представляет собой сосуд грушевидной или цилиндрической формы высотой до 11м и диаметром до 10м, характеризующиеся весьма высокой производительностью – 400 т в плавку. Конвертер покрыт стальным кожухом, внутри выложен огнеупорной кладкой. В нижней части конвертера глухое дно, легко заменяемое. Конвертер устанавливается на стойки и может свободно поворачиваться вокруг горизонтальной оси цапф, что необходимо для загрузки, взятия пробы и выпуска готовой стали.
Процесс выплавки стали в конвертере заключается в следующем: в начале происходит загрузка металлического лома (иногда железной руды), затем заливают жидкий чугун, переводят конвертер в вертикальное положение и загружают известь для удаления фосфора, находящегося в чугуне и руде. Опускают водоохлаждаемую фурму (от нем.Form, букв. – форма) – устройство для подвода дутья в конвертер, через которую подаётся кислород. В результате окисления примесей чугуна (углерода, кремния, марганца, фосфора) выделяется тепло в количестве, достаточном для поддержания металла в жидком состоянии в течении всего процесса без поступления тепла из других источников. Время продувки зависит от вместимости конвертера, заданной марки стали и данных анализа. Температура в конвертере поднимается до 2000…2500ºС. Продолжительность плавки 5-…60 минут.
Заключительным этапом получения стали является её раскисление, заключающееся в удалении вредных примесей оксида железа FeO. Раскисление производится добавкой в жидкую сталь раскислителей – марганца, кремния и алюминия:
FeO + Mn = Fe + MnO;
2FeО + Si = 2Fe + SiO2;
3FeO + 2Al = 3Fe + Al2O3.
В кислородном конвертере можно останавливать процесс на заданном содержании углерода и получать сталь самых различных марок. Недостатком кислородно-конвертерного способа получения стали является необходимость сооружения сложных и дорогостоящих пылеочистительных установок, так как в процессе плавки образуется много пыли. Строительство кислородного конвертера требует значительных затрат. Не уступая по качеству мартеновскому способу получения стали, конвертерный способ значительно превосходит его по производительности. Конвертеры выплавляют 400 т/ч стали, а мартеновская печь – 80…100 т/ч.
С учетом указанных преимуществ, а также того, что при конвертерном способе коэффициент использования топлива, равный 70%, значительно больший, чем для других способов, и можно обойтись без миксеров (хранилищ чугуна), кислородно-конвертерная плавка будет в дальнейшем применяться всё более широко.
Мартеновский способ.
Мартеновский способ (от имени французского металлурга П. Мартена) – один из старейших способов производства стали.
Сталь в мартеновских печах выплавляется из передельного чугуна (твёрдого или жидкого), металлического лома, иногда вместо него применяют железную руду, вводят флюсы, главным образом, известняк. Топливом служат газы: доменный, коксовый, природный, а также мазут.
Мартеновский процесс делится на три этапа: плавление, кипение и раскисление.
Во время плавления окисляются кремний, марганец и фосфор за счёт кислорода оксида железа FeO. Образующиеся оксиды SiO2, MnO2 и P2O3, соединяясь с известняком, образуют шлак. Сера в виде FeS также соединяется с СаО и переходит в шлак. Для ускорения процесса расплавления и окисления примесей в печь подают через водоохлаждаемые фурмы кислород, благодаря чему сокращаются время плавки и расход топлива и руды.
Во время кипения окисляется углерод. При этом осуществляется химический контроль за количеством углерода в стали. Когда достигается необходимое содержание углерода, серы и фосфора, сталь раскисляют ферросплавами или алюминием.
Мартеновсий процесс длится 8…14 часов в зависимости от вместимости печи. В настоящее время работают печи производительностью от 40 до 900 тонн в плавку.
Плавка в дуговых и индукционных электрических.
Такая плавка является важнейшим способом получения стали высокого качества для производства деталей машин и инструментов. Она имеет ряд преимуществ перед мартеновской и кислородно-конвертерной. Электропечь быстро нагревается до заданной температуры - 2000ºС. Легко регулируется тепловой процесс. В электропечи легче легировать сталь, можно более полно удалять серу и фосфор, получать более раскислённую сталь. Электропечи бывают дуговые и индукционные. Большее применение находят дуговые печи. Процесс плавки в них в зависимости от вместимости длится 2,5…8 часов.
Производство стали в индукционных печах осуществляется значительно реже, чем в дуговых. Их чаще всего применяют при переплавке отходов легированной стали. Высокая температура, возможность создания вакуума, отсутствие науглероживающего металла позволяют получать в них сталь с малым содержанием углерода, Вместимость этих печей небольшая.
Дата добавления: 2018-04-15; просмотров: 773; Мы поможем в написании вашей работы! |
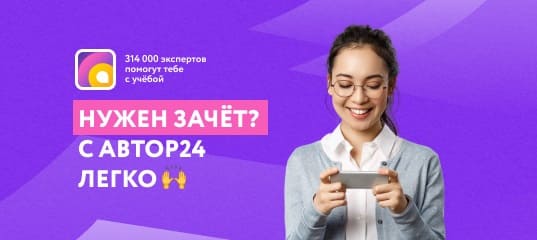
Мы поможем в написании ваших работ!